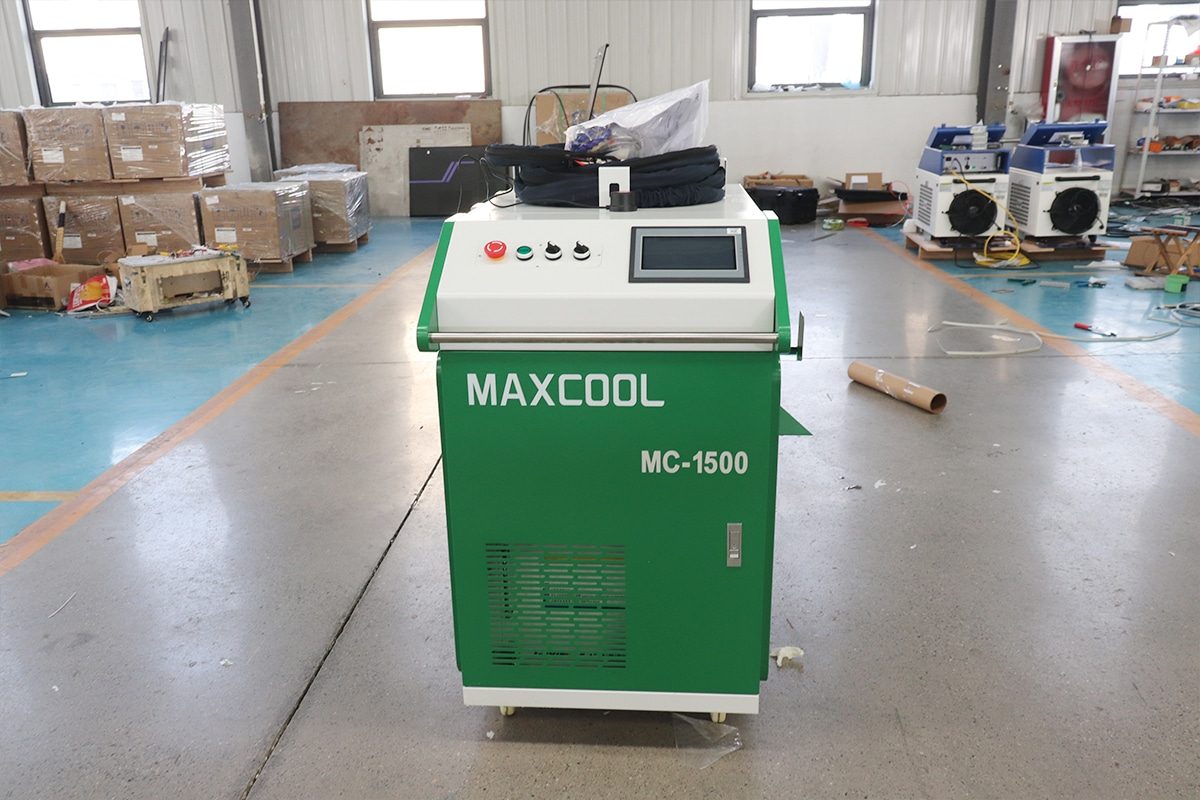
What Is Pulse Laser Cleaning?
Over the last few decades, laser technology has evolved into a sophisticated toolkit that encompasses a wide range of applications—from medical procedures and scientific research to manufacturing and materials processing. Among these applications, pulse laser cleaning has emerged as a remarkable technique for surface preparation, paint and oxide removal, restoration of priceless artifacts, and more. Pulse laser cleaning involves the use of short, high-intensity bursts of laser light to remove surface contaminants or unwanted coatings without causing damage to the underlying material.
In an era of increasingly stringent environmental regulations and growing demand for efficient, precise, and eco-friendly cleaning methods, pulse laser cleaning stands out as a revolutionary solution. Although it has been in development for some time, continuous research and technological improvements have enhanced its capabilities, extending its potential for broader industrial and cultural heritage applications. This article delves deeply into the realm of pulse laser cleaning, examining both the fundamentals of how pulse lasers interact with materials and the real-world benefits and challenges associated with adopting this technology.
