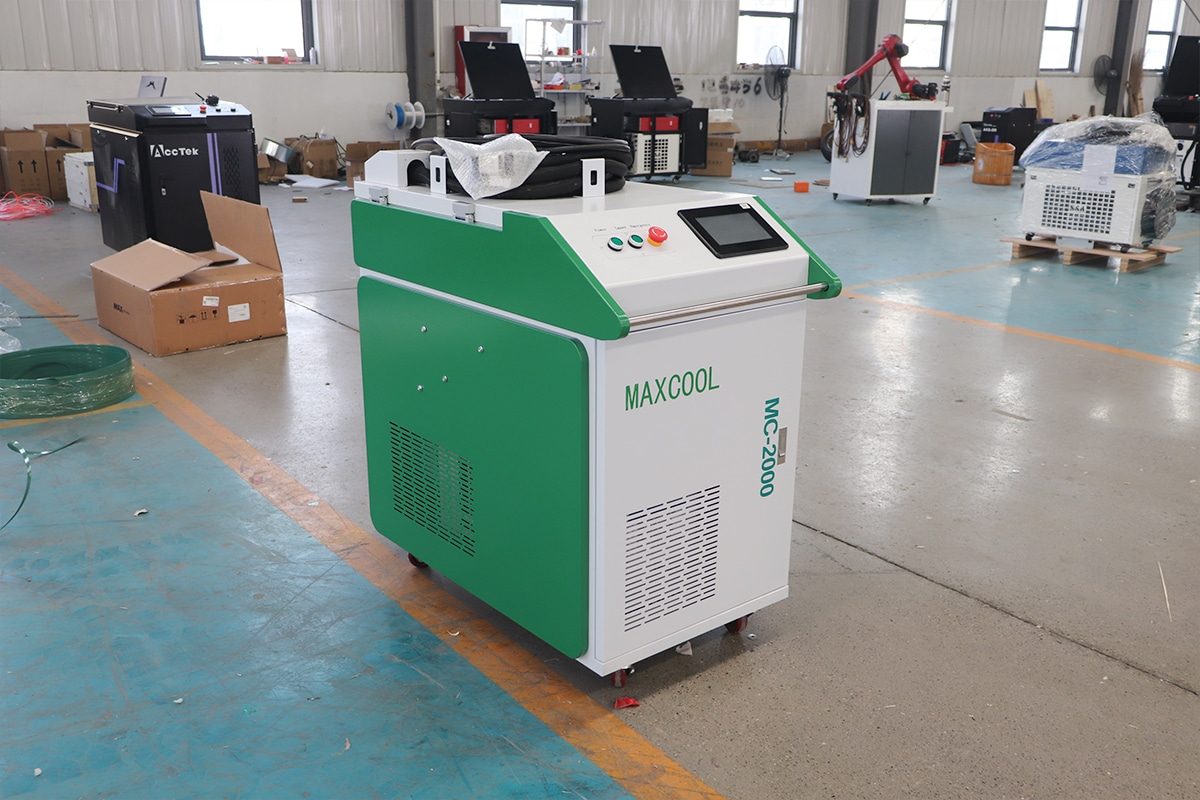
What Is Laser Cleaning?
Mechanism of Action
- The laser energy is absorbed by the contaminants or coatings on the surface.
- The intense, localized heat causes the impurities to vaporize, crack, or be lifted away from the material underneath.
- Because the laser parameters (power, pulse width, frequency, scanning speed, etc.) can be precisely controlled, the process can be finely tuned to avoid damaging the underlying substrate—at least in theory.
Applications
- Removing rust from metals, including steel, iron, and other alloys.
- Stripping paint or coatings in a way that leaves the base material intact.
- Cleaning molds, historical artifacts, or other objects that are sensitive to mechanical abrasion.
- Preparing surfaces for welding, bonding, or further processing by eliminating residual contaminants.
Advantages
- No need for chemical solvents or abrasive media, reducing environmental impact.
- Minimal damage risk for many materials (when carefully operated).
- High precision and repeatability, which are ideal for automated or robotic applications.
- Often a relatively clean process with low waste—just the removed material or dust.
