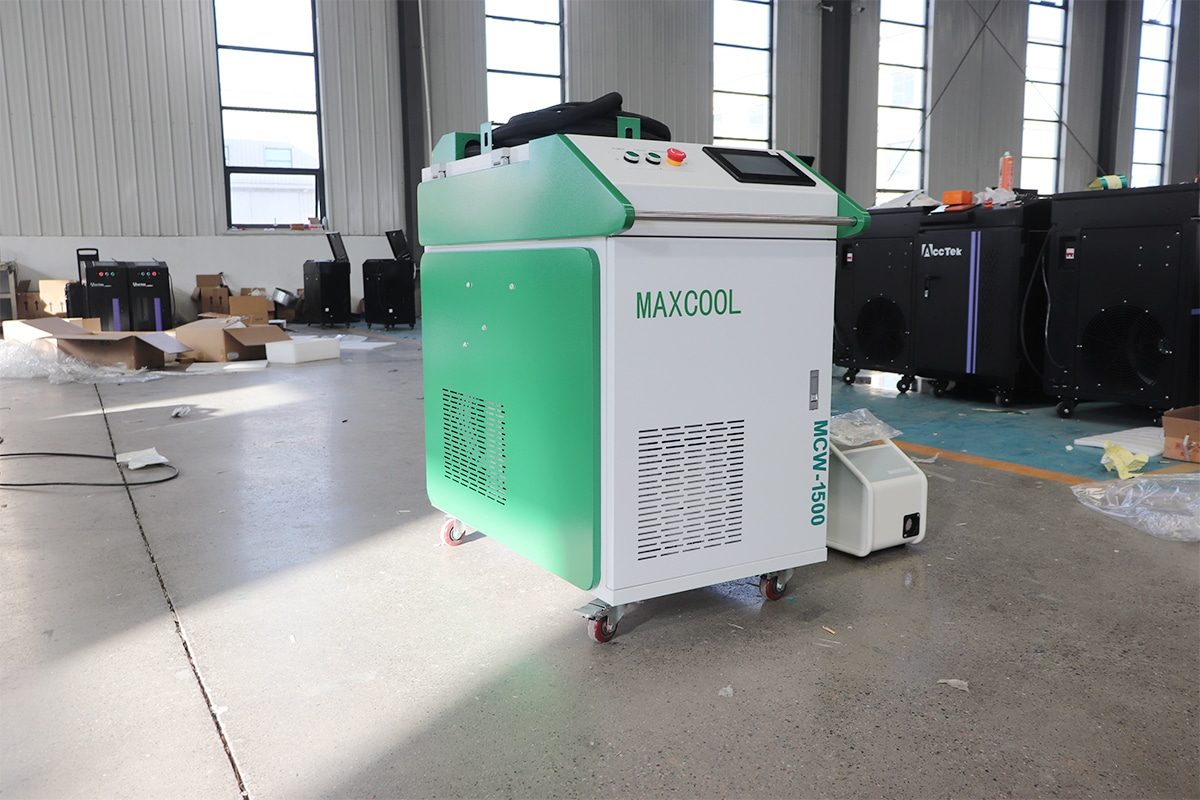
What Are The Common Problems of Laser Welding Machines?
Laser welding, a process that harnesses concentrated beams of light to fuse materials, has gained immense popularity in industries ranging from automotive and aerospace to electronics and medical device manufacturing. The technology’s rise stems from its numerous advantages over traditional welding methods, including a smaller heat-affected zone, higher welding speeds, excellent weld quality, minimal distortion, and the ability to weld dissimilar metals or difficult-to-reach areas. Because of these benefits, laser welding machines have become a staple in modern manufacturing environments where precision and efficiency are paramount.
However, despite the many advantages, laser welding is not without its challenges. Numerous variables influence the quality and consistency of a weld: laser power, beam focus, welding speed, material composition, shielding gas choice, machine maintenance, and even the operator’s level of training. If these parameters are not correctly managed, weld defects and quality issues can arise, sometimes leading to production delays, costly rework, or failure of the welded part in service.
In practice, organizations that adopt laser welding must become adept at identifying, diagnosing, and mitigating common problems to fully capitalize on the benefits of this technology. Typical issues include porosity, cracks, spatter, excessive distortion, incomplete penetration, poor fit-up, and thermal damage to the surrounding material. Some of these challenges are universal to welding processes, while others are specific to the unique characteristics of laser-based joining.
