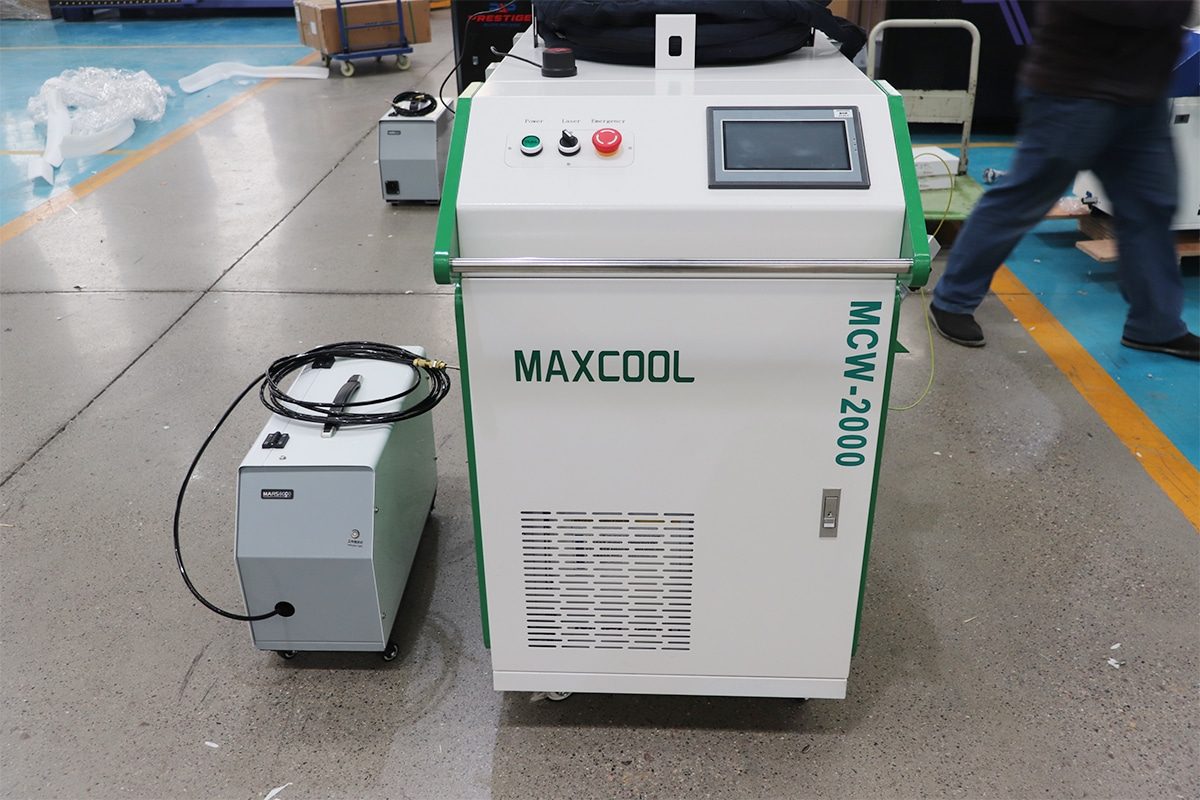
Overview of Laser Welding
Principles and Processes
Types of Laser Welding
Keyhole Laser Welding
Keyhole laser welding uses a high-energy laser beam to vaporize the material at the welding point, creating a small cavity called a “keyhole.” This keyhole is surrounded by molten material, and as the laser moves along the seam, the keyhole advances, leaving a solidified weld behind.
- Characteristics: Deep penetration, suitable for thick materials.
- Applications: Automotive parts, aerospace components, and thick metal sheets.
- Advantages: Provides strong, deep welds with minimal material distortion.
Conduction Laser Welding
Conduction laser welding operates with lower energy density, heating the material’s surface to create a shallow weld pool. The molten material solidifies quickly, forming a smooth and aesthetic weld.
- Characteristics: Limited penetration, used for thin materials and decorative welds.
- Applications: Jewelry, electronics, and medical devices.
- Advantages: Produces visually appealing welds without spatter.
Advantages and Limitations
Advantages
- High Precision: The focused laser beam allows for accurate welding, especially for small or intricate parts.
- Minimal Heat-Affected Zone (HAZ): Reduces thermal distortion, preserving the material’s properties.
