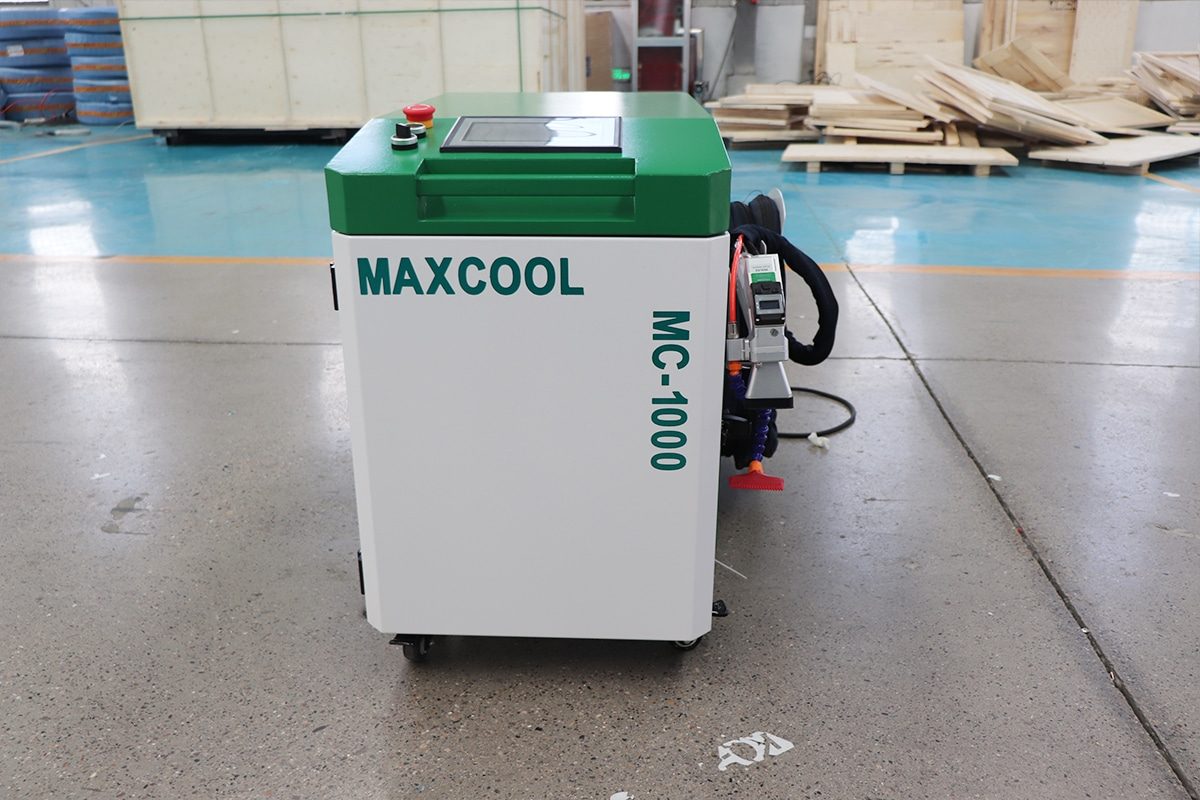
Understanding Laser Cleaning Machines
What Are Laser Cleaning Machines?
Core Components of a Laser Cleaning Machine
The performance and life expectancy of a laser cleaning machine depend on its core components, each playing a critical role in its operation. These components include:
- Laser Source: The laser source is the heart of the cleaning machine, generating the high-energy beams used for cleaning. Most laser cleaning machines use fiber lasers due to their efficiency, durability, and precision. Fiber lasers typically have a long lifespan, often exceeding 50,000 operational hours, making them a reliable choice for industrial applications.
- Optical System: The optical system includes lenses, mirrors, and delivery mechanisms that focus and direct the laser beam onto the surface to be cleaned. High-quality optical components ensure accurate beam delivery and minimize energy loss, contributing to the machine’s overall efficiency. Proper maintenance of these components is essential to avoid wear and ensure longevity.
- Cooling System: Laser cleaning generates significant heat, requiring an efficient cooling system to maintain stable operation. These systems use air or liquid cooling to dissipate heat from the laser source and optical components, preventing overheating and extending the machine’s life. Regular servicing of the cooling system is vital to avoid thermal stress-related damage.
