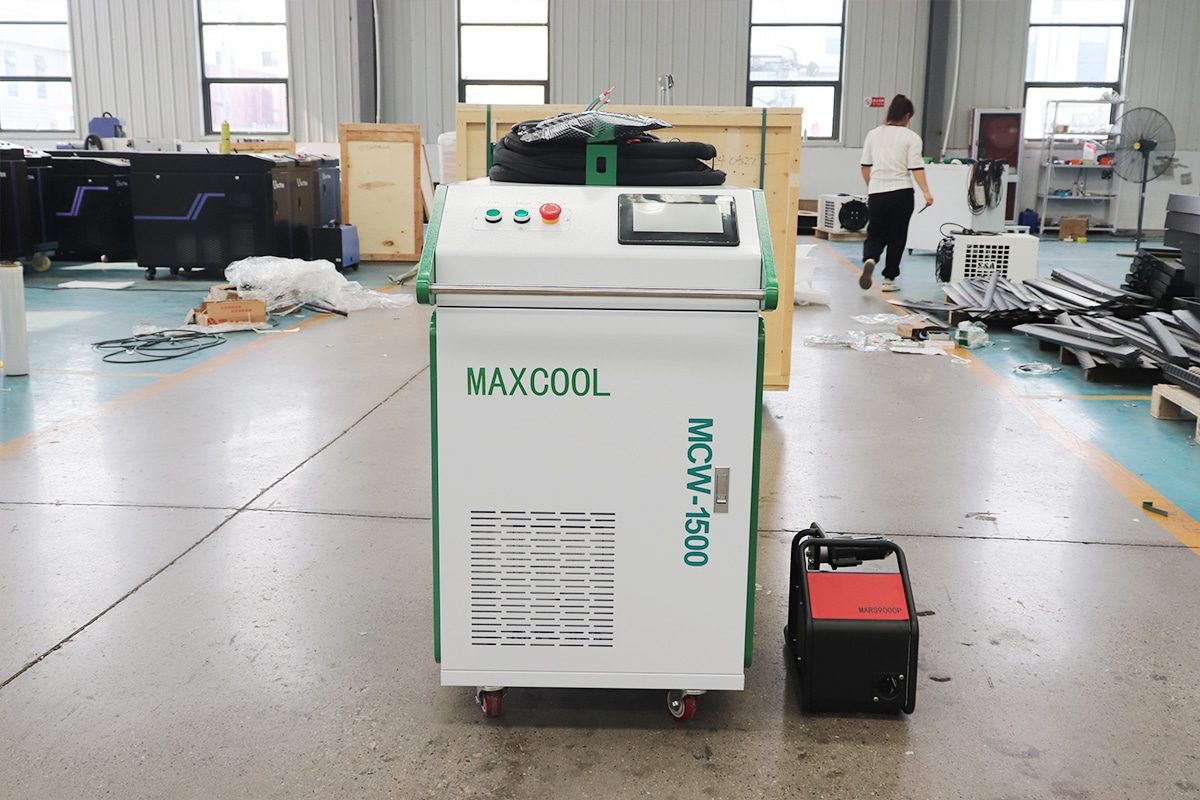
Understanding Laser Technology and Cleaning Principles
To effectively utilize laser cleaning technology, it is essential to understand the underlying principles of laser operation. Students should familiarize themselves with key laser concepts, including:
- Laser Physics: Understanding wavelength, power levels, beam intensity, and pulse duration.
- Mechanisms of Laser Cleaning: Learning how laser ablation removes contaminants such as rust, paint, grease, and oxidation while preserving the substrate.
- Types of Laser Cleaning Systems: Exploring pulsed vs. continuous-wave lasers and their respective applications.
- Comparison with Traditional Methods: Evaluating the efficiency, cost, and environmental benefits of laser cleaning versus chemical, abrasive, and ultrasonic methods.
