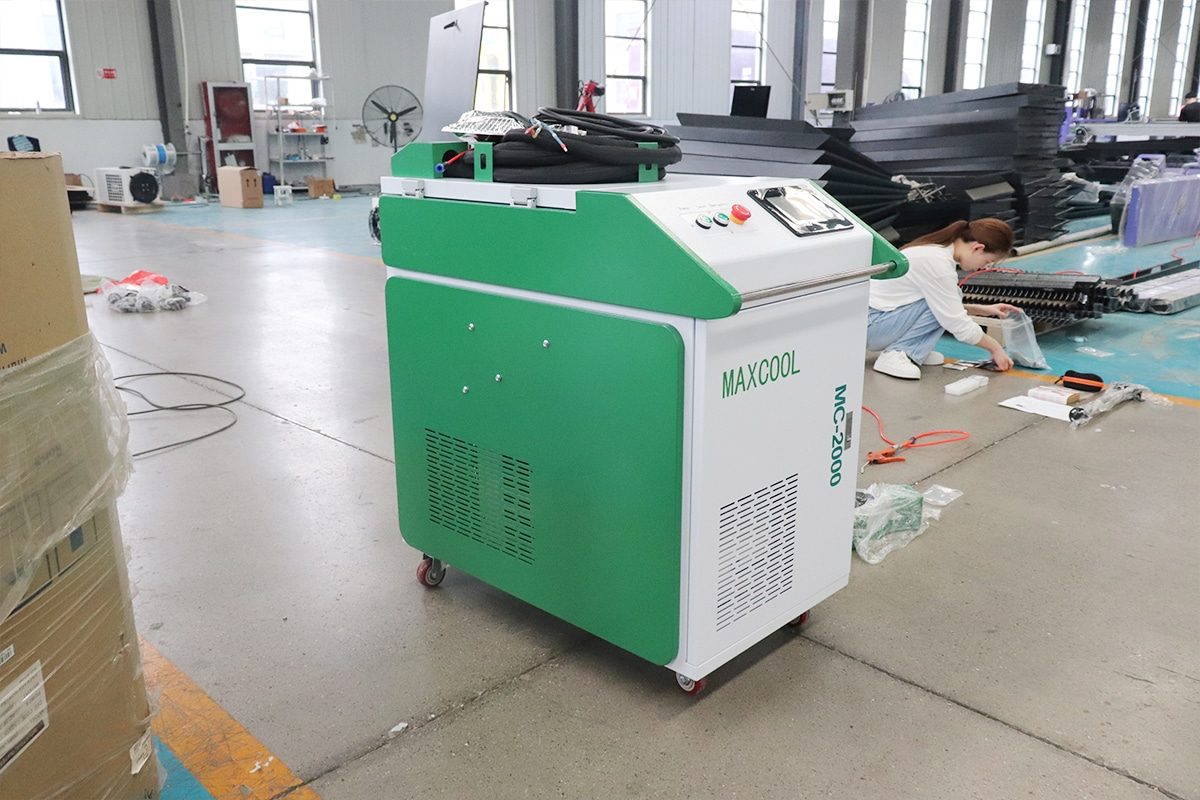
Understanding Laser Cleaning Machines
How Laser Cleaning Works
Laser cleaning involves two primary types of laser operations—continuous and pulse lasers. These methods are chosen based on the type of surface material, the nature of the contaminants, and the intended outcome.
- Continuous Laser: Continuous lasers provide a constant output of laser energy and are typically used in applications where a steady, consistent beam is required for cleaning surfaces. The continuous nature of the laser allows for a uniform and controlled cleaning process, particularly when dealing with larger areas or surfaces that require less precision.
- Pulse Laser: Pulse lasers deliver energy in brief, high-intensity bursts. These lasers are ideal for cleaning delicate or highly resistant materials, as the rapid, intense pulses can effectively remove stubborn contaminants without causing excessive heat buildup in the surrounding material. Pulse lasers are often used for more intricate cleaning tasks where precision is paramount.
Applications of Laser Cleaning
Laser cleaning machines have gained popularity across various industries for their versatility and efficiency. Some of the most common applications include:
- Rust and Scale Removal: One of the primary uses of laser cleaning is for the removal of rust and scale from metal surfaces, particularly in the automotive and manufacturing industries. Laser cleaning eliminates the need for abrasive methods or chemicals that could damage the underlying metal.
- Paint and Coating Stripping: Laser cleaning can effectively remove layers of paint or coatings without harming the surface beneath, making it ideal for industries such as automotive repair, shipbuilding, and surface preparation.
- Surface Preparation: Laser cleaning is often used to prepare metal and plastic surfaces for subsequent processes like welding, bonding, or coating by removing contaminants like oil, grease, or oxides.
- Heritage Conservation: Laser cleaning is increasingly used for cleaning historical monuments, sculptures, and artworks. The precision of lasers makes them perfect for delicate cleaning tasks where traditional methods might cause damage to the material.
Types of Dangers in Laser Cleaning Operations
Laser Radiation Hazards
The most significant danger associated with laser cleaning machines is the risk of exposure to harmful laser radiation. Lasers emit highly focused beams of light that, if not properly controlled, can cause severe damage to the eyes and skin.
- Eye Injuries: Direct exposure to laser radiation can lead to serious eye injuries, including retinal burns and permanent vision loss. Even reflected or scattered laser beams can cause significant harm if proper safety protocols are not in place.
- Skin Burns: The intense energy generated by the laser beam can cause thermal burns when it comes into contact with the skin. The risk increases when high-power lasers are used, which can cause deep tissue damage.
