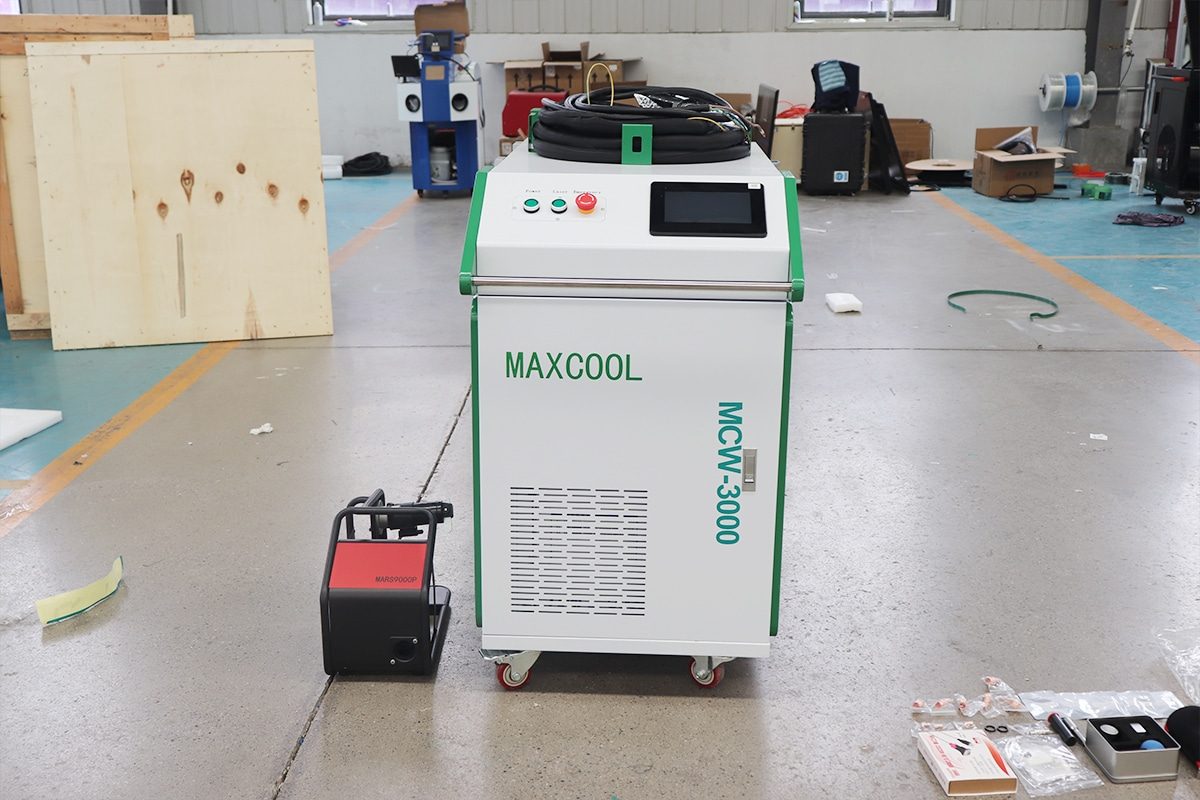
Laser Rust Removal VS Chemical Rust Removal
Rust is a common issue that affects metal surfaces in various industries, and removing rust effectively is essential to maintain the functionality and appearance of machinery, equipment, and structures. There are several methods for removing rust, with two of the most commonly used being chemical rust removal and laser rust removal. This article will explore the differences between these two techniques, providing an in-depth comparison of their effectiveness, safety, environmental impact, cost, and more. We will also consider the factors to weigh when choosing the most suitable rust removal method for your needs.
Table of Contents
Understanding Rust and Its Formation
What is Rust?
Rust is the result of the corrosion process that occurs when iron or its alloys, such as steel, react with oxygen and moisture in the environment. Chemically, rust is composed primarily of iron oxide, which forms when metal oxidizes due to prolonged exposure to air and water. This chemical reaction leads to the degradation of the metal surface, weakening its structure and appearance.
Rust typically manifests as a reddish-brown coating on metal surfaces, which can be flaky and uneven. Over time, if not addressed, rust can cause irreversible damage to materials, leading to costly repairs or replacements.
Rust typically manifests as a reddish-brown coating on metal surfaces, which can be flaky and uneven. Over time, if not addressed, rust can cause irreversible damage to materials, leading to costly repairs or replacements.
Why is Rust a Problem?
