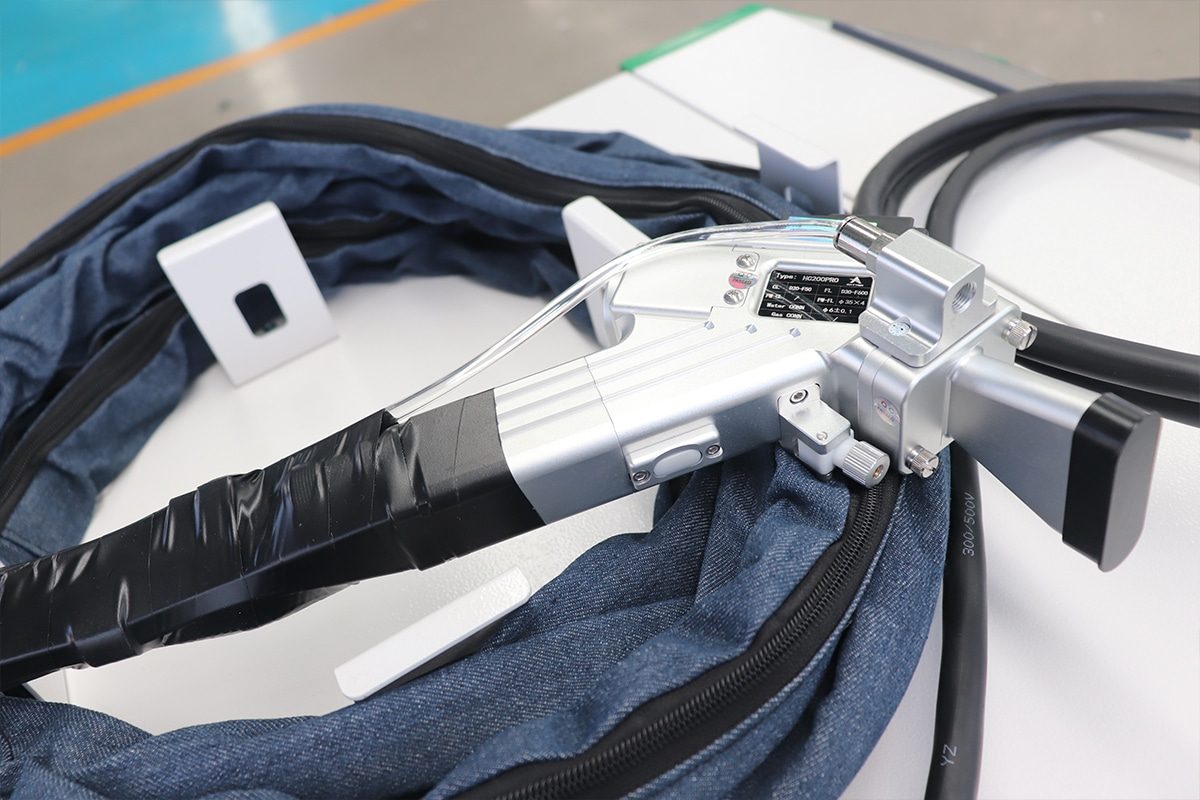
Laser Rust Removal VS Sandblasting Rust Removal
Rust removal plays a crucial role in maintaining the quality, performance, and safety of metal components across various industries. Over time, exposure to moisture and oxygen causes metal surfaces to develop rust, weakening their structural integrity and diminishing their visual appeal. Traditionally, sandblasting has been the preferred method for rust removal, known for its effectiveness in cleaning surfaces through abrasive impact. However, with advancements in laser technology, laser rust removal has emerged as an innovative, non-contact alternative that offers greater precision and environmental benefits.
Choosing the right rust removal method depends on multiple factors, including the type of metal, the complexity of the surface, environmental considerations, and long-term operational costs. This article provides a detailed comparison of laser rust removal and sandblasting, examining their strengths, limitations, safety implications, and practical applications. By understanding the differences between these two techniques, industries can make informed decisions about the best approach for their specific needs.
Table of Contents
Understanding Rust and Its Impact
What Is Rust?
Rust is a form of corrosion that occurs when iron or its alloys, such as steel, come into contact with oxygen and moisture, triggering an electrochemical reaction. This reaction produces iron oxide, commonly recognized as rust, which appears as a reddish-brown, flaky layer on metal surfaces. The process of rusting accelerates in environments with high humidity, salty air, or water exposure, making it a significant challenge for industries relying on metal structures and equipment. Rust not only deteriorates the surface of metals but also causes progressive damage if not addressed in time.
