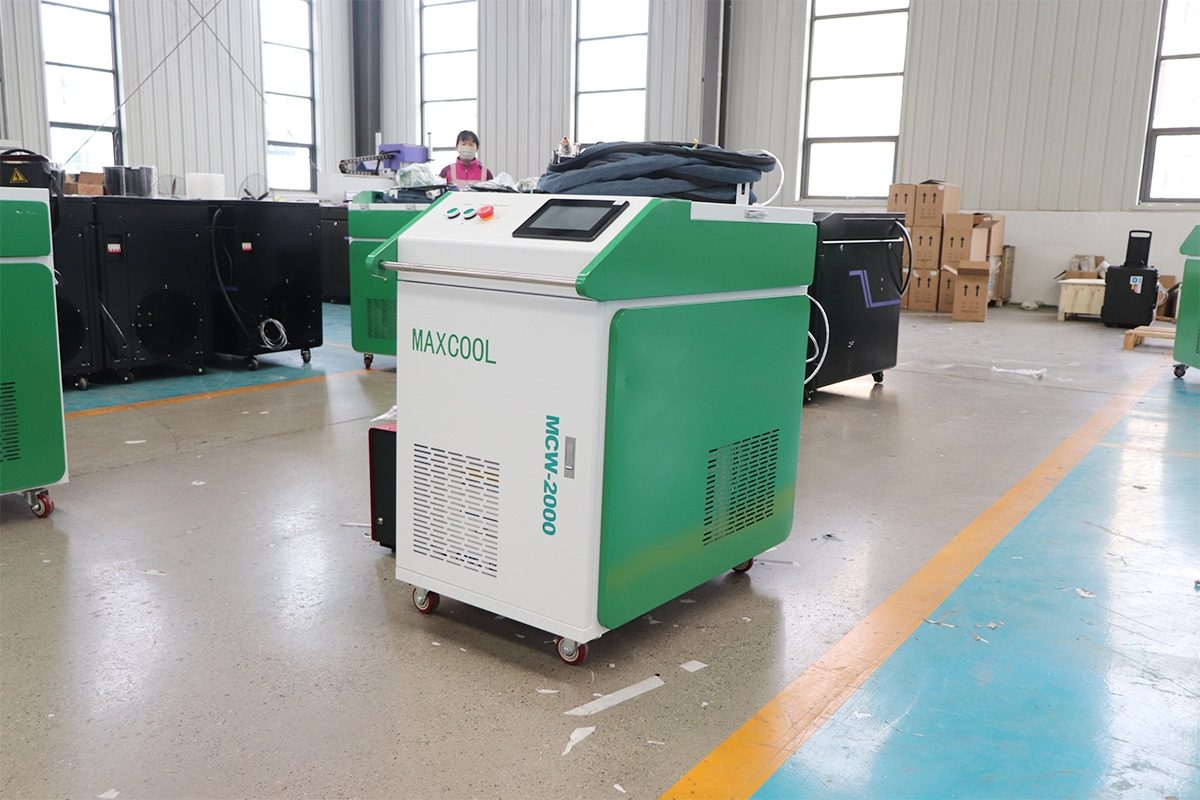
Fundamentals of Laser Welding Machines
Basic Principles of Laser Welding
Types of Laser Welding Techniques
- Conduction Welding: In conduction welding, the laser heats the workpiece surface until it melts, but the energy does not penetrate deeply. The primary mechanism is thermal conduction, where heat transfers through the material from the weld surface inward. This approach is generally used for thin sections or when cosmetic weld appearance is paramount, as the resulting welds have a smooth top surface but shallower penetration.
- Keyhole Welding: Keyhole welding involves using sufficient laser power to create a deep, narrow vapor cavity, often referred to as a “keyhole,” within the material. The beam penetrates more substantially, and molten metal flows around the keyhole before solidifying. This technique produces deeper welds and is advantageous for thicker materials or high-volume production setups, offering rapid processing and high aspect ratio welds.
Laser Sources
- Fiber Lasers: Fiber lasers use an optical fiber doped with rare-earth elements (e.g., ytterbium) as the lasing medium. Their high energy efficiency, compact size, and robust design make them an increasingly popular choice. Fiber lasers typically have lower maintenance demands, longer operational lifespans, and excellent beam quality, leading to precise, repeatable welds. They are also well-suited for high-volume industrial environments.
- Diode Lasers: Diode lasers generate light directly from semiconductor diodes. Although typically available in lower to moderate power ranges, they can be clustered or stacked for higher outputs. Known for efficiency and compactness, diode lasers are ideal for applications requiring less power but high reliability. Thermal management is crucial, as overheating can rapidly degrade diode performance.