The purpose of this article is to provide a thorough examination of the most frequent problems encountered with laser welding machines, exploring both technical causes and potential solutions. By understanding these issues in detail, businesses can adopt best practices, optimize their welding processes, and maintain the efficiency and reliability of their laser welding systems. Whether you are a production engineer, a machine operator, or simply interested in advanced welding processes, the insights shared here will help you better harness laser welding technology.
Table of Contents
Fundamentals of Laser Welding
Before delving into the most common problems associated with laser welding, it is crucial to understand the basics of how these machines function and the parameters that govern weld quality.
How Laser Welding Works
At its core, laser welding relies on the principle of using a focused beam of coherent light to melt the surfaces of two (or more) materials so they can fuse upon cooling. Unlike conventional welding processes, which may rely on electrodes or a broader heat source like a flame, lasers concentrate a tremendous amount of energy into a small area. This results in rapid heating, localized melting, and quick solidification. The heat-affected zone (HAZ) is consequently smaller, leading to less distortion and thermal stress in the surrounding material.
Several key components constitute a laser welding setup:
- Laser Source: The source generates a coherent light beam. Common industrial lasers used for welding include fiber lasers, CO2lasers, and Nd: YAG lasers. Each type has its strengths, wavelength characteristics, and applications.
- Beam Delivery and Optics: After generation, the laser beam travels through optical elements (lenses, mirrors, fiber-optic cables) to reach the workpiece. Focusing lenses converge the beam to a precise spot, where the energy density is high enough to melt metal.
- Workpiece Holding/Positioning: Fixtures or specialized motion systems (such as robotic arms or CNC tables) hold or move the parts to be welded. Precision in positioning is critical, as even minute deviations can affect weld quality.
- Shielding Gas: An inert or semi-inert gas (e.g., argon, helium, nitrogen) may be used to protect the molten pool from oxidation or contamination. The gas can also influence weld penetration and overall stability.
Key Parameters Affecting Weld Quality
Laser welding is sensitive to multiple parameters, each of which can profoundly affect the resulting weld:
- Laser Power: Higher power typically results in deeper penetration. However, excessive power can lead to defects like spatter, keyhole instability, and even burn-through.
- Welding Speed: The speed at which the laser beam or workpiece moves impacts the interaction time between the laser and the material. Slow speeds increase heat input and risk excessive penetration or distortion; high speeds can lead to incomplete fusion.
- Focal Position: Proper focus ensures that maximum energy density is delivered at the workpiece surface (or slightly within). Misalignment in focus can reduce penetration and cause inconsistent weld beads.
- Material Properties: Different metals and alloys have distinct melting points, reflectivities, thermal conductivities, and absorption characteristics, all influencing how the laser interacts with the surface.
- Shielding Gas Flow: Correct choice of gas type and flow rate reduces oxidation, porosity, and weld pool contamination. Improper gas can cause weld defects.
- Joint Design and Fit-Up: The geometry of the joint—whether it is a butt joint, lap joint, or fillet weld—and the gap between parts all affect how the laser beam melts and fuses the material.
Understanding these fundamentals lays the groundwork for diagnosing and addressing the typical problems that arise in laser welding. In the following sections, we will explore these problems in detail, explaining their causes, how they manifest, and what can be done to mitigate or prevent them.
Porosity and Gas Entrapment
Porosity is the formation of small voids or voids within a weld and is a major issue with any welding process, including laser welding. These pores typically result from trapped gas bubbles that fail to escape before the weld pool solidifies. Not only do pores weaken the weld, but they can also serve as initiation points for cracks and corrosion over time.
Causes
- Improper Shielding Gas: If the gas flow rate is incorrect or the type of gas is incompatible with the material, the weld pool may become contaminated by atmospheric oxygen or nitrogen.
- Surface Contamination: Oils, grease, or moisture on the workpiece surface can vaporize under the laser beam, introducing gas into the molten pool.
- Excessive Welding Speed: When welding too quickly, the molten pool might solidify before gas bubbles can escape.
- Material Composition: Certain metals or alloys have high gas solubility and can trap gas more readily during solidification.
Effects
- A weakened weld structure leads to reduced mechanical strength.
- Increased risk of crack formation.
- Potential leak paths if the weld is used in pressure or vacuum applications.
Solutions
- Surface Preparation: Thoroughly clean parts before welding. Remove all contaminants using solvents, degreasers, or laser cleaning systems (where available).
