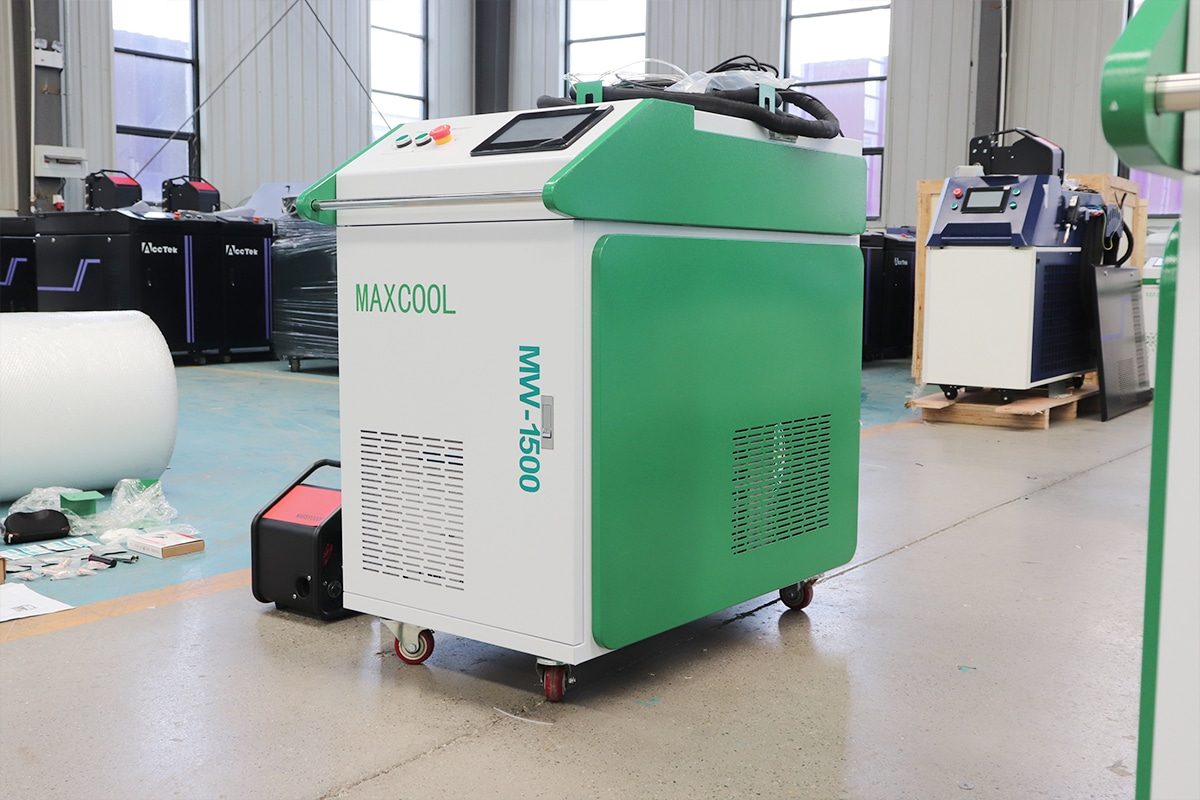
What Is the Cost of Laser Welding Machines?
In recent years, laser welding machines have become an indispensable tool in various industries, from automotive manufacturing and aerospace to electronics and heavy-duty industrial production. These machines offer unparalleled precision, speed, and versatility, making them the top choice for businesses aiming to improve their welding operations. However, purchasing a laser welding machine represents a significant investment, with costs that vary depending on machine type, power level, features, and manufacturer.
This article provides an exhaustive exploration of the cost of laser welding machines with power outputs between 1kW and 3kW (1000W, 1500W, 2000W, and 3000W). We will examine the technology behind laser welding, provide a breakdown of the factors influencing costs, compare laser welding with traditional welding methods, and explore the long-term return on investment (ROI) these machines offer. This comprehensive guide will assist businesses in understanding the costs and benefits of laser welding machines, enabling informed decision-making.
Table of Contents
Overview of Laser Welding Technology
Laser welding is a process that uses a highly focused laser beam to heat and melt materials, allowing them to fuse. Unlike traditional welding methods, which rely on an external heat source, laser welding uses concentrated energy to generate heat at the precise point where the materials are joined. This results in a smaller heat-affected zone, which minimizes material deformation and improves the overall quality of the weld.
Fiber laser welding is one of the most widely used types of laser welding, known for its efficiency, versatility, and precision. It uses a fiber optic cable to deliver the laser beam, providing superior beam quality and high energy efficiency. Fiber lasers are especially suitable for high-speed, automated welding processes, making them ideal for industrial applications that require precision and consistency.
Key Advantages of Fiber Laser Welding
- High Precision: The laser beam can be precisely controlled, allowing for tight tolerances and minimal post-weld finishing.
- Speed: Laser welding is faster than most traditional welding techniques, increasing production output and reducing labor costs.
- Minimal Heat-Affected Zone (HAZ): The concentrated nature of the laser beam results in a smaller HAZ, reducing material distortion and warping.