- CO2 Lasers: CO2 lasers employ a gas mixture (primarily carbon dioxide) as the gain medium. They have been a mainstay in sheet metal cutting and welding for decades due to their ability to produce high continuous-wave power. However, they often require larger footprints and more intensive maintenance—such as regular realignment and gas checks—when compared to fiber lasers.
- Nd: YAG Lasers: Nd: YAG (Neodymium-doped Yttrium Aluminum Garnet) lasers are solid-state systems, previously favored for certain precision tasks. While they remain effective in specific niche applications, the rise of fiber lasers has overshadowed Nd: YAG due to fiber’s higher energy efficiency and simpler maintenance. Still, Nd: YAG machines can deliver excellent weld quality when properly maintained and operated.
Components of a Laser Welding Machine
A laser welding system consists of several interdependent subsystems:
- Laser Source: The core mechanism generating the laser beam (e.g., fiber, diode, CO2, or Nd: YAG).
- Beam Delivery Optics: Lenses or mirrors that direct and focus the beam onto the workpiece, sometimes incorporating fiber-optic cables for remote delivery.
- Cooling System: Maintains stable temperatures in the laser source and associated components, often via a chiller or water-cooling unit.
- Motion Control or Robotics: Positions the laser head or workpiece accurately. This may be a robotic arm, gantry, or CNC table.
- Control Electronics and Software: Oversees laser power modulation, beam pulses, welding speed, and safety features like interlocks and emergency stops.
Why Service Life Matters
Key Components and Their Lifespans
Laser Source
- Fiber Lasers: Widely praised for their robust design and excellent beam quality, fiber lasers often achieve operational lifespans of tens of thousands of hours. Their doped fiber cores and minimal use of free-space optics reduce the likelihood of misalignment and contamination, leading to extended uptime and lower maintenance demands.
- Diode Lasers: Diodes can be exceptionally durable, offering service lives of 10,000 to 30,000 hours or more. However, precise thermal management is critical; excessive heat can degrade diode performance and shorten component lifespans.
- CO2 Lasers: Traditionally dominant in industrial settings, CO2 lasers can deliver high continuous-wave power but require more frequent service. Their gas mixtures degrade over time, while internal optics and power supplies may demand periodic alignment or replacement.
- Nd: YAG Lasers: Solid-state Nd: YAG lasers still see use in specialized niches. Flash lamp-pumped versions need lamp replacements every few hundred to a thousand hours, while diode-pumped models are more durable. Proper alignment and regular checks help maintain acceptable lifespans.
Optics and Beam Delivery System
Cooling System
Mechanical Systems
Electronics and Control Systems
Consumables
Operating Parameters and Their Impact on Service Life
Power Setting and Duty Cycle
Welding Speed and Heat Input
Materials and Their Effects
Pulse VS. Continuous Wave (CW) Operation
- Pulse Mode: Laser energy is delivered in short bursts, allowing for precise control of heat input and reduced thermal distortion. However, each pulse creates a rapid heating and cooling cycle, which can place repetitive stress on the laser source and optics if power levels are too high.
- Continuous Wave (CW) Mode: The laser emits a steady beam at a given power. CW welding typically provides stable operating conditions but may generate higher average heat over longer durations. Machines designed for CW must have robust cooling solutions to handle the sustained load without compromising component longevity.
Shielding Gas and Ambient Conditions
Operator Skill and Process Control
Conclusions on Operating Parameters
Maintenance Strategies and Best Practices
Preventive VS. Predictive Maintenance
Cleaning and Inspection of Optics
Optical components (lenses, mirrors, protective windows) are critical to beam quality. Even minor contamination can cause light scattering and hot spots:
- Regular Visual Checks: Inspect optics for dust, spatter, or damage before each shift.
- Proper Cleaning Techniques: Use recommended lens wipes and solvent; never wipe optics with rough or dirty materials.
- Alignment Verification: Confirm that all optical elements remain properly aligned after cleanings or repairs.
Cooling System Maintenance
Cooling units—water chillers or air-cooled systems—must dissipate heat effectively to prevent thermal stress on laser sources and optics:
- Coolant Quality: Replace or top up coolant at intervals specified by the manufacturer, ensuring it remains free of contaminants.
- Filter Checks: Clean or replace filters regularly to maintain optimal flow and reduce the risk of overheating.
- Leak Inspections: Periodically inspect hoses, fittings, and seals, as even a small coolant leak can lead to equipment damage over time.
Mechanical and Motion System Care
Robotic arms, gantry systems, or CNC tables position the laser head with high precision:
- Lubrication: Keep bearings, linear guides, and drive screws well-lubricated to reduce friction and wear.
- Alignment: Verify axis calibration and correct any drift to maintain accuracy.
- Wear Monitoring: Listen for unusual noises and watch for jerky movements, both of which can indicate mechanical stress or failing components.