- Control System: The control system manages the operation of the laser cleaning machine, including power settings, pulse frequency, and beam intensity. Advanced control systems often feature intuitive software interfaces, allowing operators to customize settings for different materials and cleaning requirements. Regular updates and calibration of the control system are essential to maintain peak performance.
- Protective Housing and Safety Features: To ensure operator safety and machine durability, laser cleaning machines are equipped with protective housing and safety mechanisms. These include enclosures that prevent exposure to laser radiation, emergency shut-off systems, and interlocks that stop the laser if the housing is opened. High-quality protective features enhance both safety and the machine’s longevity.
Factors Affecting the Life Expectancy of Laser Cleaning Machines
Quality of Components
The quality of components used in a laser cleaning machine is the most significant factor influencing its life expectancy. Machines built with high-grade materials and precision-engineered parts are generally more durable and reliable. Key components include:
- Laser Source: High-quality laser sources, such as fiber lasers, are known for longevity, often exceeding 50,000 operational hours. Inferior laser sources may degrade faster, reducing performance and lifespan.
- Optics: Premium lenses and mirrors ensure efficient laser beam delivery and resist wear over time. Poor-quality optics are prone to scratches and misalignment, leading to frequent replacements.
- Cooling Systems: Reliable cooling systems maintain consistent operating temperatures, preventing thermal stress that can damage the laser source and other components.
Frequency and Intensity of Use
The operational load on a laser cleaning machine significantly affects its lifespan. Machines that are used heavily or operated at maximum intensity for prolonged periods are subject to increased wear and tear. Key considerations include:
- Operating Hours: Machines used continuously for multiple shifts will experience faster degradation compared to those used intermittently.
- Cleaning Intensity Settings: Operating the machine at maximum laser intensity or power for extended durations can strain the laser source and other components.
Maintenance Practices
Proper maintenance is essential to keep a laser cleaning machine functioning efficiently over its expected lifespan. Neglecting routine upkeep can lead to premature failure of components and costly downtime. Essential maintenance practices include:
- Regular Cleaning: Removing dust, debris, and contaminants from optical components and other parts prevents performance issues.
- System Inspections: Periodic checks ensure that components like cooling systems, lenses, and control panels are in optimal condition.
- Timely Replacement of Consumables: Filters in cooling systems and worn-out optical parts should be replaced promptly to avoid cascading damage.
- Software Updates and Calibration: Keeping the control system updated ensures accurate and efficient machine operation.
Environmental Conditions
The environment in which a laser cleaning machine operates plays a critical role in its durability. Harsh or unsuitable conditions can accelerate wear and reduce lifespan. Factors to consider include:
- Temperature and Humidity: Excessive heat or humidity can strain the cooling system and other components. Maintaining a stable environment with controlled temperature and humidity levels is essential.
- Dust and Contaminants: Operating in dusty or dirty environments can clog cooling systems, damage optical components, and compromise overall machine performance. Protective measures, such as enclosures and air filtration systems, can mitigate these risks.
- Vibrations and Shocks: Machines installed in environments with high vibrations or physical shocks may experience faster mechanical degradation.
Operator Expertise
The expertise of the operator is often an overlooked yet vital factor in determining the lifespan of a laser cleaning machine. Skilled operators can maximize efficiency while minimizing wear, whereas untrained personnel may inadvertently cause damage. Key considerations include:
- Proper Operation: Knowledge of machine settings and recommended usage guidelines prevents unnecessary strain on components.
- Error Prevention: Trained operators are less likely to make mistakes that could result in costly repairs or downtime.
- Preventive Measures: Experienced users can identify potential issues early and take corrective action before significant damage occurs.
Typical Life Expectancy of Key Components
Laser Source
The laser source is the most critical and durable component in a laser cleaning machine. Most modern machines use fiber lasers, known for their exceptional longevity and efficiency.
- Typical Lifespan: Fiber lasers typically last between 50,000 to 100,000 operational hours, depending on their quality and usage conditions. Diode lasers, another common type, may have slightly shorter lifespans but still offer excellent durability.
- Factors Affecting Lifespan: Consistent maintenance, avoiding overuse, and operating the laser within its recommended power settings are crucial to maximizing its lifespan.
- Signs of Wear: Decreasing beam quality or inconsistent output power often indicates that the laser source is nearing the end of its lifespan.
