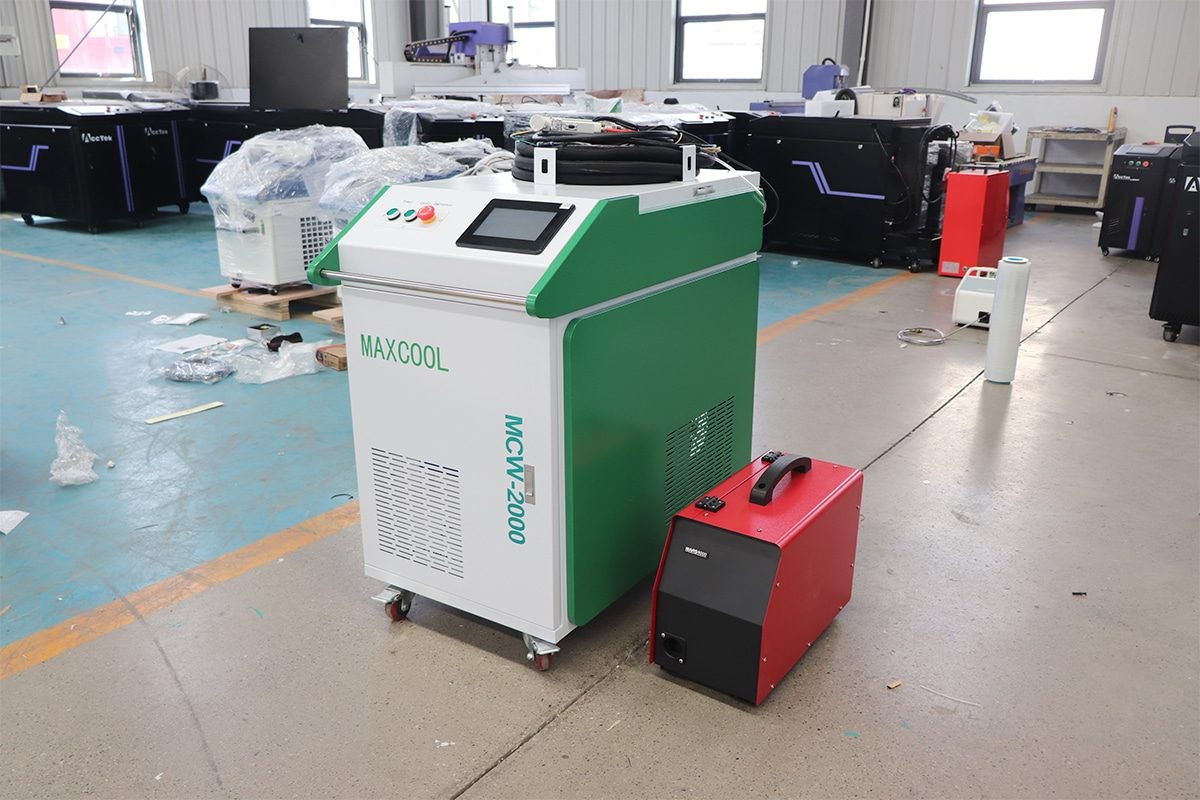
Overview of Laser Welding
Principles and Processes of Laser Welding
Types of Laser Welding Technologies
There are several types of laser welding technologies, each suited for different applications:
- Laser Beam Welding (LBW): A general term for using a laser to join materials, providing deep penetration and fast processing.
- Laser Keyhole Welding: Creates a vaporized cavity (keyhole) that allows deep, strong welds with minimal heat impact.
- Conduction Mode Welding: Used for surface-level welds where deep penetration is not needed, often used in thin materials and decorative welds.
- Pulsed Laser Welding: Uses short bursts of laser energy to weld delicate components, ideal for micro-welding in electronics and medical devices.
Advantages and Limitations of Laser Welding
Advantages
- High Precision and Minimal Distortion: The focused laser beam ensures clean and accurate welds with a small heat-affected zone (HAZ).
