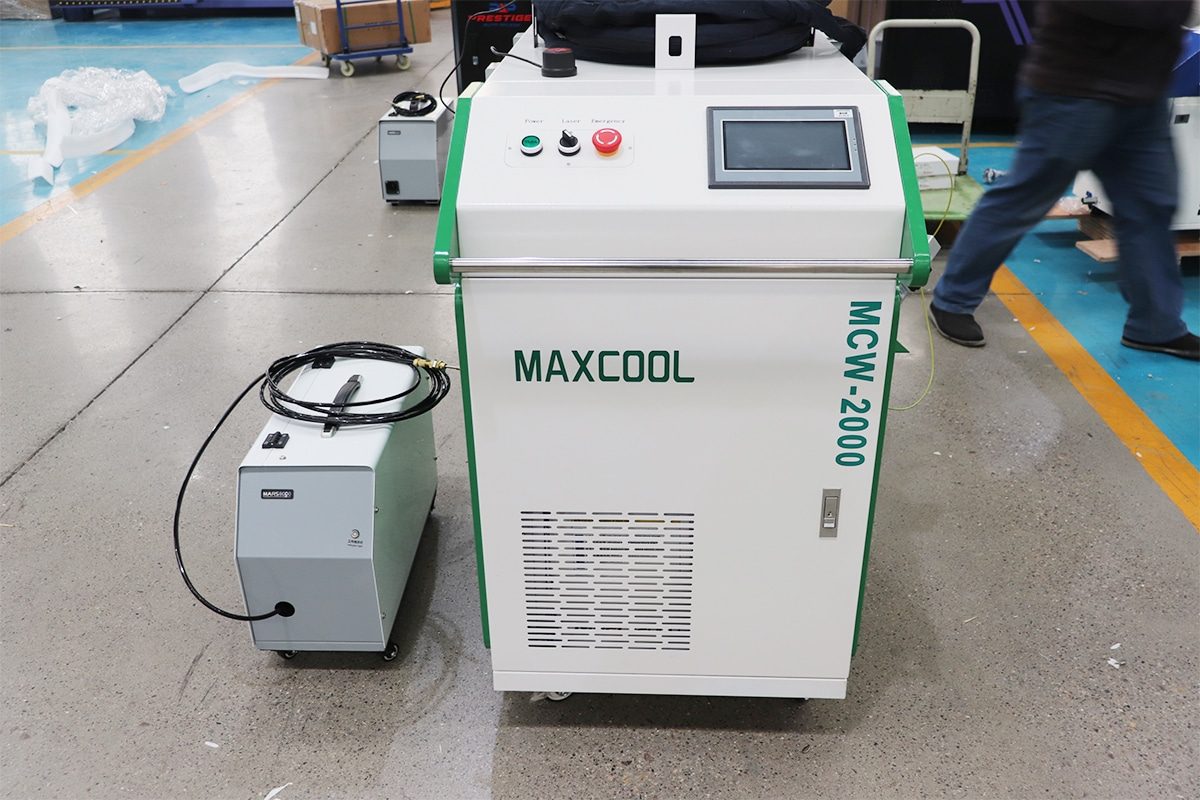
Laser cleaning has revolutionized the approach to removing rust, coatings, contaminants, and residues from surfaces across industries. As a precise, non-contact, and eco-friendly method, laser cleaning minimizes damage to underlying materials while eliminating the need for harsh chemicals or abrasive tools. By harnessing laser energy, contaminants are removed through processes like ablation, vaporization, or thermal decomposition. However, achieving optimal cleaning effectiveness requires a comprehensive understanding of the various factors that influence this process. Material properties, contaminant characteristics, laser parameters, and environmental conditions all play critical roles in determining laser cleaning outcomes. This article explores these key influencing factors, offering insights to maximize laser cleaning efficiency and precision for diverse industrial applications.
Principles of Laser Cleaning
Laser cleaning is a process that uses highly focused laser beams to remove contaminants, coatings, rust, and other unwanted materials from surfaces. By delivering controlled energy, the laser disrupts the bonds within the contaminant layer, allowing it to be removed without damaging the underlying material. The effectiveness of this cleaning process depends on a complex interaction between the laser and the contaminant material, achieved through ablation, vaporization, or thermal decomposition.
- Ablation: The laser energy is absorbed by the contaminant layer, causing it to rapidly heat and detach from the surface. This high-intensity energy transfer breaks down the material and removes it in the form of plasma, vapor, or small particles.