Laser Safety Considerations
Working with high-powered lasers involves inherent risks, making safety knowledge a priority. Students should seek information on:
- Laser Classification & Risk Assessment: Understanding laser hazard levels (Class 1–4) and their safety implications.
- Personal Protective Equipment (PPE): Proper selection and usage of laser safety goggles, gloves, and protective clothing.
- Hazards & Precautions: Risks associated with direct beam exposure, reflections, and material interactions.
- Regulatory Compliance: Familiarity with OSHA, ANSI Z136.1, and local laser safety regulations.
- Emergency Procedures: Learning appropriate responses to accidental exposure, equipment malfunctions, and workplace hazards.
Understanding Machine Operation and Maintenance
Proper operation and maintenance of laser cleaning machines ensure optimal performance and longevity. Students should study:
- User Interface & Settings: Learning how to adjust laser power, pulse frequency, and scanning speed based on material type.
- Calibration & Focusing Techniques: Ensuring precise beam alignment to maximize efficiency and avoid material damage.
- Routine Maintenance: Understanding how to clean optical components, inspect cooling systems, and maintain power sources.
- Troubleshooting Common Issues: Recognizing signs of overheating, beam misalignment, and irregular cleaning patterns.
Workplace Safety and Emergency Preparedness
A structured safety approach is crucial in industrial laser applications. Students should explore:
- Workplace Safety Standards: Understanding best practices for setting up a secure laser cleaning environment.
- Fire & Fume Control: Implementing proper ventilation and fire suppression measures to handle contaminants released during cleaning.
- Electrical & Mechanical Safety: Understanding grounding techniques and precautions for handling high-voltage laser equipment.
- Emergency Protocols: Preparing for equipment failures, laser exposure incidents, and power disruptions.
Certification and Continuous Learning
As laser cleaning technology evolves, continuous education is essential. Students should explore:
- Industry Certifications: Pursuing certifications such as Laser Safety Officer (LSO) or manufacturer-specific training programs.
- Ongoing Training: Keeping up-to-date with new technologies, safety standards, and best practices through industry webinars, research papers, and trade conferences.
- Networking & Industry Engagement: Connecting with professionals and organizations to stay informed about advancements in laser cleaning applications.
Advanced Technical Knowledge
For those seeking deeper expertise, exploring advanced laser principles is beneficial. Key topics include:
- Material-Specific Parameter Optimization: Adjusting laser power, pulse duration, and beam profile based on material characteristics.
- Automated & Robotic Laser Cleaning: Understanding the integration of laser systems with robotic arms and CNC-controlled applications.
- Software & Process Control: Learning how modern software enhances laser precision, repeatability, and efficiency.
- Advanced Troubleshooting: Diagnosing complex laser system failures and implementing corrective measures.
Material-Specific Considerations
Different materials react differently to laser cleaning, requiring careful parameter adjustments. Students should study:
- Metals: Understanding how steel, aluminum, copper, and titanium interact with laser energy.
- Non-Metal Materials: Exploring the challenges of cleaning plastics, ceramics, and composite materials.
- Surface Coatings & Contaminants: Investigating laser techniques for removing paints, corrosion, oxidation layers, and industrial residues.
- Damage Prevention: Learning how to adjust settings to prevent surface warping, discoloration, or micro-cracking.
Industry-Specific Applications
Laser cleaning is utilized across various industries, each with unique requirements. Students should explore:
- Aerospace: Non-damaging cleaning of aircraft components, turbine blades, and composite materials.
- Automotive: Rust removal, paint stripping, and weld preparation for vehicle manufacturing.
- Manufacturing & Heavy Industry: Cleaning molds, precision tools, and production machinery.
- Electronics: Safe laser cleaning techniques for circuit boards and delicate electronic components.
- Marine & Shipbuilding: Removal of corrosion, marine growth, and coatings from ship structures.
- Energy Sector: Cleaning power plant components, pipelines, and renewable energy equipment.
- Historical & Cultural Conservation: Restoring statues, paintings, and artifacts using laser-based techniques.