Effects of Rust on Metals and Structures
The presence of rust can have serious consequences for both the appearance and functionality of metal objects. Key effects include:
- Structural Weakening: Rust penetrates metal surfaces, creating cracks and weakening the material’s structural integrity. This is especially dangerous for load-bearing structures like bridges and pipelines.
- Decreased Efficiency: In mechanical systems, rust increases friction between moving parts, leading to wear, energy losses, and reduced performance.
- Surface Damage: Rust flakes and peels, compromising the material’s protective coatings, which accelerates further corrosion.
- Aesthetic Degradation: Rusty surfaces appear unsightly, which affects the market value of consumer products and equipment.
- Safety Risks: Unchecked rust on critical infrastructure can lead to failures, posing risks to human safety and costly repairs or replacements.
Importance of Timely and Effective Rust Removal
Proactive rust removal avoids the high costs and safety risks associated with corroding metals. Timely rust removal ensures:
- Longer Equipment Lifespan: Preventing further corrosion extends the service life of machinery, tools, and infrastructure.
- Enhanced Performance: Removing rust restores the smooth operation of components, reducing downtime and maintenance costs.
- Structural Integrity: Routine rust removal protects vital structures from collapse and ensures compliance with safety standards.
- Environmental Protection: Regular maintenance helps prevent hazardous structural failures, such as leaking pipes or damaged storage tanks, which can cause environmental contamination.
- Cost Savings: Early intervention reduces the need for expensive repairs, replacements, or complete overhauls of corroded assets.
Both sandblasting and laser rust removal play a critical role in managing rust effectively. The right rust removal method can prevent structural degradation, increase efficiency, and maintain safety and aesthetics, making it an essential part of asset management across industries.
Sandblasting Rust Removal
What Is Sandblasting?
Sandblasting, also known as abrasive blasting, is a surface cleaning method that involves propelling abrasive materials at high speed onto a metal surface to remove rust, paint, scale, or other contaminants. The process relies on the kinetic energy of abrasive particles, which erode and strip away unwanted layers, revealing the bare metal underneath. Sandblasting has been widely used across industries such as construction, automotive restoration, shipbuilding, and manufacturing due to its ability to handle large surfaces efficiently.
How Sandblasting Works
Sandblasting involves the use of compressed air or centrifugal force to accelerate abrasive particles, directing them through a nozzle onto the rusted surface. The high-impact contact removes rust by chipping away at the corroded material layer by layer. Operators can adjust the air pressure, abrasive type, and blasting angle to optimize results based on the surface material and the extent of corrosion. The process works well on flat or curved surfaces, although complex or delicate objects may require more controlled methods.
Equipment Used in Sandblasting
- Air Compressor: Provides the necessary compressed air to drive the abrasive particles.
- Blast Pot (Abrasive Tank): Stores and feeds the abrasive material into the air stream.
- Blasting Hose and Nozzle: Directs the flow of abrasives onto the target surface. Different nozzle sizes allow for better control over the blasting process.
- Abrasive Media: Common materials include sand, steel grit, glass beads, aluminum oxide, and plastic particles, selected based on the type of metal and cleaning requirements.
- Protective Gear: Due to the dust and airborne contaminants generated, operators wear helmets, respirators, gloves, and protective clothing to safeguard against health risks.
Advantages of Sandblasting
- Effective for Heavy-Duty Applications: Sandblasting is highly efficient at removing thick rust, paint, and heavy contaminants, making it suitable for large industrial projects.
- Versatile: Works well on various surfaces, including steel, iron, concrete, and wood, and can prepare surfaces for painting or coating.
- Surface Preparation: It creates a textured surface that improves the adhesion of paints, primers, or coatings, ensuring long-lasting protection.
- Quick Process: Sandblasting is relatively fast, especially for large surfaces, reducing downtime during maintenance.
- Cost-Effective for Basic Needs: With relatively simple equipment and a wide selection of abrasive media, sandblasting offers an economical option for many businesses.
Limitations and Drawbacks of Sandblasting
- Health Hazards: The abrasive materials generate dust and airborne particles that can cause respiratory issues, such as silicosis if operators are not adequately protected.
- Environmental Concerns: Sandblasting produces significant waste, including spent abrasive materials and dust, which must be disposed of properly to avoid environmental contamination.
- Surface Damage Risks: High-intensity blasting can erode not only the rust but also the underlying metal, compromising the surface integrity, especially on thin or delicate materials.