Table of Contents
Fundamentals of Lasers and Laser-Material Interactions
Laser Basics
A laser (Light Amplification by Stimulated Emission of Radiation) is a device that emits coherent light. Unlike ordinary light sources, which emit light in many directions and at various wavelengths, lasers produce a beam of light that is monochromatic (single wavelength or narrow band of wavelengths), coherent (all waves are in phase), and highly collimated (able to remain tightly focused over long distances).
Key components of a laser include:
- Active medium: Could be a solid (e.g., Nd:YAG), a gas (e.g., CO₂), or a fiber doped with rare-earth elements.
- Energy source or pump: Supplies energy to excite the active medium.
- Optical resonator: Typically formed by a pair of mirrors, helping to amplify light within the cavity and produce the output beam.
Laser Wavelengths and Material Response
Different laser sources emit light at different wavelengths—Nd:YAG lasers often operate at 1064 nm, while fiber lasers can operate anywhere from around 200 nm up to 2 µm, depending on their design. The wavelength largely determines how a material will absorb or reflect the laser energy. Materials with higher absorption at a given wavelength will more readily convert the incoming light into heat or facilitate photochemical reactions. In the context of pulse laser cleaning, understanding the absorption spectrum of the substrate and the contaminant is essential for an effective and safe cleaning process. Ideally, the contaminant should absorb more of the laser energy than the substrate, so the contaminant is removed without harming the underlying material.
What Makes a Laser “Pulse”
A pulse laser does not emit a continuous beam but rather delivers laser energy in discrete bursts or pulses. Pulse durations can range from nanoseconds (10⁻⁹ seconds) to femtoseconds (10⁻¹⁵ seconds) in ultrafast laser systems. In cleaning applications, nanosecond or picosecond pulse lasers are commonly used. These short pulses deliver extremely high peak power for a brief moment, causing an intense interaction with contaminants or surface films. Pulse lasers are thus highly suited to processes like ablation, where precise material removal is desired without significant thermal conduction into the substrate.
Pulse Laser Cleaning
Definition and Core Principles
Pulse laser cleaning is a surface-cleaning process that relies on a pulse laser beam to remove contaminants, rust, paint, oxide films, and other unwanted materials from a substrate. The foundation of this process lies in the difference in absorption properties and the controlled application of very short bursts of high-intensity light. When the laser is directed onto the surface, the contaminants—often more absorptive—heat up rapidly. This leads to a quick and localized vaporization, sublimation, or spallation of the contaminant layer, effectively lifting it off without imposing significant thermal stress on the base material.
Physical Mechanisms of Pulse Laser Cleaning
Two main physical mechanisms are frequently cited in pulse laser cleaning:
- Photothermal Ablation: The contaminant or coating absorbs the laser radiation and is rapidly heated to temperatures high enough to vaporize or decompose it. The high temperature attained happens in such a short timescale that the energy transfer to the substrate is limited, preserving the underlying material.
- Photomechanical Ablation: When the absorption is extremely fast, the heated layer can expand rapidly, generating acoustic or shock waves that break away the contaminant from the substrate. These shock waves can help lift off the particles and materials without necessarily vaporizing everything.
Pulse duration, laser fluence, and material absorption all interact to determine the balance between these two mechanisms. Many laser cleaning processes exhibit a combination of photothermal and photomechanical ablation.
Comparison with Continuous-Wave Laser Cleaning
While it is possible to clean surfaces with continuous-wave (CW) lasers, pulse lasers often provide a superior level of control and efficiency. CW lasers deliver a steady beam, making it more difficult to keep thermal input low. A continuous beam may lead to excessive heat buildup, risking damage to heat-sensitive substrates. Pulse lasers, on the other hand, deliver energy in short intervals, concentrating the energy in short bursts. This way, a high peak power can be reached without continuously transferring heat to the workpiece.
