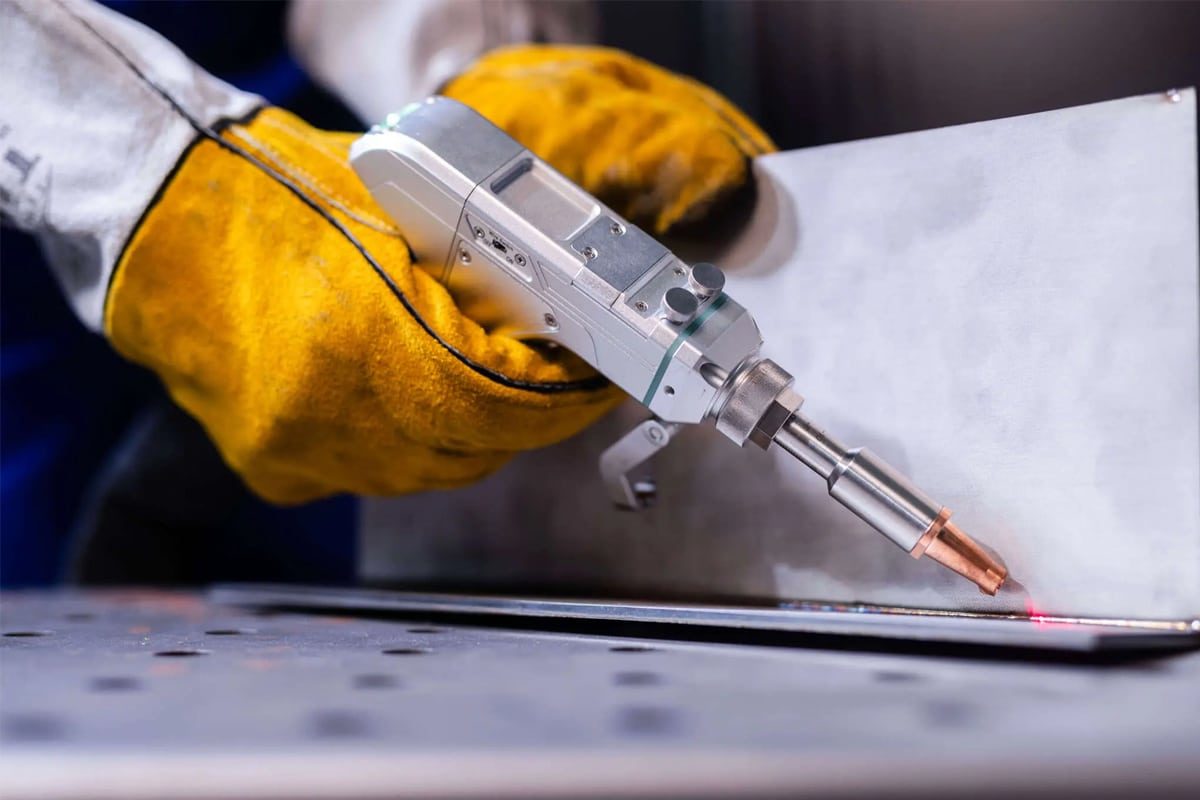
Laser Welding VS MIG Welding
Welding is a critical process in modern manufacturing and construction, helping to create strong, durable joints between metal parts. Among the various welding techniques, Laser Welding and Metal Inert Gas (MIG) Welding stand out due to their widespread use and distinct advantages. Laser Welding offers unparalleled precision and speed, making it ideal for intricate and high-volume applications with minimal heat distortion. On the other hand, MIG Welding is renowned for its versatility, ease of use, and cost-effectiveness, suitable for a broad range of materials and thicknesses. This article delves into a comprehensive comparison between Laser Welding and MIG Welding, exploring their principles, benefits, limitations, and ideal applications to help you make informed decisions in your welding processes.
Table of Contents
Understanding Laser Welding
Definition and Basic Principles
Laser welding is a highly precise welding process that uses a focused laser beam to fuse metal components. The laser beam, which stands for “Light Amplification by Stimulated Emission of Radiation,” produces intense energy concentrated on a small area, allowing it to melt and join metals. Laser welding offers high welding speeds, deep penetration, and minimal distortion, making it ideal for applications where precision is paramount.