- Fast Welding Speeds: Laser welding is significantly faster than arc welding, increasing productivity.
- No Contact and No Electrode Wear: Unlike traditional arc welding, laser welding is non-contact, reducing tool wear and contamination risks.
- Minimal Post-Processing Required: Produces smooth, clean welds, reducing the need for grinding or finishing.
- Easily Automated: Integrates well with CNC machines and robotic systems, making it ideal for mass production.
- Works with a Wide Range of Materials: Suitable for metals, alloys, and even dissimilar materials.
Limitations
- High Initial Investment: Laser welding machines are expensive, requiring significant upfront costs.
- Limited Effectiveness on Very Thick Materials: Deep penetration requires high-power lasers, increasing equipment costs.
- Reflective Metal Challenges: Materials like aluminum and copper require specialized laser settings to minimize reflection and absorption issues.
- Requires Skilled Operators: While automation is possible, programming and maintenance require expertise.
Applications of Laser Welding in Various Industries
Laser welding is widely adopted in industries that demand precision, speed, and high-quality welds:
- Automotive Industry: Used for car body panels, batteries, exhaust systems, and precision components.
- Aerospace Industry: Ensures lightweight and strong welds in engine components, turbine blades, and fuel tanks.
- Electronics Industry: Ideal for micro-welding in circuit boards, semiconductors, and sensors.
- Medical Device Manufacturing: Used for surgical instruments, implants, and medical sensors that require biocompatibility and high precision.
- Jewelry and Watchmaking: Enables fine, intricate welds without damaging delicate materials.
- Shipbuilding and Heavy Machinery: Applied in high-strength, corrosion-resistant welds for marine and industrial applications.
Overview of Arc Welding
Principles and Processes of Arc Welding
The key components of arc welding include:
- Power Supply: Provides a constant or variable current (AC or DC) to sustain the arc.
- Electrode: Can be consumable (melts to form the weld) or non-consumable (uses a separate filler material).
- Shielding Method: Either shielding gas (inert gases like argon, and CO2) or flux coating (on stick electrodes or flux-cored wire) protects the weld from oxidation.
- Weld Pool: The molten metal that forms during welding and solidifies to create the joint.
Types of Arc Welding Technologies
There are several arc welding methods, each designed for specific applications:
- Shielded Metal Arc Welding (SMAW) – Stick Welding
- Uses a flux-coated consumable electrode that melts to form the weld.
- The flux creates a protective gas shield and slag to prevent oxidation.
- Advantages: Simple, portable, and works well in outdoor conditions.
- Common Applications: Structural steel, pipelines, shipbuilding, and repair work.
- Gas Metal Arc Welding (GMAW) – MIG (Metal Inert Gas) Welding
- Uses a continuous consumable wire electrode with an external shielding gas (argon, CO2, or mixtures).
- Offers high welding speed, minimal spatter, and clean welds.
- Advantages: Easy automation, high productivity, minimal post-weld cleaning.
- Common Applications: Automotive manufacturing, metal fabrication, and industrial welding.
- Gas Tungsten Arc Welding (GTAW) – TIG (Tungsten Inert Gas) Welding
- Uses a non-consumable tungsten electrode with argon or helium shielding gas.
- Produces high-quality, precise welds with superior control over heat input.
- Advantages: Best for thin materials, non-ferrous metals, and critical welds.
- Common Applications: Aerospace, medical devices, automotive, and precision fabrication.
- Flux-Cored Arc Welding (FCAW)
- Similar to MIG welding but uses a flux-filled wire for self-shielding or dual shielding (flux and gas).
- Advantages: Effective in outdoor environments and for thick materials.
- Common Applications: Construction, shipbuilding, heavy structural welding.
- Submerged Arc Welding (SAW)
- Uses a continuous consumable electrode under a granular flux layer, which prevents spatter and enhances weld quality.
- Advantages: High deposition rate, deep penetration, and minimal fumes.
- Common Applications: Pressure vessels, pipelines, shipbuilding, and thick steel welding.