- Optimized Shielding Gas: Choose an appropriate gas (argon, helium, or a mix) and adjust flow rates to ensure adequate coverage.
- Parameter Adjustment: Lower welding speed or adjust laser power to allow for adequate degassing of the melt pool.
- Use of Proper Filler Material: In hybrid laser welding (laser + filler wire), ensure that filler material is consistent with base metal composition to reduce porosity formation.
- Preheating: For certain metals, mild preheating can help reduce moisture and improve weld pool fluidity, aiding in gas escape.
Cracks and Material Defects
Cracks are severe defects that compromise weld integrity. They can appear within the weld bead itself (solidification cracks) or in the heat-affected zone (HAZ) (liquation or stress cracks). Laser welding, while generally producing smaller HAZs compared to traditional processes, is still susceptible to cracks if parameters or materials are not matched correctly.
Causes
- High Thermal Gradients: Laser welding’s localized heat can create steep temperature gradients, leading to high residual stresses that can cause cracking upon cooling.
- Brittle Microstructures: Certain alloys, such as high-strength aluminum alloys, martensitic steels, or nickel-based superalloys, may form brittle phases under rapid cooling.
- Pre-Existing Material Defects: Material with inclusions, impurities, or internal defects can exacerbate crack formation once molten and rapidly solidified.
- Improper Joint Design: Stress concentrations due to poor fit-up or joint geometry can encourage cracking.
Effects
- Potential for sudden weld failure during service.
- Reduced fatigue life and overall reliability.
- Increased costs due to rework or rejection of welded assemblies.
Solutions
- Material Selection: Use alloys specifically designed for weldability.
- Pre- and Post-Weld Treatment: Preheating or post-weld heat treatment can alleviate internal stresses and reduce brittleness.
- Parameter Tuning: Adjust laser power, speed, and focus to manage cooling rates and avoid excessively brittle microstructures.
- Proper Joint Design: Ensure joint edges and geometry minimize stress concentrations. When possible, use chamfers or radius edges in high-stress areas.
- Use of Filler Materials: In some cases, adding a filler wire with a compatible composition helps mitigate solidification cracks.
Spatter and Oxidation
Spatter consists of small droplets of molten material ejected from the weld pool. It is undesirable because it can create surface defects, reduce weld smoothness, and even contaminate nearby surfaces or optical components in the laser system. Oxidation, meanwhile, refers to the reaction of molten metal with oxygen, forming oxides that degrade the weld’s mechanical properties.
Causes
- Excessive Laser Power: Surpassing the optimal heat input can cause vigorous molten metal ejections.
- Insufficient Shielding Gas Coverage: If the weld pool is exposed to air, molten metal can oxidize quickly, creating spatter and irregular weld surfaces.
- High Welding Speed: Rapid movements can lead to turbulent flow in the weld pool, spattering molten droplets away.
- Impurities and Surface Contamination: Traces of oil, paint, or rust can volatilize and contribute to spatter or oxidation.
Effects
- Rough weld surface, leading to poor aesthetic and potential stress risers.
- Inclusion of oxide films within the weld, reducing weld toughness and ductility.
- Possible damage to optical components if the spatter adheres to the focusing lens or mirrors.
Solutions
- Optimize Laser Parameters: Decrease laser power or adjust speed to maintain a stable weld pool without excessive agitation.
- Improve Shielding: Enhance gas flow coverage using specialized nozzles or gas cups. Choose an appropriate shielding gas that reduces oxidation.
- Surface Preparation: Clean workpieces thoroughly to remove contaminants that can cause gas bursts or spatter.
- Regular Maintenance: Ensure that protective windows or covers near the beam path are clean and replace them if spatter accumulates.
Inconsistent Penetration and Depth Control
Weld penetration depth is a critical quality metric. Inconsistent penetration can lead to weak joints if the weld does not fuse through the necessary thickness, or to damage if the laser penetrates too deeply and compromises underlying structures or materials.
Causes
- Incorrect Focal Point: The laser’s focus might be set too high or too low relative to the workpiece surface.
- Fluctuating Laser Power: In stable operation, the laser should deliver consistent power. Equipment malfunctions or power supply issues can cause variations in output.
- Changing Material Thickness: If the part thickness or geometry changes, the same laser setting may no longer be sufficient to achieve uniform penetration.
