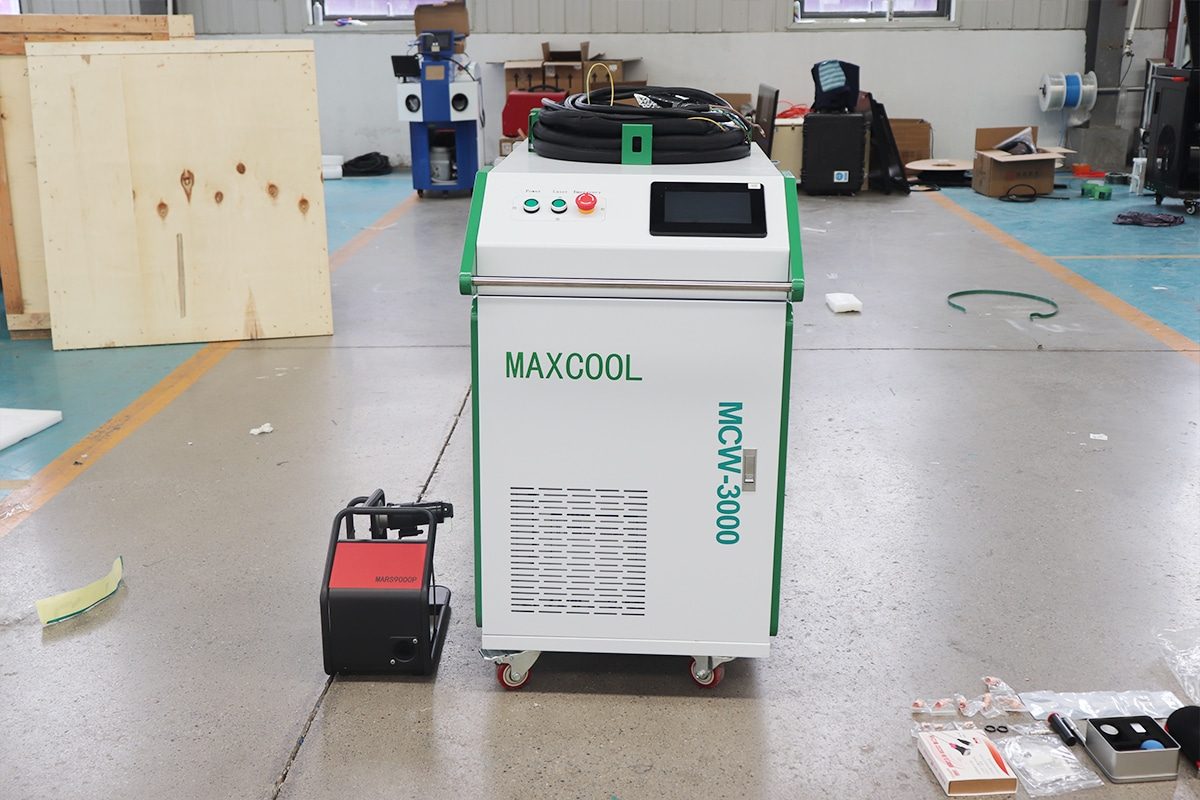
Why Are Laser Welding Machines So Expensive?
Laser welding machines have become a vital component of modern manufacturing due to their unmatched precision, speed, and ability to create high-strength welds across a wide range of materials. Industries such as automotive, aerospace, and electronics rely on these advanced systems for critical applications that demand superior quality and reliability. However, the cost of laser welding machines often raises questions for potential buyers. Why are these machines so expensive? The answer lies in the sophisticated technology, specialized components, and extensive research and development that go into their production. From high-powered laser sources to precision control systems, every element is designed to maximize performance and durability. Additionally, compliance with stringent safety and industry standards, along with the need for skilled labor and comprehensive customer support, further elevates their cost. This introduction delves into the complex factors that make laser welding machines a substantial investment in modern manufacturing.
Table of Contents
Understanding Laser Welding Technology
Laser welding represents a highly advanced and efficient method of joining materials, providing superior precision, speed, and strength. It has become a critical process in industries such as automotive, aerospace, and medical device manufacturing, where precision and reliability are paramount. The concentrated heat source offered by laser welding enables narrow, deep welds and high processing speeds that traditional methods cannot match.
Basics of Laser Welding
Laser welding works by focusing a high-energy laser beam on the materials to be joined. The energy from the laser quickly heats and melts the material, creating a fusion bond as the molten material cools. The laser’s high precision and energy concentration result in minimal heat-affected zones and reduced thermal distortion, making it ideal for applications that demand accuracy and clean welds. This capability is particularly advantageous for delicate components or intricate designs, as it ensures strong, consistent welds without compromising structural integrity.
