Introduction to Laser Cleaning Machines
Laser cleaning machines are advanced tools designed to efficiently remove contaminants such as rust, paint, and oxides from a wide range of surfaces. Using high-intensity laser beams, these machines offer a non-contact, environmentally friendly solution that is rapidly becoming the preferred method for industrial and commercial cleaning tasks. Unlike traditional cleaning methods that rely on abrasive materials or harsh chemicals, laser cleaning is precise and selective, targeting only the unwanted material while preserving the integrity of the underlying surface. This makes it an ideal choice for delicate tasks, such as cleaning historic artifacts, as well as more demanding industrial applications like preparing metal surfaces for welding or painting.
Laser cleaning is also highly versatile, capable of handling various materials including metals, ceramics, and composites. The process is simple yet effective: the laser beam is absorbed by the contaminant, which is then vaporized or ablated, leaving the surface clean and ready for further processing. Beyond its cleaning efficiency, laser cleaning is an eco-friendly option. It eliminates the need for chemicals and reduces waste, contributing to safer working environments and lower environmental impact. The technology is widely used in industries such as automotive, aerospace, electronics, and protection where precision and cleanliness are important. Laser cleaning machines provide a modern, effective, and sustainable solution for a variety of cleaning and surface preparation needs, making them an essential tool in both industrial and specialized settings.
Laser Cleaning Machines
There are many types of laser cleaning machines to meet different industrial needs. The continuous laser cleaning machine is designed for heavy-duty applications that require high efficiency and speed. It emits a constant laser beam and is ideal for removing thick rust, paint, or other contaminants from metal surfaces. The pulsed laser cleaning machine operates with short pulses of energy. This type is better suited for delicate cleaning tasks, such as removing oxides on complex components or cleaning surfaces without damaging the underlying material.
For increased mobility, handheld laser cleaning machines offer a portable solution that enables operators to clean hard-to-reach areas or move easily between job sites. Additionally, robotic laser cleaning machines offer automated solutions for large-scale or repetitive tasks, ensuring consistent results and reducing manual labor. The flexibility and precision of these types of laser cleaning machines make them versatile tools for a variety of industrial cleaning applications.
-
Standard Continuous Laser Cleaning Machine
Rated 4.75 out of 5$3,200 – $6,600 This product has multiple variants. The options may be chosen on the product page -
Portable Continuous Laser Cleaning Machine
Rated 4.50 out of 5$3,100 – $6,500 This product has multiple variants. The options may be chosen on the product page -
Double Wobble Continuous Laser Cleaning Machine
Rated 5.00 out of 5$3,700 – $7,100 This product has multiple variants. The options may be chosen on the product page
-
Double Wobble Pulse Laser Cleaning Machine
Rated 4.75 out of 5$4,300 – $16,000 This product has multiple variants. The options may be chosen on the product page -
Luggage Pulse Laser Cleaning Machine
Rated 5.00 out of 5$6,300 – $16,800 This product has multiple variants. The options may be chosen on the product page -
Backpack Pulse Laser Cleaning Machine
Rated 4.75 out of 5$6,600 – $8,900 This product has multiple variants. The options may be chosen on the product page -
High Power Pulse Laser Cleaning Machine