- Inconsistent Welding Speed: Variations in speed can result in changes in the energy per unit length delivered to the workpiece.
Effects
- Weakened welds that do not meet load requirements.
- Material damage if penetration cuts entirely through the workpiece.
- Post-weld rework or scrapping of parts.
Solutions
- Focus Optimization: Use alignment aids (such as camera systems or manual measuring tools) to set the focal point precisely.
- Consistent Power Supply: Regularly calibrate and maintain the laser source to ensure output stability.
- Adaptive Welding Systems: Advanced laser welding machines may include real-time sensors that adjust power or speed based on feedback (e.g., seam tracking, penetration depth monitoring).
- Parameter Standardization: Develop and document parameter sets for different material thicknesses or geometries. Strictly adhere to these documented parameters during production.
Inaccurate Fit-Up and Gap Tolerance
Laser welding can be less forgiving than some conventional welding processes when it comes to gaps or misalignment between the parts to be joined. Because the laser focuses energy on a small spot, large gaps can reduce energy transfer and lead to poor weld quality or incomplete fusion.
Causes
- Poor Part Tolerances: Inconsistent manufacturing processes can result in parts that do not fit together properly.
- Thermal Expansion: As parts heat up, they can deform or warp slightly, increasing or shifting the gap.
- Inconsistent Clamping or Fixturing: If parts are not held firmly and consistently, they may shift during the weld.
- Operator Error: Incorrect setup or insufficient inspection before welding can lead to misalignment.
Effects
- Insufficient fusion between parts leads to a weak or intermittent weld.
- Possible weld defects such as undercuts or gaps in the weld bead.
- Rework or scrappage of assemblies.
Solutions
- Tight Manufacturing and Tolerance Control: Ensure parts are produced within tighter dimensional tolerances to facilitate consistent fit-up.
- Effective Fixturing: Use robust fixtures or clamping systems to minimize part movement.
- Edge Preparation: Ensure edges are smooth, parallel, and free from burrs. Consider beveling edges if necessary.
- Pre-Weld Inspection: Check alignment and gap distances before activating the laser. Automated vision systems can further enhance fit-up accuracy.
Heat-Affected Zone (HAZ) and Distortion
One of the touted benefits of laser welding is a smaller heat-affected zone compared to traditional processes. However, if parameters are poorly managed, the HAZ can still become larger than desired, causing stress, distortion, and potential changes in the metallurgical properties of the base material.
Causes
- Excessive Heat Input: Too much power or a slow travel speed leads to more heat migration into the material.
- Material Susceptibility: Some alloys, especially those that undergo phase transformations (like certain steels), can become hard or brittle in the HAZ.
- Inadequate Cooling: If the surrounding fixtures or environment do not dissipate heat effectively, temperature can build up, enlarging the HAZ.
- Repeated Passes: Multiple weld passes in the same area without allowing cool-down can amplify distortion and HAZ.
Effects
- Warping or deformation of parts, potentially leading to assembly misfits.
- Changes in mechanical properties, such as brittleness or reduced toughness.
- Internal stress can lead to cracking during service.
Solutions
- Controlled Heat Input: Optimize laser power and speed to minimize unnecessary heat.
- Use of Chilling Fixtures: Some assemblies benefit from water-cooled or otherwise temperature-controlled fixtures to keep part temperatures stable.
- Allow Cooling Time: If multiple passes are necessary, pause between passes to let the material cool, reducing distortion buildup.
- Material-Specific Processes: Tailor parameters to the specific alloy, especially when working with high-strength steels or other heat-sensitive materials.
Improper Shielding Gas and Contamination
Shielding gas plays a pivotal role in many welding processes, including laser welding. If the shielding gas is not chosen properly, or if contamination occurs, weld quality and appearance can be severely compromised.
Causes
- Wrong Gas Type: Different metals require different shielding environments (argon, helium, or nitrogen). Using an incompatible gas can lead to chemical reactions in the weld pool.
- Insufficient Flow Rate or Coverage: Low flow or poor nozzle design can allow ambient air to contaminate the weld area, leading to oxidation, porosity, and discoloration.
- Moisture or Impurities in Gas Supply: If the gas is not pure or the lines contain condensation, contamination can occur.
- Inadequate Cleaning: Dirt, grease, or oxides on the metal surface can react during welding if not removed.
Effects
- Porosity, inclusions, and other internal defects.
