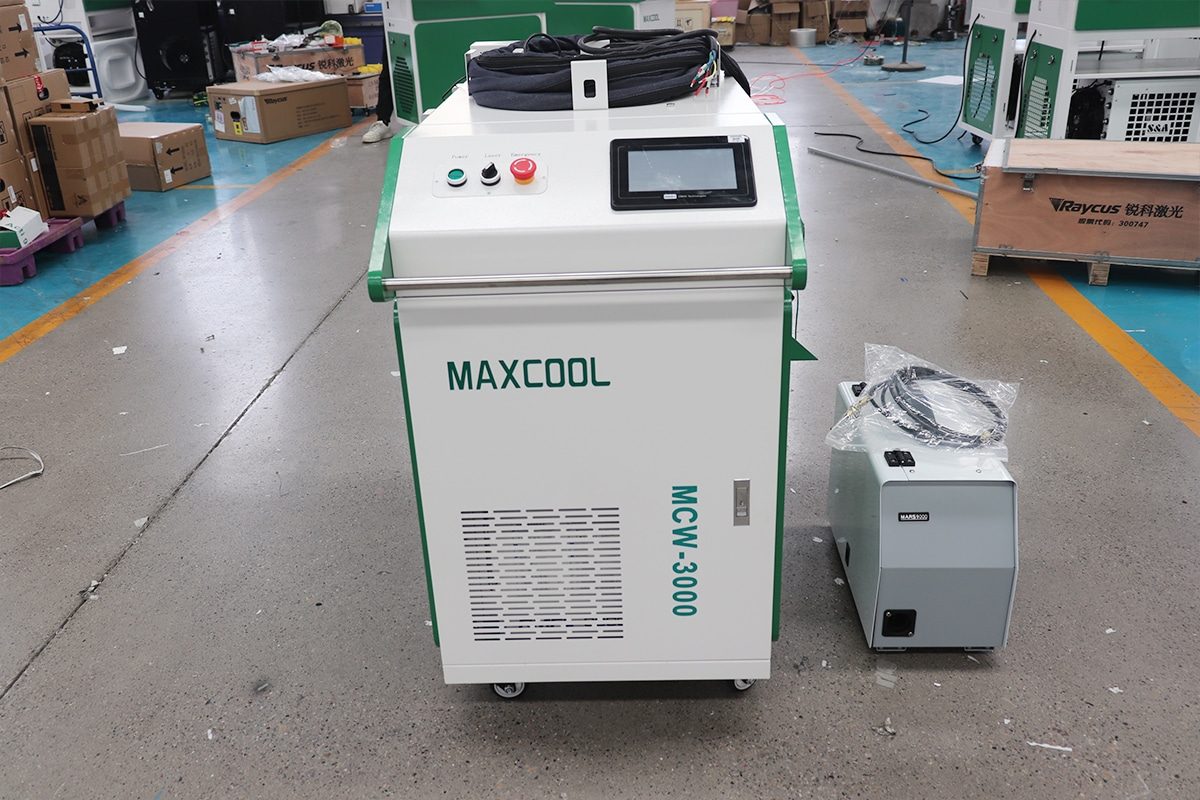
Understanding Laser Welding Machines
Factors Affecting the Cost of Operating Laser Welding Machines
Energy Consumption
Laser welding machines rely on significant electrical power to operate. The cost of electricity depends on machine power output and local rates:
- 1 kW Laser Welding Machines: Typically consume 4–6 kWh per hour, costing $0.40–$0.60 per hour based on average electricity rates ($0.10–$0.20 per kWh). With an 8-hour daily operation, this results in energy costs of $3.20–$4.80 per day or $8,000–$10,000 annually.
- 6 kW Laser Welding Machines: Higher-powered machines consume 20–25 kWh per hour, leading to annual energy costs of $15,000–$20,000, assuming similar operating hours.
Consumables
Consumables required for laser welding machines include shielding gases and protective components:
- Shielding Gases: Argon or nitrogen gases shield the weld from oxidation. A single cylinder costs $50–$100 and lasts about 8–10 hours of welding. For continuous daily use, monthly shielding gas expenses could range from $500 to $2,000, adding up to $6,000–$24,000 annually, depending on usage.
- Optics and Components: Protective lenses, nozzles, and mirrors degrade over time. Replacement costs range from $50 to $200 per item, typically replaced every 2–6 months, contributing an additional $1,000–$3,000 per year to consumables.
Maintenance and Repairs
Maintenance ensures a laser welding machine operates efficiently and prolongs its lifespan:
- Scheduled Maintenance: Includes cleaning optical components, calibrating the machine, and replacing minor parts. Costs per session range from $500 to $1,500, with 2–4 sessions annually.
- Repairs: Unscheduled repairs, such as replacing a damaged laser diode or fixing electronic boards, can cost anywhere from $2,000 to $10,000 per incident. Machines in heavy-use environments often experience higher repair needs.
Labor Costs
Labor costs depend on the level of automation and the expertise required to operate and oversee the machine:
- Operator Wages: Skilled operators earn $20–$35 per hour, equating to $160–$280 per day for an 8-hour shift. This translates to annual labor costs of $40,000–$70,000 per operator for a single machine.
- Automation: Fully automated systems reduce the need for manual intervention but still require supervision and periodic maintenance, adding to labor costs indirectly.