Rated 4.75 out of 5$9,300 – $64,300 This product has multiple variants. The options may be chosen on the product page
Comparison Between Continuous and Pulsed Laser Cleaning Machines
Feature | Continuous Laser Cleaning Machine | Pulsed Laser Cleaning Machine |
Laser Operation | Emits a constant, steady beam of laser energy | Emits laser energy in short, high-intensity pulses |
Power Range | Typically ranges from 1000W to 3000W | Typically ranges from 100W to 1000W |
Cleaning Speed | Faster cleaning speed, suitable for large-scale and high-volume tasks | Slower cleaning speed, more precise for delicate surfaces |
Surface Material Suitability | Ideal for cleaning robust materials like metals and thick coatings | Suitable for cleaning sensitive materials like plastics and composites |
Energy Efficiency | Higher energy consumption due to continuous operation | More energy-efficient due to short bursts of energy |
Heat Impact | Generates more heat, which may affect heat-sensitive materials | Lower heat impact, minimizing the risk of damage to sensitive surfaces |
Precision | Less precision compared to pulsed lasers; best for uniform surfaces | High precision, ideal for intricate and detailed cleaning tasks |
Applications | Suitable for heavy-duty cleaning tasks like rust removal, paint stripping | Ideal for applications requiring high precision, such as mold cleaning |
Operating Cost | Generally higher due to increased power consumption | Lower operating costs due to reduced power consumption |
Portability | Often larger and less portable | More compact and portable, easy to transport |
Maintenance Requires | Regular maintenance to manage continuous operation and heat | Lower maintenance requirements due to pulsed operation |
Applications of Laser Cleaning Machines
Laser cleaning machines are highly adaptable tools that can be used across industries to achieve efficient, precise, and environmentally friendly surface cleaning and treatment. They provide a non-abrasive solution that effectively cleans rust and oxides from metal surfaces without damaging the underlying material, making them used in areas such as automotive, shipbuilding, and heavy machinery maintenance. Laser cleaning machines can also remove paint and coatings. They can remove paint, varnish, and other coatings without the use of chemicals or abrasive methods, making them ideal for industries such as aerospace and electronics manufacturing where precision is critical.
In surface preparation for welding, bonding, or painting, laser cleaning ensures that surfaces are free of contaminants such as oil, grease, and dust, which can help achieve strong bonds and high-quality surface finishes in industries such as automotive and aerospace. Laser cleaning is increasingly used in cultural heritage restoration, where its precision can gently remove dirt and contaminants from delicate artifacts and monuments, preserving their integrity. Laser cleaning machines provide a versatile and effective solution for a wide range of industrial and conservation applications, with both efficiency and environmental benefits.
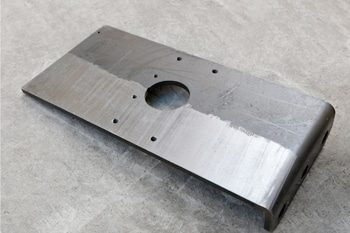

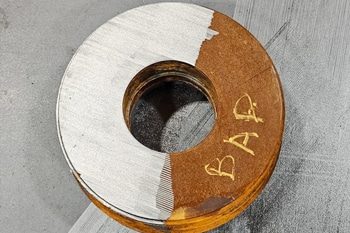
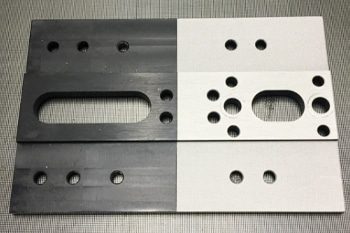
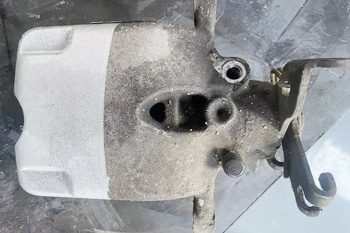
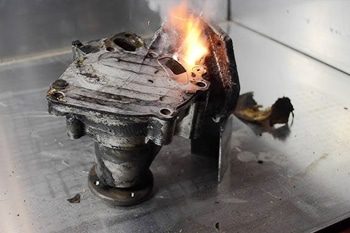
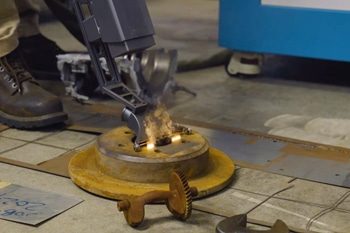
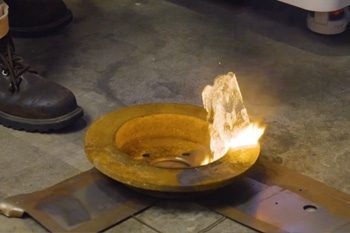
Customer Reviews
After switching to a laser cleaning machine for our aerospace components, the difference has been remarkable. The precision with which it removes contaminants without damaging the surface is unparalleled. It's also cut down our cleaning time significantly, which has been a huge boost for our production line. We’re extremely satisfied with the performance and would highly recommend it to others in the industry.