- Limited Precision: While effective for large and uniform surfaces, sandblasting lacks the precision required for intricate or complex components.
- Setup and Cleanup Requirements: The equipment setup is extensive, and the post-blasting cleanup process can be labor-intensive due to residual media and dust.
- Regulatory Compliance: Many regions have strict regulations governing the use of certain abrasive media, especially silica-based materials, which can complicate the process.
Sandblasting remains a powerful tool for rust removal, particularly in applications requiring rapid, large-scale cleaning. However, the method’s environmental impact, health risks, and limitations in handling precision work mean that it is often best suited for rugged, outdoor applications or heavy-duty cleaning tasks.
Laser Rust Removal
What Is Laser Rust Removal?
Laser rust removal is an advanced surface cleaning technique that uses high-energy laser beams to remove rust, paint, and other contaminants from metal surfaces without direct contact. This method employs focused laser pulses to evaporate or ablate rust, leaving the underlying metal surface clean and intact. Unlike traditional abrasive techniques like sandblasting, laser rust removal is precise, non-invasive, and generates minimal waste, making it a preferred choice for modern industries focused on efficiency and sustainability.
How Laser Rust Removal Works
Laser rust removal works through a process known as laser ablation. When the laser beam strikes the rusted surface, the rust absorbs the high-intensity light energy, which causes it to heat rapidly and vaporize. The laser’s energy is carefully controlled to ensure it removes only the rust, leaving the base material unaffected. Since metals reflect most of the laser’s energy, they remain largely unharmed, even after multiple cleaning cycles. The laser can be adjusted for different rust levels and surface types, ensuring optimal cleaning results.
In continuous laser systems, the beam stays active for high-speed cleaning, while pulsed lasers deliver rapid bursts of energy suitable for precision work. Laser rust removal is effective on flat, curved, or complex surfaces, including intricate components that are challenging for abrasive cleaning methods.
Equipment Used in Laser Rust Removal
- Laser Source: Typically a fiber laser, which offers excellent precision and reliability. Depending on the task, continuous or pulsed laser sources are used.
- Beam Delivery System: Includes optics, scanners, and focusing lenses that guide and shape the laser beam for precise targeting.
- Control Unit: Manages laser power, pulse frequency, and beam direction, ensuring efficient and safe operation.
- Cooling System: Regulates the temperature of the laser unit, preventing overheating during extended use.
- Safety Enclosure and Gear: Operators use protective eyewear and follow safety protocols to prevent exposure to laser radiation.
- Portable or Robotic Platforms: Laser rust removal systems can be handheld for on-site tasks or mounted on robotic arms for automated applications.
Advantages of Laser Rust Removal
- Non-Abrasive and Non-Contact: Since no abrasive materials are used, laser rust removal preserves the surface integrity of the metal, avoiding any erosion or surface deformation.
- Precision and Control: Laser beams can be finely tuned for selective rust removal, making this method ideal for intricate components, delicate objects, or areas with complex geometries.
- Minimal Waste Production: Laser cleaning produces minimal waste, mainly in the form of fumes that can be captured using ventilation systems, making it an environmentally friendly option.
- Increased Safety: The absence of dust and abrasive particles reduces health risks, and safety enclosures ensure operator protection from laser radiation.
- Low Maintenance and Operational Costs: Laser systems have fewer consumables, such as abrasives or chemicals, and require minimal maintenance, leading to lower long-term operational expenses.
- Automation-Friendly: Laser systems are easily integrated into automated workflows using robotic arms, enhancing efficiency in industrial processes.
- Versatility: Laser rust removal is suitable for a wide range of industries, including aerospace, electronics, manufacturing, automotive restoration, and cultural artifact preservation.
Limitations and Considerations of Laser Rust Removal
- High Initial Investment: Laser rust removal equipment can be expensive to acquire, which may be a barrier for smaller businesses. However, the long-term savings often justify the investment.
- Training Requirements: Operators need specialized training to use laser cleaning systems safely and effectively.
- Power Consumption: High-powered laser systems may have significant energy demands, which can impact operational costs.
- Slower for Large Surfaces: While highly effective for small and complex parts, laser rust removal can be slower than sandblasting for large-scale cleaning tasks.
- Material Compatibility: Although ideal for metal surfaces, laser rust removal may not be effective on non-metallic surfaces or rust mixed with certain coatings that do not absorb laser energy efficiently.
- Upfront Safety Measures: Proper laser enclosures and safety protocols must be in place to prevent accidental exposure to laser radiation.
