Laser Cleaning Plastic
Plastic Laser Cleaning Machine
-
Standard Continuous Laser Cleaning Machine
Rated 4.75 out of 5$3,200 – $6,600 This product has multiple variants. The options may be chosen on the product page -
Portable Continuous Laser Cleaning Machine
Rated 4.50 out of 5$3,100 – $6,500 This product has multiple variants. The options may be chosen on the product page -
Double Wobble Pulse Laser Cleaning Machine
Rated 4.75 out of 5$4,300 – $16,000 This product has multiple variants. The options may be chosen on the product page -
Luggage Pulse Laser Cleaning Machine
Rated 5.00 out of 5$6,300 – $16,800 This product has multiple variants. The options may be chosen on the product page -
Backpack Pulse Laser Cleaning Machine
Rated 4.75 out of 5$6,600 – $8,900 This product has multiple variants. The options may be chosen on the product page -
High Power Pulse Laser Cleaning Machine
Rated 4.75 out of 5$9,300 – $64,300 This product has multiple variants. The options may be chosen on the product page -
Double Wobble Continuous Laser Cleaning Machine
Rated 5.00 out of 5$3,700 – $7,100 This product has multiple variants. The options may be chosen on the product page
Benefits of Laser Cleaning Plastic
Non-Contact Cleaning
Laser cleaning provides a non-contact method, ensuring that delicate plastic surfaces are not damaged or distorted during the cleaning process.
Precision and Control
With adjustable power settings, laser cleaning can precisely target contaminants without affecting the underlying plastic, ensuring consistent results.
Chemical-Free Process
Laser cleaning eliminates the need for harsh chemicals, making it an environmentally friendly and safer option for plastic cleaning in sensitive industries.
Versatile Application
It is effective on a variety of plastic types, making it suitable for diverse industries, from automotive to electronics and packaging.
No Abrasion or Surface Damage
Unlike traditional cleaning methods, laser cleaning does not cause surface abrasion, maintaining the integrity and appearance of plastic components.
Reduced Downtime
The efficiency and speed of laser cleaning reduce production downtime, helping manufacturers increase productivity and maintain operational flow.
Factors to Consider Before Buying Plastic Laser Cleaning Machines
Plastic Material Sensitivity
Ensure the machine is suitable for the specific plastic types you work with, as some plastics may be more sensitive to laser exposure.
Laser Power Settings
Check if the machine offers adjustable laser power to handle different cleaning tasks. Variable settings are essential for achieving precision on delicate plastic surfaces.
Cleaning Speed
Evaluate the cleaning speed to meet your production requirements. Faster machines increase efficiency, but slower, precise models may be better for delicate cleaning tasks.
Non-Contact Cleaning Capability
Ensure the machine provides non-contact cleaning to prevent mechanical damage or surface distortion, especially when working with softer plastic materials.
Automation Level
Consider whether you need a handheld or automated system. Automated machines are ideal for large-scale, consistent operations, while handheld models offer flexibility.
Maintenance Requirements
Look for machines that require minimal maintenance, ensuring consistent operation without frequent downtime or complex servicing, saving both time and costs.
Energy Consumption
Evaluate the machine’s energy efficiency. Lower energy consumption reduces operational costs and aligns with sustainability goals, especially for long-term use.
Environmental Impact
Laser cleaning is generally eco-friendly, but it’s important to choose a machine that further minimizes waste and aligns with your company’s environmental policies.