Types of Laser Welding Machines
- Fiber Laser Welding Machines: These machines utilize optical fibers to generate and transmit the laser beam. Known for their high beam quality, efficiency, and durability, fiber lasers excel at welding reflective metals like aluminum and copper. Their minimal maintenance requirements and long operational life make them popular in demanding industrial settings.
- CO2 Laser Welding Machines: CO2 lasers generate a laser beam using a mixture of gases and are primarily used for welding non-metals or metals with moderate precision needs. Although less efficient than fiber lasers for metal welding, CO2 lasers are still valuable for specialized applications.
- Nd Laser Welding Machines: Historically used in many industries, Ndlasers offer good beam quality but are being gradually replaced by fiber lasers due to higher efficiency, lower maintenance, and better overall performance.
Advantages Over Traditional Welding Methods
Laser welding offers several advantages over traditional welding techniques such as MIG (Metal Inert Gas), TIG (Tungsten Inert Gas), and stick welding. Here are some of the key benefits:
- Precision and Control: Laser welding delivers unparalleled precision, creating clean, narrow welds with minimal distortion. Traditional methods often produce broader heat-affected zones and may not achieve the same level of detail.
- High Speed and Efficiency: Laser welding processes are much faster than conventional welding, reducing production times and increasing throughput. This makes laser welding an attractive option for high-volume manufacturing.
- Minimal Post-Processing: The precision and cleanliness of laser welds minimize the need for extensive post-weld processing, such as grinding or polishing, which is often required for traditional welds.
- Non-Contact Process: Laser welding is a non-contact process, meaning there is no physical tool wear or risk of contamination from the welding head. This contrasts with traditional welding methods that involve direct contact with the materials being joined.
- Automated and Robotic Integration: Laser welding systems are easily integrated into automated and robotic production lines, increasing productivity and reducing labor costs. Traditional welding processes often require more manual intervention and oversight.
To further explore the comparative benefits and applications of laser welding and traditional methods, you can refer to the article “Laser Welding VS Traditional Welding“. Understanding these distinctions highlights why laser welding machines are more complex and often come with a higher price tag due to their technological advantages and capabilities.
Components of Laser Welding Machines
Laser welding machines are complex systems that integrate multiple advanced components to deliver high-precision, efficient, and high-strength welds. The cost of these machines is driven by the intricate engineering and specialized technology built into each component.
Laser Sources
The laser source is the heart of any laser welding machine and plays a significant role in determining the machine’s overall performance and cost. The most commonly used laser sources are fiber lasers, CO2 lasers, and Nd lasers, each with unique characteristics suited for different applications. Fiber lasers are particularly favored due to their high efficiency, excellent beam quality, and ability to weld reflective metals. The development and manufacturing of high-power laser sources involve advanced materials, precise engineering, and extensive research, making them a major contributor to the cost of laser welding machines.
Optics and Beam Delivery Systems
Laser welding relies on precisely controlled optics and beam delivery systems to direct and focus the laser beam onto the target area. High-quality lenses, mirrors, and optical fibers ensure accurate beam positioning and consistent weld quality. The optical components must be manufactured to exacting standards to handle high-power laser energy without degradation. Additionally, beam delivery systems may include automated systems for precise movement and positioning, adding to the complexity and cost of the overall machine. The integration of adaptive optics for real-time control and monitoring further increases the performance and cost.
Cooling Systems
Laser welding generates significant amounts of heat, which must be managed effectively to maintain optimal performance and prevent damage to components. Cooling systems, typically water or air-cooled, are integrated to regulate the temperature of the laser source and other heat-sensitive components. Industrial water coolers are common in high-powered laser systems, offering precise temperature control to ensure consistent operation. Reliable cooling system design and implementation can help extend machine life and smooth operation, but it can also add complexity and cost to the machine.
Control Systems and Software
Modern laser welding machines are equipped with advanced control systems and software to manage the welding process with precision and automation. These systems allow operators to set parameters such as laser power, welding speed, and beam focus. Control software also enables integration with automated production lines, remote monitoring, and data logging for quality control. Developing intuitive, reliable, and feature-rich software requires significant investment in research and engineering. Moreover, ensuring compatibility with various industrial protocols and standards increases the complexity and cost of these systems.
Safety Features
Laser welding machines are powerful and inherently pose risks, necessitating robust safety features to protect operators and surrounding environments. These features may include protective enclosures, safety interlocks, emergency stop buttons, laser shielding, and specialized eyewear. Compliance with stringent safety standards and regulations is mandatory, and manufacturers must incorporate various safety mechanisms to meet these requirements. The cost of designing, testing, and certifying these safety features is substantial, but essential to ensure safe operation and regulatory compliance.
Each of these components contributes to the overall performance, reliability, and safety of laser welding machines. While the integration of such sophisticated components makes these machines more expensive, it also enables them to deliver unparalleled precision, efficiency, and durability in demanding industrial applications.