- Surface discoloration, scale, or reduced corrosion resistance.
- Potential for cracking due to localized contamination.
Solutions
- Appropriate Gas Selection: Match the gas to the material. For instance, argon for stainless steel, helium for materials requiring deeper penetration or higher thermal conductivity, etc.
- Proper Flow Control: Use flowmeters and ensure the nozzle or gas delivery system fully covers the molten pool.
- Gas Purity Assurance: Use high-purity shielding gases and maintain clean, dry lines. Check for leaks or condensation in the system.
- Part Cleaning: Always degrease, remove oxides, and otherwise prepare the part before welding.
Reflective Materials and Laser Instability
Welding highly reflective materials such as aluminum, copper, or precious metals can pose challenges. The laser beam can be partially reflected into the machine’s optical system, potentially damaging components if not properly managed. Moreover, reflection can lead to unstable energy absorption, causing inconsistent weld penetration.
Causes
- High Reflectivity: Metals like copper reflect a significant portion of the laser wavelength, especially in the near-infrared range, reducing effective energy absorption.
- Beam Reflections: Reflected laser light can bounce back into the resonator or focusing optics, causing instability and potential damage.
- Incorrect Wavelength: Some laser wavelengths are absorbed better by specific materials. Using the wrong wavelength for a highly reflective metal can exacerbate reflection problems.
- Suboptimal Surface Condition: Polished or highly reflective surfaces can further enhance reflection.
Effects
- Inconsistent weld penetration leads to variable weld quality.
- Potential damage to the laser source or focusing optics.
- Lower energy efficiency and possible spatter or blowouts due to rapid shifts in absorption.
Solutions
- Use of Fiber Lasers: Fiber lasers, especially at specific wavelengths, can offer better absorption for certain reflective metals.
- Surface Preparation: Roughening or texturizing the surface can reduce reflectivity and improve initial energy coupling.
- The Angle of Incidence: Slightly tilting the workpiece or the laser head can prevent direct back reflections into the source.
- Protective Optics: Incorporate sensors and protective windows to guard against back-reflected light.
Maintenance and Downtime Issues
Laser welding machines are sophisticated systems requiring regular maintenance to sustain performance. Ignoring maintenance schedules can result in unexpected breakdowns or degraded weld quality.
Causes
- Dirty Optics: Dust, spatter, or debris accumulates on the lenses and mirrors, diminishing beam quality and power.
- Cooling System Problems: Laser sources typically require water or air cooling. Leaks or insufficient coolant flow can cause overheating and performance drops.
- Mechanical Wear: Moving components in robotic arms, linear drives, or CNC tables can degrade over time.
- Lack of Preventive Maintenance: Without scheduled inspections and part replacements, minor issues can escalate into system failures.
Effects
- Reduced weld quality due to decreased laser power or poor beam focusing.
- Increased downtime, leading to production losses.
- Shortened machine lifespan if serious damage occurs.
Solutions
- Regular Cleaning: Establish a routine for inspecting and cleaning optical components. Maintain a clean environment around the laser machine to minimize dust.
- Cooling System Monitoring: Check coolant levels, flow rate, and temperature. Replace filters and address leaks promptly.
- Replace Wear Parts: Proactively change out items like seals, gaskets, and protective windows before they fail.
- Service Contracts: Partner with reputable service providers or the machine’s manufacturer for periodic maintenance and calibration checks.
Operator Error and Training Deficiencies
Even the most advanced laser welding machine depends on skilled, knowledgeable operators. Mistakes in setting parameters, aligning parts, choosing gases, or performing maintenance can all lead to poor welds and machine issues.
Causes
- Insufficient Training: Operators may not fully understand how each parameter (power, speed, focus) affects weld outcomes.
- Parameter Mismanagement: Using the same parameters for different materials or thicknesses can cause suboptimal or defective welds.
- Lack of Procedural Compliance: Skipping steps like cleaning, pre-weld checks, or system calibrations can introduce defects.
- Limited Troubleshooting Skills: When a problem arises, operators might not know how to diagnose or correct it effectively.
Effects
- Inconsistent production quality, leading to increased scrap and rework.
- Machine damage if operators disregard safety procedures or over-stress components.
- Potential safety hazards include the risk of improper laser use or inadequate protective measures.
Solutions
- Comprehensive Training: Invest in formal training programs that cover both theoretical and practical aspects of laser welding.
