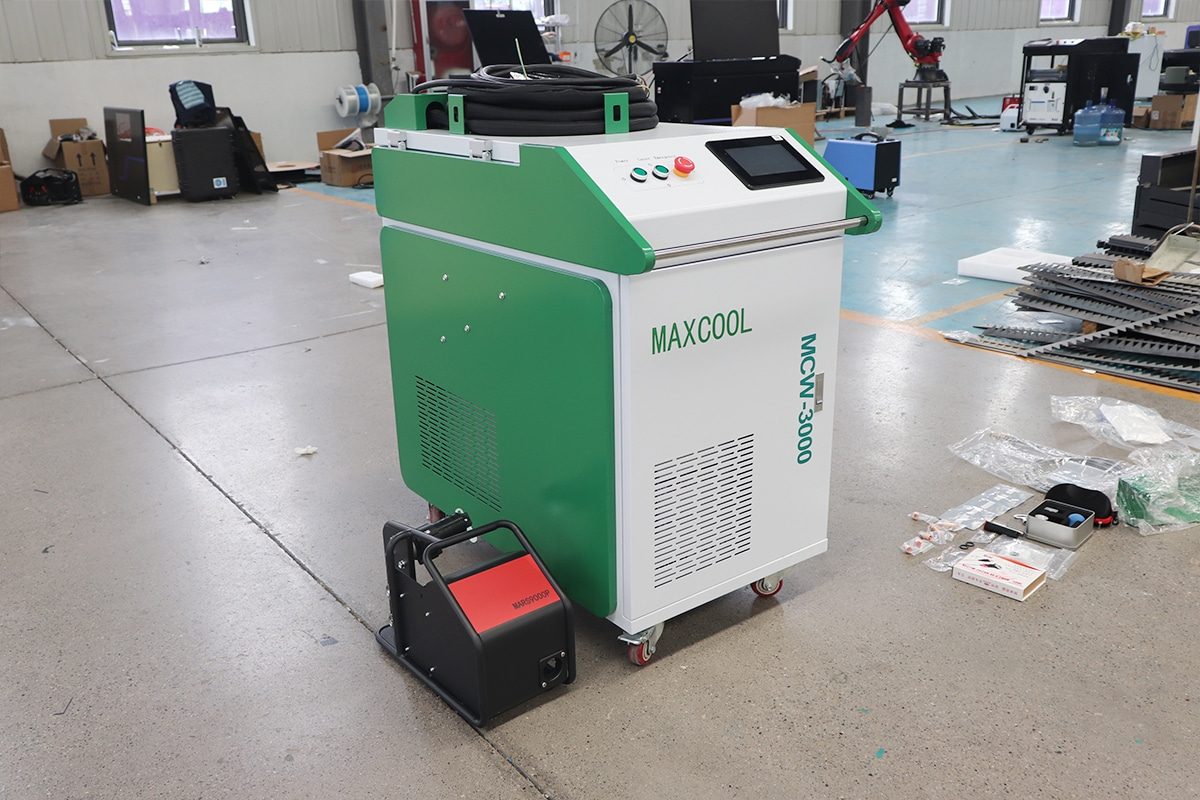
Laser Welding Defect Guide
Laser welding has emerged as a cornerstone of modern manufacturing, providing precision, speed, and high-quality results. It is a versatile process used in industries ranging from automotive and aerospace to medical device production. However, like all manufacturing processes, laser welding can experience defects that can undermine the quality and strength of the weld. Understanding the common laser welding defects, their causes, and their prevention is critical for improving production processes and ensuring the longevity and reliability of the final product.
This comprehensive guide aims to provide an in-depth understanding of laser welding defects, focusing on their description, causes, impacts, and strategies for prevention. Whether you are a laser welding technician, an engineer, or a manufacturer, this guide will serve as an invaluable resource for troubleshooting and optimizing your welding operations.
Table of Contents
Understanding Laser Welding
What is Laser Welding?