- Plasma Arc Welding (PAW)
- Uses a constricted plasma arc for higher energy concentration and deeper penetration.
- Advantages: Precise, controlled welds suitable for automation.
- Common Applications: Aerospace, electronics, and high-precision industrial fabrication.
Advantages and Limitations of Arc Welding
Advantages
- Versatile and Applicable to A Wide Range of Materials: Works with steel, stainless steel, aluminum, and alloys.
- Cost-Effective: Arc welding machines and consumables are affordable compared to laser welding systems.
- Strong Welds for Thick Materials: Ideal for structural and heavy-duty applications.
- Portable and Practical for Fieldwork: Stick welding (SMAW) can be used in outdoor, remote, and harsh environments.
- Well-Established and Easy-to-Train Workers: Skilled labor and resources are widely available.
Limitations
- Produces More Heat Distortion: Causes larger heat-affected zones (HAZ) than laser welding.
- Slower Than Laser Welding: Some methods require multiple passes to weld thick sections.
- More Post-Weld Cleaning Needed: Processes like SMAW and FCAW create slag that must be removed.
- Lower Precision Compared to laser welding: Not ideal for micro-welding or delicate parts.
- Safety Concerns: Generates harmful fumes, sparks, and UV radiation, requiring proper protective gear and ventilation.
Applications of Arc Welding in Various Industries
Arc welding is widely used across industries that require strong, durable welds for structural and heavy-duty applications:
- Construction and Infrastructure: Used for bridges, buildings, pipelines, and industrial structures.
- Shipbuilding and Marine Engineering: Essential for hull construction, underwater welding, and vessel repairs.
- Automotive and Transportation: Applied in chassis, vehicle frames, and exhaust systems.
- Oil and Gas Industry: Used in pipeline welding, offshore platforms, and refinery structures.
- Manufacturing and Heavy Equipment: Applied in machinery, industrial components, and fabrication shops.
- Aerospace Industry: Used for structural and high-strength components.
- Maintenance and Repair Work: Common for machinery repairs, railroads, and mining operations.
Principles of Laser Welding
Working Principles of Laser Welding
There are two primary modes of laser welding:
- Conduction Mode Welding
- Occurs at low energy densities (<10⁶ W/cm²).
- The laser heats the metal surface, creating a broad and shallow weld pool.
- Suitable for thin materials and applications where minimal penetration is required.
- Keyhole Mode Welding
- Occurs at high energy densities (>10⁶ W/cm²), where the laser vaporizes a small portion of the metal.
- This creates a deep, narrow cavity (keyhole) filled with vaporized metal, allowing deep penetration welding.
- Commonly used in the automotive, aerospace, and precision fabrication industries.
Interaction Between Laser and Metal
Factors Affecting Laser-Metal Interaction:
- Absorption of Laser Energy
- Metals absorb laser energy at different rates based on their wavelength and reflectivity.
- Materials like steel and titanium absorb laser energy efficiently, while aluminum and copper require specialized lasers due to their high reflectivity.
- Thermal Conductivity
- High thermal conductivity metals (copper, aluminum) dissipate heat quickly, requiring higher laser power.
- Low thermal conductivity metals (stainless steel, titanium) retain heat longer, making them easier to weld.
- Phase Transition and Plasma Formation
- At high power densities, the laser vaporizes the metal, creating a plasma cloud that can absorb or scatter laser energy.
- Optimizing shielding gas (argon, helium) helps control plasma formation and improves weld quality.
- Surface Condition
- Oxides, coatings, or rough surfaces can affect laser absorption and weld consistency.
- Pre-cleaning with laser cleaning or chemical treatments improves welding performance.
Key Parameters Affecting Laser Welding
To achieve high-quality welds, several critical parameters must be controlled:
- Laser Power
- Determines the amount of heat input into the weld.
- Higher power enables deeper penetration, while lower power is ideal for thin materials and fine welding.
- Welding Speed
- Faster welding reduces heat input, minimizing distortion.