- Fast Processing: Laser welding enables high-speed operations, particularly in automated systems.
- Versatility: Can weld various materials, including dissimilar metals and heat-sensitive components.
- Clean Process: Produces welds with minimal spatter and requires little to no post-weld cleaning.
Limitations
- High Initial Cost: Laser welding systems are expensive to purchase and install.
- Complex Setup: Precise alignment of the laser and workpieces is critical for effective welding.
- Material Restrictions: Reflective metals like aluminum and copper can present challenges without adjustments.
- Limited Thickness: Welding very thick materials may require multiple passes or additional equipment.
Applications of Laser Welding
Laser welding is a preferred technique in industries where precision, speed, and aesthetics are essential. Key applications include:
- Automotive Industry: Welding car bodies, electric vehicle batteries, and engine components.
- Aerospace Industry: Joining lightweight and high-strength materials like titanium and aluminum.
- Medical Devices: Fabricating surgical tools, implants, and diagnostic equipment.
- Electronics: Assembling delicate components, including sensors, microchips, and circuit boards.
- Jewelry and Luxury Goods: Creating seamless, decorative welds in gold, silver, and other precious metals.
- Energy Sector: Manufacturing batteries, solar panels, and fuel cells.
Overview of TIG Welding
Principles and Processes
Key elements of the TIG welding process include:
- Tungsten Electrode: Provides consistent heat without melting.
- Inert Gas Shielding: Prevents oxidation and contamination.
- Manual Control: Requires skilled operation to manage heat, electrode position, and filler material.
Advantages and Limitations
Advantages
- High-Quality Welds: TIG welding produces clean, precise welds with excellent strength and finish, making it suitable for aesthetic and structural applications.
- Versatility: It can be used on a wide range of materials, including aluminum, stainless steel, magnesium, and exotic alloys.
- No Spatter: Unlike other welding methods, TIG welding does not produce a spatter, ensuring a cleaner work area and finish.
- Fine Control: The process allows welders to precisely control heat input and filler material, enabling detailed work on thin or delicate materials.
- No Consumable Electrodes: The tungsten electrode is non-consumable, reducing the need for frequent replacements.
Limitations
- Skill-Dependent: TIG welding requires a high level of expertise and practice, making it less accessible for beginners.
- Slower Process: It is time-intensive compared to methods like MIG or laser welding, limiting its efficiency for large-scale production.
- Heat-Affected Zone (HAZ): TIG welding generates a larger HAZ, which can lead to material distortion in thin or heat-sensitive metals.
- Limited Automation: While TIG welding can be automated, its precision often relies on manual operation, reducing its suitability for high-speed, repetitive tasks.
- Higher Labor Costs: The skill and time required for TIG welding can increase overall project costs.
Applications of TIG Welding
TIG welding is widely used across industries that require precision and high-quality results. Its ability to handle various metals and create strong, visually appealing welds makes it invaluable for many applications, including:
- Aerospace: Welding thin aluminum and titanium components in aircraft manufacturing.
- Automotive: Fabricating exhaust systems, chassis components, and high-performance engine parts.
- Construction: Joining pipelines, structural steel, and pressure vessels.
- Art and Design: Creating sculptures, decorative metalwork, and jewelry.
- Medical Devices: Assembling surgical instruments and medical equipment.
- Maintenance and Repairs: TIG welding is commonly used for repairing damaged parts and machinery due to its precision and versatility.
Comparison of Laser Welding and TIG Welding
Efficiency and Speed
- Laser Welding: Laser welding is significantly faster than TIG welding, especially in automated setups. The focused laser beam allows for high-speed operation, making it ideal for high-volume production environments. Laser welding’s efficiency is further enhanced by its ability to complete welds in a single pass, even for deeper joints, which minimizes production time.
- TIG Welding: TIG welding is a slower, manual process that requires considerable skill and attention. While it excels in detailed and intricate work, the time required for setup, welding, and post-weld cleanup makes it less efficient for large-scale production or high-speed applications.
Precision and Accuracy
- Laser Welding: Offers unmatched precision due to its focused beam and minimal heat dispersion. Laser welding is ideal for applications with tight tolerances and small or delicate components, as it can create highly accurate welds even in complex geometries.