Laser welding is a high-precision welding process that uses a focused laser beam as the heat source to join materials, typically metals or thermoplastics. The intense energy of the laser melts the material at the joint, creating a strong bond when it solidifies. The process can be automated, providing high consistency and repeatability.
One of the defining features of laser welding is its ability to produce narrow, deep welds with minimal thermal distortion, making it ideal for applications where precision is paramount. It is also capable of welding thin or delicate materials that might be challenging with traditional welding methods.
Types of Laser Welding Processes
Laser welding can be divided into two primary modes: conduction welding mode and keyhole welding mode. Both modes use the same basic principle of using a laser to melt material, but they differ in the way the heat is applied and the resulting weld characteristics.
- Conduction Welding Mode: In conduction welding, the laser beam heats the surface of the material, causing it to melt and form a shallow molten pool. The process relies primarily on heat conduction from the surface to the underlying material. This mode is suitable for thin materials and provides good weld quality with minimal thermal distortion.
- Keyhole Welding Mode: Keyhole welding, also known as deep penetration welding, creates a deep, narrow melt pool. The laser beam penetrates through the material, forming a vapor cavity or “keyhole.” The keyhole mode is typically used for welding thicker materials and results in a stronger, more durable weld. This mode requires precise control of the laser parameters to avoid defects such as burn-through.
Applications of Laser Welding
Laser welding is used in a wide range of industries, including:
- Automotive: Laser welding is used to join parts in the manufacturing of vehicles, including body panels and critical structural components.
- Aerospace: Precision welding is vital for aerospace applications where weld integrity is critical for safety and performance.
- Medical Devices: Laser welding is used to create sterile, high-quality joints in medical instruments and implants.
- Electronics: Small, delicate components in electronics often require laser welding to ensure high precision and minimal thermal impact.
Common Laser Welding Defects
Laser welding defects can arise for a variety of reasons, including improper setup, poor material quality, or human error. Below is a detailed discussion of the most common defects encountered in laser welding, their causes, and the potential impacts on weld quality.
Porosity
- Description: Porosity refers to small holes or gas pockets trapped within the weld. These voids can appear on the surface or within the body of the weld.
- Causes: Porosity is primarily caused by the presence of gases trapped during the welding process. These gases can originate from contaminants on the material surface (such as moisture, oil, or dirt), from the material itself (like hydrogen or oxygen in the metal), or from the welding process itself. Improper shielding gas or insufficient gas flow can also lead to the formation of porosity.
- Impact: Porosity can weaken the weld, reducing its strength and durability. In critical applications, such as aerospace or medical devices, porosity can lead to premature failure of the welded parts. Additionally, excessive porosity can necessitate costly rework, further increasing production time and costs.
Cracking
- Description: Cracking occurs when the weld material or the surrounding base material fractures, leading to the formation of visible cracks.
- Causes: Cracking can occur due to several factors, including rapid cooling of the weld, improper selection of welding parameters (such as speed, power, or focus), or the presence of impurities in the base material. Another common cause is thermal stresses during cooling, especially when welding materials with different thermal expansion properties or thicknesses.
- Impact: Cracks can significantly compromise the structural integrity of the welded part, especially in high-stress environments. Cracking often leads to part failure, which can be catastrophic in critical applications such as aerospace or automotive manufacturing.
Undercuts
- Description: Undercuts are grooves or depressions formed along the edges of the weld. These grooves can appear when the laser beam melts the material too deeply, resulting in a weakened joint.
- Causes: Undercuts are usually caused by improper heat settings, such as too high a laser power or too fast a travel speed. A high power setting causes excessive melting, while a fast travel speed prevents the material from properly fusing, both of which can lead to undercuts.
- Impact: Undercuts weaken the weld, reducing its tensile strength and making it more prone to failure under stress. This defect is especially concerning for structural applications, where the integrity of the weld is crucial.
Excessive Spatter
- Description: Excessive spatter refers to small droplets of molten material that are ejected from the weld pool during the welding process.
