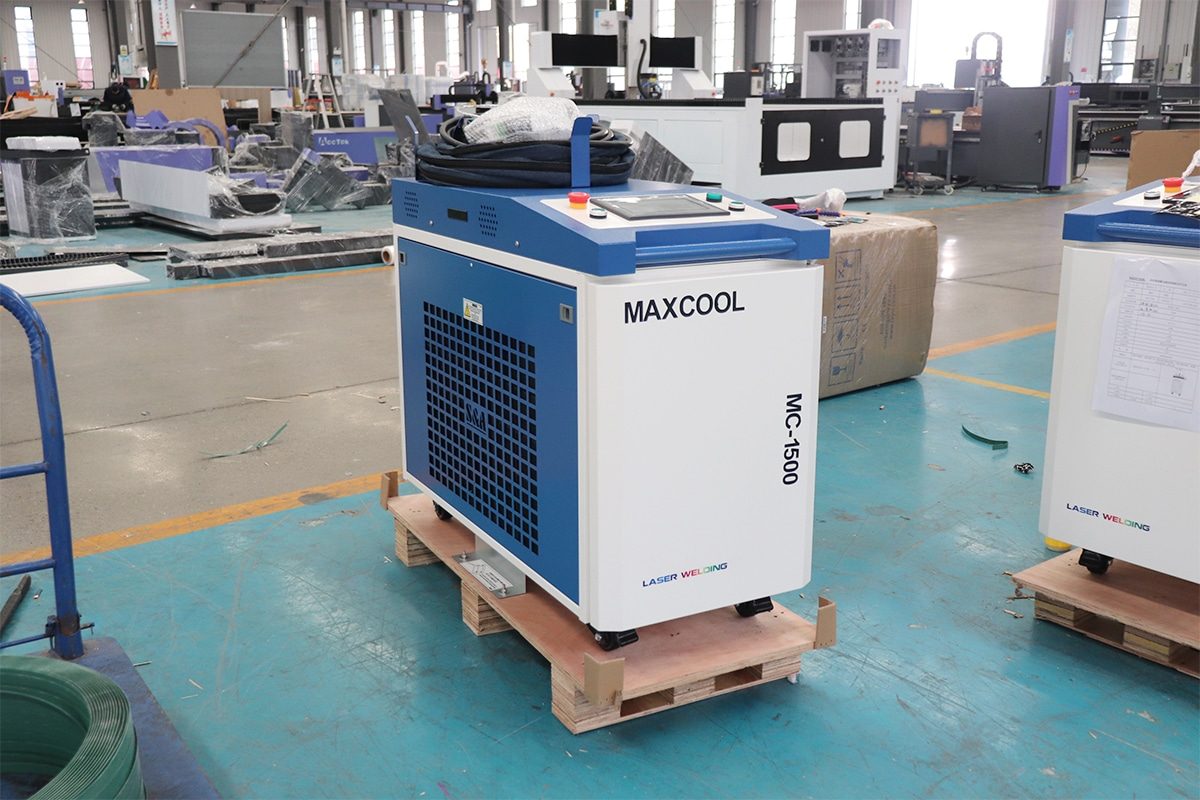
Operating Environment of Laser Cleaning Machines
Laser cleaning technology is a rapidly growing field in industrial applications, offering a cleaner, more efficient alternative to traditional methods of surface cleaning. Laser cleaning machines use high-intensity laser beams to remove contaminants like rust, paint, oil, and other unwanted materials from a variety of surfaces. This process is particularly advantageous because it is non-abrasive, does not involve chemicals, and minimizes waste. As industries increasingly adopt laser cleaning machines for applications in manufacturing, automotive, aerospace, and more, understanding the operating environment for these machines becomes essential.
While laser cleaning technology offers significant advantages in terms of precision, efficiency, and environmental friendliness, its performance heavily depends on the conditions in which the machine operates. Factors like temperature, humidity, air quality, and power supply all play a crucial role in determining the efficiency, safety, and longevity of the equipment. Poor environmental conditions can lead to machine malfunction, reduced output, safety hazards, and even premature equipment failure.
This article explores the key environmental considerations for operating laser cleaning machines, from temperature and humidity control to electrical power stability, air quality management, and safety protocols. By understanding these factors, businesses and technicians can optimize the performance of their machines, minimize downtime, and ensure the safety of operators.