Optical and Delivery System
The optical and delivery system includes lenses, mirrors, and delivery fibers that direct the laser beam to the target surface. These components are highly sensitive and require careful handling to ensure longevity.
- Typical Lifespan: Depending on usage and environmental conditions, optical components can last between 5,000 to 20,000 operational hours. Delivery fibers may last longer, often aligning with the lifespan of the laser source.
- Factors Affecting Lifespan: Regular cleaning to remove dust and contaminants, avoiding scratches during handling, and preventing misalignment are essential to maintaining these components.
- Signs of Wear: Reduced precision, energy loss, or visible damage to lenses and mirrors are common signs that the optical system needs replacement or repair.
Cooling System
The cooling system prevents overheating of the laser source and other components, ensuring consistent performance and protecting the machine from thermal damage. Cooling systems are typically air-based or liquid-based.
- Typical Lifespan: A well-maintained cooling system can last between 5 to 10 years, depending on the type and quality.
- Factors Affecting Lifespan: Regular replacement of filters, cleaning of heat exchangers, and monitoring for leaks or blockages are critical to prolonging the cooling system’s lifespan.
- Signs of Wear: Ineffective cooling, rising operating temperatures, or unusual noises often indicate the need for servicing or replacement.
Control Systems and Software
The control systems and software act as the brains of the machine, regulating laser output, adjusting cleaning settings, and ensuring safe operation.
- Typical Lifespan: While the hardware in control systems can last 10 to 15 years, the software may require updates every few years to maintain compatibility and optimize functionality.
- Factors Affecting Lifespan: Regular software updates, proper storage conditions, and protecting the control system from electrical surges are key to maintaining its performance.
- Signs of Wear: Delayed responses, inaccurate settings, or software malfunctions indicate potential issues with the control system.
Protective Housing and Safety Features
The protective housing and safety features shield the machine from external damage and ensure operator safety during operation. These include enclosures, interlocks, and emergency shut-off mechanisms.
- Typical Lifespan: High-quality protective housing can last the entire lifetime of the machine, often exceeding 10 to 15 years, provided it is not subjected to excessive physical damage.
- Factors Affecting Lifespan: Avoiding exposure to corrosive environments, regular cleaning, and inspecting safety mechanisms are crucial to maintaining these features.
- Signs of Wear: Visible damage, loose connections, or malfunctioning safety interlocks should be addressed immediately to ensure continued safe operation.
Prolonging the Life Expectancy of Laser Cleaning Machines
Preventive Maintenance
Routine maintenance is critical to the longevity of any machinery, and laser cleaning machines are no exception. Preventive maintenance ensures that all components operate efficiently and minimizes the risk of unexpected failures.
- Regular Cleaning: Dust, dirt, and debris can accumulate on optical components, cooling systems, and protective housings. Regular cleaning prevents damage and ensures consistent performance.
- System Inspections: Periodic inspections help identify potential issues, such as worn lenses, misaligned optics, or cooling system inefficiencies, before they escalate into costly repairs.
- Consumable Replacements: Replace consumables, such as cooling system filters or worn optics, on schedule to avoid strain on the machine.
- Software Updates: Keep control systems up to date with the latest software versions to maintain optimal performance and security.
Proper Usage Guidelines
Operating laser cleaning machines within their recommended parameters is crucial to preventing unnecessary wear and tear. Improper usage can lead to premature failure of components.
- Adhere to Manufacturer Instructions: Always follow the manufacturer’s guidelines for operating power, cleaning settings, and cooling requirements.
- Avoid Overuse: Allow the machine sufficient rest between intensive operations to prevent overheating and reduce strain on the laser source.
- Monitor Machine Performance: Pay attention to performance metrics and address irregularities promptly to avoid long-term damage.
Environmental Optimization
The environment in which a laser cleaning machine operates plays a significant role in its longevity. Unfavorable conditions can accelerate wear and impact performance.
- Temperature and Humidity Control: Maintain stable environmental conditions, as extreme temperatures or high humidity can strain the cooling system and electronics.
- Clean Workspace: Minimize exposure to dust, debris, and contaminants by keeping the workspace clean. This reduces the likelihood of particles entering the machine and damaging internal components.
- Protect from Vibrations: Install the machine in a stable location to avoid mechanical stress caused by vibrations or shocks.
