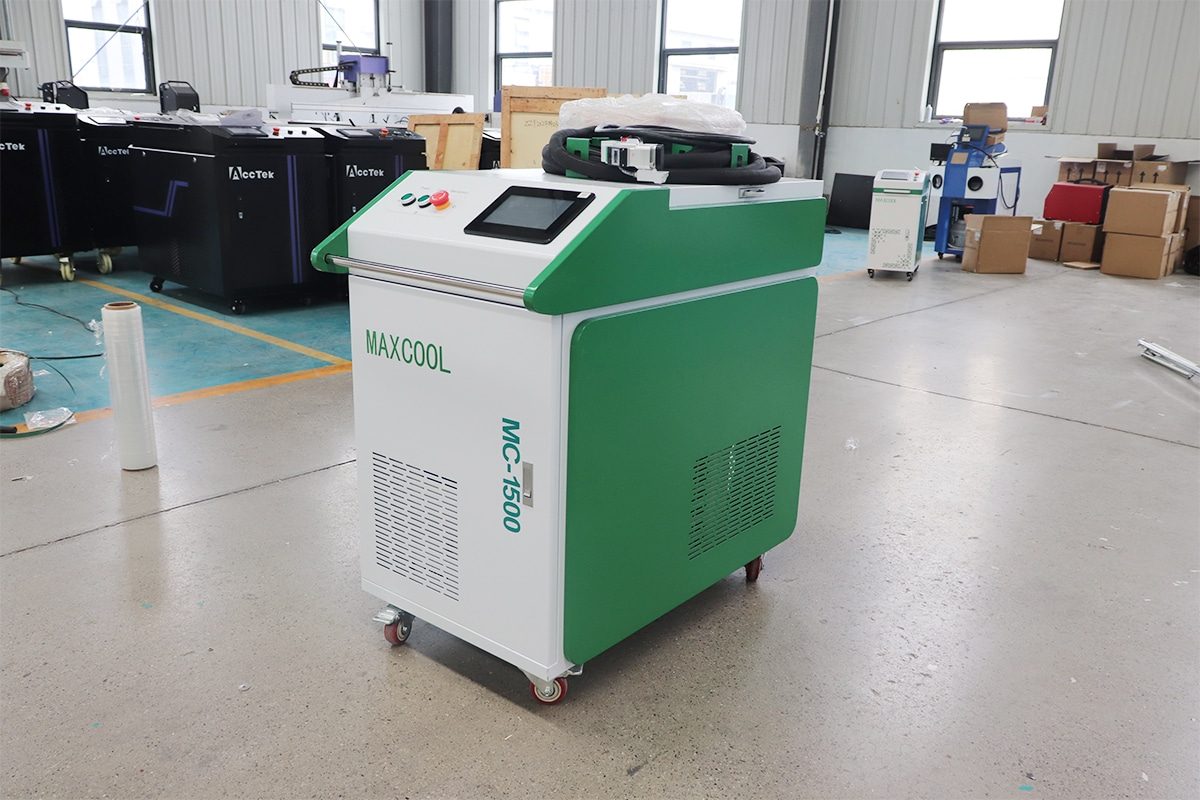
Understanding Laser Cleaning Technology
What Is Laser Cleaning?
Principles of Laser-Material Interaction
Absorption of Laser Energy
Thermal Effects
The absorbed laser energy increases the temperature of the contaminants rapidly. This rapid heating can cause:
- Thermal Expansion: The sudden temperature rise leads to thermal expansion of the contaminant layer, creating mechanical stress at the interface between the contaminant and the substrate.
- Vaporization and Sublimation: If the temperature exceeds the boiling point of the contaminant material, it vaporizes or sublimates, effectively removing it from the surface.
Photophysical and Photochemical Reactions
High-intensity laser irradiation can induce photophysical and photochemical reactions within the contaminant layer:
- Photophysical Ablation: The laser energy breaks the bonds within the contaminant material, causing it to disintegrate into smaller particles or gaseous byproducts.
- Photochemical Decomposition: The laser may trigger chemical reactions that alter the contaminant’s composition, making it easier to remove.
Plasma Formation
Minimal Heat Affected Zone (HAZ)
Key Laser Parameters Influencing Interaction
- Wavelength: Determines how deeply the laser penetrates the material and which materials absorb the energy.