- Causes: Spatter is often caused by excessive laser power or improper shielding gas flow. Too much power can cause the molten material to become turbulent, leading to ejection. Similarly, insufficient shielding gas can result in the formation of spatter as the weld pool is exposed to atmospheric gases.
- Impact: Spatter can affect the aesthetics of the weld, leaving unwanted material deposits around the weld area. It can also interfere with the functionality of the part, especially if the spatter is not cleaned off before further processing.
Incomplete Fusion
- Description: Incomplete fusion occurs when the base material and the weld metal fail to properly bond, resulting in weak areas within the weld joint.
- Causes: Incomplete fusion is often caused by insufficient laser power, improper welding speed, or a misaligned joint. When the heat input is too low or inconsistent, the weld metal may not melt enough to fuse properly with the base material.
- Impact: Incomplete fusion reduces the strength of the weld, making it more susceptible to failure. In high-stress environments, this can lead to catastrophic failure of the welded component.
Distortion
- Description: Distortion occurs when the welded material warps or bends due to uneven heating and cooling during the welding process.
- Causes: Distortion is primarily caused by uneven heat distribution during welding. When one area of the material heats and cools faster than another, it can cause the material to warp. This is often exacerbated by the thickness and type of material being welded.
- Impact: Distortion can affect the fit and function of the welded part, leading to misalignment or functional issues in the final assembly. In some cases, distortion may require additional rework to correct.
Surface Oxidation
- Description: Surface oxidation occurs when the weld area reacts with oxygen, forming an oxide layer on the surface of the material.
- Causes: Oxidation is typically caused by improper shielding gas or insufficient gas flow. When the shielding gas does not adequately protect the weld pool from atmospheric gases, oxygen can react with the molten material, causing oxidation.
- Impact: Oxidation can degrade the mechanical properties of the weld and reduce its corrosion resistance. In certain applications, oxidation may compromise the overall durability of the part.
Keyhole Defects
- Description: Keyhole defects occur when the laser beam penetrates too deeply into the material, creating an unstable vapor cavity or keyhole.
- Causes: Keyhole defects are usually caused by excessive laser power or improper control of the laser parameters. High laser power or slow travel speed can cause the laser to penetrate too deeply into the material, forming a keyhole that is difficult to stabilize.
- Impact: Keyhole defects can weaken the weld by creating voids and inconsistent fusion. This results in poor mechanical properties and a higher risk of failure under stress.
Excessive Reinforcement
- Description: Excessive reinforcement occurs when too much material accumulates above the base material, forming an undesirable bead or mound.
- Causes: Excessive reinforcement is typically caused by slow welding speed or too high a laser power. When the laser stays on the same spot for too long or applies too much heat, it melts too much material, leading to excess reinforcement.
- Impact: Excessive reinforcement increases the weight and volume of the weld, which may not be desirable in certain applications. It may also require additional machining or finishing work to remove excess material.
Burn Through
- Description: Burn-through occurs when the laser beam penetrates completely through the material, leaving a hole in the weld.
- Causes: Burn-through is usually caused by too much laser power, too slow a welding speed, or the use of thin materials. Excessive heat input can cause the material to melt all the way through, creating an unwanted hole.
- Impact: Burn-through creates holes in the material, weakening the weld and often rendering the part unusable. In critical applications, burn-through can lead to part failure and costly rework.
Oxidation
- Description: Oxidation is a process where oxygen reacts with the weld material, forming an oxide layer on the surface.
- Causes: Oxidation can occur due to insufficient shielding gas, environmental contamination, or high ambient oxygen levels. It is exacerbated by high temperatures and poor gas flow during the welding process.
- Impact: Oxidation can reduce the mechanical properties of the weld, leading to corrosion, poor fatigue resistance, and eventual part failure. In some cases, it may also affect the appearance of the welded part.
Causes of Laser Welding Defects
Laser welding defects can arise due to a variety of factors, including improper machine setup, material issues, or environmental influences. Below are the primary causes of laser welding defects:
- Improper Laser Parameters: Inadequate control of laser parameters—such as power, speed, and focus—can lead to numerous welding defects, including porosity, cracking, and burn-through. Ensuring optimal laser settings for each specific welding job is critical to preventing these issues.