Table of Contents
The Importance of the Operating Environment
The operating environment of a laser cleaning machine is a critical factor that directly impacts its performance, longevity, and safety. While laser cleaning technology is advanced and highly efficient, it requires precise conditions to function at its best. The quality of the environment surrounding the machine can affect everything from the laser’s output to its mechanical components and even operator safety.
Understanding the relationship between the operating environment and the laser machine’s performance is essential for technicians, engineers, and business owners who rely on these systems. Inadequate environmental conditions can lead to issues like inconsistent cleaning results, higher maintenance costs, system downtime, and even permanent damage to the machine. Conversely, maintaining an optimal environment ensures smooth operation, increased efficiency, and prolonged equipment lifespan.
Several key factors influence the environment in which laser cleaning machines should operate. These include temperature and humidity control, air quality management, electrical power stability, and safety considerations. Addressing each of these factors contributes to the overall effectiveness of the laser cleaning process. Failure to properly manage the operating environment could lead to subpar cleaning results, inefficient use of energy, and safety risks for both operators and nearby equipment.
By understanding the importance of these considerations and implementing effective control measures, operators can ensure that their machines perform at optimal levels, reduce maintenance costs, and maintain a safe working environment.
Temperature and Humidity Control
Temperature and humidity are two of the most critical factors that influence the performance of laser cleaning machines. Both of these elements affect the machine’s efficiency, the precision of the laser, and even the longevity of the system. Proper control of temperature and humidity is essential for ensuring consistent cleaning results, minimizing downtime, and maintaining safety standards.
Ideal Temperature Range
Laser cleaning machines are designed to operate within a specific temperature range. Typically, this range is between 18℃ to 25℃ (64℉ to 77℉), though manufacturers may recommend slightly different ranges depending on the model and the components used. Within this temperature range, the machine’s cooling systems, laser output, and electronics function optimally. Operating outside this range can cause several issues.
Too high a temperature can lead to overheating of sensitive components, such as the laser source or optics. Overheating may result in reduced laser power, inconsistent cleaning performance, and potential damage to the machine. Additionally, higher temperatures can accelerate the degradation of the machine’s internal parts, requiring more frequent maintenance and reducing the overall lifespan of the equipment.
Too low a temperature can also have detrimental effects. Cold temperatures can cause the laser’s cooling system to work inefficiently, leading to possible condensation and moisture buildup within the machine. This can create a risk of short-circuiting or electrical malfunction. Furthermore, laser efficiency may decrease in colder environments, leading to diminished cleaning results.
For businesses relying on laser cleaning systems, maintaining the machine within the recommended temperature range is crucial for optimal performance. Environmental monitoring systems or thermostats can be used to ensure the machine operates within the right conditions.
Temperature Fluctuations and Their Impact
While maintaining an ideal temperature range is important, temperature fluctuations can be even more damaging to the performance of laser cleaning systems. Rapid changes in temperature, such as those that may occur when the machine is moved between different locations or during significant weather shifts, can cause several problems.
Laser cleaning machines are highly sensitive to temperature changes, particularly when it comes to the optical components and the alignment of the laser. Sudden shifts in temperature can cause thermal expansion and contraction, which may affect the precision of the laser beam, leading to inaccurate cleaning results. For example, a machine that is operated in a cold environment and then moved to a warmer area could experience misalignment, resulting in an uneven cleaning pattern or inefficiencies.
Gradual temperature fluctuations, such as those caused by day-night cycles or seasonal changes, can also cause the machine’s internal components to wear out faster due to constant expansion and contraction. To mitigate these effects, it is advisable to install environmental control systems, such as HVAC units, to maintain a stable temperature throughout the operation period.
Humidity Considerations
In addition to temperature, humidity control plays a significant role in maintaining the optimal operating environment for laser cleaning machines. Humidity levels that are too high or too low can create a range of issues.
High humidity can cause condensation within the laser cleaning machine, especially in sensitive areas like the laser head, electronics, and optics. Excess moisture can damage these components, leading to electrical failures, rusting, and degradation of materials. In some cases, the presence of moisture may also interfere with the laser’s precision, as the laser beam can scatter when passing through water droplets in the air.
Low humidity, on the other hand, can lead to static buildup, which can damage sensitive electronic components within the machine. Static discharge can affect the functionality of control systems, sensors, and other electrical components, potentially leading to costly repairs or system shutdowns.