The basic principle behind laser welding is the absorption of laser energy by the metal surface, which converts light energy into heat. This localized heat melts the metal, and as the molten material cools, it forms a strong weld. The depth and width of the weld can be controlled by adjusting the laser’s power and focus, allowing for versatility across a range of materials and thicknesses.
Types of Laser Welding
Laser welding operates in two primary modes, depending on the material thickness and the desired weld characteristics:
Conduction Mode Welding
In Conduction Mode Welding, the laser beam melts the surface of the material without creating a vaporized cavity (keyhole). The heat is conducted from the surface into the material, resulting in a shallow weld with a wide profile. This mode is typically used for thin materials where deep penetration is not required. The advantage of conduction mode welding is that it produces smooth welds with minimal surface defects, making it ideal for applications where appearance is important.
Keyhole Mode Welding
Keyhole Mode Welding is used for welding thicker materials. In this mode, the laser beam is focused with higher intensity, causing localized vaporization of the material, which forms a “keyhole” or cavity. This keyhole allows the laser energy to penetrate deeper into the material, resulting in a deep, narrow weld. Keyhole mode welding is highly efficient and provides strong welds with excellent depth-to-width ratios, making it suitable for industrial applications that require deeper penetration.
Equipment and Components
A laser welding system is composed of several essential components that work together to ensure the precision and efficiency of the welding process:
- Laser Source: The heart of the system generates the laser beam. Fiber lasers, Nd lasers, and CO2 lasers are commonly used, with fiber lasers being the most popular for metal welding due to their high efficiency and excellent beam quality.
- Beam Delivery System: Transfers the laser from the source to the workpiece, typically through optical fibers in fiber lasers or mirrors in other laser systems.
- Focusing Optics: Lenses or mirrors focus the laser beam to a small spot size, increasing the power density at the weld point. Precise focusing can help achieve the desired weld depth and quality.
- Workpiece Manipulation System: Positions the workpiece under the laser beam, often using CNC machines, robotic arms, or automated positioning systems for high precision and repeatability.
- Shielding Gas Supply: Inert gases like argon or nitrogen are used to shield the weld pool from oxidation and contamination during the welding process, ensuring a clean and high-quality weld.
- Control System: Manages parameters like laser power, beam focus, and movement to ensure consistent welding performance. Modern laser welding systems often integrate CNC controls or robotics for automated operations.
- Safety Systems: Due to the high intensity of laser beams, protective enclosures, interlocks, and laser safety glasses are necessary to prevent accidents and ensure operator safety.
Advantages of Laser Welding
- High Precision: Laser welding allows for pinpoint accuracy, making it ideal for delicate and intricate components. The small heat-affected zone minimizes warping and thermal distortion.
- High Welding Speed: Laser welding offers faster speeds compared to many traditional welding methods, increasing productivity, especially in high-volume production environments.
- Deep Penetration: Keyhole mode welding enables deep, narrow welds in thick materials, often in a single pass, reducing the need for multiple operations.
- Minimal Heat Input: The concentrated energy of the laser beam limits heat diffusion, resulting in less thermal distortion and fewer changes to the material’s properties.
- Non-Contact Process: As a non-contact process, laser welding reduces tool wear, contamination, and the need for physical electrodes or filler materials, lowering long-term operational costs.
- Versatility: Laser welding can be used on a variety of metals, including carbon steel, stainless steel, titanium, and aluminum, as well as some non-metallic materials.
- Easily Automatable: Laser welding integrates seamlessly with automated systems, such as robotic arms and CNC machines, enabling continuous, high-precision production.
Disadvantages of Laser Welding
- High Initial Investment: Laser welding equipment is more expensive than traditional welding machines like MIG welders. This can be a barrier for smaller operations or workshops with limited budgets.
- Strict Joint Fit-Up: Laser welding requires precise alignment of the parts to be welded, with minimal gaps between them. Poor fit-up can result in incomplete fusion or weld defects.
