Laser Cleaning Residues
Residue Laser Cleaning Machines
-
Standard Continuous Laser Cleaning Machine
Rated 4.75 out of 5$3,200 – $6,600 This product has multiple variants. The options may be chosen on the product page -
Portable Continuous Laser Cleaning Machine
Rated 4.50 out of 5$3,100 – $6,500 This product has multiple variants. The options may be chosen on the product page -
Double Wobble Pulse Laser Cleaning Machine
Rated 4.75 out of 5$4,300 – $16,000 This product has multiple variants. The options may be chosen on the product page -
Luggage Pulse Laser Cleaning Machine
Rated 5.00 out of 5$6,300 – $16,800 This product has multiple variants. The options may be chosen on the product page -
Backpack Pulse Laser Cleaning Machine
Rated 4.75 out of 5$6,600 – $8,900 This product has multiple variants. The options may be chosen on the product page -
High Power Pulse Laser Cleaning Machine
Rated 4.75 out of 5$9,300 – $64,300 This product has multiple variants. The options may be chosen on the product page -
Double Wobble Continuous Laser Cleaning Machine
Rated 5.00 out of 5$3,700 – $7,100 This product has multiple variants. The options may be chosen on the product page
Benefits of Laser Cleaning Residues
Non-Abrasive Cleaning
Laser cleaning does not damage the surface, making it ideal for delicate materials or components that require precision cleaning without causing wear.
Environmentally Friendly
Laser cleaning eliminates the need for harsh chemicals, producing no secondary waste, making it a sustainable, eco-friendly alternative to traditional methods.
Precision and Control
The adjustable power and focus of laser cleaning allow precise residue removal, ensuring only targeted areas are cleaned without affecting surrounding surfaces.
Versatile Applications
Laser cleaning can handle various residues, from rust and oil to paint and coatings, across different materials such as metals, plastics, and stone.
Reduced Operational Costs
With minimal maintenance, no consumables, and faster cleaning times, laser cleaning can reduce operational expenses and increase efficiency over conventional cleaning methods.
Enhanced Worker Safety
Laser cleaning minimizes exposure to hazardous chemicals and reduces the physical labor required, creating a safer working environment for employees.
Factors to Consider Before Buying Residue Laser Cleaning Machines
Type of Residue
Determine the types of residues, such as rust, oil, or paint, that need removal to select the appropriate laser cleaning power and configuration.
Material Compatibility
Ensure the machine can handle the material you're cleaning, whether it's metal, plastic, or stone, without causing damage or altering its properties.
Power Output
Choose between pulsed and continuous lasers based on your cleaning needs. High-power machines are better suited for heavy-duty residue removal on larger surfaces.
Cleaning Speed and Efficiency
Assess the machine’s cleaning speed and efficiency to meet your production demands. Faster machines can enhance productivity but may require more power.
Portability and Mobility
Depending on your workspace, consider whether you need a portable machine for flexible use or a stationary unit for more intensive industrial cleaning.
Energy Consumption
Evaluate the energy consumption of the machine. More powerful machines may offer faster cleaning but could lead to higher operational costs.
Maintenance and Durability
Consider the machine's long-term maintenance needs, including the availability of replacement parts, service, and overall durability to ensure cost-effectiveness.
Automation and Control Features
Look for automation options and customizable control settings to allow for better precision, efficiency, and ease of use, especially in complex cleaning tasks.