Fumes and Particulate Matter
Laser cleaning generates fumes and particulate matter as a byproduct of the material vaporization process. These can pose serious health risks if inhaled.
- Toxic Fumes: When certain materials are vaporized by the laser, they can release harmful gases, including carbon monoxide, ozone, or volatile organic compounds (VOCs). These fumes can have adverse effects on respiratory health if inhaled over prolonged periods.
- Particulate Matter: Fine dust or metal particles generated during cleaning can pose a threat to the respiratory system. Inhalation of these particles can cause respiratory disorders or other long-term health issues.
Electrical Hazards
Laser cleaning machines operate with high electrical currents and voltages, which can present serious risks if safety precautions are not followed.
- Electric Shock: Accidental contact with exposed electrical components can lead to electric shocks, which can cause burns, muscle contractions, and even cardiac arrest in severe cases.
- Fire Hazards: Electrical failures, such as short circuits or overheating, can result in fires. In combination with combustible materials in the area, such fires can escalate quickly.
Fire Hazards
Lasers can generate intense heat, which, in combination with flammable materials in the vicinity, increases the risk of fire.
- Ignition of Combustibles: Sparks or stray laser beams can ignite nearby combustible materials, including paper, plastics, or other flammable substances.
Mechanical Hazards
Laser cleaning machines often involve complex mechanical components such as robotic arms and moving parts, which can create potential hazards for operators.
- Pinching and Entanglement: Moving robotic arms, conveyors, or other mechanical systems can pose risks of entanglement or pinching.
- Falling Objects: Equipment malfunctions or improper handling can lead to falling components, which could injure workers.
Chemical Exposure
Laser cleaning often involves the removal of coatings, residues, or contaminants that may contain harmful chemicals. These chemicals pose a risk if they are not handled safely.
- Skin and Eye Burns: Direct contact with chemical residues can cause burns or irritation to the skin and eyes.
- Toxicity: Inhalation or absorption of certain chemicals can lead to poisoning or long-term health effects.
Ergonomic Hazards
Prolonged operation of laser cleaning machines can lead to ergonomic issues, particularly due to repetitive motions or uncomfortable postures.
- Musculoskeletal Disorders (MSDs): Operators may suffer from strains, sprains, and repetitive stress injuries if they are not provided with ergonomic equipment or proper workstations.
Thermal Hazards
Laser cleaning machines can generate significant heat, leading to thermal hazards for operators.
- Burns: Operators are at risk of burns from the hot surfaces of the equipment or the materials being cleaned.
Noise Hazards
Noise from laser cleaning machines, especially those that involve moving parts or high-powered lasers, can be harmful over time.
- Hearing Damage: Prolonged exposure to high noise levels can result in hearing loss or tinnitus.
Psychological Hazards
The fast-paced nature of laser cleaning operations, along with potential exposure to hazards, can lead to psychological stress.
- Stress and Fatigue: Repetitive tasks, high-pressure environments, and constant vigilance in avoiding accidents can contribute to mental and emotional fatigue.
Preventive Measures and Safety Protocols
In order to minimize the dangers associated with laser cleaning machines, several safety protocols and preventive measures must be implemented.
- Protective Equipment: Personal protective equipment (PPE) is essential for preventing injuries. Operators should wear laser safety goggles, protective gloves, face shields, and flame-resistant clothing. In addition, hearing protection, respiratory protection, and heat-resistant garments may be necessary, depending on the specific risks of the cleaning process.
- Proper Ventilation Systems: Effective ventilation systems are crucial to remove fumes, particulate matter, and harmful gases from the work environment. Local exhaust ventilation systems should be installed near the laser cleaning area to capture and remove contaminants at their source.
- Regular Maintenance and Inspections: Regular inspections and maintenance of laser cleaning machines are critical to ensuring their safe operation. Components such as the laser, cooling system, and ventilation equipment should be checked periodically to ensure they are functioning correctly.
- Comprehensive Training and Education: Operators should undergo comprehensive training on the safe use of laser cleaning machines. Training should include instruction on the operation of the equipment, hazard identification, emergency procedures, and the proper use of PPE.
- Engineering Controls: Engineering controls, such as laser enclosures and automatic shutdown systems, should be implemented to minimize exposure to hazards. Laser enclosures prevent unintended exposure to laser radiation, and automatic shutdown systems can reduce the risk of injury in case of malfunction.
- Administrative Controls: Administrative controls include safety protocols, guidelines, and standard operating procedures that ensure safe operation. Safety audits and continuous monitoring should be conducted to ensure compliance with safety standards.
Best Practices for Safe Operation
- Site Assessment and Planning: A thorough site assessment should be conducted before the installation of laser cleaning equipment. The assessment should identify potential hazards and ensure that appropriate safety measures are in place.
- Personal Protective Equipment (PPE) Selection: The selection of PPE should be based on the specific risks of the operation. Operators should be provided with the correct PPE to protect against laser radiation, fumes, heat, and noise.
- Safe Work Procedures: Clear and concise safe work procedures should be established for each laser cleaning task. These procedures should address all aspects of operation, including setup, cleaning, and shutdown.
- Emergency Preparedness: Emergency response plans should be developed and regularly practiced. Operators should be trained in first aid, fire safety, and emergency evacuation procedures to respond effectively to any accidents.
- Continuous Improvement and Feedback: Continuous improvement initiatives should be implemented to enhance safety. Feedback from operators should be collected to identify potential hazards and improve safety protocols.