- Reflective Materials: Materials such as aluminum and copper, which have high reflectivity, can reflect the laser beam, reducing welding efficiency and requiring specialized laser systems or parameters.
- Safety Concerns: The high energy of laser beams poses safety risks, including eye and skin injuries. Adequate safety measures, such as protective enclosures and laser-safe eyewear, are mandatory.
- Complexity: Operating and maintaining a laser welding system requires trained personnel. The complexity of the equipment, especially the laser source and optical components, can result in higher maintenance requirements.
- Limited Thickness Range: Although laser welding can handle thick materials in keyhole mode, very thick materials may still require alternative methods like multi-pass welding or other welding techniques.
Applications of Laser Welding
- Laser welding is widely used in industries that demand precision, speed, and high-quality joints:
- Automotive Industry: Used for welding car body panels, transmission components, and battery systems in electric vehicles. Laser welding’s speed and precision make it ideal for mass production and lightweight designs.
- Aerospace and Defense: Critical components in aircraft engines, fuel systems, and structural parts are often laser welded to meet stringent quality and safety standards.
- Medical Devices: Laser welding is employed for producing surgical instruments, implants, and medical equipment that require precise, clean welds without post-processing.
- Electronics: In electronics manufacturing, laser welding is used for micro-welding components, such as sensors, batteries, and circuit boards, where precision and minimal thermal impact are critical.
- Jewelry and Artisanal Crafts: Laser welding allows for intricate and precise joining of delicate materials in jewelry making, enabling customization and detailed craftsmanship without damaging surrounding materials.
- Energy and Power Generation: In the energy sector, laser welding is used to fabricate and repair components in power plants, pipelines, and renewable energy systems, where reliability and strength are paramount.
Understanding MIG Welding
Definition and Basic Principles
MIG Welding, also known as Metal Inert Gas welding or Gas Metal Arc Welding (GMAW), is a welding process that utilizes a continuously fed wire electrode and a shielding gas to create an electric arc between the electrode and the workpiece. This arc generates the necessary heat to melt the electrode and the base materials, forming a molten weld pool. As the molten material cools, it solidifies, creating a strong weld joint.
The shielding gas, typically argon, helium, or a mix of gases, protects the weld pool from atmospheric contamination, such as oxygen and nitrogen, which can lead to porosity and other defects in the weld. MIG welding is known for its versatility, speed, and ease of use, making it one of the most popular welding methods for both industrial and hobbyist applications.
Equipment and Components
MIG welding systems consist of several essential components that work together to create the welding arc and protect the weld area:
- Power Source: Supplies constant voltage to maintain a stable arc. Most MIG welders use direct current (DC) with a positive electrode (DC+), which allows for deeper penetration and cleaner welds.
- Wire Feed System: Feeds the consumable wire electrode from a spool to the welding gun at a consistent speed. The wire serves as both the electrode and the filler material.
- Welding Gun: Directs the wire electrode and shielding gas to the weld area. It typically includes a trigger mechanism that controls the wire feed and gas flow.
- Shielding Gas Supply: A gas cylinder connected to the welding system provides a steady flow of inert or semi-inert gas to shield the weld pool from atmospheric contaminants. The type of gas used depends on the material being welded and the desired weld characteristics.
- Work Clamp (Ground Clamp): Connects the workpiece to the welding power source, completing the electrical circuit needed to create the arc.
- Control Panel: Allows the operator to adjust key welding parameters such as voltage, wire feed speed, and shielding gas flow rate, ensuring optimal welding performance.
Advantages of MIG Welding
- Ease of Use: MIG welding is often considered one of the easiest welding techniques to learn, making it ideal for beginners and less experienced welders. The continuous wire feed simplifies the process by eliminating the need for manual feeding of filler material.
- High Welding Speed: The continuous wire feed allows for faster welding compared to other processes like Stick or TIG welding. This makes MIG welding an efficient option for production environments where speed is essential.
