Laser Cleaning Oxide Layers
Oxide Layers Laser Cleaning Machines
-
Standard Continuous Laser Cleaning Machine
Rated 4.75 out of 5$3,200 – $6,600 This product has multiple variants. The options may be chosen on the product page -
Portable Continuous Laser Cleaning Machine
Rated 4.50 out of 5$3,100 – $6,500 This product has multiple variants. The options may be chosen on the product page -
Double Wobble Pulse Laser Cleaning Machine
Rated 4.75 out of 5$4,300 – $16,000 This product has multiple variants. The options may be chosen on the product page -
Luggage Pulse Laser Cleaning Machine
Rated 5.00 out of 5$6,300 – $16,800 This product has multiple variants. The options may be chosen on the product page -
Backpack Pulse Laser Cleaning Machine
Rated 4.75 out of 5$6,600 – $8,900 This product has multiple variants. The options may be chosen on the product page -
High Power Pulse Laser Cleaning Machine
Rated 4.75 out of 5$9,300 – $64,300 This product has multiple variants. The options may be chosen on the product page -
Double Wobble Continuous Laser Cleaning Machine
Rated 5.00 out of 5$3,700 – $7,100 This product has multiple variants. The options may be chosen on the product page
Benefits of Laser Cleaning Oxide Layers
Precision Cleaning
Laser cleaning effectively removes oxide layers with pinpoint accuracy, targeting only the contaminants without affecting the underlying material.
Environmentally Friendly
This method uses no chemicals or abrasive materials, reducing environmental impact and making it a sustainable choice for industrial cleaning.
Minimal Downtime
Fast and efficient, laser cleaning minimizes operational downtime by quickly removing oxide layers, leading to improved productivity and reduced maintenance costs.
Enhanced Safety
With no hazardous chemicals involved, laser cleaning provides a safer working environment for operators, reducing risks associated with traditional cleaning methods.
Versatile Applications
Ideal for various surfaces and materials, laser oxide layer cleaning is adaptable to different industrial needs, including aerospace, automotive, and manufacturing sectors.
Long-Term Cost Savings
By extending the lifespan of equipment and reducing the need for manual labor or replacement parts, laser cleaning offers significant long-term cost savings.
Factors to Consider Before Buying Oxide Layers Laser Cleaning Machines
Laser Power
Ensure the machine has adequate laser power for your specific oxide removal needs. Higher power offers better efficiency but may increase energy consumption.
Wavelength and Beam Quality
Choose a machine with the right wavelength and beam quality to effectively target oxide layers without damaging the underlying material.
Surface Compatibility
Verify that the laser cleaning machine is compatible with the surfaces and materials you frequently work with, including metals, ceramics, and composites.
Operating Costs
Consider the long-term operating costs, including maintenance, energy consumption, and replacement parts, to ensure the machine fits within your budget.
Size and Portability
Assess the size and portability of the machine to ensure it fits your workspace and meets your mobility requirements for different cleaning applications.
User-Friendliness
Look for features that enhance ease of use, such as intuitive controls and automated settings, to minimize training time and operator error.
Safety Features
Ensure the machine includes comprehensive safety features, such as protective enclosures and emergency shutoff systems, to safeguard operators during use.
Support and Warranty
Check for reliable customer support and a robust warranty to address any potential issues and ensure the long-term reliability of the laser cleaning machine.