Challenge of Parameter Selection and Optimization
Understanding Laser Parameters
One of the earliest and most persistent issues users face is determining the correct laser parameters for a given cleaning task. Laser cleaning machines typically offer adjustable settings—such as power, pulse duration, repetition rate (frequency), and scanning speed. Each of these must be tuned for the specific substrate and the contaminant.
- Power: A higher wattage enables more rapid material removal but raises the risk of heating or damaging the substrate.
- Pulse Duration: The length of each laser pulse, which influences how quickly energy is delivered. Short pulses can concentrate energy more effectively but also require careful control to prevent surface micro-cracking.
- Repetition Rate: Measured in Hertz (Hz), this determines how many pulses per second the laser fires. An inappropriate repetition rate might either waste energy or fail to remove contaminants effectively.
- Scanning Speed: How quickly the laser beam moves over the surface. A slower speed may allow deeper penetration into stubborn contaminants, but it can also lead to overheating or inefficiency.
Consequences of Incorrect Settings
In practice, if an operator chooses incorrect parameters, the cleaning efficiency and quality can suffer. For instance:
- Insufficient Power or Inappropriate Parameters: The laser might fail to remove thick layers of rust or paint, or the process might be so slow as to be unfeasible for production.
- Excessive Power: Overheating, discoloration, or even ablation of the base material can occur. This is particularly problematic with delicate or high-value components, such as aerospace parts or historical artifacts.
- Mismatch of Pulse Duration and Material Response: You might see micro-cracks or changes in surface properties if the pulses are too intense or too short.
Best Practices for Optimization
- Material Testing: Before full-scale cleaning, conduct test runs with coupon samples or inconspicuous areas.
- Parameter Libraries: Some laser cleaning machine providers, including Maxcool CNC, supply recommended parameter presets for common materials.
- Real-Time Monitoring: Use sensors—such as camera vision systems or thermal sensors—to adjust parameters on the fly.
- Progressive Trials: Start with moderate power and gradually increase until the desired cleaning rate is achieved without causing damage.
Potential Surface Damage
Understanding the Risk
While laser cleaning is frequently lauded for its non-contact and selective nature, it’s not entirely risk-free when it comes to damaging the surface being cleaned. High-intensity laser beams can cause micro-abrasion, melting, or discoloration on sensitive materials if not carefully applied.
- Thermal Damage: If the laser dwell time is too long or the power is too high, the surface can heat up, potentially altering its microstructure or causing warping.
- Surface Roughening: For certain materials—especially softer metals or specific polymers—the ablation process can roughen the surface if the laser pulses remove minute amounts of the substrate along with the contaminant.
- Color Changes: Discoloration or slight oxidation might appear if the substrate temperature rises or if there is an interaction with ambient oxygen during the cleaning process.
Scenarios Where Damage Is Common
- Historical Artifact Restoration: Laser cleaning is a popular choice for art conservation, but the delicate nature of some artifacts means the cleaning parameters must be extremely carefully chosen.
- Thin or Highly Reflective Surfaces: Stainless steel, aluminum alloys, and other reflective materials can become susceptible to local hotspots or uneven cleaning patterns.
- Composites and Plastics: The different layers within composites can respond to heat in unpredictable ways, while plastics can easily melt or deform if the laser energy is excessive.
Preventive Measures
- Pulse Modulation: Employ shorter pulses and adjust the repetition rate to limit how much heat accumulates in the material.
- Gentle Cleaning Approach: For delicate substrates, use multiple low-intensity passes rather than a single high-power pass.
- Advanced Beam Shaping: Some modern laser systems can shape or distribute the beam to reduce hotspots and achieve a more uniform energy distribution.
- Thermal Management: Use cooling techniques or position the workpiece so that heat can dissipate more effectively.
Laser Safety Concerns
The Nature of Laser Hazards
Laser beams, by definition, concentrate a large amount of energy into a small area. Depending on the laser class and power, these beams can pose risks to human operators if not properly contained or if personal protective equipment (PPE) is not used. Some of the main safety considerations include:
- Eye Exposure: Even diffused or reflected beams at certain wavelengths can cause permanent eye damage.