Comparison with Other Plastic Cleaning Methods
Feature | Laser Cleaning | Chemical Cleaning | Mechanical Cleaning | Ultrasonic Cleaning |
Precision | High precision, targets specific areas | Moderate, depending on chemical strength | Low, risk of surface damage | Moderate, depending on frequency |
Surface Damage Risk | Minimal to none, non-contact process | Potential damage due to chemical reaction | High, especially with abrasive methods | Low, but some risk for delicate plastics |
Environmental Impact | Eco-friendly, no chemicals or waste | High, use harmful chemicals | Moderate, generates physical waste | Moderate, uses water and energy |
Operational Speed | Fast, with instant results | Slow, involves application and drying | Medium, depending on the method used | Fast, but requires setup |
Energy Consumption | Low to moderate, energy-efficient | Low, unless heating is involved | Low to moderate, depending on tools used | High, due to ultrasonic transducers |
Cost Efficiency | High, low operating and maintenance costs | Low, recurring cost of chemicals | Moderate, tool wear and labor required | High, equipment and operational costs |
Safety | Safe with proper shielding and use | Low, exposure to hazardous chemicals | Low, risk of injury from abrasives | Moderate, risk of burns or damage |
Application of Laser Cleaning Plastic
- Automotive Industry: Laser cleaning is used to remove paint, coatings, and contaminants from plastic components in automotive manufacturing, ensuring clean surfaces for further processing, such as painting or bonding.
- Electronics and Semiconductors: In the production of electronic devices, laser cleaning can effectively remove adhesives, residues, or oxides from plastic housings or components without affecting delicate electronics.
- Medical Device Manufacturing: Medical-grade plastics require stringent cleanliness. Laser cleaning is ideal for removing contamination and ensuring the surfaces are clean and sterile, without the risk of chemical residue.
- Packaging Industry: Plastic packaging materials, such as containers and films, can be cleaned with lasers to remove contaminants or labels, offering a safe, fast, and chemical-free cleaning process.
- Aerospace Components: For plastic parts used in aerospace applications, laser cleaning can remove unwanted layers or residues while maintaining the structural integrity of the material, essential for safety-critical components.
- Restoration and Conservation: Laser cleaning is used in restoring plastic artifacts or products by delicately removing surface impurities without causing damage to the underlying material, making it suitable for cultural preservation.
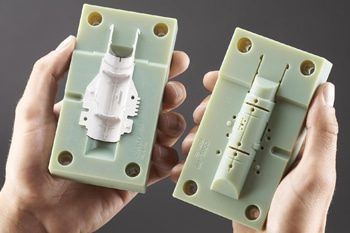
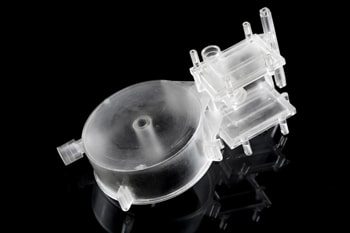
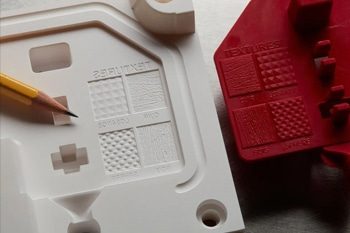
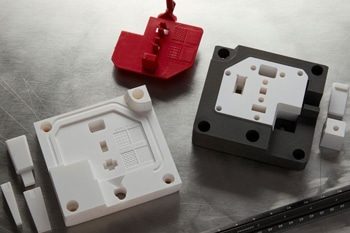
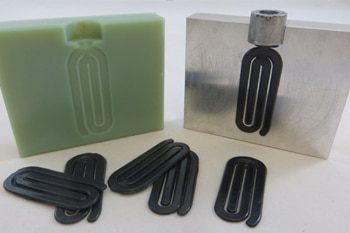
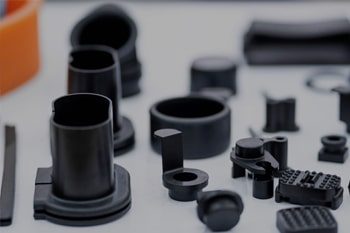
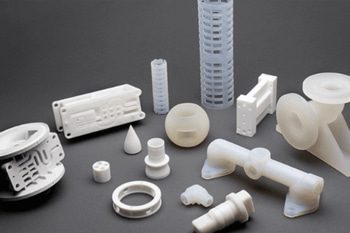
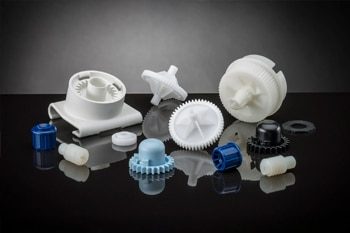