- TIG Welding: While precise, TIG welding relies heavily on the operator’s skill. This makes it more prone to variability, especially for repetitive tasks. However, experienced welders can achieve highly detailed results, making it suitable for fine, artistic, or custom work.
Heat-Affected Zone (HAZ)
- Laser Welding: The heat-affected zone in laser welding is minimal due to the concentrated nature of the laser beam. This reduces thermal distortion and preserves the properties of the surrounding material, making it ideal for heat-sensitive components or applications requiring structural integrity.
- TIG Welding: TIG welding generates a larger heat-affected zone due to the broader heat dispersion around the weld pool. This can lead to distortion, particularly in thin or sensitive materials, requiring additional post-weld processing to mitigate.
Weld Quality and Strength
- Laser Welding: Produces clean, high-quality welds with smooth surfaces and no spatter. The ability to control penetration depth ensures strong and consistent joints, even for dissimilar materials. Laser welds are also visually appealing and often require minimal post-weld finishing.
- TIG Welding: Known for its exceptional weld quality, TIG welding creates strong, aesthetically pleasing welds. The manual control over heat and filler material allows for customized weld profiles, making it suitable for applications where weld appearance and strength are equally important.
Equipment and Setup
- Laser Welding: Requires sophisticated equipment, including laser sources, optical systems, and precision alignment tools. While highly effective, the setup process is complex and best suited for production environments where automation can offset the initial investment and setup time.
- TIG Welding: TIG welding equipment is relatively simple and portable, making it ideal for fieldwork, repairs, or smaller workshops. However, TIG welding requires more manual intervention during setup and operation, which can increase labor time for larger projects.
Cost Considerations
- Laser Welding: The initial cost of laser welding equipment is high, and maintenance requires skilled personnel. However, its high efficiency, speed, and automation capabilities often result in a better return on investment (ROI) for large-scale or high-precision applications.
- TIG Welding: TIG welding equipment is significantly more affordable, and operating costs are lower, especially for small-scale projects or one-off tasks. However, the slower process and reliance on skilled operators can increase labor costs over time for high-volume production.
Factors Affecting Selection
Material Type and Thickness
The material type and thickness significantly impact the choice between laser welding and TIG welding.
- Laser Welding: Laser welding is highly effective for a wide range of materials, including stainless steel, aluminum, titanium, and even dissimilar metals. It is particularly suitable for thin materials and offers deep penetration with minimal heat distortion. However, for highly reflective metals like copper and brass, adjustments or specialized equipment may be necessary.
- TIG Welding: TIG welding works well with various metals, particularly stainless steel, aluminum, and magnesium. It is ideal for joining thinner materials but can also handle thicker materials when multiple passes are used. TIG welding offers superior control over the weld pool, making it suitable for metals prone to cracking or deformation.
Throughput and Speed Requirements
The speed and productivity requirements of the welding project often determine whether laser welding or TIG welding is the better choice.
- Laser Welding: Laser welding is exceptionally fast, especially in automated production lines. It can complete welds in a single pass, making it ideal for high-volume production environments. Its speed significantly reduces production time and improves overall throughput.
- TIG Welding: TIG welding is a slower process, as it requires precise manual operation. It is better suited for small-scale projects, custom applications, or situations where speed is less critical.
Weld Quality and Precision Requirements
The level of weld quality and precision required is another crucial factor in selecting between these two methods.
- Laser Welding: Laser welding excels in applications demanding high precision and clean welds. Its focused beam ensures minimal heat-affected zones (HAZ) and creates visually appealing, high-strength welds. This makes it suitable for industries like aerospace, automotive, and electronics, where precision is critical.
- TIG Welding: TIG welding is known for producing high-quality, aesthetically pleasing welds. The process allows the operator to have complete control over the heat input and filler material, making it ideal for projects requiring intricate designs or detailed finishes.
Availability of Skilled Labor
The availability and expertise of the workforce can also influence the choice between laser welding and TIG welding.
- Laser Welding: Operating laser welding systems require training in equipment setup, programming, and maintenance. While automation reduces the need for manual labor, skilled technicians are essential for troubleshooting and maintaining the system.
- TIG Welding: TIG welding relies heavily on the skill and experience of the operator. Mastering TIG welding requires time and practice, as the process demands precise control over the weld pool, heat input, and filler material application.