- Versatility: MIG welding is compatible with a wide range of metals, including carbon steel, stainless steel, and aluminum. It can weld materials of varying thicknesses, from thin sheet metal to thicker components.
- Cleaner Welds with Less Slag: Unlike Stick welding, MIG welding produces less slag, reducing the need for extensive post-weld cleanup. This leads to cleaner, more aesthetically pleasing welds.
- Continuous Welding: The use of a continuous wire feed allows for long, uninterrupted welds, reducing the need for frequent stops and starts during the welding process.
- Cost-Effective: MIG welding equipment tends to be more affordable compared to advanced welding methods like laser welding, making it accessible for small businesses, workshops, and hobbyists.
Disadvantages of MIG Welding
- Portability Issues: MIG welding machines are generally bulkier and less portable due to the need for gas cylinders and wire feed systems. This can make it challenging to use MIG welders in remote or difficult-to-reach areas.
- Sensitivity to Environmental Conditions: MIG welding requires shielding gas to protect the weld pool, making it less suitable for outdoor use. Wind and drafts can disperse the shielding gas, leading to weld contamination and defects.
- Limited to Thin-to-Medium Materials: While MIG welding is versatile, it is not ideal for welding very thick materials in a single pass. Thicker materials may require multiple passes, which can reduce productivity.
- Spatter Formation: MIG welding can produce weld spatter, requiring additional post-weld cleanup. This spatter can also affect the quality of the weld if not properly managed.
- Dependence on Consumables: MIG welding relies on a continuous supply of wire electrodes and shielding gas, which can add to the overall cost of operation over time. Regular replacement of consumables is also necessary.
Applications
MIG welding is widely used across a variety of industries due to its speed, versatility, and relatively low cost:
- Automotive Industry: MIG welding is extensively used for car body repairs, manufacturing, and assembly, particularly for welding thin sheet metal and structural components.
- Construction and Structural Welding: In construction, MIG welding is used for fabricating structural steel, bridges, and heavy equipment. Its ability to produce long, continuous welds makes it ideal for large-scale projects.
- General Metal Fabrication: MIG welding is the go-to method for fabrication shops and metalworking industries that need to weld a variety of materials, from mild steel to aluminum.
- Manufacturing: In high-volume manufacturing environments, MIG welding is used for welding parts in production lines, such as household appliances, industrial machinery, and metal enclosures.
- Hobbyist and DIY Projects: MIG welding is popular among hobbyists and DIY enthusiasts for creating metal art, repairing machinery, or fabricating custom parts.
- Shipbuilding and Maritime Industry: MIG welding is also used in the shipbuilding industry for welding the structural framework and metal components of ships, boats, and other marine structures.
Laser Welding VS MIG Welding
Welding Speed
- Laser Welding: Known for its high-speed capabilities, laser welding can produce deep, narrow welds quickly. In applications such as automotive manufacturing, laser welding significantly reduces cycle times. This makes it highly effective for large-scale production where precision and speed are critical.
- MIG Welding: MIG welding is also relatively fast, but it may not match the speed of laser welding, particularly for thinner materials. The continuous wire feed helps maintain consistent welding, but thicker materials may require multiple passes, reducing productivity.
Weld Quality
- Laser Welding: Produces clean, precise welds with minimal spatter or need for post-processing. It has a very small Heat-Affected Zone (HAZ), which helps maintain the integrity of the surrounding material. This is crucial for applications requiring aesthetically pleasing or high-performance joints.
- MIG Welding: While MIG welding can produce strong welds, it often results in more spatter, requiring post-weld cleanup. The HAZ is larger, which may cause slight material distortion or changes in mechanical properties near the weld area.
Material Compatibility
- Laser Welding: Can weld a variety of metals, including carbon steel, stainless steel, titanium, and even dissimilar metals. However, reflective metals like copper and aluminum may require specialized lasers or settings to improve absorption and efficiency.
- MIG Welding: MIG welding is versatile and works well with common metals such as carbon steel, stainless steel, and aluminum. It’s not ideal for joining dissimilar metals without proper filler materials or advanced techniques.