- Parameter Libraries: Create standardized “recipes” for different materials and thicknesses to minimize guesswork.
- Standard Operating Procedures (SOPs): Develop clear SOPs that detail each step from part preparation to post-weld inspection.
- Ongoing Skill Development: Encourage continuous learning through certification courses, vendor-led seminars, and on-site practice.
Undercut and Lack of Fusion
While incomplete penetration often garners the most attention, undercutting and lack of fusion on the edges or sidewalls of a weld can be equally detrimental. Undercut refers to a groove melted into the base metal at the weld toe but left unfilled, whereas lack of fusion implies that the molten metal did not bond fully with one or more surfaces.
Causes
- Excessive Travel Speed: If the laser head travels too fast, the molten pool might not have enough dwell time to wet the edges, causing incomplete fusion or undercuts.
- Low Laser Power or Poor Beam Position: Insufficient heat input, or a beam offset from the seam, can lead to sidewall fusion defects.
- Joint Misalignment: If the joint is not accurately aligned beneath the laser beam, the molten metal might not reach or fuse the adjoining surfaces.
- Material Coatings or Oxides: Some metals, like aluminum, quickly form oxide layers that resist fusion unless thoroughly removed or displaced.
Effects
- Reduced Weld Strength: Even minor undercuts act as stress concentrators, weakening the joint under load or cyclic stress.
- Potential Fatigue Cracking: The notch effect of an undercut can drastically reduce fatigue life.
- Leakage Paths: If the application demands hermetic sealing, lack of fusion and small gaps can lead to leaks.
Solutions
- Speed and Power Balance: Adjust laser travel speed and power to ensure adequate melt pool fluidity and complete sidewall fusion.
- Proper Beam Alignment: Use mechanical or optical seam tracking to keep the laser precisely centered on the joint.
- Surface Treatment: Remove oxide layers, paint, or plating before welding. For aluminum and similar metals, a pre-weld cleaning routine or employing a slight bevel can help.
- Edge Preparation: If sidewall fusion is critical, prepare edges (e.g., beveling) to enhance the accessibility of the molten metal.
Laser Safety Hazards
While safety is a concern with all welding processes, lasers introduce particular hazards, including the potential for eye or skin damage from direct or reflected beams, as well as the risk of fires or noxious fumes.
Causes
- High-Power Laser Emissions: Laser beams in the kilowatt range can cause severe injury or damage if protective measures are insufficient.
- Specular Reflection: Highly reflective materials can scatter a beam unpredictably, posing an elevated risk to nearby personnel.
- Inadequate Enclosures: Some production lines fail to incorporate robust enclosures or interlock systems, allowing stray beams to escape.
- Fume Generation: Vaporized metal or coatings can create hazardous fumes, especially if extraction or filtration is lacking.
Effects
- Permanent Eye Injury: A direct or reflected laser beam can damage the retina irreversibly.
- Skin Burns: High-intensity radiation can burn exposed skin.
- Health Risks from Fumes: Prolonged inhalation of metal vapor or particulate can lead to respiratory issues.
Solutions
- Laser Safety Training: Operators must be trained in safe handling practices and should understand beam paths and reflection risks.
- Protective Gear: Laser safety glasses rated for the specific wavelength, plus protective clothing or barriers against spatter.
- Proper Enclosures & Interlocks: Fully enclosed welding cells with fail-safe door interlocks and emergency shut-offs help contain beams.
- Fume Extraction Systems: Local exhaust ventilation and filters remove airborne contaminants at the source.
Filler Wire Feeding Issues
While many laser welding applications are autogenous (no filler material), certain tasks require filler wire to bridge gaps, join thicker sections, or modify weld chemistry. If the filler wire feed system malfunctions or is poorly synchronized, weld quality and consistency suffer.
Causes
- Poor Wire Feed Alignment: The filler wire may not enter the molten pool at the correct angle or position, causing incomplete mixing or spatter.
- Irregular Wire Diameter: Variations in wire diameter can create inconsistent filler deposition rates.
- Mechanical Jamming or Bending: Inadequate feed motor torque, small guide rollers, or clogged wire liners can lead to feed stops or surges.
- Incorrect Parameter Synchronization: If the laser power or travel speed does not match the wire feed rate, the filler will not melt uniformly.
Effects
- Irregular Bead Profile: Insufficient filler can lead to underfill or incomplete joint coverage, while too much filler causes excess weld reinforcement.