- Pulse Duration: Short pulses (nanoseconds to femtoseconds) reduce thermal effects on the substrate.
- Energy Density (Fluence): Controls whether the laser induces surface heating, melting, or ablation.
- Repetition Rate: Affects the overall speed of cleaning and potential heat accumulation.
Advantages of Laser Cleaning Over Traditional Methods
Laser cleaning offers numerous benefits compared to conventional cleaning techniques, making it an attractive option for various industries:
- Non-Contact and Non-Abrasive: Laser cleaning does not require physical contact with the surface, eliminating mechanical stress or abrasion that could damage delicate components. This non-contact approach preserves the substrate’s integrity and extends the lifespan of equipment.
- High Precision and Selectivity: The ability to precisely control laser parameters enables selective cleaning of contaminants without affecting the underlying material. This is particularly beneficial for applications requiring fine detail or when working with sensitive substrates.
- Environmentally Friendly: Laser cleaning eliminates the need for chemical solvents and reduces the production of secondary waste like blasting media. This results in fewer environmental hazards and lower disposal costs, aligning with increasingly stringent environmental regulations.
- Reduced Operational Costs: While the initial investment may be higher, laser cleaning reduces long-term costs associated with consumables, waste management, and maintenance. The process is often faster and requires less labor, improving overall efficiency.
- Improved Safety: By avoiding hazardous chemicals and reducing airborne pollutants, laser cleaning creates a safer working environment. Operators are less exposed to toxic substances, and the need for personal protective equipment is minimized.
- Versatility Across Materials: Laser cleaning is effective on a wide range of materials, including metals, ceramics, plastics, and composites. This versatility makes it suitable for diverse applications across multiple industries.
- Automation and Integration: Laser cleaning systems can be easily integrated into automated production lines, allowing for consistent and repeatable cleaning processes. This automation enhances productivity and ensures high-quality results.
- Minimal Waste Generation: The process produces minimal waste, often only the vaporized contaminants, which can be managed with proper ventilation and filtration systems. This contrasts with traditional methods that generate significant solid or liquid waste.
- Enhanced Surface Preparation: Laser cleaning not only removes contaminants but can also modify surface properties to improve adhesion for coatings, paints, or adhesives. This dual function streamlines processes and enhances product performance.
- Energy Efficiency: Advancements in laser technology have led to more energy-efficient systems, reducing operational costs and environmental impact.
Pulse Laser Cleaning Machines
Working Principle
Key aspects of the working principle include:
- Selective Absorption: Contaminants typically absorb laser energy more effectively than the substrate due to differences in optical properties. This allows the laser to target and remove unwanted layers while leaving the base material largely unaffected.
- Minimal Thermal Diffusion: The extremely short duration of laser pulses limits heat transfer to the substrate, reducing the risk of thermal damage or alteration of material properties.
- Precise Energy Control: Adjustable laser parameters—such as wavelength, pulse duration, energy density, and repetition rate—enable fine-tuning of the cleaning process for different materials and contaminants.
Advantages
Pulse laser cleaning machines offer several significant advantages:
- High Precision and Selectivity: The ability to deliver energy in controlled pulses allows for precise removal of contaminants without damaging the underlying substrate. This makes pulse lasers ideal for applications requiring meticulous detail or when working with sensitive materials.
- Minimal Thermal Impact: Short pulse durations minimize heat diffusion into the substrate, reducing the risk of thermal deformation, micro-cracking, or changes in material properties. This is particularly important when cleaning heat-sensitive components.
- Versatility Across Materials: Pulse lasers are effective on a wide range of materials, including metals, ceramics, polymers, and composites. They can remove various contaminants such as oxides, coatings, residues, and micro-particulates.
- Controlled Material Removal: Adjustable laser parameters enable selective layer-by-layer removal, allowing for the stripping of thin films or specific coatings without affecting underlying layers. This level of control is beneficial for processes like paint stripping or oxide layer removal.
- Improved Surface Quality: The non-contact nature and precision of pulse laser cleaning can enhance surface properties, improving adhesion for coatings or bonding applications. It leaves the substrate clean and free of residues without introducing abrasives or chemicals.
Disadvantages
Despite their advantages, pulse laser cleaning machines have some limitations:
- Higher Initial Investment: Pulse laser systems are generally more complex and costly due to the advanced technology required to generate high-energy pulses with precise control. This can result in a higher upfront investment compared to continuous laser systems.