- Skin Burns: Direct contact with high-power laser beams can burn skin or ignite flammable materials.
- Fumes and Particulates: Laser ablation can generate dust or hazardous fumes, particularly when vaporizing coatings that contain heavy metals or other toxins.
Common Oversights in Laser Safety
- Inadequate Enclosures or Barriers: Open-beam setups can increase the risk of accidental exposure, especially if the laser is used in a busy environment.
- No Eye Protection: Operators may overlook the critical importance of protective eyewear rated for the specific laser wavelength.
- Lack of Training: Many accidents happen because untrained personnel operate or stand near laser equipment without being aware of the potential hazards.
- Poor Ventilation: If the fumes generated during cleaning are not properly extracted, operators can be exposed to toxic substances.
Compliance and Mitigation
- Class 1 Laser Systems: Ideally, laser cleaning machines are integrated into enclosures that bring them down to a “Class 1” rating, meaning the laser radiation is safely contained.
- Protective Equipment: Specialized goggles, gloves, and sometimes face shields are necessary, depending on the application.
- Fume Extraction: An industrial-grade ventilation system or local exhaust setup should filter out hazardous particulates or gases.
- Regular Training and Audits: Routine safety training for all operators and periodic reviews ensure that protocols are followed.
High Initial Capital Cost
Financial Considerations
One of the most cited barriers to adopting laser cleaning is the upfront expense. While the exact price varies depending on power rating, brand, and additional features, laser cleaning systems often cost more than simpler mechanical or chemical methods. The capital investment may include:
- Laser Source: Fiber or solid-state lasers are costly pieces of technology, particularly in higher wattage ranges.
- Beam Delivery System: This can range from handheld scanning heads to fully robotic or automated stages.
- Safety Enclosures: Enclosures, fume extractors, and other safety-related peripherals also add to the total cost.
- Integration Costs: For industrial use, you might need to integrate the laser cleaning machine into a production line, adding engineering and software expenses.
Long-Term Economic Benefits
Despite the higher initial cost, laser cleaning can pay for itself over time due to:
- Lower Consumable Expenses: No chemicals, blasting media, or frequent replacement parts are generally required.
- Reduced Waste Disposal: Traditional methods often incur significant costs to dispose of used abrasives or solvents.
- Automation and Labor Savings: Automated laser cleaning can reduce manual labor and associated expenses.
- Enhanced Quality: Better cleaning results can lead to fewer defects and rework in subsequent processes.
Strategies to Overcome Cost Barriers
- Leasing or Rental Options: Some suppliers or third-party providers offer flexible financing models that reduce the upfront burden.
- Government Incentives: In certain regions, there may be grants or tax credits for adopting greener, more energy-efficient technologies.
- Shared Ownership: Smaller companies might pool resources, allowing multiple parties to use the same system at different times.
- Phased Implementation: Start with a lower-power or smaller-scale system and scale up as efficiency gains and cost savings materialize.
Maintenance and Upkeep Challenges
Nature of Maintenance Requirements
While laser cleaning technology is designed for reliability, the system still comprises several components that can require upkeep:
- Laser Source: Although fiber lasers are known for long lifespans, they do have certain cooling and alignment needs.
- Optical Components: Lenses, mirrors, and protective windows can become contaminated or damaged by dust, debris, or splatter.
- Cooling Systems: Many laser cleaning machines use water or air-cooled systems to maintain the correct operating temperature. If these systems fail, the laser’s performance may degrade.
- Motion Control: Mechanical axes, galvanometers, or robotic arms must be lubricated, calibrated, and kept free of dirt.
Common Problems Stemming From Poor Maintenance
- Optical Degradation: When the lens or protective window becomes dirty or scratched, it can alter the beam profile or reduce laser power, leading to uneven cleaning.
- System Downtime: Neglected cooling systems might overheat, triggering automatic shutdowns or even permanent damage.
- Inconsistent Results: A misaligned beam can create stripes, streaks, or patchy cleaning patterns on the surface.
- Shortened Laser Life: Over time, inadequate maintenance can stress the laser source itself, requiring costly repairs or replacements.