To prevent these issues, it’s recommended that laser cleaning machines operate in environments where relative humidity is maintained between 30% and 60%. This range is optimal for preventing both excessive moisture and static buildup. In particularly humid environments, dehumidifiers can help reduce moisture levels, while in dry conditions, humidifiers or air ionizers can be used to maintain the proper balance.
Maintaining the right balance of temperature and humidity is not only crucial for the machine’s performance but also for the safety of operators and the quality of the work. Fluctuations in either of these factors can lead to inconsistent results, higher maintenance costs, and an increased risk of equipment failure.
Air Quality and Dust Control
The air quality within the operating environment of a laser cleaning machine is another important factor that significantly affects its performance and safety. Laser cleaning works by focusing a high-intensity laser beam on a surface to remove contaminants like rust, paint, oil, and dirt. This process generates not only the visible debris that is removed from the surface but also airborne particles, smoke, and fumes. Managing air quality, particularly dust, and fumes, is crucial to ensure the machine operates efficiently, maintains safety standards, and preserves the longevity of the equipment.
The Role of Dust
Dust is one of the most significant environmental concerns in laser cleaning operations. Airborne dust particles can cause various issues, both for the laser machine itself and the quality of the cleaning results. Dust can originate from various sources, including the surface being cleaned (for example, rust or paint particles), nearby machinery, or even from the ambient environment.
In laser cleaning, dust particles may interfere with the laser beam’s focus, leading to inconsistent or incomplete cleaning results. If dust accumulates on the optical components of the laser, such as mirrors or lenses, it can block or scatter the light, reducing the efficiency of the laser and causing the cleaning process to be less effective. Over time, dust buildup on internal components can also lead to mechanical problems, overheating, and eventually equipment failure.
Additionally, dust particles can accumulate in sensitive areas of the machine, such as the cooling system, filters, and ventilation openings, obstructing airflow and decreasing the machine’s ability to cool down properly. This can lead to overheating and other related issues, potentially resulting in system downtime.
Dust-Free Environment
Creating a dust-free environment is crucial to ensuring the laser cleaning machine operates at its best. Several strategies can help reduce dust levels in the workplace:
- Air filtration systems: Installing high-efficiency particulate air (HEPA) filters or other industrial air filtration systems can capture fine dust particles before they reach the machine. These systems help prevent the accumulation of dust on the laser’s optics and mechanical components, ensuring the machine operates efficiently.
- Regular cleaning and housekeeping: Keeping the surrounding area clean and free of debris helps reduce the amount of dust in the air. Using industrial vacuums or air purifiers can help maintain a dust-free environment in the cleaning area.
- Controlling airflow: The placement of the machine in areas with controlled airflow can also help reduce the amount of dust. For example, ensuring that the cleaning area is kept away from high-traffic zones or open windows will minimize the introduction of airborne dust from external sources.
Maintaining a clean, dust-free environment not only ensures the efficiency of the laser cleaning process but also reduces the frequency of machine maintenance and the risk of performance issues over time.
Fume Extraction
During the laser cleaning process, various fumes are generated as the laser interacts with the contaminants being removed. These fumes may contain hazardous gases and particulates that can pose health risks to operators and damage the machine if not properly managed. Therefore, fume extraction is an essential part of maintaining a safe and efficient working environment.
Fume extraction systems are designed to capture and remove the harmful fumes produced during the laser cleaning process before they can spread into the air. These systems work by drawing the fumes through a filtration system that captures particles, gases, and other pollutants. The extracted air is either filtered and returned to the room or safely vented outside, depending on the setup and local regulations.
The importance of fume extraction cannot be overstated. Without a proper fume extraction system in place, operators may be exposed to harmful gases such as carbon monoxide, ozone, or volatile organic compounds (VOCs), which can have serious long-term health effects. Fumes can also damage the equipment, leading to premature wear on filters, clogged ventilation systems, or contamination of internal components.
For optimal fume extraction, laser cleaning machines should be equipped with high-quality extraction units that provide adequate airflow and filtration capacity. The system should be designed to handle the specific types of fumes generated during the cleaning process, whether that involves volatile compounds, metals, or other byproducts. Regular maintenance of these systems is essential to ensure their continued effectiveness in keeping the work environment safe and clean.
Maintaining Air Quality for Laser Cleaning Systems
In addition to dust and fume control, ensuring good general air quality is essential for the overall operation of laser cleaning machines. Airborne contaminants such as moisture, oils, and gases can interfere with the laser beam’s focus or the performance of the machine’s optical components.