- Slower Cleaning Speeds for Thick Layers: While pulse lasers excel at precision cleaning, they may be less efficient at removing thick contaminants or coatings quickly. The process can be time-consuming for large-scale cleaning where high material removal rates are needed.
- Technical Complexity: Operating pulse laser systems requires specialized knowledge to optimize parameters for different materials and contaminants. This may necessitate additional training or hiring skilled personnel, potentially increasing operational costs.
- Maintenance and Operational Costs: The sophisticated components of pulse lasers may demand more frequent maintenance and calibration to ensure consistent performance. Replacement parts and service can be more expensive due to the complexity of the technology.
Applications
Pulse laser cleaning machines are ideal for applications that demand precision and minimal impact on the substrate:
- Circuit Board Cleaning: Removing oxides, flux residues, and contaminants from printed circuit boards (PCBs) without damaging delicate traces or components.
- Semiconductor Fabrication: Precision cleaning of wafers and microelectronic devices where even microscopic contaminants can affect performance.
- Artifact Conservation: Gently removing soot, pollutants, biological growth, or overpainting from historical artifacts, sculptures, and paintings while preserving the original material.
- Surface Preparation: Cleaning turbine blades, engine components, and airframe surfaces to improve bonding, coating adhesion, or to prepare for non-destructive testing.
- Sterilization and Cleaning: Removing contaminants from surgical instruments, implants, and medical equipment where sterility and precision are critical.
- Mold and Die Cleaning: Cleaning molds and dies used in injection molding or casting without altering their dimensions or surface finish, extending tool life.
- Maintenance of Precision Instruments: Removing residues from high-precision tools and equipment to maintain accuracy and performance.
- Component Cleaning: Cleaning engine parts, transmission components, and other precision parts to remove oils, greases, and residues before assembly.
- Surface Treatment: Preparing surfaces for welding or bonding by removing contaminants and creating optimal surface conditions.
- Material Analysis: Controlled removal of layers for surface analysis or sample preparation in materials science and nanotechnology research.
Continuous Laser Cleaning Machines
Working Principle
Key aspects of the working principle include:
- Steady Energy Delivery: The continuous laser provides constant power output, resulting in uniform heating of the contaminant layer.
- Thermal Interaction: Prolonged exposure to laser energy increases the temperature of both the contaminant and, to some extent, the substrate, facilitating the removal of unwanted material.
- Removal Mechanisms: Contaminants are removed through thermal effects such as melting, evaporation, or thermal shock due to temperature gradients.
Advantages
Continuous laser cleaning machines offer several notable advantages:
- High Material Removal Rate: The constant energy delivery of continuous lasers enables the rapid removal of thick layers of contaminants such as heavy rust, paint, or coatings. This makes them highly effective for large-scale cleaning tasks where speed is essential.
- Efficiency for Large Areas: Continuous lasers are well-suited for cleaning extensive surfaces due to their ability to maintain consistent power output over time. This leads to efficient processing of large components or structures without frequent interruptions.
- Simpler System Design: The technology behind continuous lasers is generally less complex than that of pulsed lasers. This simplicity can result in more robust equipment with potentially lower maintenance requirements.
- Cost-Effective: Continuous laser systems often have a lower initial cost compared to pulsed laser systems. They can be a more economical choice for applications that do not require the precision of pulsed lasers.
- Ease of Operation: With fewer parameters to adjust compared to pulsed lasers, continuous laser cleaning machines can be easier to operate, reducing the need for specialized training.
Disadvantages
Despite their benefits, continuous laser cleaning machines have some limitations:
- Increased thermal effects: Continuous delivery of laser energy results in increased heat input to the contaminant and substrate. This increased heat load can cause thermal damage or a larger heat-affected zone.
- Reduced Precision: Continuous lasers may not offer the same level of precision as pulsed lasers. They are less suitable for applications requiring selective removal of thin layers or cleaning of delicate or heat-sensitive materials.
- Limited Material Compatibility: Not ideal for cleaning substrates that are sensitive to heat or for removing contaminants that require precise energy control for effective removal.
- Possible Oxidation: The higher temperatures generated during continuous laser cleaning can sometimes lead to oxidation of the substrate surface, which may necessitate additional post-cleaning treatments.