Electronics and Control Panel Maintenance
The control system manages power delivery, motion control, and safety interlocks:
- Environmental Protection: Ensure control cabinets are free from dust and moisture, using sealed enclosures or filters if necessary.
- Cable and Connector Checks: Inspect connections for signs of wear, corrosion, or looseness.
- Software Updates: Install firmware or software patches to improve performance and address known issues.
Documentation and Record-Keeping
Accurate logs create a clear picture of each machine’s usage and maintenance history:
- Operating Hours: Track total run time to plan preventive tasks.
- Component Replacements: Note the date, reason, and outcome for any part swap.
- Parameter Changes: Record major adjustments to power, duty cycle, or feed rates to correlate with component wear.
Training and Standard Operating Procedures
Properly trained personnel are instrumental in preventing premature machine wear:
- Skill Development: Teach operators how to adjust parameters safely and recognize early warning signs of component stress.
- Step-by-Step SOPs: Create protocols for start-up, shutdown, and cleaning tasks, ensuring consistent practices.
- Safety Emphasis: Emphasize laser safety protocols and handling procedures to minimize accidental damage.
Scheduling Maintenance
Maintenance intervals should reflect both usage intensity and environmental conditions:
- Tailored Intervals: High-duty cycles or dusty work environments may require more frequent checks than light usage scenarios.
- Combine Preventive and Predictive: Maintain basic schedules while utilizing data-driven insights to refine service intervals.
- Annual Overhauls: At least once a year, conduct a comprehensive machine audit, addressing wear items proactively for uninterrupted production.
Common Failure Modes and Troubleshooting
Degradation of Laser Power
- Symptoms: Gradual decrease in weld penetration, inconsistent weld quality, or slower processing speeds.
- Possible Causes: Contaminated optics, misaligned beam delivery paths, aging laser diodes, or insufficient cooling.
- Troubleshooting: Begin by inspecting and cleaning all optical components. Check for proper alignment of mirrors or fiber delivery, and verify that coolant flow and temperature are within specifications. If problems persist, measure the laser’s output power; a significant drop may indicate diode or resonator degradation.
Overheating and Thermal Shutdowns
- Symptoms: Sudden power cuts, temperature alarms, or protective shutdowns during prolonged or high-power operations.
- Possible Causes: Low coolant levels, clogged filters, faulty chillers, or inadequate ventilation.
- Troubleshooting: Ensure the coolant circuit is free of leaks and contamination. Clean or replace any filters, and verify that fans and heat exchangers are functioning correctly. Check ambient conditions—excessive room temperature can overstress cooling systems.
Optics Damage
- Symptoms: Visible burns or cracks on lenses and mirrors, hot spots in the beam profile, or rapid power drop during welding.
- Possible Causes: Contamination from spatter or dust, improper cleaning methods, back-reflection damage (especially with highly reflective metals).
- Troubleshooting: Inspect optics under proper lighting to detect micro-cracks or debris. Use only manufacturer-approved cleaning tools and solvents. Consider upgrading to protective windows or specialized anti-reflective coatings when welding reflective materials.
Electrical Failures
- Symptoms: Inconsistent power output, flickering control panels, or complete system shutdowns.
- Possible Causes: Voltage spikes, faulty power supplies, deteriorated cables, or loose connections.
- Troubleshooting: Test power supply outputs for stability. Inspect wiring harnesses and connectors for signs of corrosion or physical damage. Use surge protectors or uninterruptible power supplies (UPS) to safeguard sensitive electronics.
Mechanical Wear and Positioning Errors
- Symptoms: Crooked weld seams, dimensional inaccuracies, or unexpected vibrations and noise.
- Possible Causes: Worn bearings, misaligned motion axes, loose drive belts, or robotic collision events.
- Troubleshooting: Perform routine alignment checks and calibration procedures. Lubricate rails, gears, and bearings at recommended intervals. If motion errors persist, inspect for backlash in drive components or damage to servo motors.
Software and Control Glitches
- Symptoms: Unresponsive user interface, erratic parameter changes, or unexplained process interruptions.
- Possible Causes: Outdated firmware, corrupted software, or disrupted network connections (in networked systems).
- Troubleshooting: Restart the control system and monitor error logs for clues. Update software to the latest versions provided by the manufacturer. Check that all communication cables and network connections are secure and functioning.
Premature Consumable Wear
- Symptoms: Frequent replacement of protective windows, nozzles, or specialized lenses. Excessive spatter buildup on optics.
- Possible Causes: Incorrect shielding gas flow, excessive laser power, or welding dirty/oily materials.
- Troubleshooting: Adjust gas flow parameters and review weld settings. Clean workpieces thoroughly before welding to reduce spatter. Use lower power settings when possible, or introduce pulse welding techniques to reduce material ejection.