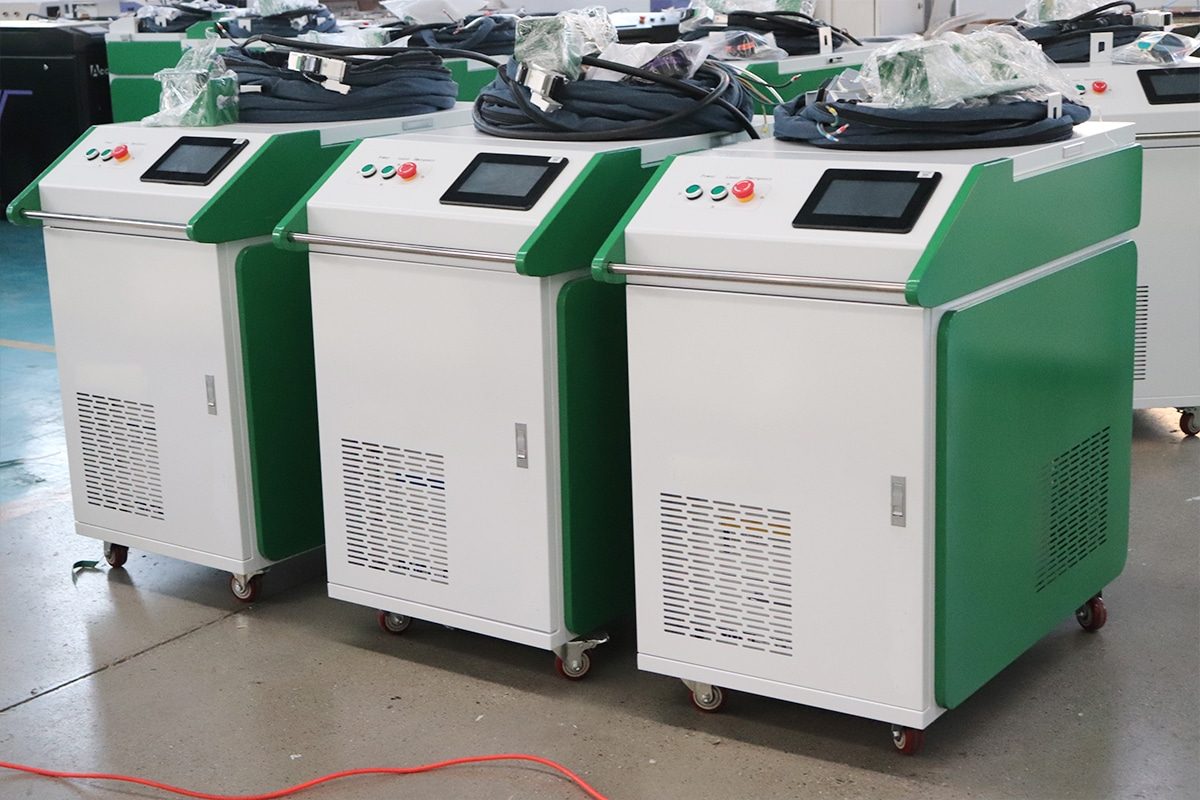
Understanding Rust and Corrosion
The Formation of Rust
Rust primarily appears when iron (or alloys containing iron) reacts with oxygen and moisture. This electrochemical reaction proceeds as follows:
- Oxidation (Anodic Reaction): Iron atoms lose electrons and form positively charged iron ions.
- Reduction (Cathodic Reaction): Oxygen in the presence of water gains these electrons, producing hydroxide ions.
- Iron Oxides: The iron ions and hydroxide ions combine, eventually converting into iron oxides—commonly recognized as rust.
Impact on Materials and Structures
The presence of rust can have far-reaching consequences, extending well beyond surface discoloration:
- Structural Weakening: Rusted metal loses strength and can develop cracks or flakes, potentially leading to mechanical failure in load-bearing components like bridges, pipelines, and steel frames.
- Safety Concerns: Corroded elements in machinery or vehicles can result in hazardous conditions, including system malfunctions, leaks, or compromised structural stability.
- Economic Costs: Fixing or replacing rusted parts and dealing with downtime are expensive. Over time, cumulative maintenance and repair costs can be significant, especially for large-scale industrial or infrastructural assets.