Rust poses significant challenges in various industries. It affects the integrity and durability of equipment, machinery, and infrastructure. The presence of rust can lead to:
- Structural Weakness: Rust compromises the strength of metals, making them brittle and prone to breakage.
- Aesthetic Damage: Rust disfigures metal surfaces, affecting the appearance of products or structures.
- Operational Failures: Rust can impair the function of mechanical parts, such as gears, valves, and pipes, leading to breakdowns or inefficiency in operations.
- Health and Safety Hazards: Corroded metal surfaces may pose risks to workers, particularly in industries like construction, automotive, and shipbuilding.
Chemical Rust Removal
What is Chemical Rust Removal?
Chemical rust removal involves using various chemical agents to dissolve or neutralize rust on metal surfaces. These chemical solutions typically contain acids, alkalis, or solvents that react with the iron oxide (rust) to break it down or convert it into a more manageable substance.
Common chemical rust removers include:
- Phosphoric Acid: Converts rust into a black iron phosphate layer that can be easily removed.
- Oxalic Acid: Used for light rust removal and can also clean stains from metals.
- Citric Acid: A milder acid often used for delicate applications.
How Chemical Rust Removal Works
The process typically involves applying the chemical solution directly onto the rusted surface and allowing it to react with the rust. Depending on the solution used, this process can take anywhere from a few minutes to a few hours. After the rust has been neutralized or dissolved, the metal surface is usually scrubbed, rinsed, and dried.
For large-scale applications, chemicals may be used in immersion tanks or sprayed onto metal parts for thorough rust removal.
For large-scale applications, chemicals may be used in immersion tanks or sprayed onto metal parts for thorough rust removal.
Applications of Chemical Rust Removal
Chemical rust removal is widely used in industries where large metal surfaces need to be cleaned, such as:
- Automotive and Transportation: Removing rust from vehicle bodies and engine components.
- Construction and Infrastructure: Treating rust on metal beams, structures, and equipment.
- Marine Industry: Dealing with rust on ships, pipelines, and marine equipment exposed to saltwater.
- Manufacturing: Cleaning rust off machine parts, tools, and other equipment.
Advantages of Chemical Rust Removal
- Cost-Effective: Chemical solutions are often inexpensive, making this method an attractive option for budget-conscious applications.
- Simplicity and Accessibility: Chemical rust removers are widely available, easy to use, and suitable for both large and small-scale operations.
- Effective on Heavily Rusted Surfaces: Chemicals are efficient in breaking down thick layers of rust.
- Wide Range of Applications: Chemical rust removal can be used on various types of metals and rust severity.
Disadvantages of Chemical Rust Removal
- Environmental Concerns: Many rust removal chemicals are toxic and hazardous to the environment. Proper disposal of these chemicals is necessary to avoid contamination.
- Health Risks: Direct contact with chemical rust removers can cause skin burns, eye irritation, and respiratory issues if inhaled.
- Potential for Material Damage: Chemicals can sometimes react with the underlying metal or paint, causing further damage, etching, or discoloration.
- Labor-Intensive: The application and post-treatment (scrubbing, rinsing, drying) can be time-consuming and labor-intensive.
Laser Rust Removal
What is Laser Rust Removal?
Laser rust removal utilizes high-powered lasers to remove rust and contaminants from metal surfaces. The laser beam heats the rust to extremely high temperatures, causing it to vaporize or be blown away by the force of the laser pulse. This technique is known for its precision, speed, and non-abrasive nature, making it ideal for delicate applications.
How Laser Rust Removal Works
In laser rust removal, a focused laser beam is directed at the rusted surface. The laser’s intense heat causes the rust particles to evaporate or peel off, leaving the underlying metal intact. The process can be finely controlled, adjusting the power and pulse frequency to ensure efficient rust removal without damaging the metal substrate.
Laser rust removal is typically carried out with fiber lasers, which are highly efficient at focusing on the specific wavelengths required to remove rust and contaminants from metals.
Laser rust removal is typically carried out with fiber lasers, which are highly efficient at focusing on the specific wavelengths required to remove rust and contaminants from metals.
Applications of Laser Rust Removal
Laser rust removal is used in industries where precision and non-invasive cleaning are critical:
- Aerospace: Cleaning delicate aircraft components without damaging sensitive materials.
- Electronics: Removing rust and contaminants from microelectronics and circuit boards.
- Automotive: Restoring car body parts, exhaust systems, and other components with minimal damage.
- Heavy Machinery: Treating industrial equipment and tools without disassembling or affecting the underlying parts.