Best Practices for Maintenance
- Scheduled Cleaning: Regularly inspect and clean optics with appropriate materials and procedures. Use only approved solvents and lint-free wipes for cleaning lenses.
- Preventive Checklists: Develop weekly or monthly checklists for verifying coolant levels, checking airflow, and ensuring mechanical components are lubricated.
- Log Operational Hours: Keep track of the system’s runtime and perform recommended service tasks at the intervals specified by the manufacturer.
- Staff Training: Equip operators with the knowledge to recognize early warning signs—such as unusual noises, temperature fluctuations, or drops in cleaning efficiency.
Operator Training and Skill Requirements
Complexity of Operation
Although laser cleaning is often marketed as user-friendly, some level of technical knowledge is essential to handle the equipment properly and adjust parameters for different applications. This complexity includes:
- Understanding Material Properties: Different substrates respond differently to laser energy.
- Parameter Mastery: Selecting power, pulse width, frequency, and scanning speed is not always straightforward.
- Diagnostic Skills: Operators need to spot issues such as beam misalignment, dirty optics, or parameter mismatch before serious problems arise.
Consequences of Insufficient Training
- Lower Cleaning Quality: Inexperienced users may fail to fully remove contaminants or, conversely, damage the surface.
- Safety Risks: Without proper instruction, operators might neglect critical safety procedures, putting themselves and colleagues at risk.
- Wasted Time and Resources: Trial-and-error learning can lead to wasted laser hours, potential part rejections, and inefficiency.
Building a Skilled Workforce
- Vendor Training Programs: Many laser system suppliers, including Maxcool CNC, offer on-site or virtual training sessions.
- Mentorship: Pair new operators with experienced staff who can guide them through best practices and common pitfalls.
- Regular Refreshers: Even seasoned users can benefit from periodic retraining, especially as software updates or hardware improvements are introduced.
- Cross-Training: Broaden the skill base by having multiple operators trained, reducing risk if key personnel are absent.
Cleaning Rate and Throughput Issues
Factors Affecting Cleaning Speed
One concern that arises in production environments is whether laser cleaning can match the throughput of other methods. The cleaning rate is influenced by multiple factors:
- Laser Power and Wavelength: Higher-wattage lasers can generally remove contaminants faster. The wavelength also impacts the absorption characteristics of specific materials.
- Contaminant Thickness: Rust that is several millimeters thick demands more time and energy than a thin coating.
- Laser Spot Size: A larger spot can clean a broader area per pass, but may distribute energy more thinly.
- Automation Level: Robotic or automated setups can maintain consistent speeds and reduce idle time between passes.
When Throughput Becomes a Problem
- Heavy Rust Removal in High-Volume Processes: If a manufacturing line requires rapid turnaround, a laser system with insufficient power may create a bottleneck.
- Large Surface Areas: Cleaning an entire ship hull or large industrial equipment might be time-consuming if the machine is not optimized or if the scanning system is too slow.
- Multiple Passes Required: In some scenarios—especially sensitive or intricate parts—multiple low-power passes are safer, but they take more total time.
Optimization Strategies
- Selecting the Appropriate Laser Power: Over time, upgrading to a higher-power laser can greatly improve throughput if your workload justifies it.
- Use of Automation: Robotic arms, linear actuators, or conveyor systems can speed up the process and minimize manual intervention.
- Focus on Critical Zones: Sometimes, only certain areas need thorough cleaning. A targeted approach can cut down total cycle times.
- Combination Methods: In rare cases, you might combine laser cleaning with mechanical pre-removal of thick deposits, then finalize with the laser for precision.
Reflection and Scattering Challenges
The Issue of Reflective Materials
Metals like aluminum, copper, and certain alloys have high reflectivity at specific laser wavelengths. This reflectivity can cause several problems:
- Energy Loss: If much of the laser light is reflected instead of absorbed, cleaning becomes less efficient, requiring more passes or higher power.
- Back-Reflection Damage: In extreme cases, the reflected laser energy can travel back up the beam path, potentially damaging internal optical components.
- Uneven Cleaning: Different surface finishes can exhibit varying levels of reflectivity, leading to patchy results.