- Damage to Historical Artifacts: In heritage conservation, rust can obscure or destroy intricate features and degrade the historical value of metal artifacts, requiring specialized methods to carefully remove corrosion without harming the underlying material.
Overview of Rust Removal Methods
Mechanical Abrasion
Chemical Treatments
Electrochemical Techniques
Thermal Methods
Laser Cleaning
Laser Rust Removal
Principles of Laser Cleaning
Laser rust removal hinges on the principle of selective absorption and rapid heating. A focused laser beam with appropriate power and wavelength is directed onto the corroded surface:
- Photon Absorption: Rust typically absorbs the laser’s energy more readily than the underlying metal.
- Rapid Heating and Ablation: The absorbed energy vaporizes or loosens the rust, causing it to flake off or sublimate away.
- Minimal Substrate Damage: With proper parameter tuning, the laser removes oxidation layers while leaving the base metal largely intact.
Types of Lasers Used for Rust Removal
CW Fiber Laser
Characteristics:
- Consistent energy output over time.
- Suitable for situations demanding uniform energy distribution.
- Tends to heat the substrate more, which can be managed through beam defocusing and controlled scan speed.
Pros and Cons:
- Pros: Simpler construction, lower cost compared to high-end pulsed lasers, and easy integration with robotic systems.
- Cons: May pose a higher risk of thermal damage if not carefully controlled, making it less ideal for extremely delicate or heat-sensitive items.
Pulse Fiber Laser
Characteristics:
- Pulse durations can range from nanoseconds to microseconds.
- High peak power enables effective ablation with minimal thermal conduction into the substrate.
Pros and Cons:
- Pros: Minimizes heat transfer to the metal, leading to lower substrate damage and a more precise cleaning action.
- Cons: Generally higher initial cost, and slightly more complex control systems compared to CW lasers.
Process and Equipment
A typical laser rust removal setup includes:
- Laser Source: Generates the beam, commonly a fiber laser for industrial or restoration applications.
- Beam Delivery System: May use fiber-optic cables and galvanometer mirrors (galvos) to scan the laser beam rapidly across the surface.
- Cooling Unit: Ensures the laser operates at optimal temperatures.
- Control Software: Allows operators to adjust pulse frequency, power output, and scanning speed.
- Dust or Fume Extraction: Collects debris and prevents inhalation of vaporized rust particles.
Advantages of Laser Rust Removal
- Precision and Non-Contact: The process does not physically touch the workpiece, preserving delicate features.
- Minimal Residue: No harsh chemicals or abrasives are required, reducing secondary cleanup.
- Selective Removal: Laser settings can target rust or specific coatings without damaging the substrate.
- Scalable and Automated: Robotic integration makes it feasible for high-volume industrial operations.
- Eco-Friendliness: Eliminates or significantly reduces chemical waste compared to many traditional methods.
Disadvantages and Limitations
- High Initial Cost: Industrial laser systems can be expensive, potentially limiting accessibility for smaller workshops.
- Safety Requirements: Operators must use protective eyewear and other precautions to guard against intense laser beams and fume hazards.
- Energy Consumption: High-power lasers can draw substantial electricity.
- Limitations with Complex Geometry: Hard-to-reach internal or recessed areas may require repositioning or specialized optics.
Typical Applications
- Industrial Pretreatment: Automotive, aerospace, and marine industries use lasers to remove rust before welding, painting, or bonding.
- Heritage Conservation: Museums and restoration workshops benefit from the non-abrasive, low-distortion nature of laser cleaning.
- Precision Component Cleaning: High-value machined parts can be cleaned thoroughly without risking surface deformation.
- Batch Processing: Automated lines can handle large volumes of rusted parts in a cost-effective, repeatable manner.
Safety Considerations
Using lasers for rust removal necessitates rigorous safety measures:
- Laser Classification and Shielding: Enclosures or barriers are often required to contain scattered or reflected beams.
- Protective Eyewear: Must be specifically rated for the laser’s operating wavelength.
- Ventilation and Extraction: Crucial for removing hazardous fumes and dust generated during ablation.