Key Advantages of Pulse Laser Cleaning
Non-Contact Process and Minimal Substrate Damage
One of the greatest advantages of pulse laser cleaning is its non-contact nature. Traditional cleaning methods like abrasive blasting or chemical etching require physical contact or chemical reaction with the substrate, potentially harming delicate surfaces or introducing micro-scratches. By contrast, a laser beam does not mechanically abrade the surface. The cleaning action is driven purely by light absorption, minimizing physical wear and tear.
Furthermore, because pulse laser cleaning is typically tuned for high absorption by the contaminant and lower absorption by the substrate, the risk of unintended damage is limited. The short pulse duration restricts heat flow into the material, resulting in less distortion, oxidation, or other thermal effects.
High Precision and Selective Removal
Pulse laser cleaning can be fine-tuned to remove specific contaminants or coatings with minimal effect on the substrate or other adjacent layers. This selective removal is invaluable in industries such as semiconductor manufacturing and heritage restoration, where even minor substrate damage can cause significant financial or cultural loss. Moreover, lasers can be focused to a very small spot size—on the order of micrometers—allowing for precise local cleaning operations.
Environmentally Friendly and Safe
Compared to many chemical cleaning processes that involve harmful solvents or produce significant waste, pulse laser cleaning typically results in very little secondary waste. The ablated material is often vaporized or reduced to particulates that can be captured in a filtration system. Eliminating the need for hazardous chemicals reduces environmental risk and protects operator health.
Versatility Across Different Materials
From metallic surfaces and plastic parts to stone monuments and delicate artworks, pulse laser cleaning finds applications in a wide variety of settings. By carefully selecting parameters such as wavelength, pulse duration, repetition rate, and fluence, operators can adapt the process for different contaminants and substrates. This versatility has made laser cleaning a popular choice in industries ranging from automotive to cultural heritage.
Automation and Integration in Production Lines
Modern pulse laser cleaning systems can be easily automated using robotics or gantry systems. An operator simply programs the system to direct the laser beam along predefined paths. This automation leads to consistent, repeatable results and can improve throughput in a production environment. The ability to integrate pulse laser cleaning seamlessly into existing production workflows further expands its appeal for mass manufacturing processes.
Potential Drawbacks and Limitations
While pulse laser cleaning offers a host of benefits, it is not without limitations.
Equipment Cost and Initial Investment
Industrial-grade pulse laser systems can be costly, especially when compared to simpler mechanical methods or chemical baths. The upfront investment includes not only the laser source but also beam delivery optics, positioning mechanisms, safety enclosures, and control electronics. However, many companies justify the initial cost with the promise of lower consumable use, minimal disposal costs, and reduced environmental compliance expenses.
Power and Energy Consumption
High-power pulse laser systems can consume significant amounts of electricity and typically require advanced cooling systems to maintain stable operating temperatures. For small-scale or portable systems, power requirements can limit the practicality of field use. Nevertheless, improvements in laser efficiency—particularly in fiber lasers—have mitigated some of these challenges.
Requirement for Skilled Operators
While automation can reduce labor costs in some contexts, operator skill is still critical for tasks like parameter selection, system setup, and real-time process monitoring. Laser cleaning technicians need an understanding of how laser settings (pulse energy, repetition rate, scanning speed, etc.) interact with a given material. Additionally, laser safety training is mandatory to ensure a safe working environment.
Safety Considerations
Lasers, particularly high-power pulse lasers, pose safety risks if not used correctly. Direct or diffuse reflections can damage the eyes and skin. Adequate protective equipment, shielding, and safety interlocks are essential. In addition, ablated materials might release harmful fumes or particulates, necessitating adequate ventilation and filtration systems.