- Versatility: Fiber lasers can weld a wide variety of metals and alloys, making them suitable for multiple industries and applications.
- Automation Integration: Fiber laser welding systems can be easily integrated with CNC machines and robotic arms, making them ideal for automated production lines.
Types of Laser Welding Machines
Laser welding machines come in various configurations depending on the intended use, scale of production, and desired level of automation. When considering a purchase, businesses typically choose between automatic and handheld laser welding machines, each offering different advantages.
Automatic Laser Welding Machines
Automatic laser welding machines are designed for large-scale industrial operations where speed, precision, and automation are critical. These machines are often integrated with robotic systems and CNC controls, enabling them to perform highly accurate and repeatable welds. Automatic machines are used in high-volume production environments where consistency and efficiency are paramount.
Price Range: $30,000 to $80,000, depending on power level, automation features, and brand.
Advantages
- High Productivity: Automatic machines can run continuously, maximizing production output in high-volume environments.
- Consistency and Precision: Automation ensures that each weld is identical, reducing human error and ensuring high-quality results.
- Advanced Capabilities: Automatic machines often feature multi-axis welding and customizable settings, allowing them to handle more complex welding tasks.
Applications
- Automotive Manufacturing: Ideal for welding car frames, exhaust systems, and other parts that require precise, high-speed welding.
- Aerospace Industry: Used to weld high-strength materials like aluminum and titanium for aircraft parts.
- Heavy-Duty Industrial Fabrication: Suitable for welding thick metal plates used in shipbuilding, construction, and heavy machinery.
Handheld Laser Welding Machines
Handheld laser welding machines are more portable and versatile than automatic systems. These machines are used in small-to-medium-sized workshops and by businesses that require flexibility. Handheld machines offer precise control, making them ideal for on-site repairs and custom welding tasks that require manual oversight.
Price Range: $3,000 to $7,500, depending on the machine’s power output and additional features such as cooling systems or automation options.
Advantages
- Portability: Handheld machines allow for mobility and can be used in various locations, including remote job sites.
- Flexibility: These machines can handle a range of materials and are suitable for both small production tasks and repair work.
- Lower Cost: Handheld fiber laser welders are generally less expensive than automatic machines, making them accessible to smaller businesses.
Applications
- Metal Fabrication: Suitable for welding small metal components and structures in custom workshops or fabrication shops.
- On-Site Repairs: Ideal for welding tasks that need to be performed in the field, such as repairing machinery, metal structures, or piping systems.
- Custom Manufacturing: Useful for small-batch production where manual control and precision are required.
Cost Breakdown for Laser Welding Machines
The price of a laser welding machine can vary depending on several factors. While power level is a major determinant, other factors such as machine features, brand reputation, and additional systems (such as cooling and automation) significantly impact the overall cost. Below is a detailed breakdown of the factors that contribute to the pricing of laser welding machines.
Power Output
The power output of a laser welding machine is one of the most significant factors influencing its price. Higher-powered machines can handle thicker materials, weld at faster speeds, and are generally more expensive due to their enhanced capabilities.
- 1kW (1000W): Suitable for light-duty tasks such as welding thin metals and small components. Price Range: $3,000 to $3,500.
- 5kW (1500W): A versatile option for small to medium-sized production tasks, balancing power and precision. Price Range: $3,500 to $4,000.
- 2kW (2000W): Designed for medium-duty industrial applications, including automotive parts manufacturing and metal fabrication. Price Range: $4,500 to $5,500.
- 3kW (3000W): Built for heavy-duty applications such as shipbuilding and large-scale metal fabrication. Price Range: $6,500 to $7,500.
Machine Features
Additional features can significantly increase the cost of a laser welding machine. Common features that impact pricing include:
- CNC Automation: Machines with CNC control systems provide precision and automation, reducing the need for manual labor and increasing productivity. However, these systems come at a premium.
- Cooling Systems: Machines with water-cooling systems are more expensive but are essential for high-volume, continuous operation to prevent overheating and ensure consistent performance.
- Multi-Axis Capability: Machines equipped with multi-axis welding heads allow for more complex welding tasks, adding to the overall cost.
- Robotic Integration: Advanced machines integrated with robotic arms enable fully automated, multi-axis welding. While more expensive, these systems provide significant savings in labor costs and improve production efficiency.
Brand and Manufacturer
The reputation and reliability of the manufacturer also influence the price of a laser welding machine. Well-known brands with a proven track record of delivering high-quality machines often charge a premium for their products. These brands, such as IPG Photonics, Raycus, and MAX Laser, offer machines that are more durable, and efficient, and come with robust after-sales support and warranties.
Maintenance and Operating Costs
In addition to the initial purchase price, businesses should consider the ongoing costs associated with operating and maintaining a laser welding machine. These costs include:
- Power Consumption: Higher-powered machines consume more electricity, leading to higher operational costs, especially in high-volume production settings.
- Consumables: Over time, certain components such as lenses, protective windows, and nozzles will need to be replaced, adding to long-term maintenance expenses.
- Training and Setup Costs: Many manufacturers offer operator training and installation services, which may incur additional costs but are essential for ensuring the machine’s optimal performance.