- Training and Certification: Operators need thorough instruction in safe laser operation, beam path control, and emergency shutdown procedures.
Electrolytic Rust Removal
Chemistry of Electrolytic Cleaning
At the heart of electrolysis for rust removal lies an electrochemical reaction in an alkaline solution—commonly prepared by dissolving washing soda (sodium carbonate) or baking soda (sodium bicarbonate) in water. The rusted item acts as the cathode (negative electrode), while a separate piece of metal, typically steel, serves as the anode (positive electrode). When a direct current is applied:
- Reduction at the Cathode: Rust (iron oxide) gains electrons, which can convert some of it back to iron or loosen the oxide layer.
- Oxidation at the Anode: The anode may corrode, forming oxides or releasing metal ions into the solution.
- Sludge and Flaking: Loosened rust detaches from the surface, accumulating as residue or sludge in the bath.
Equipment and Setup
A basic electrolytic setup includes:
- Container: A non-conductive vessel (e.g., plastic bucket) large enough to immerse the rusted item.
- Electrolyte Solution: Water mixed with sodium carbonate or sodium bicarbonate.
- Anode: A piece of iron or mild steel. (Stainless steel is sometimes used but can introduce environmental and health concerns due to potential chromium release.)
- DC Power Supply: A battery charger or adjustable power source capable of delivering low voltages (6–12V is typical).
- Suspension Method: Wires or clips to hold the object in place without direct contact with the anode.
Process Description
- Preparation: Clean the workpiece to remove grease or dirt.
- Immersion: Place both the rusted item (connected to the negative terminal) and the anode (connected to the positive terminal) in the electrolyte, ensuring they do not touch.
- Power Application: Switch on the power supply at a suitable voltage. Bubbles of hydrogen (at the cathode) and oxygen (at the anode) indicate electrolysis is in progress.
- Monitoring: The rust gradually loosens and may require occasional brushing. More heavily rusted items might need extended treatment or multiple sessions.
- Rinsing and Drying: After the process, thoroughly rinse and dry the workpiece to prevent flash rusting, then apply protective coatings if desired.
Advantages of Electrolytic Rust Removal
- Low Cost and Accessible: A straightforward setup of basic household items and a power supply makes it ideal for hobbyists.
- Preserves Detail: Less risk of aggressive metal removal, beneficial for historical artifacts or intricate parts.
- Environmentally Mild: Alkaline solutions are generally safer to handle than strong acids, provided spent solutions are disposed of responsibly.
- Deep Cleaning: Crevices and internal cavities can be reached, as the process is not limited by line-of-sight.
Disadvantages and Limitations
- Time-Consuming: Severely rusted objects may require long soak times, sometimes multiple days.
- Size Constraints: The immersion container must accommodate the entire part, and larger setups can become unwieldy.
- Sludge and Disposal: The electrolyte becomes contaminated with rust particles and, if stainless steel anodes are used, potentially hazardous metals.
- Risk of Over-Cleaning: Excessive voltage or prolonged treatment may damage metal surfaces if not carefully monitored.
Typical Applications
- Antique Tools and Hardware: Wrenches, knives, and machine parts that need gentle restoration.
- Historic and Archaeological Artifacts: Museum conservators employ electrolysis to preserve original detail without harsh abrasion.
- Hobbyist Restoration: Automotive components or household metal items that require low-cost, do-it-yourself rust removal.
Safety Considerations
Although relatively simple, electrolytic rust removal still demands caution:
- Hydrogen Gas: The cathode releases hydrogen, requiring proper ventilation to avoid buildup.
- Electrical Hazards: Water and electricity can be dangerous if mishandled; using a grounded outlet and a GFCI (Ground-Fault Circuit Interrupter) is advisable.
- Chemical Disposal: Spent solutions, particularly those containing metals from the anode, should be disposed of by local regulations.
- Personal Protective Equipment (PPE): Gloves and goggles are recommended to prevent exposure to alkaline solutions and rust residues.
Comparative Analysis
Effectiveness in Removing Rust
- Laser Rust Removal: Highly effective, particularly with well-tuned parameters such as beam intensity, pulse duration (if pulsed), and scanning speed. Thick or heavily layered rust might require multiple passes but can be removed thoroughly without damaging the substrate.
