Laser Cleaning Rubber
Rubber Laser Cleaning Machine
-
Standard Continuous Laser Cleaning Machine
Rated 4.75 out of 5$3,200 – $6,600 This product has multiple variants. The options may be chosen on the product page -
Portable Continuous Laser Cleaning Machine
Rated 4.50 out of 5$3,100 – $6,500 This product has multiple variants. The options may be chosen on the product page -
Double Wobble Pulse Laser Cleaning Machine
Rated 4.75 out of 5$4,300 – $16,000 This product has multiple variants. The options may be chosen on the product page -
Luggage Pulse Laser Cleaning Machine
Rated 5.00 out of 5$6,300 – $16,800 This product has multiple variants. The options may be chosen on the product page -
Backpack Pulse Laser Cleaning Machine
Rated 4.75 out of 5$6,600 – $8,900 This product has multiple variants. The options may be chosen on the product page -
High Power Pulse Laser Cleaning Machine
Rated 4.75 out of 5$9,300 – $64,300 This product has multiple variants. The options may be chosen on the product page -
Double Wobble Continuous Laser Cleaning Machine
Rated 5.00 out of 5$3,700 – $7,100 This product has multiple variants. The options may be chosen on the product page
Benefits of Laser Cleaning Rubber
Precision Cleaning
Laser cleaning offers precise removal of rubber contaminants without damaging the underlying material, making it ideal for delicate or intricate components.
Environmentally Friendly
Laser cleaning eliminates the need for harsh chemicals or solvents, making it an eco-friendly solution that helps reduce environmental pollution and hazardous waste.
Non-Abrasive Process
Unlike mechanical cleaning methods, laser cleaning is non-abrasive, preventing surface damage and ensuring longer life for molds and industrial parts.
Reduced Maintenance Costs
Laser cleaning machines require minimal maintenance, lowering operational costs and providing long-term savings compared to traditional cleaning methods that involve frequent upkeep.
Improved Efficiency
The high-speed process of laser cleaning rubber enables quicker turnaround times, improving overall production efficiency without compromising the quality of cleaning.
Versatile Application
Laser cleaning is adaptable to various industries and can be used on different materials, making it an ideal solution for diverse rubber cleaning applications.
Factors to Consider Before Buying Rubber Laser Cleaning Machines
Laser Power
Ensure the machine offers adjustable laser power suitable for your specific rubber cleaning applications, enabling effective removal without damaging the underlying material.
Material Compatibility
Check that the machine can handle various types of rubber and other materials involved in your processes to ensure efficient and damage-free cleaning.
Cleaning Speed
Consider the machine’s cleaning speed and whether it matches your production requirements. Faster cleaning times will increase efficiency and reduce downtime.
Precision
Look for a machine that provides high precision, allowing selective cleaning of delicate surfaces or intricate components without harming the surrounding areas.
Machine Size
Evaluate whether the machine’s size and design fit into your workspace. Compact or portable models may be more suitable for space-limited environments.
Energy Consumption
Analyze the machine’s energy efficiency to reduce operational costs. Energy-efficient models will help minimize power consumption during long-term use.
Maintenance Requirements
Choose a machine that requires minimal maintenance to reduce downtime and associated costs. Consider the availability of spare parts and technical support.
Safety Features
Ensure the machine is equipped with essential safety features, such as protective enclosures, emergency stop buttons, and operator-friendly controls to minimize risks during use.