Depreciation
The initial cost of a laser welding machine ranges from $50,000 to $500,000. Over a typical lifespan of 7–10 years, depreciation accounts for 10%–20% of the machine’s value annually:
- A $100,000 machine depreciates by $10,000–$15,000 annually, while a $300,000 machine incurs depreciation costs of $30,000–$50,000 per year.
Training and Certification
Training and certification are essential to ensure operators can handle the machines effectively and safely:
- Training Costs: Programs range from $1,000 to $5,000 per operator, depending on their complexity. Advanced training for new technologies or certification upgrades may add to these expenses.
- Indirect Costs: Downtime during training reduces productivity, indirectly increasing the cost of operation.
Infrastructure and Utilities
Laser welding machines require supporting infrastructure to function efficiently:
- Cooling Systems: Water chillers or air conditioning units cost $1,000–$3,000 annually to operate.
- Ventilation: Proper exhaust systems, crucial for safety, incur installation costs of $5,000–$20,000 and recurring costs of $500–$1,500 per year.
- Power Stabilizers: Installation of stabilizers or backup power systems costs $2,000–$10,000 upfront, with minimal annual operational costs.
Operational Efficiency and Cost Optimization
Regular Maintenance
Proper maintenance is crucial for keeping laser welding machines in optimal working condition and avoiding costly downtime. Regular inspections and servicing ensure the machine operates at peak efficiency, extending its lifespan and reducing the likelihood of expensive repairs.
- Scheduled Inspections: Routine cleaning of optical components, calibration of laser settings, and lubrication of moving parts prevent wear and tear. Maintenance sessions, costing approximately $500–$1,500 per session, can save thousands by averting major breakdowns.
- Proactive Repairs: Addressing minor issues early, such as replacing worn lenses or filters, prevents these problems from escalating into costly failures.
Energy Optimization
Energy consumption is a significant contributor to the operating cost of laser welding machines. Optimizing energy use can significantly lower electricity bills without compromising productivity.
- Choosing Energy-Efficient Machines: Fiber lasers, for instance, are more energy-efficient compared to CO2 lasers, consuming up to 50% less power for equivalent tasks. Investing in energy-efficient technology reduces long-term energy expenses.
- Power Management: Machines can be programmed to operate at lower power levels when full capacity isn’t needed, minimizing waste. Implementing power-saving modes during idle periods can further decrease consumption.
- Facility Upgrades: Using energy-efficient infrastructure, such as voltage stabilizers and LED lighting in the workspace, helps reduce the overall energy demand.
Efficient Material Usage
Efficient use of materials during laser welding minimizes waste and reduces the need for expensive consumables.
- Precision Welding: Laser welding provides high accuracy, reducing material waste compared to traditional methods. Operators can fine-tune the laser beam’s intensity and focus to use only the necessary material for each weld.
- Recycling Materials: Scrap metal and excess materials generated during welding can often be recycled, offsetting the cost of raw materials.
- Optimizing Shielding Gas Usage: By calibrating the gas flow rate to match the specific welding task, businesses can reduce shielding gas consumption by up to 20%, lowering annual gas expenses significantly.
Automation Integration
Automation is a powerful tool for improving operational efficiency and reducing labor costs in laser welding processes.
- Robotic Welding Systems: Integrating robotic arms or automated gantry systems ensures consistent weld quality and reduces reliance on manual labor. While initial automation setup costs range from $20,000 to $100,000, the long-term savings in labor costs and productivity gains make this a worthwhile investment.
- Software Optimization: Advanced software allows machines to perform complex welding tasks with minimal human intervention. Features like predictive maintenance alerts and real-time monitoring ensure optimal performance, reducing downtime.
- Multi-Machine Control: Skilled operators can oversee multiple automated machines simultaneously, cutting labor costs and increasing throughput.
Cost Comparison with Traditional Welding
When comparing the costs of laser welding machines with traditional welding methods like MIG, TIG, or arc welding, it’s important to consider both the upfront investment and the long-term operating expenses. While laser welding machines have a higher purchase price, their efficiency and lower running costs often make them a better choice over time.
- Initial Investment: Laser welding machines typically cost between $4,000 and $50,000, while traditional welding machines range from $1,000 to $10,000. Although the initial cost of laser welding is higher, its advanced capabilities and efficiency can offset this over time.
- Energy Costs: Laser welding machines, especially fiber lasers, are highly energy-efficient, consuming 20%–50% less electricity than traditional welding machines. This means lower energy bills, especially in high-production settings.
- Consumables: Laser welding requires fewer consumables, such as shielding gases and protective optics, costing about $1,000–$3,000 annually. Traditional welding relies on more consumables, like electrodes and filler materials, leading to higher annual costs of $5,000–$15,000.
- Maintenance: Laser welding machines need regular maintenance, costing $2,500–$6,000 annually, but they are durable and require fewer repairs. Traditional welding machines may have lower per-repair costs but require frequent replacements of parts like nozzles and tips, adding up to $3,000–$8,000 annually.
- Labor Costs: Laser welding machines can be automated, reducing the need for manual labor. A single operator can manage multiple machines, lowering labor costs. Traditional welding often requires one operator per machine, leading to higher labor expenses over time.
- Speed and Quality: Laser welding is faster and more precise, reducing production time and the need for rework. Traditional welding methods are slower and may result in more material waste or post-weld cleaning requirements, which add to overall costs.