MarkAerospace Manufacturing
We’ve been using the laser cleaning machine for rust removal and surface prep on classic car restorations, and it’s been a game-changer. The results are clean and consistent, and the best part is that it doesn’t damage the original metal. It’s made our restoration process much more efficient and helped us achieve a higher level of detail. Couldn’t be happier with this investment!
SusanAutomotive Restoration
As a preservationist, maintaining the integrity of historical artifacts is paramount. The laser cleaning machine has been invaluable in our work. It allows us to clean delicate surfaces like stone and metal with incredible precision, without causing any harm to the original material. It’s an essential tool in our conservation efforts and has delivered outstanding results every time.
JamesHistorical Preservation
The laser cleaning machine has streamlined our production process by providing a reliable and efficient method for removing contaminants from electronic components. It’s much faster and cleaner than the methods we used previously, and the reduction in chemical usage is a significant bonus for both our workers and the environment. The machine has exceeded our expectations in every way.
KarenElectronics Manufacturing
Rust and corrosion are constant challenges in the shipbuilding industry, and the laser cleaning machine has made a tremendous impact. It’s incredibly effective at removing rust without damaging the metal underneath, and the speed at which it works has greatly improved our turnaround times. This machine has quickly become an indispensable part of our maintenance operations.
DavidShipbuilding Industry
Related Resources
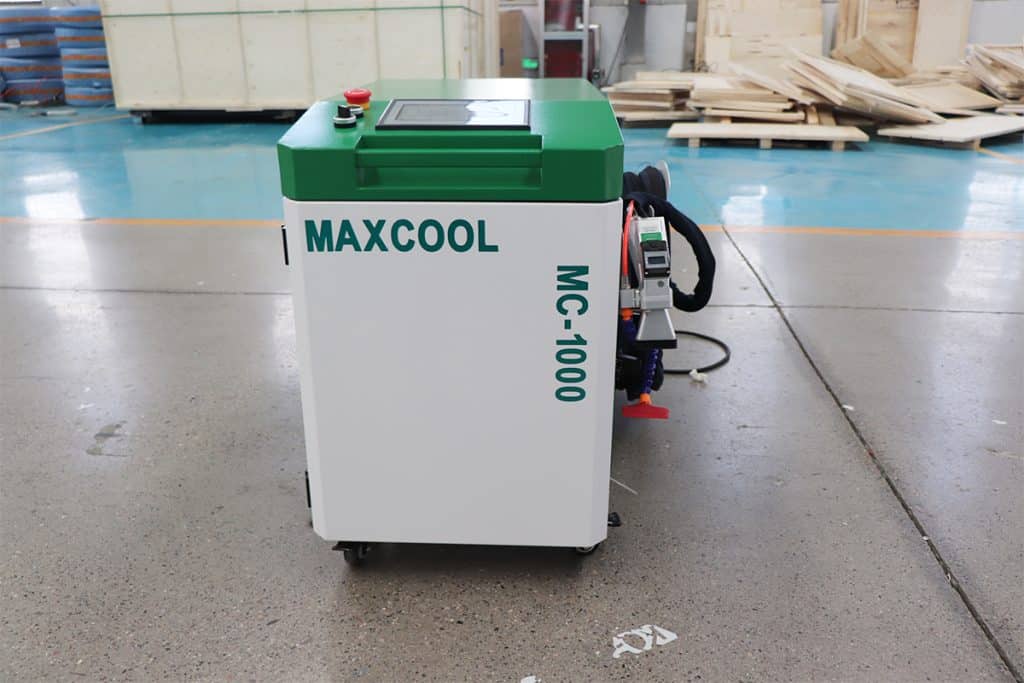
How Laser Parameters Affect the Cleaning Process?