Precision and Control
- Laser Welding: Offers superior precision, allowing for small, intricate welds without damaging surrounding materials. It is ideal for industries such as aerospace, electronics, and medical device manufacturing where accuracy is essential.
- MIG Welding: While MIG welding provides good control over the weld, it lacks the precision of laser welding. The weld bead is generally wider, making it less suitable for fine or detailed work.
Heat Input and Distortion
- Laser Welding: The concentrated energy of the laser beam minimizes heat input and reduces the size of the Heat-Affected Zone (HAZ). This limits thermal distortion and preserves the material’s properties, even in delicate or thin materials.
- MIG Welding: MIG welding involves higher heat input, which can cause greater distortion and a larger HAZ. This may require additional steps, such as clamping or straightening, to correct any deformations after welding.
Operational Costs
- Laser Welding: Though laser welding offers long-term savings due to lower energy consumption and minimal post-processing, the initial setup can be expensive. The non-contact process also reduces wear and tear on equipment, lowering maintenance costs over time.
- MIG Welding: MIG welding has lower initial setup costs but incurs ongoing expenses for consumables, such as wire electrodes and shielding gas. Frequent maintenance and post-weld cleanup add to the operational costs.
Equipment Costs and Maintenance
- Laser Welding: The upfront cost of laser welding equipment is high. However, the equipment tends to be durable, and since the process is non-contact, wear and tear on parts are minimal. Regular maintenance focuses on optics and laser alignment.
- MIG Welding: MIG welding machines are more affordable, but consumables like electrodes and gas can add to long-term expenses. Maintenance is required more frequently to replace worn contact tips, nozzles, and liners.
Safety Considerations
- Laser Welding: Requires strict safety protocols due to the high-power laser beams. Operators must wear protective eyewear, and enclosures are often needed to prevent exposure to laser radiation. The equipment may include interlocks and other safety features to ensure a secure working environment.
- MIG Welding: Standard welding safety measures apply, such as wearing gloves, helmets, and protective clothing. MIG welding produces fumes and ultraviolet light, which can pose health risks without proper ventilation and personal protective equipment (PPE).
Automation and Integration into Production Lines
- Laser Welding: Easily integrated into automated production lines using CNC systems or robotic arms. This makes it ideal for industries that require high-speed, precise welding with minimal human intervention, such as automotive and electronics manufacturing.
- MIG Welding: MIG welding can also be automated, but it is more common in semi-automated setups. It may not achieve the same level of speed or precision as laser welding in fully automated environments but is still effective for mass production applications.
In summary, both laser welding and MIG welding have their advantages and are suitable for different applications. Laser welding excels in precision, speed, and minimal heat distortion, making it ideal for industries that demand high-quality, intricate welds. On the other hand, MIG welding offers versatility, ease of use, and affordability, making it a practical choice for general fabrication and construction. Depending on the production needs and budget, companies can select the appropriate welding method to optimize efficiency and output.
Factors to Consider When Choosing Between Laser Welding and MIG Welding
Choosing between laser welding and MIG welding depends on several critical factors that align with the project’s needs, operational requirements, and long-term goals. Below are key considerations to help businesses make an informed decision.
Project Requirements
- Laser Welding: Best suited for projects that demand high precision, minimal thermal distortion, and aesthetic welds. It is commonly used in industries such as aerospace, medical devices, electronics, and automotive for intricate tasks or lightweight structures.
- MIG Welding: More practical for general fabrication and large-scale construction projects, such as building frames, bridges, and machinery, where high strength is required but appearance is less critical.
Material Type and Thickness
- Laser Welding: Ideal for thin metals and can handle a range of materials, including stainless steel, titanium, and dissimilar metals. However, highly reflective materials like copper and aluminum may require specialized lasers or process adjustments.
- MIG Welding: Works well with thicker materials and can weld common metals such as carbon steel, stainless steel, and aluminum. It is effective for both thin and medium-thick metals but may require multiple passes for very thick materials.
Production Volume
- Laser Welding: Offers high-speed performance and easy integration with automation systems, making it ideal for high-volume production lines with consistent welding needs. This process reduces downtime and increases throughput.