- Material Issues: The type, quality, and condition of the material being welded significantly impact the success of the laser welding process. Contaminants, surface oxidation, and material inconsistencies can introduce defects.
- Shielding Gas Problems: Inadequate shielding gas flow or improper gas composition can lead to oxidation, porosity, and other defects. Proper shielding gas management is essential to protect the weld pool from atmospheric contamination.
- Improper Joint Fit-Up: Misalignment of the joint or poor fit-up can cause incomplete fusion, distortion, or cracking. Ensuring precise alignment of the parts being welded is vital for defect-free welds.
- Equipment Malfunction: Malfunctions in welding equipment, such as misalignment of the laser beam or cooling system issues, can lead to defects in the weld.
- Environmental Factors: External factors such as drafts, humidity, or contamination in the welding environment can influence the quality of the weld. A controlled environment is crucial for consistent results.
- Operator Skill and Experience: Operator skill plays a significant role in the success of laser welding. Inexperienced operators may fail to properly adjust machine settings, monitor weld quality, or handle complex welding tasks, resulting in defects.
Prevention of Laser Welding Defects
Preventing laser welding defects requires careful attention to several key aspects of the process. By addressing the causes of defects proactively, manufacturers can achieve higher-quality welds and reduce rework.
- Proper Machine Setup and Calibration: Regular machine calibration and proper setup are essential for ensuring consistent weld quality. This includes verifying the laser’s power, focus, and beam alignment.
- Optimizing Laser Parameters: Using the correct laser power, speed, and focus for the material and joint type is crucial. Experimenting with different parameters and conducting tests can help optimize the welding process.
- Material Preparation: Materials should be thoroughly cleaned to remove contaminants such as oils, rust, or oxidation. Preheating the material can also help prevent cracking and improve weld quality.
- Joint Design and Fit-Up: Ensuring proper joint alignment and fit-up minimizes the risk of defects like incomplete fusion or distortion. The joint design should facilitate effective heat transfer and melt pool formation.
- Effective Shielding Gas Management: Proper shielding gas selection and flow rates are essential for protecting the weld pool from atmospheric contamination and preventing oxidation and porosity.
- Training and Operator Skills: Training operators on best practices for laser welding and ensuring they understand the nuances of different welding scenarios can greatly reduce the risk of defects.
- Regular Maintenance of Equipment: Routine maintenance and inspection of welding equipment, including the laser and cooling systems, help prevent equipment-related defects. Regular checks can identify issues before they affect the weld quality.
Summary
Laser welding is a highly efficient and precise method for joining materials, but like any manufacturing process, it is susceptible to defects. Understanding these defects, their causes, and their impacts is essential for achieving high-quality welds. By optimizing machine settings, ensuring proper material preparation, and training operators, manufacturers can minimize defects and improve weld quality.
This guide has provided a comprehensive overview of common laser welding defects, their causes, and strategies for prevention. By implementing these best practices, you can ensure the success of your laser welding operations and produce high-quality, defect-free parts.
Get Laser Welding Solutions
When facing challenges with laser welding defects, it’s crucial to seek reliable and expert solutions to ensure high-quality, precise, and durable welds. Maxcool CNC offers cutting-edge laser welding machines designed to optimize performance, reduce defects, and enhance overall welding quality. By selecting the right equipment tailored to your specific needs, such as machines with adjustable parameters for power, speed, and focus, you can prevent common welding issues such as porosity, cracking, and incomplete fusion.
Maxcool CNC also provides comprehensive technical support, including guidance on optimal machine setup, training on operator skills, and assistance in troubleshooting welding defects. With years of experience and innovation, Maxcool CNC ensures that your laser welding operations run efficiently, minimizing rework and material wastage. For those looking to address laser welding defects comprehensively, Maxcool CNC’s solutions promise advanced technology, expert consultation, and a commitment to delivering the highest standards of quality in laser welding.