This article explores how laser parameters like wavelength, pulse duration, energy, and scanning speed influence the efficiency and outcome of the laser cleaning process.
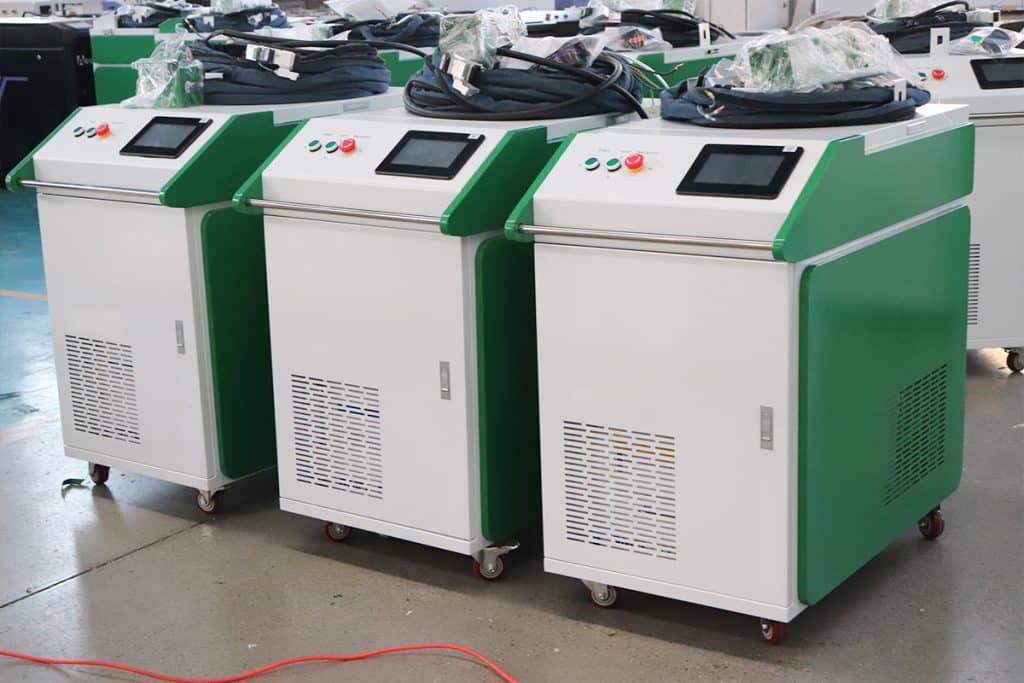
Laser Rust Removal VS Electrolytic Rust Removal
This article explores how laser and electrolytic methods can remove rust, detailing their principles, advantages, disadvantages, and typical applications for effective corrosion control.
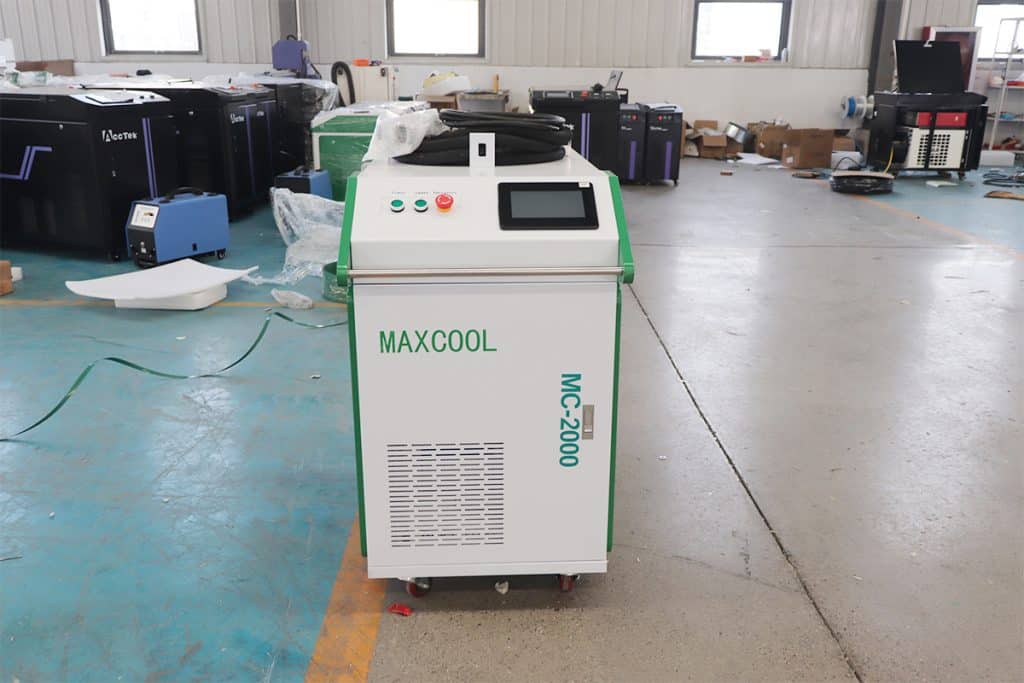
Is Laser Cleaning Eco-Friendly?