Substrate Sensitivity and Process Parameter Constraints
Though generally recognized for low thermal impact, pulse laser cleaning can still potentially damage very heat-sensitive materials if pulse parameters are not optimized. Certain polymers, composites, or historically significant materials require careful experimentation or advanced knowledge to avoid discoloration, warping, or other forms of degradation.
Applications of Pulse Laser Cleaning
The versatility of pulse laser cleaning is evident in a diverse array of commercial, industrial, scientific, and cultural applications. Below are the major sectors where this technology has made significant inroads.
Industrial Applications
- Rust and Oxide Removal: Oxides, particularly rust (iron oxide), can compromise the structural integrity of steel and other metals. Removing these oxides is often essential before welding, painting, or coating. Pulse laser cleaning excels at stripping away rust, leaving a pristine metal surface with minimal residue. This is particularly beneficial in industries like shipbuilding, pipeline maintenance, and general metal fabrication, where large, corroded surfaces require thorough preparation.
- Paint and Coating Removal: Removing old or worn paint layers is a common challenge in maintenance and refurbishment tasks, whether on aircraft, automobiles, or industrial equipment. Traditional methods—like abrasive blasting or chemical solvents—can be messy, environmentally hazardous, and potentially damaging to substrates. Laser cleaning offers a precise and eco-friendly alternative. It is especially useful for removing paint from sensitive alloys in the aerospace sector, where structural integrity is paramount.
- Surface Preparation for Welding or Bonding: The quality of a weld, adhesive bond, or other surface-joining technique is highly dependent on surface cleanliness. Residual grease, oxides, or contaminants can weaken the joint. Pulse laser cleaning swiftly cleans and preps surfaces, ensuring an optimal bond or weld without using abrasives or chemicals. This is common in high-value manufacturing environments such as automotive, aerospace, and electronics assembly.
- Semiconductor Manufacturing and Electronics: Semiconductor wafers and electronic components demand ultra-clean surfaces. Micro-contaminants at the micron or even sub-micron level can cause defects leading to failures or reduced performance. Picosecond or femtosecond laser pulses can be employed to remove extremely thin, precise layers of contaminants without damaging the underlying wafer or circuit. The control and cleanliness provided by pulse laser cleaning make it an increasingly attractive solution for microelectronics manufacturers.
Cultural Heritage and Art Conservation
- Cleaning Historical Monuments and Sculptures: Historic buildings, sculptures, and monuments are susceptible to grime, biological growth (lichen, moss), and pollutants. Traditional cleaning methods can erode delicate details or introduce chemicals that degrade the stone over time. Pulse laser cleaning allows conservators to selectively remove layers of dirt and biological matter, preserving the patina or the original stone beneath. This technique has been employed in several high-profile restoration projects worldwide.
- Restoration of Paintings and Murals: The gentle, non-contact nature of laser cleaning can be advantageous for sensitive surfaces like frescoes or old oil paintings. However, the process must be approached with extreme caution, given that the underlying pigments can be equally susceptible to laser energy. By tuning the laser to a wavelength and fluence that primarily targets varnish or dirt layers, conservators can remove these unwanted layers without disturbing the original artwork.
Precision Engineering and Aerospace
- Sensitive Components and High-Value Machinery: Many aerospace components—turbine blades, rotor parts, and intricate assemblies—require precise surface finishing. Contaminants or even slight surface irregularities can lead to decreased performance and potential failures. Pulse laser cleaning offers a highly controlled approach to remove oxidation, lubricants, or temporary protective coatings, reducing the risk of dimensional changes or part damage.
- Composite Materials in Aerospace: Modern aircraft frequently incorporate composites (carbon fiber-reinforced polymers, for example) to reduce weight. These materials can be more sensitive to heat. Abrasive methods may damage the fibers, and chemical processes can degrade the resin matrix. Pulse lasers, especially those with very short pulse durations, can remove contaminants on composite surfaces without undermining structural integrity.