Comparison with Other Rubber Cleaning Methods
Feature | Laser Cleaning | Chemical Cleaning | Mechanical Cleaning |
Precision | Highly precise, allows selective cleaning without damaging underlying surfaces | Can cause damage if not carefully controlled | Less precise, risk of abrasion to surfaces |
Environmental Impact | Eco-friendly, no chemicals or waste generated | Involves harmful chemicals, requires disposal | Can create dust or waste, and requires cleanup |
Surface Damage | Non-abrasive, no surface damage | Potential chemical reaction that could affect surfaces | Can cause wear and tear, especially on delicate parts |
Cost | Higher initial investment, lower long-term operational costs | Lower initial cost, but recurring expenses for chemicals and disposal | Moderate cost, with expenses related to equipment wear and maintenance |
Cleaning Speed | Fast cleaning, especially for high-power lasers | Slower, depends on chemical reaction time | Time-consuming, especially for detailed parts |
Safety | Safe with proper equipment; no toxic fumes | Risk of exposure to harmful chemicals and fumes | Risk of injury from abrasive tools or machinery |
Maintenance | Low maintenance, few consumables required | High maintenance, frequent replenishment of chemicals needed | Moderate maintenance, frequent replacement of parts or tools |
Application of Laser Cleaning Rubber
- Mold Cleaning: In industries such as automotive and manufacturing, laser cleaning is ideal for removing rubber residues from molds without causing surface damage. It extends the lifespan of the molds and ensures consistent product quality.
- Tire Manufacturing: Laser cleaning is used to clean rubber from tire manufacturing equipment, ensuring smooth production and reducing downtime. It also helps maintain the accuracy and performance of the machinery.
- Rubber Seal Removal: In mechanical and industrial processes, laser cleaning can remove worn or degraded rubber seals from metal parts, facilitating easy replacement and reducing manual labor.
- Rubber Buildup in Industrial Machinery: Rubber can accumulate on industrial equipment, causing operational inefficiencies. Laser cleaning effectively removes these buildups without halting production for extended periods.
- Maintenance of Rubber Components: Laser cleaning is also applied in the maintenance of rubber components, removing contaminants like oil and grease from rubber parts to restore their functionality.
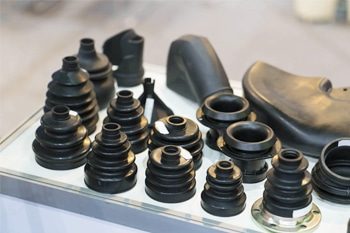
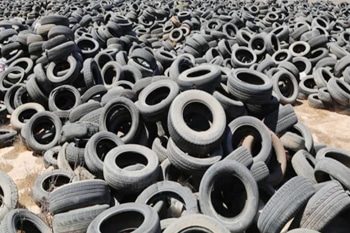
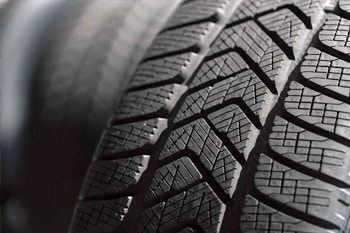
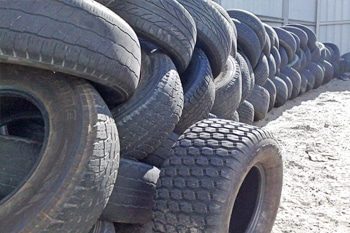
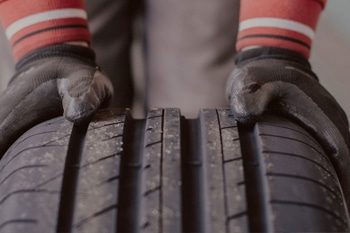
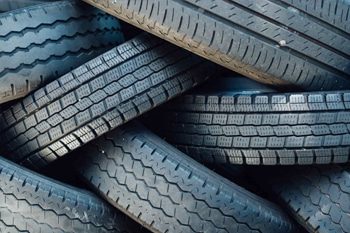
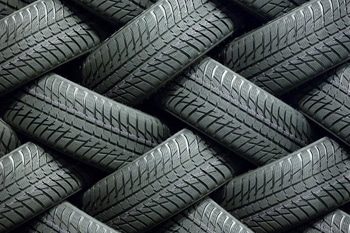
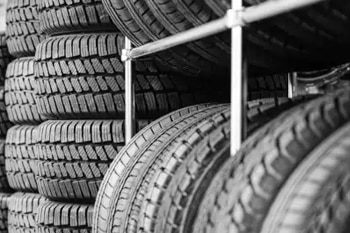