Installing air purifiers and dehumidifiers, along with proper ventilation, can help maintain a stable, clean, and dry environment that is conducive to the optimal functioning of the laser cleaning system. Furthermore, regular monitoring of air quality using sensors that detect particle levels, temperature, and humidity can help detect and prevent issues before they affect the machine’s performance.
By maintaining an air quality system that addresses both dust and fumes, businesses can prolong the life of their laser cleaning machines, improve cleaning efficiency, and create a safer working environment for operators.
Electrical Power Supply
The electrical power supply is a crucial factor in ensuring the smooth and reliable operation of laser cleaning machines. Since these machines rely on highly sensitive electronics and precise control systems, maintaining a stable and clean power supply is essential for optimal performance. Fluctuations in voltage, power surges, or electrical interference can cause a range of issues, from operational malfunctions to permanent damage to the machine.
Proper management of the power supply can help prevent downtime, extend the lifespan of the equipment, and maintain high-quality cleaning results.
Power Stability
One of the most important factors in maintaining the efficient operation of a laser cleaning machine is ensuring a stable power supply. Laser systems require constant, reliable power to function at peak efficiency. Power instability, such as frequent voltage fluctuations or power interruptions, can significantly impact the machine’s performance.
Voltage sags, spikes, or surges can interfere with the sensitive electronics and laser control systems. For instance, voltage fluctuations can cause the laser’s power output to become unstable, leading to inconsistent cleaning results or inefficient operation. If the power supply is unstable, it can also cause components like the cooling system, motors, or sensors to behave erratically, which may lead to overheating, failure to start, or system shutdowns.
To mitigate the effects of power instability, businesses should invest in uninterruptible power supplies (UPS) or power conditioning systems. These devices help maintain consistent power levels by providing backup power during interruptions or filtering out harmful surges and spikes in the electrical supply. A well-maintained UPS ensures that the laser cleaning machine can continue to operate seamlessly without sudden power losses that could affect its performance or damage its components.
Voltage and Frequency Considerations
Laser cleaning machines are designed to operate within specific voltage and frequency ranges. Ensuring that the electrical supply adheres to the correct voltage and frequency requirements is vital for the smooth operation of the system. Deviations from these specifications can cause performance issues and, in some cases, damage to the machine.
Most industrial laser cleaning machines are designed to operate at standard voltages, such as 110V or 220V, depending on the region and the equipment. The frequency of the power supply is also an important consideration—typically, laser cleaning machines are built to work at 50 Hz or 60 Hz, which are standard frequencies in different parts of the world.
Operating the machine at an incorrect voltage can lead to several issues. For example:
- Low voltage can result in insufficient power for the laser, causing the machine to underperform or operate inefficiently. In this case, the laser may not generate the necessary intensity to clean surfaces properly, leading to reduced cleaning quality.
- High voltage can cause overheating, excessive wear on internal components, or permanent damage to sensitive parts of the machine, such as the laser source or control electronics.
Similarly, if the frequency of the electrical supply does not match the required standard for the laser cleaning machine, it can cause synchronization issues in the machine’s electronics, resulting in reduced performance, erratic behavior, or even damage to the system over time.
To avoid these issues, it is essential to ensure that the power supply conforms to the machine’s specifications. Businesses may need to work with local electrical providers or invest in transformers, frequency converters, or voltage stabilizers to ensure the machine operates at its optimal voltage and frequency.
Electrical Grounding
Proper electrical grounding is another important safety consideration when operating laser cleaning machines. Grounding ensures that electrical currents are safely directed away from the machine’s sensitive components and that any stray currents are safely dissipated. This is especially important in industrial environments, where the risk of electrical surges and static discharge is higher.
Electrical surges, often caused by lightning strikes or other high-power electrical events, can cause severe damage to electronic components, including the laser’s control systems. Static electricity buildup, which can occur in dry environments or when equipment is not properly grounded, can also lead to equipment malfunctions or permanent damage.
To protect against these risks, laser cleaning machines should be grounded according to the manufacturer’s guidelines and local electrical codes. Proper grounding will help to prevent electrical shocks, reduce the risk of equipment damage, and ensure the safety of operators working around the machine.
In addition to ensuring proper grounding, regular inspections should be conducted to check for any grounding issues, such as faulty connections or degraded cables. This will help maintain electrical safety and the proper functioning of the system.