- Slower speeds increase penetration but can cause excessive heat buildup and defects.
- Focus Position (Focal Spot Size)
- The focal point must be precisely aligned with the weld joint for maximum energy concentration.
- A small focal spot provides deep penetration, while a larger focal spot creates wider welds.
- Shielding Gas Type and Flow Rate
- Protects the weld pool from oxidation and contamination.
- Argon: Commonly used for stainless steel and titanium.
- Helium: Reduces plasma formation, improving penetration in deep welds.
- Nitrogen: Used for aluminum and copper alloys to enhance weld strength.
- Pulse vs. Continuous Wave (CW) Mode
- Pulsed Mode: Used for thin materials and micro-welding, reducing heat buildup.
- Continuous Wave (CW) Mode: Used for deep penetration and high-speed welding.
- Joint Fit-Up and Material Thickness
- Precise alignment is necessary to ensure proper fusion and strong welds.
- For gaps, filler material may be required to prevent defects like porosity.
Principles of Arc Welding
Working Principles of Arc Welding
The arc welding process can use consumable or non-consumable electrodes, depending on the method:
- Consumable electrodes (e.g., in MIG, Stick, and Flux-Cored welding) melt to become part of the weld.
- Non-consumable electrodes (e.g., in TIG welding) require a separate filler material.
Formation of Arc and Molten Pool
Arc Formation
There are two main types of electrical current used in arc welding:
- Direct Current (DC): Provides a stable arc and deep penetration, commonly used in TIG and MIG welding.
- Alternating Current (AC): Used for welding materials like aluminum, where oxidation layers need to be broken.
Molten Pool Formation
The characteristics of the molten pool depend on:
- Welding Current:Higher current leads to deeper penetration and a larger weld pool.
- Travel Speed:Faster speeds produce narrower welds, while slower speeds create wider welds.
- Shielding Method:Shielding gases (MIG, TIG) or flux coatings (Stick, FCAW) protect the weld from contamination.
Key Parameters Affecting Arc Welding
To achieve strong, defect-free welds, several welding parameters must be controlled:
- Welding Current (Amperage)
- Determines the amount of heat generated in the arc.
- Higher Amperage: Deeper penetration, larger weld pool, but more distortion.
- Lower Amperage: Shallower welds, better control for thin materials.
- Arc Voltage
- Controls the arc length and weld profile.
- Higher Voltage: Wider arc, less penetration, softer weld bead.
- Lower Voltage: Narrower arc, deeper penetration.
- Travel Speed
- The speed at which the electrode moves along the joint.
- Fast Travel Speed: Reduces heat input, and prevents excessive melting, but may cause lack of fusion.
- Slow Travel Speed: Increases penetration but can cause excessive heat buildup and warping.
- Electrode Type and Polarity
- Consumable electrodes (MIG, Stick, FCAW) melt into the weld.
- Non-consumable electrodes (TIG) require a separate filler material.
- Polarity:
- DC Electrode Positive (DCEP): Deeper penetration, stronger welds.
- DC Electrode Negative (DCEN): Faster deposition but shallower penetration.
- AC Welding: Used for aluminum and special applications.
- Shielding Gas or Flux
- Protects the weld pool from oxidation and contamination.
- Argon and Helium: Used in TIG and MIG welding for clean, precise welds.
- Carbon Dioxide (CO2): Used in MIG welding for deeper penetration and cost-effectiveness.
- Flux-coated electrodes (Stick Welding) and flux-cored wires (FCAW) provide self-shielding properties.
- Joint Preparation and Fit-Up
- Proper alignment and cleaning of base metals ensure strong, defect-free welds.
- Gaps and misalignment can lead to welding defects like porosity and weak joints.
Comparison of Laser Welding and Arc Welding
Efficiency and Speed
Laser Welding
- Offers high-speed operation, with welding speeds 3-10 times faster than arc welding for thin materials.
- Can weld thin metals and small components rapidly, making it ideal for automated production lines.
- Minimal need for post-processing due to clean welds.