How Scattering Complicates Matters
Even materials that aren’t highly reflective can scatter the laser beam if they have irregular or curved surfaces. This scattering can:
- Reduce Effective Energy: A scattered beam loses its intensity compared to a focused beam.
- Cause Overlaps or Missed Spots: When cleaning uneven geometries, certain angles or recessed areas can receive inconsistent laser exposure.
Possible Solutions
- Appropriate Wavelength Selection: Some laser types or wavelengths are better absorbed by certain metals.
- Optical Isolation: Use isolators or specialized coatings on mirrors and lenses to protect the laser source from back-reflections.
- Surface Preparation: In some cases, a preliminary step (like light sanding or applying an absorptive coating) can reduce reflectivity, although this may negate some advantages of laser cleaning’s chemical-free nature.
- Beam Shaping Techniques: Advanced optics can direct energy more uniformly onto curved or complex shapes.
Environmental and Health Regulations
Regulatory Framework
Laser cleaning is often promoted as an eco-friendly alternative because it eliminates the need for harsh chemicals or abrasive media. However, the process can still fall under various regulations:
- Fume Emissions: The ablation process may create gases or particulates subject to occupational health regulations.
- Noise Levels: Some systems produce noise from the laser or the accompanying extraction systems that must meet workplace standards.
- Worker Safety: Eye protection, laser enclosures, and operational guidelines are often mandated by law (e.g., OSHA in the U.S., EU Directives in Europe).
- Disposal of Removed Material: Even though no chemicals are used, the removed contaminants (e.g., rust, paint particles) must be collected and disposed of responsibly if they contain hazardous components.
Why Non-Compliance Happens
- Misunderstanding the Technology: Some facility managers might assume that because laser cleaning is “cleaner,” it’s automatically free of regulatory obligations.
- Inadequate Extraction Systems: Neglecting to invest in proper ventilation or filtration can lead to air quality violations.
- Overconfidence: Operators may skip routine checks, wrongly assuming that the process is inherently safe or always within legal limits.
Guidelines for Compliance
- Assess Potential Hazards: Conduct a thorough analysis of all byproducts generated by the laser cleaning process, including any potentially toxic coatings.
- Ventilation and Filtration: Install and maintain high-efficiency extraction systems to capture and filter out harmful particulates or fumes.
- Documentation: Keep detailed records of cleaning processes, maintenance schedules, and waste disposal for regulatory audits.
- Training and Signage: Ensure that all staff are educated about laser hazards, required PPE, and safe operation.
Issues with Inconsistent Cleaning Outcomes
Causes of Inconsistency
Nothing frustrates operators more than cleaning that yields uneven or patchy results. Some common culprits include:
- Variable Substrate Condition: Different levels of oxidation, surface roughness, or contamination thickness can lead to inconsistent results if the laser parameters remain the same.
- Beam Instability: Fluctuations in laser power or focal point alignment can produce uneven cleaning patterns.
- Operator Variability: Handheld scanning can introduce inconsistency if technique or speed varies from one pass to another.
Detecting the Problem Early
- Visual Inspection: Spot-checking the cleaned surface for color, brightness, and uniformity.
- Surface Profilometry: More advanced inspections may involve using a profilometer to measure surface roughness.
- Spectroscopic Analysis: Some setups use real-time sensors to detect the presence of contaminants or changes in the material composition.
Steps Toward Consistency
- Robotic or Automated Systems: Automating the scanning process can eliminate operator-induced variability.
- Smart Feedback Loops: Integrate sensors that adjust power or scanning speed based on real-time feedback from the surface.
- Pre-Cleaning Assessment: Evaluate how thick or stubborn the contaminants are, and adjust parameters accordingly.
- Regular Maintenance of Optics: Ensuring the beam is well-aligned and that optical components remain clean is critical.
Thermal Management and Cooling
Why Cooling Matters
Lasers and their accompanying power electronics generate heat during operation. If this heat is not effectively managed, it can degrade performance, limit duty cycles, and even cause damage.
- Thermal Expansion: Temperature fluctuations can alter the alignment of optical components.