- MIG Welding: Suitable for medium-to-high production volumes but not as efficient as laser welding for continuous, automated workflows. It performs well in settings where batch production or occasional repairs are needed.
Precision Requirements
- Laser Welding: Provides unmatched precision, with minimal heat distortion and excellent weld quality, making it essential for applications requiring intricate or small welds.
- MIG Welding: Offers good control but lacks the precision of laser welding. It is better suited for applications where tolerances are less stringent, such as structural components or repair work.
Budget Constraints
- Laser Welding: Involves a high initial investment in equipment, making it more suitable for operations with larger budgets or where long-term productivity gains are prioritized. However, it reduces operating costs over time due to lower consumable usage and minimal post-processing.
- MIG Welding: Requires less initial capital, making it accessible for smaller businesses or workshops. However, the ongoing costs of consumables (wire, gas) and maintenance can add up over time.
Environmental and Safety Regulations
- Laser Welding: Requires strict adherence to safety protocols to prevent exposure to laser radiation. It may also require special enclosures and interlock systems to ensure safe operation, especially for high-power lasers.
- MIG Welding: Produces fumes, ultraviolet radiation, and spatter, requiring proper ventilation and personal protective equipment (PPE). Outdoor use may require special shielding to protect the weld from environmental conditions like wind.
Skill Level of Operators
- Laser Welding: Requires specialized training to operate the equipment effectively and maintain the system, particularly for focusing optics and laser alignment. Skilled technicians are also needed to program CNC or robotic systems for automated operations.
- MIG Welding: Easier to learn and suitable for operators with less experience. It is widely used in fabrication shops and construction sites due to its straightforward setup and operation.
Maintenance and Operational Considerations
- Laser Welding: Involves minimal wear and tear since it is a non-contact process, reducing the frequency of maintenance. However, maintaining optical components, such as lenses and mirrors, requires specialized expertise.
- MIG Welding: Requires more frequent maintenance to replace consumables like contact tips, nozzles, and liners. Regular cleaning is also needed to prevent blockages and ensure consistent wire feeding.
Selecting the right welding technique depends on balancing multiple factors, including project requirements, material characteristics, budget, and operator skills. Laser welding excels in precision, speed, and automation but requires a higher investment and skilled operators. In contrast, MIG welding offers versatility and ease of use at a lower cost, making it ideal for general fabrication and repair work.
Summary
Both laser welding and MIG welding offer unique advantages, making them valuable tools in modern manufacturing. Laser welding excels in precision, speed, and automation, making it ideal for industries that demand intricate, high-quality welds with minimal heat distortion—such as aerospace, automotive, and electronics. It is particularly effective in high-volume production environments, although it requires a significant initial investment and skilled operators.
In contrast, MIG welding is known for its versatility, affordability, and ease of use, making it suitable for general fabrication, construction, and repair tasks. While it is less precise than laser welding, it performs well on a variety of metals and thicknesses, especially in outdoor or less controlled environments. However, it involves higher ongoing costs due to consumables and more frequent maintenance.
The decision between laser welding and MIG welding depends on specific project needs, such as material type, production volume, precision requirements, and budget.
Get Laser Welding Solutions
When precision, speed, and high-quality results are essential, laser welding offers unmatched advantages over traditional welding methods like MIG welding. Whether your business requires intricate welds, minimal heat distortion, or integration into automated production lines, laser welding provides the solution. With its ability to handle a variety of materials—including stainless steel, titanium, and dissimilar metals—laser welding is ideal for industries such as automotive, aerospace, medical devices, and electronics manufacturing.
At Maxcool CNC, we specialize in providing advanced laser welding machines designed to meet the demands of modern industries. Our machines offer high-performance features, including customizable power outputs, automated control systems, and the flexibility to suit different production scales. Backed by expert technical support and tailored solutions, Maxcool CNC ensures you get the most out of your investment. Contact us today to explore how our laser welding solutions can elevate your production capabilities, enhance efficiency, and deliver consistent, top-quality results.