- Vaporization: For certain contaminants, the laser energy is sufficient to directly vaporize the material from solid to gas, effectively removing it without residue.
- Thermal Decomposition: In some cases, the laser energy can cause the contaminant material to decompose chemically, weakening its bond to the surface and allowing it to be easily removed.
Types of Lasers Used in Laser Cleaning
Continuous Laser
Continuous lasers provide a consistent, uninterrupted beam of energy, ideal for larger surface areas or applications where high throughput is essential. In laser cleaning, continuous lasers are often employed for heavy-duty tasks where the goal is to remove thick or highly bonded contaminants. The constant energy output effectively heats and vaporizes the contaminant, allowing for efficient cleaning.
- Applications: Continuous lasers are suitable for robust materials that can tolerate a steady energy supply, such as steel, cast iron, and thick coatings.
- Advantages: They deliver a steady energy flow, resulting in uniform cleaning and higher productivity for extensive cleaning applications.
- Considerations: Continuous lasers can generate significant heat in the substrate, making them better suited for materials with high thermal tolerance to avoid potential damage.
Pulse Laser
Pulse lasers, on the other hand, deliver energy in short, intense bursts rather than a continuous flow. This high peak power for very short intervals minimizes heat transfer to the substrate, allowing for precise cleaning on sensitive or intricate surfaces. Pulse lasers are ideal for removing contaminants in layers or when working with delicate substrates where excessive heat could cause damage.
- Applications: Pulse lasers are commonly used for detailed cleaning tasks on materials like aluminum, ceramics, and delicate components in electronics and aerospace.
- Advantages: The pulsed nature allows for precision cleaning, reducing thermal stress and preventing overheating of the substrate. They are particularly effective for removing thin, delicate, or intricate coatings.
- Considerations: Pulse lasers generally work more slowly than continuous lasers, so they may be less efficient for large-scale cleaning but offer superior precision for sensitive applications.
Factors Affecting the Effectiveness of Laser Cleaning
Material Properties
Type of Substrate Material
- Metals typically have high thermal conductivity and reflectivity. When laser cleaning metals like steel or aluminum, high reflectivity can reduce the absorption of laser energy, requiring adjustments in laser power and wavelength. High thermal conductivity helps dissipate heat quickly, reducing the risk of overheating.
- Plastics and Polymers have lower melting points compared to metals and may require precise control of laser energy and pulse duration to avoid melting or deforming the substrate during cleaning.
- Ceramics and Composites often exhibit high reflectivity and thermal resistance, necessitating careful tuning of laser parameters for effective cleaning without damaging the surface.
Absorption Characteristics
Thermal Properties
- Thermal Conductivity affects the rate at which heat is transferred away from the laser interaction zone. High-conductivity materials like copper disperse heat quickly, reducing the risk of localized melting or damage.
- Heat Capacity determines how much energy is needed to raise the temperature of the material. Materials with high heat capacity require higher energy for effective cleaning, while low heat capacity materials are more sensitive to heat input.
Surface Roughness
Oxidation State
Contaminant Characteristics
Type of Contaminants
- Rust and Oxides absorb laser energy effectively, making them relatively easy to remove with appropriate laser parameters.
- Paints and Coatings often require specific wavelengths or energy densities to break down effectively, depending on their composition.
- Organic Contaminants like oil, grease, and biological residues may vaporize at lower energy levels but require tailored parameters to avoid leaving residues or damaging the underlying substrate.
Thickness of the Contaminant Layer
Optical Properties of Contaminants
- Absorptivity and Reflectivity: Contaminants with high absorptivity at the laser wavelength are easier to remove, while highly reflective contaminants may reflect a significant portion of laser energy, reducing cleaning efficiency.
- Transmission Characteristics: Transparent or translucent contaminants may allow laser energy to penetrate through them, potentially causing unintended effects on the substrate beneath.
Laser Parameters
Wavelength
Pulse Duration
- Short Pulse Durations (Nanosecond, Picosecond, Femtosecond) offer high peak power and minimal heat diffusion, making them ideal for precise cleaning tasks without causing thermal damage to the substrate.
- Longer Pulse Durations deliver lower peak power over a more extended period, increasing the likelihood of heat transfer. This approach is more suited for applications requiring bulk material removal.
