Laser Welding Stainless Steel
Stainless Steel Laser Welding Machine
-
Handheld Standard Laser Welding Machine
Rated 4.75 out of 5$3,200 – $6,600 This product has multiple variants. The options may be chosen on the product page -
Handheld Portable Laser Welding Machine
Rated 4.75 out of 5$3,100 – $6,500 This product has multiple variants. The options may be chosen on the product page -
Handheld 3 in 1 Laser Welding Cleaning Machine
Rated 5.00 out of 5$3,200 – $6,600 This product has multiple variants. The options may be chosen on the product page -
Handheld Air-Cooled Reci Laser Welding Machine
Rated 4.75 out of 5$4,300 – $5,700 This product has multiple variants. The options may be chosen on the product page -
Handheld Double Wobble Laser Welding Machine
Rated 4.75 out of 5$3,700 – $7,100 This product has multiple variants. The options may be chosen on the product page -
Handheld Double Wire Feed Laser Welding Machine
Rated 4.75 out of 5$6,200 – $6,900 This product has multiple variants. The options may be chosen on the product page -
Portable Air-Cooled Laser Welding Machine
Rated 4.50 out of 5$4,500 – $6,400 This product has multiple variants. The options may be chosen on the product page -
Handheld Air-Cooled 3 in 1 Laser Welding Machine
Rated 5.00 out of 5$4,500 – $6,400 This product has multiple variants. The options may be chosen on the product page -
CNC Platform Automatic Fiber Laser Welding Machine
Rated 4.50 out of 5$8,500 – $12,200 This product has multiple variants. The options may be chosen on the product page -
6-Axis Robotic Automatic Laser Welding Machine
Rated 5.00 out of 5$12,200 – $15,600 This product has multiple variants. The options may be chosen on the product page
Benefits of Laser Welding Stainless Steel
High Precision and Quality
Laser welding offers unparalleled precision, resulting in high-quality welds with minimal thermal distortion and a narrow heat-affected zone, preserving material integrity.
Reduced Heat Input
The focused laser beam delivers concentrated heat, reducing the overall heat input to the stainless steel and minimizing warping or thermal damage.
Faster Welding Speed
Laser welding operates at high speeds, significantly reducing weld times and enhancing productivity in high-volume manufacturing applications.
Minimal Material Distortion
The precision of laser welding limits the heat-affected zone, reducing the risk of material distortion and ensuring tight tolerances in complex assemblies.
Versatility in Application
Laser welding can handle various stainless steel grades and thicknesses, offering flexibility for diverse applications from thin sheets to thick plates.
Reduced Post-Weld Cleanup
The clean and precise nature of laser welding reduces the need for extensive post-weld cleaning or finishing, lowering overall production costs and improving efficiency.
Factors to Consider Before Buying Stainless Steel Laser Welding Machines
Laser Power and Type
Choose a machine with suitable laser power for your specific application. Higher power ensures effective welding of various stainless steel thicknesses.
Welding Speed and Efficiency
Evaluate the welding speed and efficiency of the machine. Faster welding speeds improve productivity and reduce operational costs, which is crucial for high-volume manufacturing.
Precision and Control
Look for machines with advanced control systems for precise adjustments to welding parameters. High precision ensures consistent, high-quality welds and optimal results for complex projects.
Material Compatibility
Ensure the machine can handle various grades and thicknesses of stainless steel. Versatility in material compatibility allows for flexibility in different welding applications and requirements.
Build Quality and Durability
Assess the machine's build quality and durability. The robust construction with high-quality components ensures long-term reliability and performance, even in demanding industrial environments.
Ease of Use and Automation
Consider user-friendly interfaces and automation features. Machines that are easy to operate and automate can enhance efficiency, reduce the learning curve, and streamline production processes.
Maintenance and Support
Verify that the manufacturer offers comprehensive maintenance and support services. Reliable technical support and access to spare parts are essential for minimizing downtime and maintaining operational efficiency.
Safety Features
Check for essential safety features such as protective enclosures, safety interlocks, and emergency stop functions. These features ensure a safe working environment and protect operators from potential hazards.