Factors Contributing to the High Cost of Laser Welding Machines
Laser welding machines are complex, high-tech systems designed to deliver precise and efficient welding for a wide range of applications. Their cost is driven by several key factors, including cutting-edge technology, specialized components, and extensive research and development.
Advanced Technology and Precision Engineering
Laser welding machines rely on state-of-the-art laser technology, which includes high-powered laser sources, sophisticated optics, and highly controlled beam delivery systems. Achieving precise, consistent welds requires advanced engineering and manufacturing processes with extremely tight tolerances. Each component must be finely tuned to deliver optimal performance. The integration of advanced technologies, such as adaptive optics and real-time control systems, further enhances their capabilities but adds to the cost due to the high level of precision and complexity involved.
Research and Development Costs
Continuous innovation is at the core of laser welding technology. Companies like Maxcool CNC invest heavily in research and development (R&D) to stay ahead in a competitive market. This investment covers the development of new laser sources, enhancements in software and automation, improvements in energy efficiency, and adaptation to specific industrial applications. R&D costs are reflected in the final price of the machines, as they fund the creation and refinement of cutting-edge features that meet evolving industry demands.
Materials and Components
High-quality materials and specialized components are essential for the performance and longevity of laser welding machines. Key components such as laser sources, optical lenses, mirrors, and precision motion systems are often made from rare or expensive materials. Additionally, the production and procurement of these components involve strict quality control processes to ensure they meet the necessary specifications. Sourcing these high-grade materials and components can be costly, especially for parts that are custom-designed or imported from specialized suppliers.
Manufacturing and Assembly
The manufacturing and assembly of laser welding machines require precision and expertise. Each machine must be carefully assembled, calibrated, and tested to ensure it meets performance and safety standards. Skilled labor is necessary to carry out these tasks, as laser welding machines integrate various mechanical, electrical, and optical subsystems. Precision assembly processes and quality assurance measures, such as extensive testing and calibration, contribute to higher production costs. Unlike mass-produced consumer goods, laser welding machines often have lower production volumes, requiring dedicated resources and specialized equipment.
Compliance and Certifications
Safety and regulatory compliance are critical aspects of laser welding machine design and manufacturing. These machines must adhere to strict safety standards and obtain various certifications to be used in industrial settings. Compliance with standards such as ISO, CE, and laser safety regulations involves testing, documentation, and certification processes that are both time-consuming and costly. Incorporating features like protective enclosures, emergency stops, and interlock systems further increases production costs but ensures that the machines can be operated safely and reliably.
After-Sales Service and Support
Laser welding machines require ongoing maintenance, training, and technical support to maximize their performance and lifespan. Reliable manufacturers invest in dedicated support teams and provide comprehensive after-sales services, including installation, troubleshooting, and training programs. The cost of maintaining a knowledgeable support staff and developing training materials contributes to the overall price. Customers benefit from having reliable assistance and expertise, which helps optimize machine usage and minimizes downtime.
Economies of Scale
Laser welding machines serve a specialized market segment, and production volumes are relatively low compared to mass-market products. As a result, manufacturers cannot leverage the same economies of scale as larger industries. Fixed costs, such as R&D, manufacturing setup, and quality control, are spread across fewer units, leading to a higher per-unit cost. Additionally, purchasing small quantities of specialized components often precludes bulk discounts, further elevating the overall cost of production.
The high cost of laser welding machines is a reflection of the advanced technology, precision engineering, and comprehensive support that these systems offer. While they represent a substantial investment, the value they provide in terms of performance, efficiency, and durability makes them indispensable for industries that demand high-quality welding solutions.
The Value Proposition of Laser Welding Machines
Despite their high initial cost, laser welding machines offer a compelling value proposition for industries that prioritize precision, productivity, and long-term savings.
Long-Term Cost Savings
While laser welding machines have a higher upfront cost compared to traditional welding equipment, they offer significant long-term savings. The precision and speed of laser welding reduce material waste, lower energy consumption, and minimize the need for extensive post-processing. Additionally, the non-contact nature of laser welding results in less wear and tear on consumables, leading to lower maintenance costs over time. The efficiency and reliability of laser welding systems also minimize downtime, further enhancing operational cost-effectiveness and reducing the total cost of ownership.
Increased Productivity
Laser welding machines are designed for high-speed, automated welding processes, which dramatically boost productivity compared to traditional methods. The ability to perform continuous welds with minimal interruptions allows manufacturers to meet tight production deadlines and increase output capacity. Automation capabilities, such as integration with robotic systems and automated control systems, further streamline production workflows and reduce reliance on manual labor. This increase in productivity helps businesses achieve faster turnaround times and improve their competitive edge.