- Reduced Efficiency: Overheating can lead to drop-offs in laser power or intermittent shutdowns.
- Component Stress: Electronics and laser diodes can have shorter lifespans if routinely run at high temperatures.
Common Cooling-Related Problems
- Insufficient Coolant Flow: Clogged filters or low coolant levels can lead to poor heat exchange.
- High Ambient Temperatures: Operating the laser in hot environments without adequate HVAC can overwhelm the system’s cooling capacity.
- Inappropriate Coolant: Some lasers require specially treated water or coolants; using tap water can cause mineral deposits or corrosion.
Ensuring Proper Cooling
- Closed-Loop Chillers: These are recommended for more powerful laser systems, providing stable temperatures and filtration to prevent contamination.
- Regular Check-Ups: Monitor coolant levels, pump operation, and temperature sensors on a routine basis.
- Environmental Control: If possible, maintain a controlled environment around the laser cleaning machine.
- Alarm Systems: Modern systems often have sensors that trigger alerts or shut down the laser if the temperature exceeds safe limits.
Handling Delicate or Complex Surfaces
Challenges with Fine Structures
Some cleaning tasks involve objects with complex geometries, intricate patterns, or extremely delicate surfaces. Laser cleaning can reach into small crevices, but there are caveats:
- Limited Beam Access: The beam might not penetrate angles or recesses at a fixed orientation, leaving residues behind.
- Risk of Overcleaning: Fine details can be inadvertently ablated if the laser passes are too energetic or repeated too often.
- Heat Buildup: Small or thin surfaces can heat up quickly, risking distortion.
Strategies for Complex Surfaces
- Multi-Axis Robotic Systems: These allow the laser head to maneuver around curved or complex shapes, ensuring more thorough coverage.
- Adaptive Focusing: Systems that can dynamically adjust the focal distance help maintain optimal beam intensity, even when surfaces vary in height.
- Lower Power, Multiple Passes: This tactic ensures each pass only removes a small amount of the contaminant, reducing the chance of damaging the substrate’s detailed features.
- Customized Fixtures: Securely holding the workpiece in fixtures that rotate or tilt can present surfaces to the laser more effectively.
Dealing with Large-Scale Projects
Scale Limitations
Although laser cleaning excels in many situations, extremely large surfaces—like ship hulls, bridges, or expansive industrial structures—pose their own set of challenges:
- Time Efficiency: Covering hundreds of square meters or more can take a very long time if the laser’s spot size or scanning system is relatively small.
- Mobility and Logistics: Large-scale projects might require portable systems, power supplies, and specialized enclosures or safety zones.
- Environmental Constraints: Working outdoors introduces additional complications like wind, dust, moisture, and temperature fluctuations that can affect beam performance.
Potential Solutions
- High-Power, High-Bandwidth Systems: More robust lasers with larger scanning fields reduce the number of passes needed.
- Modular or Mobile Equipment: Some manufacturers offer mobile laser cleaning units housed in shipping containers or on trailers.
- Segmentation of Work Area: Clean the surface in sections, using consistent parameters while ensuring safety measures are adapted for each zone.
- Combination Approaches: In very large projects, a hybrid approach—mechanical removal for the bulk of the contaminants followed by laser finishing—may be more viable.
Energy Consumption Concerns
Power Draw of Laser Systems
Laser cleaning can be energy-intensive, especially if using higher-power lasers (hundreds to thousands of watts). Operators concerned about sustainability or energy costs often question whether the energy usage justifies the cleaning outcome.
- Laser Efficiency: Fiber lasers are generally more efficient than older CO2 or Nd: YAG lasers, but they still draw significant power at higher wattages.
- Peripheral Systems: Chillers, dust extraction units, and control electronics also add to the total energy consumption.
Operational VS. Overall Energy Footprint
When considering overall environmental impact, note that laser cleaning often replaces methods involving chemicals, abrasives, or significant amounts of water—each of which has its own energy and ecological footprint.
- Chemical Production and Disposal: The energy used to manufacture and transport solvents can be considerable.
- Waste Management: Disposing of contaminated media or liquids adds additional environmental costs.