- Art and Restoration: Gently removing rust from historical artifacts and sculptures.
Advantages of Laser Rust Removal
- High Precision: Lasers allow for precise rust removal without harming the base material, ensuring high-quality results.
- Eco-Friendly: No chemicals or solvents are used, making it a more sustainable option.
- Minimal Waste: The process generates minimal waste, as the rust is vaporized and not left as debris.
- Time Efficiency: Laser rust removal is typically faster than chemical methods, especially for smaller, intricate parts.
- Less Labor-Intensive: Automation of the laser cleaning process reduces the need for manual labor and intervention.
Disadvantages of Laser Rust Removal
- High Initial Cost: The equipment required for laser cleaning can be expensive, especially for high-powered lasers.
- Requires Skilled Operators: Proper training is needed to handle laser systems effectively and safely.
- Limited to Certain Materials: Laser rust removal works best on certain metals, such as steel and aluminum, but may not be suitable for all materials.
- Potential Heat Damage: If not controlled correctly, lasers can cause heat buildup, which might damage the underlying metal or paint.
Comparing Laser Rust Removal vs. Chemical Rust Removal
Rust removal is essential for maintaining the longevity and efficiency of metal surfaces across various industries. Both laser rust removal and chemical rust removal offer unique advantages and drawbacks, making it crucial to compare them based on key factors such as effectiveness, safety, environmental impact, cost, efficiency, and material compatibility.
Effectiveness
The effectiveness of rust removal depends on factors like rust thickness, metal type, and desired finish.
Chemical Rust Removal:
- Works well for deep-seated rust and heavily corroded surfaces.
- Certain chemicals (e.g., phosphoric acid) convert rust into a stable, protective layer.
- May require multiple applications for complete removal.
- Effectiveness can be impacted by uneven application or chemical dilution over time.
Laser Rust Removal:
- Provides a precise and thorough cleaning without damaging the base material.
- More effective for light to moderate rust removal.
- Can be adjusted for different rust levels using varying laser intensity settings.
- Works well on delicate or intricate components where chemical solutions may not reach.
Verdict:
- Chemical rust removal is better for heavy corrosion and large surfaces.
- Laser rust removal is superior for precision cleaning and surface preparation.
Safety and Health Considerations
Safety is a crucial factor when dealing with rust removal methods.
Chemical Rust Removal:
- Requires protective gear (gloves, goggles, masks) due to toxic fumes and skin irritation risks.
- Chemicals can be hazardous to handle, requiring controlled environments and proper ventilation.
- Can pose health risks such as burns, respiratory issues, and long-term chemical exposure.
Laser Rust Removal:
- Safer in terms of handling, as no chemicals are involved.
- Requires laser safety measures (e.g., protective eyewear and controlled operation zones).
- Generates minimal hazardous waste, reducing risks associated with disposal.
Verdict:
- Laser rust removal is the safer option, eliminating chemical hazards and reducing the need for personal protective equipment.
Environmental Impact
With increasing regulations on environmental safety, choosing an eco-friendly rust removal method is essential.
Chemical Rust Removal:
- Produces toxic chemical waste that requires proper disposal.
- Can contaminate soil and water if not handled correctly.
- Certain rust removers contain volatile organic compounds (VOCs) that contribute to air pollution.
Laser Rust Removal:
- Eco-friendly, as it does not produce chemical waste or toxic byproducts.
- Generates minimal dust, which can be captured using filtration systems.
- Reduces reliance on hazardous substances, making it compliant with environmental regulations.
Verdict:
- Laser rust removal is significantly more environmentally friendly than chemical rust removal.
Cost Comparison
Initial investment and long-term costs play a significant role in deciding the best rust removal method.
Chemical Rust Removal:
- Low initial cost, as chemical solutions and basic equipment are inexpensive.
- Requires repeated purchases of chemicals, adding to long-term costs.
- Disposal costs for hazardous waste can be high.
Laser Rust Removal:
- The high initial investment for laser equipment.
- Minimal ongoing costs (only electricity and maintenance).
- Long-term cost savings due to no recurring chemical expenses or disposal fees.
Verdict:
- Chemical rust removal is cheaper initially but incurs higher long-term costs.
- Laser rust removal has a high upfront cost but offers significant savings over time.
Time and Efficiency
Time efficiency is critical for industrial applications.
Chemical Rust Removal:
- Requires application time, waiting periods for chemical reactions, and additional scrubbing or rinsing.
- Can take several hours or even days for complete rust removal.