Applications
Continuous laser cleaning machines are best suited for applications where high power and fast cleaning of robust materials are required:
- Rust and Scale Removal: Efficiently removing heavy rust, mill scale, and corrosion from steel structures, pipes, and large machinery components.
- Surface Preparation: Cleaning and preparing metal surfaces for welding, painting, or coating in industries such as shipbuilding, automotive manufacturing, and construction.
- Hull Cleaning: Removing marine growth, old paint layers, and corrosion from ship hulls and offshore structures.
- Refinery Equipment Cleaning: Maintaining heat exchangers, reactors, and other equipment where heavy fouling occurs.
- Large Component Cleaning: Removing coatings and contaminants from sizable aerospace components where precision is less critical.
- Chassis and Bodywork Cleaning: Preparing surfaces for painting or coating by removing rust, dirt, and old paint from vehicle frames and body panels.
- Weld Seam Cleaning: Removing oxide layers and discoloration from weld seams to improve appearance and prevent corrosion.
- Deburring and Descaling: Eliminating burrs and scale from metal parts post-fabrication.
- Bridge and Structural Cleaning: Removing corrosion and old coatings from bridges, railings, and other infrastructure components to prepare for repainting or repair.
- Industrial Molds and Dies: Cleaning large molds used in industries like tire manufacturing, where buildup can affect product quality.
Pulse vs. Continuous Laser Cleaning Machines
Comparison of Working Principles
Pulse Laser Cleaning Machines
Key Characteristics:
- Selective Absorption: Contaminants absorb the laser energy more effectively than the substrate due to differences in optical properties.
- Minimal Heat Affected Zone (HAZ): Short pulses reduce thermal conduction to the substrate.
- Precision Cleaning: Allows for controlled removal of thin layers or specific contaminants.
Continuous Laser Cleaning Machines
Key Characteristics:
- Steady Energy Input: Provides consistent power for uniform cleaning over large areas.
- Higher Average Power: Suitable for rapid removal of heavy contaminants.
- Thermal Interaction: Increased heat may affect both the contaminant and substrate.
Comparison of Performance Metrics
Cleaning Speed
- Pulse Lasers: Generally slower when removing thick or heavy contaminants due to lower average power. Ideal for applications where precision is more critical than speed.
- Continuous Lasers: Offer faster cleaning speeds for large areas and thick layers, making them suitable for industrial applications requiring high throughput.
Precision and Selectivity
- Pulse Lasers: Provide high precision and control, enabling selective removal of contaminants without damaging the substrate. Suitable for delicate or detailed work.
- Continuous Lasers: Less precise due to continuous energy delivery; better suited for applications where fine detail is less critical.
Thermal Impact
- Pulse Lasers: Minimal thermal impact with a small heat-affected zone, reducing the risk of thermal damage to the substrate.
- Continuous Lasers: Greater thermal impact can lead to substrate heating, potential warping, or alteration of material properties.
Surface Quality
- Pulse Lasers: Produce cleaner surfaces with minimal oxidation and residue, improving adhesion for coatings or treatments.
- Continuous Lasers: This may cause surface oxidation or roughening due to higher heat input, possibly requiring additional post-processing.
Material Removal Rate
- Pulse Lasers: Lower material removal rates, suitable for removing thin layers or fine contaminants.
- Continuous Lasers: Higher material removal rates, effective for removing thick layers of rust, paint, or coatings.
Material Compatibility
Pulse Lasers
- Heat-Sensitive Materials: Ideal for cleaning substrates like plastics, composites, or thin metals that are sensitive to heat.
- Delicate Components: Suitable for applications in electronics, aerospace, and medical industries where precision is paramount.
- Varied Contaminants: Effective at removing oxides, thin coatings, and micro-contaminants.
Continuous Lasers
- Robust Materials: Best suited for cleaning sturdy materials such as steel, iron, and other metals capable of withstanding higher temperatures.
- Heavy Contaminants: Effective at removing thick rust, heavy paint layers, and substantial coatings.
- Large Surfaces: Suitable for cleaning large structures where precision is less critical.
Energy Consumption
Pulse Lasers
- Lower Average Power Consumption: Due to the pulsed nature, energy is delivered in short bursts, resulting in lower overall power usage.
- Efficiency in Precision Applications: Energy is utilized effectively for removing specific contaminants, and reducing waste.
Continuous Lasers
- Higher Average Power Consumption: Continuous operation at higher power levels leads to increased energy usage.