Comparison with Other Stainless Steel Welding Methods
Feature | Laser Welding | TIG Welding | MIG Welding | SMAW Welding |
Precision | High precision with minimal distortion | High precision but slower than laser | Moderate precision, more heat input | Lower precision, more heat input |
Speed | Fast welding speed, reduces production time | Slower welding speed | Faster than TIG, but slower than laser | Generally slower, dependent on skill level |
Heat Affected Zone (HAZ) | Minimal HAZ, reducing thermal distortion | Larger HAZ compared to laser | Larger HAZ, which can affect material properties | Larger HAZ can cause significant distortion |
Material Thickness | Suitable for thin to thick materials | Suitable for thin to medium materials | Suitable for thin to thick materials | Generally used for thicker materials |
Cost Efficiency | High initial cost, but low operating costs | Moderate initial and operating costs | Lower initial cost, higher operating costs | Low initial cost, moderate operating costs |
Ease of Use | Requires skilled operation and training | Requires skilled operation and training | Easier to learn and use compared to TIG | Simple to learn but requires more skill for quality welds |
Post-Weld Cleanup | Minimal, clean welds | Requires more cleanup | Moderate cleanup needed | Significant cleanup required |
Flexibility | Highly versatile for complex welds | Less versatile, suited for precise work | Versatile, suitable for various applications | Less versatile, suited for specific applications |
Automation | Highly compatible with automation | Less commonly automated | Moderately automated | Less compatible with automation |
Safety | Generally safe with appropriate shielding | Requires careful handling of inert gases | Requires proper ventilation and safety measures | Requires proper ventilation and safety measures |
Application of Laser Welding Stainless Steel
- Automotive Industry: In the automotive sector, laser welding is used for joining stainless steel components such as exhaust systems, fuel tanks, and structural elements.
- Aerospace Industry:: Laser welding plays a crucial role in the aerospace industry, where it is applied to assemble stainless steel parts for aircraft and spacecraft. This includes critical components like landing gear and fuel lines.
- Medical Devices: The medical device industry relies on laser welding for the fabrication of stainless steel components used in surgical instruments, implants, and diagnostic equipment.
- Food and Beverage Industry: In the food and beverage sector, laser welding is utilized for manufacturing stainless steel equipment such as tanks, pipes, and processing machinery.
- Architectural Applications: Laser welding is employed in architectural applications to join stainless steel elements used in building facades, railings, and decorative features.
- Industrial Machinery: For industrial machinery, laser welding provides robust and reliable joints for stainless steel parts such as frames, enclosures, and tooling.
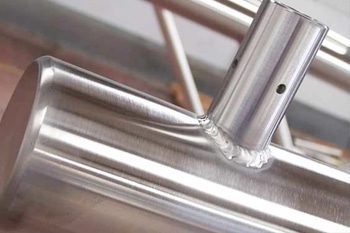
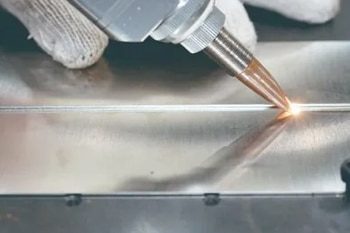
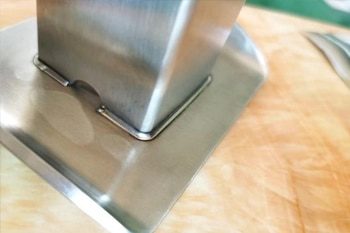
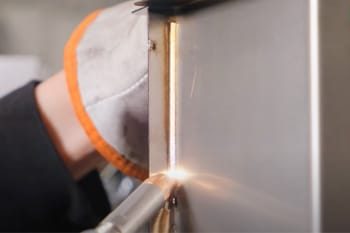
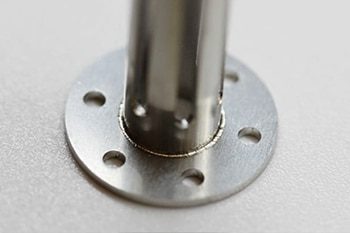
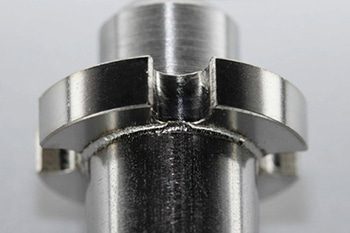
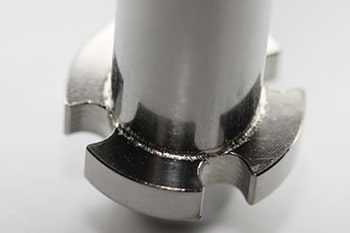
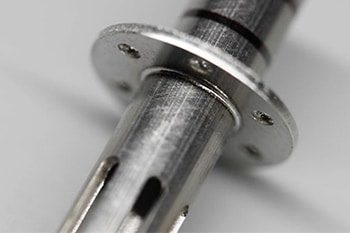