Improved Quality of Welds
The precision and accuracy of laser welding technology result in consistently high-quality welds. Laser beams can be finely focused, allowing for narrow, deep welds with minimal heat-affected zones. This reduces distortion, warping, and material degradation often seen with traditional welding methods. The clean and strong welds produced by laser welding machines require less post-processing, such as grinding or smoothing, resulting in better product aesthetics and structural integrity. For industries that demand high standards, such as aerospace and medical device manufacturing, the superior weld quality provided by laser welding machines is a critical advantage.
Versatility and Flexibility
Laser welding machines are highly versatile and capable of joining a wide range of materials, including metals, alloys, and even dissimilar materials. They offer flexibility in terms of welding thicknesses, shapes, and complex geometries, making them suitable for a variety of applications across different industries. This versatility allows manufacturers to adapt to changing production needs without investing in additional equipment. Moreover, programmable control systems and software enable rapid reconfiguration and customization of welding parameters, enhancing adaptability for diverse production requirements.
The high cost of laser welding machines reflects their exceptional capabilities, long-term value, and ability to deliver superior performance in demanding industrial environments. By investing in laser welding technology, businesses gain access to cost savings, productivity gains, improved weld quality, and unparalleled versatility, making it a worthwhile investment for those seeking to stay ahead in a competitive market.
Market Dynamics of Laser Welding Machines
The market for laser welding machines is shaped by various dynamics, including supply and demand forces, competitive pressures, and rapid technological advancements. These factors play a significant role in influencing the cost of laser welding machines, reflecting their evolving value in the global manufacturing landscape.
Supply and Demand
The cost of laser welding machines is significantly influenced by market demand. As industries such as automotive, aerospace, electronics, and medical device manufacturing continue to grow and adopt laser welding technology, demand for these machines has risen steadily. However, laser welding remains a specialized market segment, often characterized by limited production volumes and high specialization. The availability of key components, such as high-powered lasers, precision optics, and advanced control systems, can further constrain supply, driving up costs. Additionally, fluctuations in global supply chains, particularly for specialized components or rare materials, can impact production costs and, ultimately, machine prices.
Competition in the Market
The laser welding market is highly competitive, and manufacturers are constantly working to develop innovative and efficient solutions to meet different industry needs. This competition fosters a push for technological improvements, such as increased power efficiency, better beam quality, and enhanced automation capabilities. While competition can lead to price reductions in certain areas, the investment in cutting-edge technology and high-quality components often drives prices upward. Additionally, newer entrants in the market may attempt to differentiate themselves through unique features or specialized applications, further shaping the competitive landscape.
Impact of Technological Advancements
Technological advancements have a profound impact on the cost and capabilities of laser welding machines. Innovations in laser sources, such as more efficient fiber lasers, have improved machine performance but also require significant research and development investment. Improvements in automation, real-time monitoring, and software-driven controls enhance machine precision and ease of use but increase complexity and cost. Additionally, the adoption of new manufacturing techniques and materials drives the need for continuous upgrades and adaptation, ensuring that machines remain at the cutting edge of technology. While these advancements offer greater value and capabilities, they also contribute to the higher cost of laser welding systems.
The market dynamics of supply and demand, competition, and ongoing technological innovation collectively shape the cost and value of laser welding machines. Maxcool CNC is at the forefront of this evolving market, providing high quality, technologically advanced solutions to meet the diverse needs of modern industry.
Summary
Laser welding machines represent a significant investment due to the advanced technology, precision engineering, and specialized components that go into their production. High costs stem from critical elements, including sophisticated laser sources, precision optics, cooling systems, and control software, all designed for exceptional performance. Additionally, extensive research and development, compliance with strict safety and regulatory standards, and comprehensive after-sales support contribute to their pricing. Market dynamics, such as supply and demand fluctuations, competition, and continuous technological advancements, further shape the cost landscape. Despite the high initial investment, laser welding machines offer long-term value through improved productivity, reduced operational costs, and superior weld quality. For industries prioritizing precision, speed, and versatility, the benefits of laser welding technology justify its expense and reflect its vital role in modern manufacturing.
Get Laser Welding Solutions
When investing in laser welding machines, choosing a trusted and experienced manufacturer is crucial for maximizing value and performance. Maxcool CNC is a professional leader in laser welding and cleaning technology, offering state-of-the-art solutions tailored to diverse industrial needs. Our laser welding machines are engineered for precision, efficiency, and durability, with advanced features such as high-powered laser sources, superior beam quality, and intuitive control systems. We understand that every industry has unique requirements, which is why we offer customizable solutions designed to optimize your production processes and deliver high-quality welds with minimal downtime.
Maxcool CNC also provides comprehensive support services, including installation, training, and maintenance, ensuring you have the knowledge and assistance needed to operate your machine effectively. By partnering with Maxcool CNC, you gain access to cutting-edge technology, reliable service, and a team dedicated to helping you achieve the highest standards of welding performance. Contact us today to explore our laser welding solutions tailored to your needs.