Laser rust removal offers a cutting-edge solution for precision cleaning, delivering unmatched control and eco-friendliness. Although it requires a higher initial investment and specialized training, the benefits—such as minimal waste, material preservation, and easy automation—make it an increasingly popular choice for industries looking to modernize their rust removal processes.
Comparative Analysis
Efficiency and Effectiveness
- Sandblasting: Sandblasting is highly effective for removing heavy rust, paint, and thick contaminants from large surfaces. It works quickly on extensive areas, but multiple passes may be required for deeply embedded rust. Its abrasive nature makes it ideal for heavy-duty cleaning, though it may struggle with precise applications or delicate components.
- Laser Rust Removal: Laser rust removal offers excellent precision and control, making it more efficient for smaller, intricate parts and surfaces with complex geometries. It is particularly effective for selective rust removal without affecting the underlying metal. Although it may be slower for large-scale projects compared to sandblasting, laser cleaning is consistent and precise with minimal need for rework.
Cost Considerations
- Sandblasting: The initial cost of sandblasting equipment is relatively low, and abrasive materials are widely available. However, ongoing expenses for consumables (abrasive media), labor, and waste disposal can accumulate, increasing long-term operational costs.
- Laser Rust Removal: Laser rust removal systems involve higher upfront costs due to the advanced equipment required. However, these systems have low maintenance needs and minimal operational costs, as they do not require consumables. Over time, the reduced need for labor and rework makes laser cleaning a cost-effective solution, especially for frequent or high-precision tasks.
Environmental Impact
- Sandblasting: Sandblasting generates significant waste, including spent abrasive material and dust. The process can contribute to air pollution and environmental contamination if waste is not properly managed. Some abrasive materials, such as silica, are associated with environmental hazards and regulatory restrictions.
- Laser Rust Removal: Laser rust removal is environmentally friendly, producing minimal waste, typically limited to fumes and particles that can be captured using filters or ventilation systems. It eliminates the need for harmful chemicals or abrasive materials, reducing the ecological footprint. This makes laser cleaning an ideal option for industries with strict environmental regulations.
Safety and Health Implications
- Sandblasting: Sandblasting poses serious health risks, such as respiratory issues caused by inhaling dust and fine particles, including the potential for silicosis. Operators must wear extensive protective gear, including respirators, to minimize exposure. There is also a risk of abrasive material ricocheting, causing physical injuries.
- Laser Rust Removal: Laser cleaning is generally safer when proper precautions are taken. Since it produces minimal airborne particles, it reduces the risk of respiratory hazards. However, laser systems require strict safety protocols to prevent accidental exposure to laser radiation. Operators must wear protective eyewear, and enclosed workspaces are recommended to ensure safety.
Surface Integrity and Quality
- Sandblasting: While effective at rust removal, sandblasting can also erode the base metal, causing surface roughness or damage. It may not be suitable for delicate components, as it can compromise surface quality and dimensional accuracy.
- Laser Rust Removal: Laser rust removal is non-contact and non-abrasive, preserving the base material and ensuring no surface deformation. It is ideal for precision cleaning of delicate or intricate parts, maintaining the surface integrity and quality. This makes it a superior choice for applications requiring fine detailing or minimal surface disturbance.
Versatility and Adaptability
- Sandblasting: Sandblasting is versatile and can be applied to various surfaces, including metal, concrete, and wood. However, it is less adaptable to intricate geometries, confined spaces, or delicate components. The method is best suited for large, open areas and heavy-duty cleaning tasks.
- Laser Rust Removal: Laser rust removal is highly adaptable and can clean intricate surfaces, hard-to-reach areas, and components with complex geometries. It can be used on a range of metals and alloys, making it suitable for precision industries such as aerospace, electronics, and automotive restoration. Laser systems can also be automated, improving productivity in manufacturing environments.
Both sandblasting and laser rust removal have their advantages and limitations, with each method suited to specific applications. Sandblasting excels in heavy-duty, large-scale cleaning tasks but comes with environmental and safety drawbacks. In contrast, laser rust removal offers unparalleled precision, safety, and sustainability, making it the better choice for delicate parts and high-precision applications. For industries focused on automation, safety, and long-term cost savings, laser rust removal is an increasingly attractive solution.
Applications and Industries
Industries Where Sandblasting Is Commonly Used
- Construction and Infrastructure: Sandblasting is extensively used in construction to clean steel frameworks, bridges, and pipelines. It helps remove rust, paint, and other debris to prepare surfaces for protective coatings or welding. Its ability to clean large surfaces efficiently makes it essential for infrastructure projects.