This article provides an in-depth analysis of the environmental friendliness of laser cleaning to help you understand the differences between laser cleaning and traditional methods in terms of waste reduction,
Frequently Asked Questions
What Are Laser Cleaning machines and How Does it Work?
Laser cleaning machines are device that uses a focused beam of laser light to remove contaminants from surfaces. The process works through the principle of laser ablation, where the laser energy is absorbed by the contaminants on the surface, causing them to vaporize, evaporate, or be blown away by a stream of compressed air. The underlying material is left intact because the laser parameters are finely tuned to target only the unwanted substances. The process is non-contact, meaning that the laser never physically touches the surface, reducing the risk of abrasion or damage. This method is not only precise but also environmentally friendly, as it eliminates the need for chemical solvents and reduces waste.
What Materials Can Be Cleaned with Laser Cleaning Machines?
Laser cleaning machines are highly adaptable and can be used on a wide variety of materials. They are particularly effective on metals such as steel, aluminum, brass, copper, and titanium, making them ideal for industries like automotive, aerospace, and shipbuilding where rust, paint, and oxidation are common issues. Beyond metals, laser cleaning can be applied to plastics, ceramics, composites, and even delicate surfaces like historical artifacts. The ability to adjust the laser’s power, frequency, and focus allows for precise control, ensuring that even sensitive materials can be cleaned without damage. For example, in the restoration of cultural heritage, laser cleaning is used to gently remove dirt, soot, and biological growth from stone, wood, and other ancient materials without harming their integrity.
Is Laser Cleaning Safe for All Surfaces?
Laser cleaning is generally safe for most surfaces, provided that the laser’s settings are appropriately adjusted. The technology allows for precise control over the laser’s intensity, making it possible to clean even delicate surfaces without causing harm. However, it is essential to understand the material properties of the surface being cleaned. For instance, while metals can withstand higher laser intensities, softer materials like plastics or painted surfaces may require lower power settings to prevent melting or discoloration. To ensure safety, it is often recommended to perform a test on a small, inconspicuous area before proceeding with full-scale cleaning. Additionally, operators must be trained to handle the equipment properly and understand how to adjust the parameters to suit different materials.
How Does Laser Cleaning Compare to Traditional Cleaning Methods?
Laser cleaning offers several distinct advantages over traditional methods such as sandblasting, chemical cleaning, and abrasive blasting. Unlike sandblasting, which uses a high-pressure stream of abrasive material to clean surfaces, laser cleaning is non-abrasive and does not wear down the material being cleaned. This means there is no risk of damaging the substrate, making laser cleaning ideal for precision tasks. Chemical cleaning, on the other hand, often involves hazardous substances that can be harmful to both the environment and the operator. Laser cleaning eliminates the need for these chemicals, reducing environmental impact and improving workplace safety. Additionally, laser cleaning is typically faster and more efficient, especially for tasks that require precision, such as the removal of thin layers of contaminants or detailed work on complex geometries. The precision and control offered by laser cleaning make it a more versatile and effective solution in many industrial and conservation applications.