Energy/Power Density
Repetition Rate
Beam Profile and Spot Size
Process Parameters
Scanning Speed
Overlap of Laser Spots
The Angle of Incidence
Number of Passes
Environmental Factors
Ambient Temperature
Humidity
Surrounding Atmosphere
Equipment Factors
Laser System Stability
Beam Delivery System
Control Systems and Software
Operator Skill and Experience
Proper Settings
Knowledge of Materials and Contaminants
Safety Measures
Protective Equipment
Compliance with Regulations
Optimization Strategies for Effective Laser Cleaning
Selecting Appropriate Laser Parameters
The first step in optimizing laser cleaning involves choosing the most suitable laser parameters for a specific application. This includes fine-tuning factors such as wavelength, pulse duration, energy density, repetition rate, and beam profile.
- Wavelength Selection: Matching the laser wavelength to the absorption characteristics of the contaminants is essential. A well-chosen wavelength maximizes energy absorption by the contaminant while minimizing absorption by the substrate, ensuring effective cleaning without damaging the base material.
- Pulse Duration and Energy Density: Short pulse durations (e.g., nanoseconds or picoseconds) are ideal for the precise cleaning of delicate substrates with minimal thermal effects, while longer pulses can be used for bulk removal. Energy density must be carefully set to provide sufficient power for contaminant removal without causing substrate damage.
- Beam Profile and Spot Size: The choice of the beam profile (Gaussian, flat-top, etc.) and spot size influences cleaning uniformity and precision. Adjusting these parameters ensures consistent energy delivery for uniform contaminant removal.
Adjusting Process Parameters
Fine-tuning the process parameters allows for greater control over the interaction between the laser and the material surface. Adjustments to scanning speed, overlap, angle of incidence, and the number of passes can significantly impact cleaning effectiveness.
- Scanning Speed: Optimizing scanning speed ensures the appropriate amount of energy is delivered to each area. High speeds may reduce cleaning effectiveness due to insufficient energy delivery, while slower speeds increase energy exposure and risk overheating.
- Overlap of Laser Spots: Adjusting the degree of overlap between successive laser spots ensures thorough contaminant removal without leaving residue. High overlap provides complete coverage but must be balanced to avoid over-processing and substrate damage.
- The Angle of Incidence: Modifying the angle at which the laser beam strikes the surface can optimize energy absorption and minimize reflection. For complex geometries, varying the angle of incidence improves access to hard-to-reach areas.
- Number of Passes: Multiple cleaning passes may be required for thick or strongly bonded contaminants. Using several low-energy passes allows for gradual contaminant removal while minimizing the risk of substrate damage.
Material Testing and Characterization
Material testing and characterization are vital for understanding how a substrate and its contaminants interact with laser energy. This knowledge allows for precise parameter adjustment and optimized cleaning outcomes.
- Preliminary Testing: Conducting small-scale tests on sample materials helps identify optimal laser settings and ensures the desired cleaning effect. Testing reduces the risk of substrate damage and enhances process efficiency.
- Material Characterization: Analyzing the physical, thermal, and optical properties of the substrate and contaminants provides valuable insights for parameter selection. Techniques such as spectroscopy can identify absorption characteristics, informing the choice of wavelength and pulse settings.
- Monitoring and Feedback: Implementing real-time monitoring systems to assess laser-material interactions can provide immediate feedback for parameter adjustments. This allows for dynamic optimization and consistent results.
Environmental Control
Controlling environmental factors is crucial for maintaining the consistency and effectiveness of laser cleaning processes. Temperature, humidity, and the surrounding atmosphere all influence laser-material interactions and must be managed accordingly.
- Ambient Temperature: Temperature affects the thermal properties of the substrate and contaminants, potentially altering their behavior under laser irradiation. Maintaining a stable temperature environment helps ensure consistent cleaning outcomes.
- Humidity Management: High humidity can affect the absorption of laser energy, particularly in materials that absorb moisture. Controlling humidity levels reduces variability in laser interactions and ensures predictable cleaning performance.
- Dust and Particulate Control: Particulates in the surrounding environment can scatter the laser beam, reducing cleaning efficiency. Using air filtration, cleanroom conditions, or inert gas environments minimizes these issues and enhances energy delivery.
- Inert Gas Environments: Employing inert gases, such as nitrogen, during laser cleaning can prevent oxidation and enhance cleaning performance. Inert atmospheres reduce the formation of unwanted residues and improve overall process stability.