Training and Certification for Operators
The expertise of operators significantly impacts the lifespan of laser cleaning machines. Proper training ensures that machines are handled correctly, minimizing the risk of damage from user errors.
- Professional Training Programs: Provide operators with comprehensive training on machine operation, maintenance, and troubleshooting.
- Certification Requirements: Encourage certification to ensure operators have a deep understanding of the equipment and can safely and effectively manage it.
- Regular Refresher Courses: Offer periodic training sessions to keep operators updated on the latest technologies and best practices.
Manufacturer Support and Warranty Services
Partnering with a reputable manufacturer, such as Maxcool CNC, provides access to essential support services that can enhance the longevity of laser cleaning machines.
- Warranty Coverage: Take advantage of warranty programs to address defects or failures during the initial years of operation without incurring additional costs.
- Maintenance Packages: Many manufacturers offer comprehensive maintenance and service packages, including scheduled inspections, part replacements, and software updates.
- Technical Support: Access to technical assistance ensures timely resolution of issues and reduces downtime.
- Genuine Replacement Parts: Use manufacturer-recommended parts and consumables to maintain compatibility and performance.
Cost Implications of Life Expectancy
Initial Investment vs. Long-Term Value
Laser cleaning machines represent a substantial upfront investment, often costing tens of thousands of dollars depending on their power and capabilities. However, their long-term value is directly tied to their life expectancy.
- High-Quality Machines: Machines from reputable manufacturers, like Maxcool CNC, may have a higher initial cost but offer extended lifespans due to superior components and build quality.
- Cheaper Alternatives: Lower-cost machines may seem attractive initially but often come with shorter lifespans and higher maintenance needs, leading to greater expenses over time.
Maintenance Costs Over Time
The maintenance requirements of a laser cleaning machine grow as it ages. While routine maintenance can prevent major issues, older machines may incur higher costs due to wear and tear on critical components.
- Preventive Maintenance Savings: Regular upkeep, such as cleaning optics, replacing filters, and updating software, is a relatively low-cost way to extend the machine’s life.
- Component Replacements: As machines age, replacing components like laser sources, cooling systems, or optical parts becomes necessary. These replacements can be expensive and should be planned for in the operational budget.
- Downtime Costs: Poorly maintained machines may fail unexpectedly, leading to costly downtime and disruptions to operations.
Return on Investment (ROI) Analysis
The lifespan of a laser cleaning machine directly affects its ROI. Machines with longer lifespans allow businesses to maximize their usage and generate more value from the initial investment.
- Amortization of Costs: A machine that lasts 10 to 15 years spreads its initial cost over more years, reducing the annual expense compared to a machine that lasts only 5 to 7 years.
- Increased Productivity: Longer-lasting machines enable consistent performance, allowing businesses to take on more projects and increase revenue without frequent interruptions for repairs or replacements.
- Value Retention: Machines with longer lifespans tend to retain more value if resold or traded in for an upgrade, further enhancing ROI.
Cost of Repairs vs. Replacement
Over time, the cost of repairs for an aging machine can rival or exceed the cost of purchasing a new one. Businesses must weigh the cost of maintaining an older machine against the benefits of investing in a new model.
- Repair Threshold: When repair costs approach 50-70% of the cost of a new machine, replacement may be the more economical choice.
- Upgrading to New Technology: Investing in a newer machine with advanced features and improved efficiency may provide greater cost savings in the long term, especially if the older machine requires frequent repairs.
Operational Efficiency and Cost Savings
Laser cleaning machines with longer lifespans tend to maintain higher operational efficiency, reducing overall costs in several ways:
- Reduced Consumable Use: High-quality machines are designed to minimize the consumption of energy and ancillary materials, translating to lower operational costs over time.
- Minimized Downtime: Reliable machines experience fewer breakdowns, ensuring consistent operation and avoiding productivity losses.
- Sustainability Savings: Longer-lasting machines reduce the frequency of replacements, aligning with sustainability goals and reducing waste.
Warranty and Support Considerations
Investing in machines with comprehensive warranties and manufacturer support can significantly reduce long-term costs associated with repairs and maintenance.
- Warranty Coverage: Machines covered under warranty for a substantial portion of their expected lifespan minimize out-of-pocket repair costs.
- Manufacturer Support Packages: Services like extended warranties, annual maintenance contracts, and technical support reduce the financial burden of upkeep.