Can Laser Cleaning Machines Be Used in Production Lines?
Yes, laser cleaning machines can be seamlessly integrated into automated production lines, enhancing efficiency and productivity. In a production environment, laser cleaning can be used for tasks such as surface preparation before welding, paint removal, and the cleaning of molds and tools. Automated laser systems can be programmed to target specific areas with high precision, ensuring consistent results across multiple parts or products. These systems can be equipped with robotic arms, conveyor belts, or other automation tools to facilitate continuous operation, reducing the need for manual intervention. By integrating a laser cleaning machine into a production line, manufacturers can achieve higher throughput, lower operational costs, and improved product quality. Additionally, automated laser cleaning systems can be easily adapted to different production tasks by adjusting the laser parameters or reprogramming the system, making them a flexible and long-term solution for industrial cleaning needs.
What Are the Maintenance Requirements for Laser Cleaning Machines?
Laser cleaning machines are known for their durability and relatively low maintenance requirements. Regular maintenance typically involves inspecting and cleaning the optical components, such as the laser lens, to ensure that they are free from dust, debris, or any other contaminants that could affect the laser’s performance. The cooling system, which prevents the laser from overheating during operation, should also be checked regularly to ensure it is functioning correctly. This includes inspecting coolant levels, checking for leaks, and ensuring that fans or other cooling mechanisms are working efficiently. Additionally, it’s important to keep the machine’s work area clean to prevent dust or particles from entering the system. While laser cleaning machines are robust, following a regular maintenance schedule will help prolong the machine’s lifespan and maintain optimal performance. Most manufacturers provide detailed maintenance guidelines, and following these can prevent unexpected downtime and costly repairs.
How Long Does it Take to Clean a Surface with Laser Cleaning Machines?
The time required to clean a surface with a laser cleaning machine depends on several factors, including the type of material, the thickness of the contaminants, and the laser’s power settings. For example, rust removal from a metal surface might take just a few minutes per square meter, while tasks involving more delicate or intricate surfaces could take longer. High-power continuous laser systems are capable of cleaning larger areas quickly, making them suitable for industrial applications where speed is essential. In contrast, pulsed laser systems, which are typically used for more precise tasks, may operate more slowly but provide a higher level of detail and control. Regardless of the specific application, laser cleaning is generally faster and more efficient than traditional methods, particularly when dealing with complex geometries or sensitive materials. The process is also highly repeatable, ensuring consistent results with each use.
Are Laser Cleaning Machines Environmentally Friendly?
Yes, laser cleaning machines are considered an environmentally friendly alternative to traditional cleaning methods. Unlike chemical cleaning processes, which often require the use of toxic solvents and generate hazardous waste, laser cleaning is a dry, non-contact process that produces minimal waste. The only byproducts are typically small particles of the material being removed, which can be easily collected and disposed of without special handling requirements. Moreover, laser cleaning does not rely on water, chemicals, or abrasive materials, reducing the environmental impact associated with waste disposal and resource consumption. The energy efficiency of laser systems also contributes to their environmental benefits, as they consume less power compared to other industrial cleaning processes. By choosing laser cleaning, companies can reduce their ecological footprint while improving workplace safety and cleaning efficiency.
Get Laser Cleaning Solutions
At Maxcool CNC, we provide innovative laser cleaning solutions tailored to your specific needs. Our advanced laser cleaning machines offer precise, non-abrasive cleaning for a variety of materials and industries. Whether you’re looking to remove rust, paint, or contaminants, our systems ensure efficient and eco-friendly results. Our team of experts is ready to help you select the right equipment for your application, offering full consultation and support throughout the process. Contact us today to discuss how our laser cleaning solutions can optimize your operations.
By submitting your information, you’re taking the first step towards a partnership that redefines what’s possible in laser cleaning. Our team will promptly reach out to discuss your unique requirements and guide you through the journey of enhancing your manufacturing capabilities with Maxcool CNC’s laser cleaning solutions.