Electrical Safety and Redundancy
Maintaining a stable and secure electrical power supply is not only crucial for the performance of laser cleaning machines but also for the safety of operators. Electrical malfunctions, especially those related to power instability, grounding, or faulty wiring, can pose serious risks, including electric shock, fire hazards, or explosions (especially in environments with flammable materials or gases).
To ensure electrical safety, it is essential to install appropriate circuit breakers, fuses, and surge protectors. These protective devices can help prevent damage to the machine and minimize the risk of electrical fires or accidents. In high-risk environments, additional safety features, such as explosion-proof electrical enclosures, may also be necessary.
Furthermore, redundancy systems such as dual power supplies or backup generators can be used to ensure that the laser cleaning machine remains operational even in the event of a power failure. By investing in these systems, businesses can reduce the risk of downtime and maintain continuous cleaning operations, which is especially important for high-volume industries that rely on constant production.
Safety Considerations
When operating laser cleaning machines, safety is of paramount importance. Due to the powerful nature of the laser, as well as the risks associated with fumes, electrical components, and the environment itself, it is critical to take the necessary precautions to ensure that both operators and the surrounding environment remain safe. Proper safety protocols are essential to mitigate potential hazards, prevent accidents, and comply with relevant safety regulations.
Laser Safety
Laser cleaning machines utilize high-intensity lasers, which can be hazardous if not used properly. Lasers emit concentrated light energy that can cause severe eye damage, skin burns, and even permanent injury if the laser is mishandled or if proper protective measures are not in place.
To ensure laser safety, operators should follow strict safety guidelines and wear appropriate protective gear. Laser safety goggles that are specifically designed to block the wavelength of the laser being used should always be worn by those in the vicinity of the machine. These goggles are essential for protecting the eyes from potential exposure to the laser beam, which can cause retinal damage or even blindness.
Additionally, it is crucial to establish laser safety zones around the machine. The laser should only be operated in designated areas that are marked with safety signs to warn anyone nearby of the potential hazards. The machine itself should be equipped with safety interlocks or covers that automatically shut off the laser when the protective barriers are breached or when the machine door is opened.
When working with lasers, training is a critical aspect of maintaining safety. Operators should be thoroughly trained in laser safety protocols, including how to use the equipment correctly, how to identify potential hazards, and how to respond in case of an emergency.
Fire and Explosion Risk
Laser cleaning machines, while generally safe, can present a fire and explosion risk, especially in certain environments. The cleaning process itself can generate heat, particularly if the material being cleaned is highly flammable or if the machine overheats. Furthermore, some cleaning applications may involve the removal of contaminants that are volatile or hazardous, such as coatings or oils that can emit flammable fumes.
To mitigate fire and explosion risks, several precautions should be taken:
- Proper ventilation and exhaust systems: As the laser heats the surface being cleaned, it can cause materials to burn or emit potentially hazardous gases. This makes it essential to have an effective ventilation system that helps remove hot air, smoke, and fumes from the workspace. In high-risk environments, additional explosion-proof ventilation or explosion suppression systems should be installed.
- Fire-resistant materials: The machine should be housed in a location with fire-resistant walls and floors, particularly in settings where flammable materials are present. Moreover, fire extinguishers, fire blankets, and automatic sprinkler systems should be readily available and regularly maintained.
- Routine inspection of equipment: Regular maintenance checks should include inspection of the cooling system, ventilation fans, and any other components that could potentially overheat. If overheating is detected, it could be a sign of a malfunction or an impending fire hazard.
- Safe cleaning materials: When selecting materials for laser cleaning, businesses should ensure that the surfaces being cleaned do not present an undue fire risk. Avoiding highly volatile materials or substances that can combust at high temperatures will reduce the chances of a fire or explosion during cleaning operations.
By taking the necessary precautions and following fire safety guidelines, the risk of a fire or explosion during laser cleaning operations can be minimized.
Ventilation and Air Quality for Safety
Proper ventilation is a key element in ensuring both the safety and the performance of laser cleaning machines. As the laser cleaning process generates fumes, gases, and particulate matter, it is critical to remove these contaminants from the air to protect both the operators and the equipment.
Fume extraction systems are essential for capturing harmful gases and particulate matter before they can pose a health hazard. Gases such as ozone, carbon monoxide, or volatile organic compounds (VOCs) can be released during the cleaning process, especially when dealing with certain materials like metals, coatings, or oils. These gases can be toxic if inhaled over time, so an effective fume extraction system is necessary to remove them from the air and maintain a safe working environment.