Comparison with Other Residue Cleaning Methods
Feature | Laser Cleaning | Chemical Cleaning | Abrasive Blasting | Ultrasonic Cleaning |
Environmental Impact | Eco-friendly, no chemicals or waste | High chemical waste and environmental risk | Generates dust and waste particles | Requires chemical solvents, moderate waste |
Surface Preservation | Non-abrasive preserves surface integrity | May cause chemical corrosion or damage | Highly abrasive, can damage surface | Non-abrasive, gentle on surfaces |
Precision and Control | High precision, adjustable power, and focus | Difficult to control specific areas | Limited precision, hard to control | Effective in hard-to-reach areas |
Material Compatibility | Works on a variety of materials (metal, plastic, stone) | Suitable for specific materials only | Best for hard surfaces, not ideal for soft materials | Limited to small, intricate objects |
Efficiency and Speed | Fast, can clean large surfaces quickly | Time-consuming and labor-intensive | Requires setup and post-cleaning processing | Time-consuming for large-scale cleaning |
Health and Safety | Safe for workers, no chemical exposure | Hazardous chemicals and fumes | Dust and noise hazards | Requires careful handling of solvents |
Maintenance Costs | Low maintenance, no consumables required | High cost for chemicals and disposal | High cost for abrasive materials and equipment wear | Moderate maintenance costs, chemicals needed |
Operational Flexibility | Mobile and easy to operate | Requires extensive setup and disposal | Requires specialized equipment and setup | Requires immersion tanks and control setup |
Application of Laser Cleaning Residues
- Automotive Industry: Laser cleaning is utilized to remove rust, paint, and grease from car components, ensuring surfaces are clean for welding, coating, or assembly without causing damage to the material.
- Aerospace Industry: In aerospace, laser cleaning helps remove oxidation and corrosion from aircraft components, ensuring parts meet the strict safety and quality standards required in this industry.
- Manufacturing and Maintenance: Manufacturers rely on laser cleaning for residue removal during routine maintenance of machinery. This helps prolong equipment life and ensures better performance by eliminating contaminants that affect functionality.
- Restoration and Conservation: Laser cleaning is used in art restoration and conservation projects to delicately remove layers of grime or corrosion from historical artifacts, sculptures, or buildings without damaging the original surfaces.
- Energy and Power Generation: Power plants and energy facilities use laser cleaning to clean turbine blades, generators, and other equipment to maintain efficiency, especially for removing tough residues like carbon deposits and oxidation.
- Shipbuilding and Marine Applications: Laser cleaning is employed in shipyards to remove rust, coatings, and marine biofouling from ships’ hulls and other components, helping maintain the structural integrity of vessels.
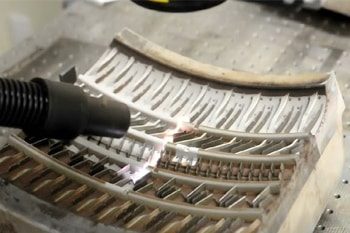
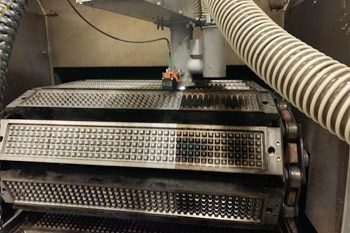
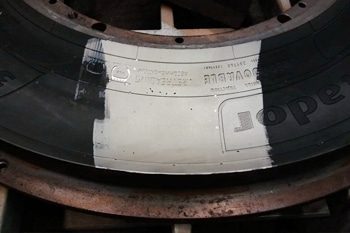
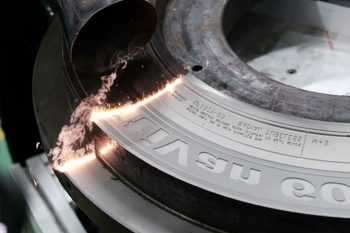
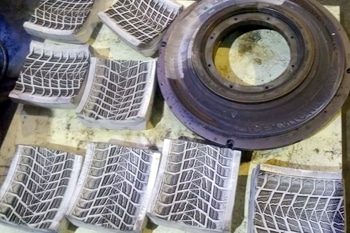
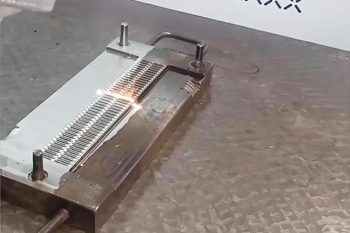
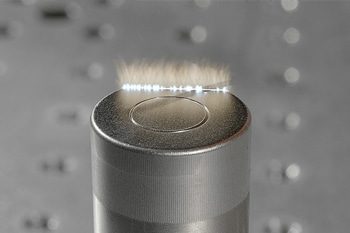
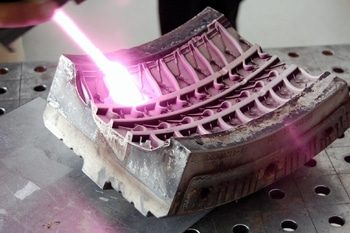