- Electrolytic Rust Removal: Also effective but generally slower. Electrolysis often loosens rust and may convert some of it back to iron. In certain cases, residual rust or a black film remains and requires light brushing or polishing afterward.
Speed and Efficiency
- Laser Rust Removal: Often faster, particularly with high-power lasers capable of ablating extensive rust quickly. Ideal for industrial settings that need a rapid turnover.
- Electrolytic Rust Removal: This can take hours or days, depending on rust severity and the capacity of the setup. It requires minimal operator intervention but is not well-suited to high-volume, time-sensitive applications.
Equipment Cost and Operational Expenses
- Laser Rust Removal: Initial investment for an industrial-grade system can be substantial, ranging from tens of thousands to hundreds of thousands of dollars. Operational costs include electricity, cooling, and maintenance of optics, though consumables (e.g., chemicals) are minimal.
- Electrolytic Rust Removal: Requires a simple DC power source, a container, and a basic electrolyte (often sodium carbonate). The overall cost is relatively low, making it attractive to individual hobbyists or small businesses.
Safety
- Laser Rust Removal: High-power lasers pose hazards such as eye injury, skin burns, and inhalation of vaporized particles. Proper training, safety goggles rated for the specific laser wavelength, and fume extraction are vital.
- Electrolytic Rust Removal: Generates hydrogen gas at the cathode and oxygen at the anode. Adequate ventilation is necessary to prevent gas buildup. Electrical safety measures are also critical, as water and electricity can be dangerous if mishandled.
Environmental Impact
- Laser Rust Removal: No chemical solutions are needed, reducing environmental waste. The main byproducts are dust and fumes, which must be filtered or captured. Energy consumption may be significant, depending on laser power and usage duration.
- Electrolytic Rust Removal: This relies on mild alkaline solutions and can release metal ions into the solution. Disposal must adhere to local guidelines, especially if using stainless steel anodes (which may introduce chromium compounds). Overall, it is considered relatively eco-friendly if managed properly.
Skill and Training Requirements
- Laser Rust Removal: Requires specific training for safe and effective use, including handling the laser’s parameters, protective equipment, and knowledge of beam reflections.
- Electrolytic Rust Removal: Straightforward to learn, with basic knowledge of electrical safety and proper handling of the electrolyte solution. Most hobbyists can master the process quickly.
Scalability and Industrial VS. Hobbyist Uses
- Laser Rust Removal: Scalability is a strong suit, as high-power units can be integrated into automated lines for mass production. Large corporations favor laser systems for consistent quality and speed.
- Electrolytic Rust Removal: Simple and inexpensive for small or medium-sized items, making it popular among hobbyists, small workshops, and restoration experts. Large-scale or industrial-level electrolysis setups become more cumbersome and time-intensive.
Substrate Impact and Preservation
- Laser Rust Removal: Non-contact and can be adjusted to minimize heat input into the base metal, preserving details and underlying material. With correct settings, damage to the substrate is negligible.
- Electrolytic Rust Removal: Gently loosens rust with minimal surface removal, especially when voltage and current are carefully controlled. It’s favored for historically significant artifacts needing delicate treatment.
Maintenance and Consumables
- Laser Rust Removal: Primary costs involve laser system upkeep, cooling systems, and maintaining the integrity of optical components. Consumables are limited mainly to protective gear and extraction filters.
- Electrolytic Rust Removal: Anodes degrade over time and must be replaced, and the electrolyte solution eventually becomes contaminated and must be discarded responsibly. Overall costs remain relatively low.
Overall Practicality in Different Contexts
- Laser Rust Removal: Best-suited for high-throughput industrial settings, high-value component cleaning, or applications requiring quick turnarounds and precise control.
- Electrolytic Rust Removal: Ideal for smaller-scale, budget-sensitive, or long-term restoration projects where speed is less critical and delicate preservation is paramount.
Typical Users
- Laser Rust Removal: Automotive, aerospace, and marine industries; large-scale fabrication shops; museums and art restoration specialists with access to advanced equipment.
- Electrolytic Rust Removal: Individual hobbyists; small workshops; museums and conservation labs dealing with smaller metal artifacts; restoration enthusiasts who prioritize gentle cleaning and low overheads.