Additionally, general ventilation should be sufficient to maintain fresh air circulation and avoid the buildup of fumes in the room. This is particularly important if the laser cleaning machine is being used in a confined or poorly ventilated space. Local exhaust systems or air purifiers can help to improve air quality by removing particulate matter from the air and preventing the accumulation of hazardous fumes.
It is also important to monitor the air exchange rate in the workspace. According to Occupational Safety and Health Administration (OSHA) standards, air changes per hour (ACH) should be adequate to maintain safe air quality. In some cases, local codes or regulations may specify the minimum ACH required based on the materials being cleaned or the size of the workspace.
General Workplace Safety Protocols
Beyond laser and fire safety, several other workplace safety considerations must be observed when operating laser cleaning machines:
- Operator training: All personnel working with or near the laser cleaning machine should undergo comprehensive training that includes both the operation of the equipment and safety protocols. The training should cover laser hazards, emergency procedures, fire safety, and the proper handling of materials.
- Personal protective equipment (PPE): In addition to laser safety goggles, operators may also need to wear additional PPE such as gloves, aprons, or face shields to protect themselves from flying debris, heat, or fumes during the cleaning process.
- Machine maintenance: Regular maintenance checks should be conducted to ensure that the laser cleaning machine is functioning correctly and safely. This includes checking the alignment of the laser, ensuring that safety interlocks and emergency shutoff switches are operational, and verifying that all ventilation and exhaust systems are working as intended.
- Emergency preparedness: The work area should be equipped with emergency supplies, such as first aid kits, eyewash stations, and fire extinguishers. In case of an emergency, a clearly defined evacuation plan should be in place, and all personnel should be familiar with the procedures for shutting down the equipment safely.
By adhering to these safety measures and maintaining a vigilant approach to workplace safety, operators can reduce the risk of accidents, injuries, and equipment damage when using laser cleaning machines.
Maintenance and Calibration
Maintaining and regularly calibrating a laser cleaning machine is essential for ensuring optimal performance, longevity, and precision. Routine maintenance helps prevent unexpected breakdowns, reduces downtime, and ensures that the machine continues to deliver high-quality cleaning results. Calibration, on the other hand, ensures that the laser cleaning machine is operating within the manufacturer’s specified parameters, providing the best cleaning performance while minimizing the risk of damage to the equipment.
Routine Maintenance
Like any high-tech industrial equipment, laser cleaning machines require ongoing maintenance to ensure they operate smoothly and efficiently. Routine maintenance includes regular checks, inspections, cleaning, and minor repairs to avoid larger, costlier issues in the future. The frequency and scope of maintenance depend on the specific machine model, its usage, and the working environment. However, general guidelines can help maintain optimal operation.
Key components to include in routine maintenance:
- Laser Source and Optics: The laser source (typically a fiber or diode laser) is the heart of the machine and should be carefully inspected for signs of wear or degradation. Over time, the laser’s intensity can decrease if the system is not maintained properly. In addition, the optical components—such as lenses, mirrors, and beam delivery optics—should be checked for dust, dirt, or scratches. Cleaning the optical components is essential, as dust or contaminants can interfere with the laser’s performance, reducing the effectiveness of the cleaning process.
- Cooling System: The cooling system prevents the laser from overheating during operation. Laser cleaning machines generate a significant amount of heat, and if the cooling system fails, the machine could overheat, causing permanent damage to the laser source or other components. Therefore, the coolant levels and the cooling system’s integrity should be checked regularly. Make sure there are no leaks, and the coolant fluid is fresh and free from contaminants.
- Air Filtration and Fume Extraction Systems: The air filtration system, including HEPA filters and fume extraction units, should be cleaned or replaced as needed. These components can accumulate dust, debris, and other contaminants, which can reduce their efficiency over time. Regular inspections ensure that the system remains effective at removing airborne particulates and fumes, which helps maintain air quality and prevents damage to sensitive internal parts of the laser cleaning machine.
- Electrical Components and Wiring: Regular checks of the electrical connections, wiring, and control systems are necessary to ensure there are no loose connections, exposed wires, or signs of electrical wear. Faulty wiring can cause short circuits, erratic machine behavior, or electrical failure. Also, ensure that the control panels and user interfaces are functioning properly, with no glitches or errors in communication between the operator and the machine.