Arc Welding
- Generally slower, especially for thick materials, as it often requires multiple passes.
- Consumable electrodes (MIG, Stick) require periodic replacement, slowing down the process.
- More post-weld cleanup is required, reducing overall efficiency.
Precision and Accuracy
Laser Welding
- Provides high-precision welding, suitable for delicate, micro, and intricate welds.
- The non-contact process reduces the risk of contamination or mechanical distortion.
- Ideal for electronics, medical devices, and aerospace components.
Arc Welding
- Less precise than laser welding due to larger electrode size and manual control variations.
- More suitable for structural applications where extreme precision is not required.
- This can result in wider weld beads and the potential for misalignment.
Heat-Affected Zone (HAZ) and Distortion
Laser Welding
- Produces a small, concentrated heat-affected zone (HAZ) due to its focused energy.
- Reduces warping and material distortion, making it ideal for thin materials and precision parts.
Arc Welding
- Generates a larger HAZ, leading to more thermal distortion and potential weakening of surrounding material.
- Requires post-weld corrections like grinding, straightening, or heat treatment.
Weld Quality and Strength
Laser Welding
- Produces high-quality, clean, and aesthetically appealing welds.
- Deep penetration welding is possible with keyhole welding mode.
- Reduced risk of defects such as porosity, cracks, or undercutting.
Arc Welding
- Capable of deep penetration welding, but quality depends on operator skill, electrode type, and shielding gas.
- More prone to spatter, slag inclusion, and inconsistent weld beads.
- May require additional post-weld finishing to remove slag and imperfections.
Equipment and Setup
Laser Welding
- Requires specialized laser sources (fiber, CO2, or diode lasers) and optical systems.
- Often integrated into CNC machines or robotic welding systems for high-volume production.
- Requires trained personnel for programming and maintenance.
Arc Welding
- Simple setup – Power source, electrode, and shielding gas (if required).
- More accessible for manual and on-site welding applications.
- Equipment is more widely available and easier to use.
Cost Considerations
Laser Welding
- High initial investment – Laser welding machines are expensive, especially for high-power fiber lasers.
- Lower operational costs – Minimal consumables, reduced post-weld processing, and longer machine lifespan.
- Cost-effective for mass production and automated manufacturing.
Arc Welding
- Lower upfront cost – Arc welding machines are affordable and widely available.
- Higher consumable costs – Requires continuous electrode replacement, shielding gas, and more post-weld labor.
- More cost-effective for small-scale and heavy-duty applications.
Choosing the Right Welding Technology
Factors to Consider When Selecting Welding Methods
Before choosing a welding process, it’s essential to evaluate the following aspects:
- Material Type and Thickness: Some welding methods perform better with specific metals and thicknesses.
- Weld Quality and Precision: If high precision and minimal distortion are required, a more advanced process may be necessary.
- Production Volume and Speed: Mass production requires faster and more automated welding techniques.
- Work Environment and Accessibility: On-site welding or fieldwork may require more portable equipment.
- Cost Constraints: Initial investment, operational costs, and long-term efficiency must be considered.
Material Compatibility and Requirements
Laser Welding
- Works well with stainless steel, carbon steel, titanium, aluminum, and even dissimilar metals.
- Highly effective for thin materials, as it reduces distortion and heat-affected zones (HAZ).
- Requires higher power lasers for reflective metals like aluminum and copper.
- Best suited for precision welding in industries like aerospace, medical devices, and electronics.
Arc Welding
- Suitable for thicker materials, such as structural steel and heavy-duty applications.
- More forgiving on rusty, painted, or dirty surfaces (especially Stick and Flux-Cored welding).
- Requires additional filler materials for certain joints and dissimilar metals.
- Used in construction, pipeline welding, shipbuilding, and repair work.
Project Specifications and Goals
Laser Welding
- Best for automated and high-speed production.
- Produces clean, precise welds with minimal post-processing.
- Ideal for small, intricate parts requiring tight tolerances.
- Suitable for industries with strict quality control, such as medical devices and aerospace.