Automotive Industry
From degreasing engine parts to removing weld residue and paint layers, the automotive industry has seen widespread adoption of pulse laser cleaning. Car manufacturers integrate robotic laser cleaning cells into production lines for tasks like spot cleaning prior to welding, or ensuring a pristine surface for high-performance coatings.
Tool and Mold Cleaning
Tools and molds used in injection molding, die-casting, or forging often experience fouling due to residue buildup from lubricants, release agents, or carbon deposits. Regular cleaning extends tool life and maintains part quality. Traditional cleaning methods can be time-consuming, abrasive, and require the tool to be removed from the production line. Pulse laser cleaning offers a faster, in-situ solution with minimal disruption.
Pulse Laser Cleaning vs. Alternative Cleaning Methods
Mechanical Abrasion
Common methods such as sanding, wire brushing, or abrasive blasting are typically inexpensive but can wear away substrate material, alter surface texture, and generate large amounts of dust or waste media. They may also be less precise, making them unsuitable for delicate surfaces.
Chemical Solvents
Chemical cleaning methods use solvents, acids, or alkalis to dissolve or strip contaminants. While effective, these methods produce chemical waste that can be hazardous to both the environment and operators. Additionally, certain substrates (e.g., some plastics or historical materials) might react adversely to specific chemicals.
Dry Ice Blasting and Other Media Blasting Techniques
Dry ice blasting uses solid CO2 pellets propelled at high speed to remove contaminants. It is relatively gentle compared to sandblasting and is considered more eco-friendly than chemical solvents. However, it still involves the physical impact of particles on the surface. Laser cleaning, by contrast, is entirely non-contact and generally easier to confine to small target areas.
Pulse laser cleaning offers a unique blend of precision, speed, and eco-friendliness, often tipping the scales in its favor for certain demanding applications. Yet, in some scenarios where large-scale, less delicate cleaning is required, mechanical or media blasting may remain more economical.
Safety and Regulatory Considerations
Given the intense energy levels involved, safe laser operation is paramount. Regulators worldwide, such as the U.S. FDA and OSHA, or the European CE directives, set guidelines on laser classes, protective measures, and operator training.
Laser Safety Classifications
Lasers are classified based on their potential for harm to the eyes and skin. Industrial pulse lasers typically fall into Class 4, the highest classification, indicating they can be dangerous under direct or reflected viewing conditions. Proper shielding, warning signs, and protective eyewear (appropriate to the laser wavelength) are essential.
Protective Gear and Enclosures
Laser safety glasses must be matched to the laser wavelength. Enclosures with safety interlocks can prevent accidental exposure. Operators also wear protective clothing if required by the process, especially if the ablated materials are hazardous or create harmful dust or fumes.
Environmental Regulations for Laser-Based Processes
Even though pulse laser cleaning reduces chemical usage, it can still generate airborne particulates and fumes. Depending on the contaminant, this emission may require filtering or other environmental controls to meet local regulations. Systems often incorporate dust collectors or fume extractors with HEPA filters or activated carbon filters to capture particles and volatile organic compounds (VOCs).
Training and Certification
Operators should receive laser safety training and, in certain jurisdictions, need formal certification. They must learn about laser controls, possible hazards, and emergency procedures. For tasks involving historically or culturally significant artifacts, specialized training in art conservation or restoration may be required to avoid permanent damage to priceless items.
Economic and Environmental Impact
Cost-Benefit Analysis
Although the initial purchase of a pulse laser cleaning system can be significant, a thorough cost-benefit analysis often justifies the expense. Traditional cleaning methods require ongoing purchases of abrasive media, chemical solvents, protective gear, and disposal processes for hazardous waste. Laser cleaning eliminates many of these recurring costs, which can lead to substantial long-term savings. Additionally, improved product quality and lower scrap rates contribute to return on investment.
Sustainability and Waste Reduction
Pulse laser cleaning is considered a green technology due to its minimal production of secondary waste. While there is energy consumption and the generation of some fumes or particulates, these can be managed with appropriate ventilation and filtration. Unlike chemical processes, there is no liquid effluent or hazardous sludge to dispose of. By integrating pulse laser cleaning, industries can reduce their reliance on harmful chemical solvents and align with ever-stricter environmental regulations.