- Mechanical Components: Over time, moving parts such as motors, gears, and other mechanical components can wear down. These parts should be inspected regularly for any signs of friction, wear, or failure. Keeping these components lubricated (as per the manufacturer’s guidelines) will prevent mechanical failure and ensure smooth operation.
- Safety Features: The safety interlocks, emergency stop buttons, and safety covers should all be tested periodically. These components are critical to protecting operators and preventing accidents during operation. They should be checked for proper functionality and replaced immediately if found to be defective.
Calibration
While routine maintenance is focused on keeping the laser cleaning machine in good condition, calibration ensures that the machine’s components are aligned and functioning according to the manufacturer’s specifications. Calibration is especially important for systems that rely on precise measurements and adjustments, such as the laser’s intensity, beam focus, and cleaning parameters.
Key calibration tasks include:
- Laser Power Calibration: The laser power output must be consistent to ensure effective cleaning. Over time, the power output of the laser may drift due to factors such as wear and tear on the laser source, environmental conditions, or fluctuations in the power supply. Calibration ensures that the laser is operating within the correct power range and that the cleaning process is as efficient as possible.
- Beam Alignment: The beam delivery system should be properly aligned to ensure the laser beam remains focused and delivers energy exactly where it is needed. Misalignment can result in uneven cleaning, inefficiency, or even damage to the material being cleaned. Regular alignment checks ensure that the beam is focused on the right spot and that there are no issues with the beam path, mirrors, or lenses.
- Optical System Calibration: The optical system, including the lenses and mirrors, should be calibrated to ensure the laser’s energy is directed accurately and evenly across the surface being cleaned. Over time, dust and debris can cause misalignment or blockages, so recalibrating the optical system ensures that the laser cleaning machine delivers a consistent cleaning effect across all areas of the work surface.
- Distance and Focus Calibration: The distance between the laser head and the surface being cleaned must be accurately controlled to ensure optimal cleaning results. The focus point of the laser also plays a crucial role in achieving the best cleaning performance. Misalignment in the distance or focus could lead to inefficient cleaning or excessive damage to the substrate. Calibration ensures that these parameters are within the correct range for the materials being cleaned.
- Software Calibration: Many modern laser cleaning machines are controlled by sophisticated software systems that regulate the laser’s performance. These systems must be regularly calibrated to ensure that the settings for power, pulse rate, beam focus, and cleaning speed are all adjusted correctly. Software calibration helps ensure that the laser cleaning machine operates at its peak efficiency and delivers the desired results.
By prioritizing both routine maintenance and calibration, businesses can ensure that their laser cleaning machines continue to deliver high-performance results, operate safely, and avoid costly downtime. A well-maintained and properly calibrated system will not only extend the lifespan of the equipment but will also enhance the overall efficiency of the cleaning process.
Summary
Laser cleaning machines are powerful tools that offer many advantages, from their precision and efficiency to their ability to clean without damaging the underlying material. However, achieving these benefits requires careful attention to the operating environment in which the machines are used. By understanding the importance of environmental control and maintaining the equipment through regular maintenance and calibration, operators can maximize the effectiveness and safety of their laser cleaning systems.
For businesses and technicians in industries such as manufacturing, automotive, aerospace, and restoration, investing in the proper operating environment and maintaining strict adherence to safety and operational standards is critical to ensuring high-quality and cost-effective laser cleaning results. By proactively managing these factors, businesses can optimize their laser cleaning operations, improve productivity, and extend the lifespan of their equipment, ultimately leading to better outcomes and greater profitability.
Get Laser Cleaning Solutions
Maxcool CNC offers state-of-the-art laser cleaning solutions designed to meet the demanding needs of industries such as manufacturing, automotive, aerospace, and metalworking. Our laser cleaning machines utilize advanced technology to deliver efficient, eco-friendly, and precise cleaning without the use of harsh chemicals or abrasive materials. Whether you are looking to remove rust, paint, coatings, or contaminants from various surfaces, our laser cleaning systems provide a non-contact, low-maintenance solution that is both cost-effective and environmentally safe.
We understand that each application requires unique considerations, from surface type to cleaning requirements. That’s why our team of experts works closely with clients to assess their needs and provide customized laser cleaning solutions tailored to their specific requirements. With Maxcool CNC, you can be assured of high-performance, reliable machines that are easy to operate and maintain, while ensuring safety and environmental standards are met.