- Inconsistent results may require reapplication.
Laser Rust Removal:
- Instantaneous rust removal with no waiting time.
- High-speed cleaning for industrial applications.
- Eliminates the need for secondary processes like washing or neutralization.
Verdict:
- Laser rust removal is far more efficient, reducing downtime and increasing productivity.
Material Compatibility
Different metals and materials respond differently to rust removal methods.
Chemical Rust Removal:
- Suitable for ferrous and non-ferrous metals but may cause discoloration or etching.
- Some chemicals can weaken or corrode delicate materials.
- Paint and coatings may be damaged during the process.
Laser Rust Removal:
- Works best on metals like steel, aluminum, and copper.
- Can be fine-tuned to avoid material damage.
- The non-contact process makes it ideal for intricate and delicate components.
Verdict:
- Laser rust removal offers superior compatibility and control over a wider range of materials.
Factors to Consider When Choosing the Right Rust Removal Method
Choosing between laser rust removal and chemical rust removal depends on various factors:
Size and Complexity of the Rusted Object
- Large surfaces (e.g., pipelines, and industrial equipment) may benefit from chemical rust removal.
- Small or intricate parts (e.g., aerospace or automotive components) are better suited for laser cleaning due to precision control.
Type of Material Being Cleaned
- Chemical rust removal: May react differently with certain metals, causing etching or damage.
- Laser rust removal: Ideal for sensitive or high-precision applications where preserving the material is crucial.
The Severity of Rust
- Heavy rust buildup: Chemical rust removers are better suited for removing deep corrosion.
- Light to moderate rust: Laser rust removal provides a clean, residue-free surface.
Desired Finish and Precision Level
- Chemical removal: May leave behind residues or require post-cleaning to achieve a smooth finish.
- Laser removal: Offers a clean, polished finish with minimal residue.
Budget Constraints and Long-Term Costs
- Limited budgets: Chemical rust removal is a more affordable short-term option.
- Long-term savings: Laser rust removal eliminates recurring costs associated with chemicals and disposal.
Speed and Efficiency Requirements
- High-speed operations: Laser rust removal is preferable for fast, continuous processing.
- Slow-paced applications: Chemical rust removal may be adequate for small-scale or occasional use.
Environmental Impact Concerns
- If eco-friendliness is a priority, laser rust removal is the better option due to zero chemical waste and minimal emissions.
Health and Safety Considerations
- If worker safety is a major concern: Laser rust removal eliminates exposure to toxic substances and hazardous fumes.
- For controlled environments with proper ventilation: Chemical rust removal may still be an option but requires strict safety measures.
Summary
Both laser rust removal and chemical rust removal have their strengths and weaknesses. The choice between the two depends on factors such as material type, rust severity, cost, environmental impact, and the desired level of precision. Laser rust removal is ideal for high-precision, environmentally conscious applications, while chemical rust removal may still be the preferred choice for heavy-duty rusting on large, industrial surfaces. Businesses should evaluate their specific needs to select the most suitable rust removal method.
Get Laser Rust Removal Solutions
Maxcool CNC specializes in high-performance laser cleaning machines designed to provide efficient, eco-friendly, and cost-effective rust removal solutions. Whether you need to restore industrial equipment, maintain precision components, or prepare surfaces for coating, our advanced fiber laser cleaning technology offers a non-contact, chemical-free method that ensures optimal results.
Our laser rust removal machines deliver precise, fast, and residue-free cleaning, making them ideal for industries such as automotive, aerospace, manufacturing, and shipbuilding. Compared to traditional chemical rust removal, our solutions offer minimal maintenance, reduced operational costs, and superior environmental benefits.
At Maxcool CNC, we provide customized solutions tailored to your specific rust removal needs, offering a range of power options, automation levels, and handheld or automated systems. Contact us today to discover the right laser cleaning machine for your business and experience a safer, more efficient rust removal process. Get in touch now for expert consultation and product recommendations!
Our laser rust removal machines deliver precise, fast, and residue-free cleaning, making them ideal for industries such as automotive, aerospace, manufacturing, and shipbuilding. Compared to traditional chemical rust removal, our solutions offer minimal maintenance, reduced operational costs, and superior environmental benefits.
At Maxcool CNC, we provide customized solutions tailored to your specific rust removal needs, offering a range of power options, automation levels, and handheld or automated systems. Contact us today to discover the right laser cleaning machine for your business and experience a safer, more efficient rust removal process. Get in touch now for expert consultation and product recommendations!