- Shipbuilding and Marine Industry: Sandblasting is critical for removing rust, barnacles, and old paint from ship hulls and marine equipment. It ensures proper surface preparation for anti-corrosion coatings, extending the lifespan of ships and preventing structural damage caused by seawater exposure.
- Automotive and Vehicle Restoration: Automotive workshops use sandblasting to remove rust, paint, and grime from car bodies and parts. It prepares vehicles for repainting or restoration, making it a popular choice for refurbishing classic and vintage cars.
- Manufacturing and Fabrication: In metal fabrication, sandblasting is used to clean metal parts before assembly, welding, or coating. It ensures a clean surface free of contaminants, enhancing the adhesion of protective layers and paints.
- Oil and Gas Industry: Sandblasting is vital for cleaning and maintaining pipelines, drilling rigs, and storage tanks. The abrasive cleaning process ensures metal components are free from rust and corrosion, minimizing the risk of leaks and equipment failures.
Industries Adopting Laser Rust Removal
- Aerospace and Aviation: Precision is critical in aerospace manufacturing and maintenance. Laser rust removal is ideal for cleaning delicate aircraft parts without damaging the surface or affecting dimensional accuracy. Its non-abrasive nature ensures compliance with stringent safety and quality standards.
- Automotive Industry: Automotive manufacturers are increasingly adopting laser rust removal to clean engine components, metal panels, and intricate parts. The precision of laser cleaning ensures thorough rust removal without eroding the metal, making it suitable for modern production lines.
- Electronics and Semiconductor Manufacturing: Laser rust removal is highly effective in cleaning delicate electronic components where precision and control are paramount. It eliminates rust and contaminants from metal connectors and circuits without causing physical damage, ensuring reliable performance.
- Cultural Heritage and Art Restoration: Museums and restoration experts use laser rust removal to clean historical artifacts, sculptures, and paintings. The controlled laser beam removes corrosion and contaminants without harming the original material, preserving the cultural value of artifacts.
- Energy and Renewable Sector: Wind turbines, solar panel mounts, and other energy infrastructure components often require rust removal for maintenance. Laser rust removal offers an eco-friendly solution that minimizes waste and extends the lifespan of critical components.
- Medical Device Manufacturing: Laser cleaning is gaining popularity in the medical field for rust removal from stainless steel instruments and implants. Its precision and cleanliness ensure compliance with medical industry standards and prevent surface contamination.
Laser rust removal and sandblasting serve distinct roles across various industries. Sandblasting remains effective for heavy-duty applications that involve large surfaces and robust structures, while laser rust removal shines in precision cleaning tasks where surface preservation is critical. As industries prioritize sustainability, automation, and precision, laser rust removal is becoming the preferred solution, delivering safer and more efficient results.
Summary
Both laser rust removal and sandblasting are effective rust removal techniques, but they serve different needs and industries. Sandblasting excels in heavy-duty applications, such as large-scale construction, shipbuilding, and automotive restoration, where fast cleaning of extensive surfaces is required. It is cost-effective for basic rust removal but carries health risks, generates significant waste, and may damage delicate materials.
Laser rust removal, on the other hand, offers unmatched precision, making it ideal for intricate components and high-value industries like aerospace, electronics, and automotive manufacturing. It is a non-contact, environmentally friendly solution that preserves surface integrity and reduces operational hazards. While laser cleaning requires a higher initial investment, it offers long-term savings with minimal maintenance and consumables. As industries increasingly focus on precision, sustainability, and safety, laser rust removal is becoming the preferred option.
Get Laser Rust Removal Solutions
If you are looking for a modern, efficient, and eco-friendly rust removal solution, Maxcool CNC offers state-of-the-art laser cleaning machines designed to meet the needs of various industries. As a professional manufacturer of laser welding and laser cleaning machines, Maxcool CNC provides reliable equipment with advanced technology to ensure precise, non-contact rust removal. Our laser rust removal systems are built for long-term performance, offering minimal maintenance, low operational costs, and easy integration into automated workflows.
Whether you need handheld laser cleaning devices for on-site tasks or automated systems for industrial production, Maxcool CNC’s laser solutions deliver unparalleled accuracy, safety, and sustainability. Our machines are ideal for industries like aerospace, automotive, electronics, and cultural preservation, where surface integrity and precision are critical.
Contact Maxcool CNC today to learn more about how our advanced laser cleaning systems can enhance your operations. Our expert team is ready to assist you in selecting the right solution and providing full technical support from installation to operation.