- Efficiency in Large-Scale Cleaning: Despite higher energy consumption, they may be more efficient for rapid cleaning of extensive areas.
Cost Considerations
Initial Investment
- Pulse Lasers: Generally have a higher upfront cost due to advanced technology and precision components.
- Continuous Lasers: Typically have a lower initial cost, making them more accessible for some businesses.
Operational Costs
- Pulse Lasers: These may incur higher maintenance costs due to complex components but can be more cost-effective for precision cleaning tasks.
- Continuous Lasers: A simpler design can lead to lower maintenance costs, but higher energy consumption may increase operational expenses.
Return on Investment (ROI)
- Pulse Lasers: Offer a better ROI in applications where precision and substrate preservation are critical.
- Continuous Lasers: Provide a quicker ROI in heavy-duty cleaning applications where speed and efficiency are prioritized.
Safety Aspects
Pulse Lasers
- Eye Safety: High peak power necessitates stringent safety measures to protect against potential eye damage.
- Material Ejection: Rapid ablation can eject particles; appropriate shielding and extraction systems are required.
- Thermal Risks: Minimal, but localized heating can still pose burn hazards.
Continuous Lasers
- Eye Safety: Continuous beams also require strict safety protocols to prevent eye injuries.
- Heat Exposure: Higher heat generation increases the risk of burns; protective equipment is essential.
- Fume Generation: Thermal decomposition of contaminants can produce fumes; effective ventilation and filtration systems are necessary.
Factors to Consider When Choosing Between Pulse and Continuous Lasers
Material Type
Substrate Sensitivity
- Heat Sensitivity: If the substrate is sensitive to heat—such as thin metals, plastics, composites, or delicate components—a pulse laser cleaning machineis preferable. The minimal thermal impact due to short pulse durations reduces the risk of warping, melting, or altering the substrate’s properties.
- Robust Materials: For substrates that can withstand higher temperatures, like thick steel or iron, a continuous laser cleaning machine may be suitable. The increased thermal input is less likely to damage these robust materials.
Type of Contaminant
- Thin or Delicate Contaminants: Pulse lasers excel at removing thin layers of contaminants, such as oxides, coatings, or surface residues. Their precision allows for selective cleaning without affecting the underlying material.
- Thick or Stubborn Contaminants: Continuous lasers are more effective at removing thick layers of rust, heavy paint, or substantial coatings. Their higher average power and continuous energy delivery enable rapid cleaning of heavy contaminants.
Cleaning Requirements
Precision Needed
- High Precision Applications: If the cleaning task requires meticulous detail and minimal impact on the substrate—such as in electronics manufacturing, aerospace components, or art restoration—a pulse laser cleaning machineis the optimal choice.
- General Cleaning Tasks: For applications where precision is less critical and speed is a priority—like cleaning large machinery or structural components—a continuous laser cleaning machine may be more appropriate.
Area Size
- Small to Medium Areas: Pulse lasers are ideal for cleaning smaller surfaces or components where detailed work is essential.
- Large Surfaces: Continuous lasers are better suited for cleaning extensive areas, such as ship hulls, pipelines, or large industrial equipment, due to their ability to deliver consistent power over longer periods.
Cost Considerations
Budget Constraints
- Pulse laser cleaning machines typically have a higher upfront cost due to their advanced technology and precision capabilities.
- Continuous laser cleaning machines generally offer a lower initial investment, making them attractive for businesses with budget limitations or those requiring less precision.
Operational Costs
- Energy Consumption: Continuous lasers often consume more energy because of their higher average power output, potentially leading to higher operational expenses.
- Maintenance Costs: Pulse lasers may incur higher maintenance costs due to their complex components and need for precise calibration.
- Longevity and Efficiency: While pulse lasers may have higher initial and maintenance costs, their precision can reduce the need for rework or additional processing, potentially offering long-term savings.
Operational Considerations
Ease of Use
- Operator Expertise: Pulse laser systems may require more specialized training to optimize laser parameters for different materials and contaminants.
- Continuous laser systems are generally simpler to operate, with fewer parameters to adjust, reducing the learning curve for operators.
Maintenance
- Maintenance Requirements: Pulse lasers may demand more frequent maintenance and calibration to maintain peak performance.
- Continuous lasers typically have a simpler design with fewer components, potentially resulting in lower maintenance needs and costs.