Cost VS. Traditional Welding Methods
Laser welding machines are more expensive than traditional welding machines such as TIG (Tungsten Inert Gas), MIG (Metal Inert Gas), SMAW (Shielded Metal Arc Welding), and FCAW (Flux-Cored Arc Welding). However, laser welding offers significant advantages that often justify the higher cost.
Laser Welding
Advantages
- High precision and speed.
- Minimal heat-affected zones and material distortion.
- Can weld a wide range of materials, including dissimilar metals.
- Automation-ready for high-volume production.
Disadvantages
- Higher initial cost.
- Requires specialized training for operators.
- Limited in applications involving very thick materials compared to some traditional methods.
TIG Welding (Tungsten Inert Gas)
Advantages
- Excellent control over the welding process.
- Produces high-quality, clean welds.
- Suitable for thin materials and critical applications.
Disadvantages
- Slow process compared to laser welding.
- Requires highly skilled operators.
- Typically used in small-scale production.
MIG Welding (Metal Inert Gas)
Advantages
- Fast and easy to learn.
- Suitable for thick materials and high-speed applications.
- Lower equipment cost than laser welding.
Disadvantages
- Less precise than laser welding.
- Higher levels of heat-affected zones and material distortion.
- Requires post-weld cleaning in some cases.
SMAW Welding (Stick Welding)
Advantages
- Versatile and can be used in outdoor settings.
- Lower cost and simple equipment.
- Ideal for thick materials and heavy industrial work.
Disadvantages
- Produces rougher welds that require post-processing.
- Less precise than laser welding.
- Slower welding speed.
FCAW Welding (Flux-Cored Arc Welding)
Advantages
- High deposition rates, which make it faster than TIG or MIG.
- Can be used outdoors, even in windy conditions.
- Suitable for thicker materials and high-speed applications.
Disadvantages
- Less precise than laser welding.
- Requires post-weld cleaning due to slag formation.
- More material waste compared to laser welding.
Long-Term Value and Return on Investment (ROI)
Despite the higher upfront costs, laser welding machines offer significant long-term value, particularly in terms of increased productivity, reduced labor costs, and material savings. Many businesses that invest in laser welding technology report a positive return on investment (ROI) over time.
Factors Contributing to Long-Term Value
- Increased Productivity: The faster welding speeds of laser machines enable businesses to produce more in less time, leading to higher output and efficiency.
- Labor Savings: Automation features such as robotic arms and CNC control reduce the need for manual labor, lowering operational costs over time.
- Material Savings: The precision of laser welding reduces material waste, particularly when working with expensive metals like aluminum, stainless steel, and titanium.
- Improved Product Quality: Consistent, high-quality welds result in fewer defects and rework, improving overall production quality and customer satisfaction.
ROI Considerations
- Production Volume: Businesses with high production volumes or demanding precision tasks are more likely to see a faster return on their investment in a laser welding machine.
- Labor Cost Reduction: The automation capabilities of laser welding machines can significantly reduce the need for skilled welders, contributing to long-term labor cost savings.
How to Choose the Right Laser Welding Machine
When selecting a laser welding machine, businesses should carefully assess their production needs, long-term goals, and budget constraints. Here are some key factors to consider:
Assess Your Production Needs
- Material Thickness: Choose a machine with the appropriate power level based on the thickness of the materials you need to weld. Thicker materials require higher power outputs (2kW to 3kW), while thinner materials can be handled by lower-powered machines (1kW to 1.5kW).
- Production Volume: If your business requires high-volume production, investing in an automatic machine with CNC automation and robotic arms may be a better long-term investment.
Consider the Features You Need
- Automation: For businesses looking to maximize efficiency and precision, investing in a machine with CNC control or robotic integration can improve productivity but will increase the cost.
- Portability: If your business requires flexibility, a handheld laser welding machine may be the right choice. These machines are ideal for on-site repairs and custom tasks that demand manual control.
Budget Considerations
- Upfront Costs vs. Long-Term ROI: While laser welding machines have higher initial costs, consider the long-term savings in labor, material waste, and increased production efficiency.
- Maintenance and Operating Costs: Don’t forget to factor in the ongoing costs of maintenance, power consumption, and consumables when calculating the total cost of ownership.
Brand and After-Sales Support
- Reputation Matters: Choose a reputable brand with a proven track record for quality and reliability. Established manufacturers like IPG Photonics, Raycus, and MAX Laser offer machines with strong warranties and reliable after-sales support.
Summary
Investing in a laser welding machine is a significant decision for any business. Machines with power levels between 1kW and 3kW are highly versatile, offering solutions for both light-duty and heavy-duty applications. While these machines come with higher upfront costs compared to traditional welding systems, the long-term benefits of increased productivity, reduced labor costs, and improved product quality often make them a worthwhile investment.
By understanding the factors that influence the cost of laser welding machines, such as power output, machine features, and brand reputation, businesses can make informed decisions that maximize their return on investment. Whether you need an automatic system for high-volume production or a handheld machine for flexible, on-site welding, laser welding technology offers the precision, speed, and efficiency necessary to stay competitive in today’s demanding industrial landscape.