Arc Welding
- More versatile for on-site and outdoor welding.
- Capable of deep penetration for thick metals, making it ideal for structural projects.
- Lower precision than laser welding, but strong welds for heavy fabrication.
- Used in infrastructure, repair work, shipbuilding, and manufacturing.
Budget and Resource Considerations
Laser Welding
- High Initial Investment: Laser welding machines are expensive but reduce operational costs over time.
- Low Consumable Costs: No need for electrodes, minimal filler materials, and reduced post-weld cleanup.
- Lower Labor Costs: Automation reduces the need for skilled welders.
- More cost-effective for high-volume production.
Arc Welding
- Lower Upfront Costs: Welding machines are affordable and widely available.
- Higher Operational Costs: Continuous use of electrodes, shielding gas, and post-weld cleaning.
- More Labor-Intensive: Requires skilled welders, increasing labor costs.
- Better for one-off projects or field repairs.
Environmental and Safety Considerations
Emissions and Environmental Impacts
Laser Welding
- Lower emissions and minimal waste: The precise, concentrated laser beam produces fewer fumes and minimal spatter.
- No need for consumables: Unlike arc welding, laser welding does not require electrodes or flux, reducing waste and chemical byproducts.
- Energy-efficient for thin materials: Uses less energy per weld in high-speed, automated applications.
- Potential reflective energy waste: Some metals (e.g., aluminum, copper) reflect laser beams, reducing efficiency.
Arc Welding
- Higher emissions: Generates more fumes, gases, and slag, which can be hazardous to both workers and the environment.
- Higher material waste: Consumable electrodes and filler materials create additional waste.
- Energy-intensive for thick materials: Requires higher power input for deep penetration welding.
- Potential water pollution: Waste materials, slag, and flux residues can contaminate water sources if not properly managed.
Occupational Health and Safety Hazards
Laser Welding
- No direct contact with metal: Since laser welding is a non-contact process, it eliminates risks like electrode burns or spatter injuries.
- Less exposure to harmful fumes: Produces fewer toxic fumes compared to arc welding.
- Laser radiation hazards: High-power lasers can cause eye and skin injuries, requiring specialized protective gear.
- Risk of fire and reflection hazards: Laser beams can reflect off shiny surfaces, posing a fire or eye injury risk.
- Requires enclosed workstations: To prevent laser exposure, operators often use safety enclosures and automated systems.
Arc Welding
- High fume and gas exposure: Produces toxic fumes (e.g., ozone, nitrogen oxides, metal oxides) that require proper ventilation.
- Arc flash hazards: Intense UV and IR radiation can cause severe eye burns (welder’s flash) and skin damage.
- Spatter and burns: Molten metal spatter can cause serious burns if protective gear is not worn.
- Noise pollution: Arc welding produces high noise levels, leading to potential hearing loss over time.
- Electrical shock risks: Direct contact with live electrodes or wet surfaces can result in electric shocks.
Regulatory Compliance and Standards
Laser Welding Regulations
- Laser Safety Standards
- ANSI Z136.1 (U.S.): Regulates laser safety measures.
- IEC 60825 (International): Defines laser classification and safety guidelines.
- OSHA (Occupational Safety and Health Administration): Requires protective eyewear and enclosures for laser operations.
- Environmental Compliance
- ISO 14001: Focuses on environmental management systems to minimize industrial emissions.
- REACH (EU Regulation): Ensures safe use of chemicals in industrial processes.
Arc Welding Regulations
- Welding Safety Standards
- ANSI Z49.1: Covers welding safety measures, including fume control and protective gear.
- AWS D1.1: Welding structural steel safety and quality standards.
- OSHA Regulations: Requires proper ventilation, personal protective equipment (PPE), and electrical safety measures.
- Fume and Emission Control Standards
- NIOSH (National Institute for Occupational Safety and Health): Establishes exposure limits for welding fumes.
- EPA (Environmental Protection Agency): Regulates emissions and hazardous material handling.