- Porosity and Spatter: Intermittent wire feeding can trap gas pockets and create a spatter as the wire abruptly enters the weld pool.
- Weakened Weld: Improper filler-metal fusion leads to discontinuities and reduced mechanical properties.
Solutions
- Wire Feed System Maintenance: Clean rollers, liners, and drive systems regularly. Replace worn components.
- Alignment and Angle: Set the filler wire contact tip and delivery angle precisely relative to the laser beam.
- Consistent Wire Quality: Source filler wire with tight diameter tolerances and store it in a clean, dry environment.
- Parameter Coordination: Develop synergy between wire feed rate, laser power, and travel speed. Perform test welds to fine-tune synchronization.
Preventive Measures and Best Practices
Implementing preventive strategies can dramatically reduce the incidence of the problems discussed above. By integrating the following best practices into daily operations, organizations can minimize downtime, maximize weld quality, and ensure a safer work environment.
Thorough Material Testing and Selection
- Conduct weldability assessments before production runs.
- Choose materials and filler metals designed to work with laser welding.
Strict Parameter Documentation
- Maintain a database of optimal laser settings (power, speed, focus) for each material and joint type.
- Regularly update these settings based on feedback from quality control.
Quality Assurance Practices
- Use real-time monitoring tools (e.g., melt pool imaging, infrared sensors) to detect defects early.
- Perform non-destructive testing (NDT) methods, such as X-ray or ultrasonic examination, on critical welds.
Detailed Maintenance Schedules
- Clean and inspect optics (lenses, mirrors) on a fixed schedule.
- Monitor cooling systems, gas flow lines, and mechanical drives for wear or leaks.
- Calibrate laser power output and focusing mechanisms periodically.
Robust Training Programs
- Ensure that operators fully understand how to set up, adjust, and troubleshoot the laser welding process.
- Provide refresher courses and advanced training as technology evolves.
Use of Advanced Technologies
- Incorporate automated beam alignment systems.
- Invest in closed-loop controls that can adapt laser power or speed in real-time.
- Explore hybrid laser welding (laser + arc, or laser + filler wire) for challenging materials or thick sections.
Safe Work Environment
- Implement proper laser safety measures, including eyewear, shielding, and warning signs.
- Provide ergonomically sound workstations and fixtures.
By prioritizing these best practices, organizations can not only mitigate the most common laser welding problems but also build a reputation for high-quality, reliable welded components.
Summary
Laser welding machines have revolutionized metal joining in numerous industries, offering high precision, minimal distortion, and consistent weld quality. However, the technology comes with its own set of challenges. Common problems—such as porosity, cracking, spatter, inconsistent penetration, distortion, and issues with reflective materials—often traced back to a combination of parameter mismanagement, material incompatibilities, equipment maintenance lapses, and human error.
Addressing these challenges requires a holistic approach. It begins with a thorough understanding of the laser welding process fundamentals—laser power, speed, focal position, material characteristics, and gas coverage. Next, implementing robust preventive and mitigation strategies can reduce the incidence of defects. This includes meticulous part and surface preparation, careful monitoring and control of welding parameters, regular machine maintenance, and rigorous operator training.
In essence, the key to overcoming the common problems associated with laser welding machines lies in technical expertise, disciplined process control, and forward-looking adoption of emerging innovations. With these elements in place, laser welding will continue to stand at the forefront of modern manufacturing—reliably delivering high-quality, high-performance welds that meet the exacting demands of industries around the world.
Get Laser Welding Solutions
Achieving consistently high-quality laser welds requires a well-rounded strategy that addresses both technological and operational factors. First, select a laser welding machine that matches your material and production requirements; high-performance systems from Maxcool CNC ensure stable power output and accurate beam delivery. Next, optimize welding parameters—such as laser power, travel speed, and focal position—to maintain a stable keyhole and proper penetration depth. Incorporate real-time monitoring tools to detect defects early and automatically adjust parameters as needed.
Equally important, keep your equipment well-maintained, focusing on clean optics, reliable cooling systems, and secure fixturing that minimizes motion inaccuracies. Comprehensive training equips operators to diagnose issues like porosity or cracks and implement rapid corrective actions. Finally, ensure proper safety and environmental controls, including effective shielding gas coverage and fume extraction. By combining robust machinery, precise process control, and skilled operators, you can overcome common laser welding challenges and achieve optimal weld quality.