Global Market Outlook
The global market for laser cleaning is anticipated to grow steadily in the coming years. Key drivers include:
- Increasing environmental regulations are banning or restricting chemical cleaning agents.
- Rising labor costs and a push toward automation.
- Expanding manufacturing sectors, particularly in Asia and other emerging markets.
- Growing awareness in specialized fields such as art restoration and heritage conservation.
As more laser manufacturers enter the market, competition will likely lower the barriers to adoption, further accelerating this trend.
Practical Guidelines for Adopting Pulse Laser Cleaning
If you are considering incorporating pulse laser cleaning into your operations, here are some practical guidelines:
- Assessment of Material and Contaminant: Analyze the surface you need to clean. Identify the substrate material and the nature of the contaminant (composition, thickness, adhesion properties). Conduct small-scale tests to find optimal laser parameters.
- Choose the Right Laser System: Select a laser type (fiber, Nd:YAG, diode-pumped solid-state, etc.) that offers the necessary pulse energy, repetition rate, and wavelength. Check for reputable manufacturers that provide solid warranties, technical support, and training.
- Integration and Automation: Decide how the laser system will be used—manually, semi-automatically, or fully automated with robotics. Integrating the system into existing production lines may require additional tooling or software development.
- Safety Infrastructure: Implement a safety enclosure if needed. Install appropriate ventilation, fume extraction, and ensure operators are trained in laser safety. Determine laser safety signage, interlocks, and emergency stops.
- Process Parameter Optimization: Experiment with different pulse durations, scanning speeds, spot sizes, and repetition rates. Optimizing these parameters ensures maximum cleaning efficiency while avoiding damage to the substrate.
- Monitoring and Documentation: Maintain records of cleaning parameters, performance data, and operator training certifications. For sensitive or high-value work, document each stage of the process, including before-and-after inspections.
- Maintenance and Calibration: Schedule regular calibration and maintenance of the laser and optical components. Keep the beam delivery system clean, and check alignment periodically for consistent, reliable performance.
Summary
Pulse laser cleaning is a non-contact surface treatment method that harnesses short, high-energy pulses of laser light to selectively remove contaminants or coatings while preserving the substrate. By directing brief bursts of focused laser energy at a target surface, it induces rapid heating and evaporation or spallation of rust, paint, or other unwanted layers. This targeted approach ensures minimal thermal effect on underlying materials, making pulse laser cleaning especially suitable for delicate or high-value substrates such as aerospace components or cultural heritage artifacts. Additionally, it forgoes chemical solvents and abrasive media, leading to fewer emissions and a more environmentally responsible approach. Although pulse laser cleaning systems require a higher initial investment and operator training, they often offer long-term cost savings through reduced maintenance and consumables. As technology advances, improvements in laser sources and automation continue to expand the method’s versatility, making it a potent choice for industries and applications worldwide.
Get Laser Cleaning Solutions
Selecting the right pulse laser cleaning solution can make all the difference when removing contaminants without damaging the underlying surface. At Maxcool CNC, we specialize in delivering integrated laser cleaning systems tailored to diverse industrial needs, from rust removal and paint stripping to precision cleaning of sensitive components. Our team of experts assesses each application to recommend the ideal combination of power, pulse frequency, and beam delivery options, ensuring effective material removal and minimal substrate impact. We also emphasize safety, incorporating protective enclosures, sensors, and user-friendly control interfaces to safeguard both operators and work environments. Beyond equipment sales, Maxcool CNC supports customers with professional installation, hands-on training, and reliable after-sales service. Our goal is to streamline your production processes, reduce waste, and enhance overall efficiency. By partnering with Maxcool CNC, you gain a trusted resource dedicated to providing innovative, cost-effective, and sustainable laser cleaning solutions.