- Water Usage: Abrasive blasting or chemical baths can require large volumes of water, which then need treatment or disposal.
Optimizing Energy Use
- Energy-Saving Modes: Modern laser systems often include standby modes that reduce power consumption when the machine is idle.
- Process Efficiency: Optimizing parameters to achieve the desired level of cleanliness in fewer passes also reduces total energy consumption.
- System Sizing: Choose a laser power level appropriate to the task. Oversized systems can waste energy if consistently run at a fraction of their capacity.
- Facilities Management: Ensure that the environment is well-managed so cooling and extraction systems run efficiently.
Upgrades and Technological Evolution
Rapid Advances in Laser Technology
The laser industry is continuously evolving. New wavelengths, higher power diodes, better beam shaping, and more efficient cooling systems come to market regularly. Owners of laser cleaning machines sometimes struggle with how to keep pace:
- Obsolescence: A machine purchased even a few years ago may not feature the latest efficiency or safety upgrades.
- Compatibility: Upgrading the laser source or scanning head might require changes to power supplies, control software, or cooling systems.
Strategies for Future-Proofing
- Modular Designs: Systems designed with interchangeable modules (e.g., a separate laser source, scanning head, and control unit) can be updated piece by piece without replacing the entire machine.
- Extended Service Agreements: Some manufacturers offer ongoing hardware or software upgrade paths for existing customers.
- Close Collaboration with Vendors: Regular communication with the machine supplier can keep you informed of new features or improvements that might benefit your operation.
Availability of Replacement Parts and Service
Supply Chain Realities
Laser cleaning machines, like all high-tech equipment, rely on specialized parts—particularly the laser source and optical components. Delays or shortages in obtaining these parts can cause extended downtime:
- Global Sourcing: Certain components, such as diodes or specialized optics, might come from overseas suppliers. Political or economic disruptions can impact lead times.
- Proprietary Designs: If a particular part is custom-made for a manufacturer, you might have fewer options for sourcing replacements.
Mitigation Steps
- Spare Parts Inventory: Keep critical spares in stock, especially items prone to wear or damage (lenses, protective windows, filters).
- Service Contracts: Some manufacturers offer priority service or guaranteed response times if you enter into a maintenance agreement.
- Local Partners: Working with local distributors or service centers can reduce shipping times and costs.
Balancing Cost, Safety, and Performance
The Trilemma
Many of the challenges discussed can be summarized by the struggle to balance cost, safety, and performance. Each variable influences the others:
- Higher Power: Improves throughput and cleaning capability but increases cost and safety risks.
- More Extensive Safety Measures: Ensures compliance but can add to capital and operational expenses.
- Lower Costs: Potentially means choosing a less powerful or feature-rich system that might limit performance or reliability.
Finding the Right Configuration
Operators must carefully assess their specific needs:
- Nature of Contaminants: High-power systems are more crucial for thick coatings or severe corrosion.
- Production Volume: If you need rapid throughput, automation, and higher-power lasers may be justified.
- Regulatory Environment: Stricter safety and environmental laws might necessitate more extensive enclosures, filtering systems, or documentation.
- Budget Constraints: Companies must consider the total cost of ownership, not just the purchase price.
Real-World Case Study Highlights
To bring these challenges into sharper focus, consider a fictionalized example based on common industry scenarios:
- Scenario: A mid-sized manufacturing company decides to adopt a laser cleaning solution to remove paint from aluminum components before welding.
- Problem Encountered: Inconsistent cleaning results with some spots still showing residual paint and the occasional discoloration of the aluminum.
- Root Causes:
- The operator used default parameters that were better suited for steel, not aluminum.
- The scanning speed was too high, reducing the dwell time on stubborn areas.
- Optical contamination occurred because the protective window was not regularly cleaned, causing uneven power distribution.
- Solutions Implemented:
- Adjusted the power, frequency, and scanning speed specifically for aluminum.
- Devised a maintenance schedule for cleaning and inspecting the optics.
- Trained operators on how to spot incomplete paint removal in real time.
- Outcome: Consistent paint removal, improved weld quality, and a notable reduction in rework.