Comparison with Other Cleaning Oxide Layers Methods
Feature/Method | Laser Cleaning | Sandblasting | Chemical Paint Removal | Mechanical Grinding | Electrolytic Paint Removal | Ultrasonic Rust Removal |
Precision | High precision, targets only oxide | Moderate precision, abrasive effects | Variable precision, risk of damage | Moderate precision, abrasive effects | High precision, but can be uneven | High precision, limited by shape |
Environmental Impact | Low, no chemicals or abrasives | High, generates dust and waste | High, uses hazardous chemicals | Moderate, creates dust and debris | Low, mainly uses water and electricity | Low, non-toxic cleaning solution |
Safety | High, no hazardous materials | Moderate, requires safety precautions | Low, involves handling toxic chemicals | Moderate, dust and noise issues | High, generally safe with proper setup | High, non-toxic and safe |
Efficiency | High, quick and effective | Moderate, can be time-consuming | Variable, depends on chemical used | Moderate, can be time-consuming | High, effective for specific cases | Moderate, slower than other methods |
Surface Compatibility | Broad, works on various surfaces | Limited, may damage certain surfaces | Limited, may react with some materials | Limited, may damage delicate surfaces | Limited, effective on conductive surfaces | Broad, effective on various surfaces |
Cost of Operation | Moderate, energy-efficient | Low, but requires abrasive materials | Variable, cost of chemicals | Moderate, wear on grinding tools | High, specialized equipment needed | Moderate, requires ultrasonic equipment |
Maintenance | Low, minimal wear and tear | High, frequent maintenance needed | Moderate, cleanup and handling required | Moderate, wear on equipment | High, requires maintenance and setup | Moderate, periodic equipment care needed |
Versatility | High, adaptable to various applications | Moderate, specific to certain tasks | Low, specialized for paint removal | Moderate, specific to rough surfaces | Low, limited to conductive surfaces | Moderate, limited to small parts |
Application of Laser Cleaning Oxide Layers
- Aerospace Industry: Laser cleaning effectively removes oxide layers from aircraft components, ensuring optimal performance and safety by preparing surfaces for inspection, repair, and coating.
- Automotive Manufacturing: Ideal for cleaning rust and oxide layers from automotive parts, laser technology enhances the durability and appearance of components, leading to improved assembly and performance.
- Shipbuilding: In shipbuilding, laser cleaning removes corrosion and oxide layers from metal surfaces, ensuring structural integrity and extending the lifespan of vessels and marine equipment.
- Construction Equipment: For heavy machinery and construction equipment, laser cleaning eliminates rust and contaminants, improving functionality and reducing maintenance needs for extended equipment life.
- Electronics Industry: Laser cleaning is used to prepare electronic components by removing oxide layers and residues, ensuring reliable performance and extending the lifespan of sensitive electronic parts.
- Manufacturing and Fabrication: In manufacturing and fabrication, laser cleaning prepares metal surfaces for welding, coating, and bonding, ensuring high-quality finishes and reducing post-processing requirements.
- Historical Restoration: Laser cleaning is employed in the restoration of historical artifacts and buildings, effectively removing oxidation and dirt without damaging delicate surfaces or original materials.
- Energy Sector: In the energy sector, laser cleaning is used to maintain and restore equipment such as turbines and generators, enhancing efficiency and preventing performance degradation due to oxide buildup.
- Metal Recycling: Laser cleaning aids in the recycling process by removing contaminants from metal scrap, improving the quality of recycled materials, and ensuring they meet industry standards for reuse.
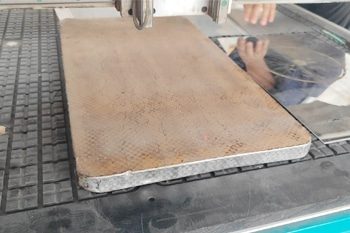
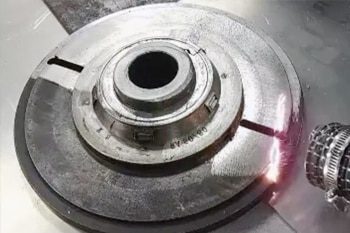
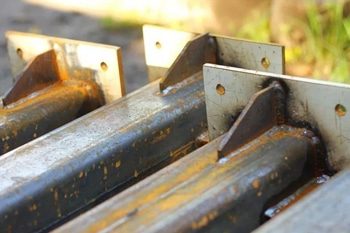
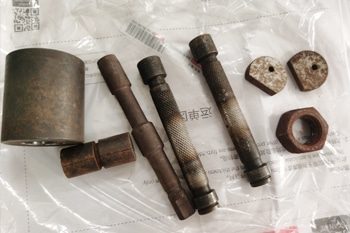
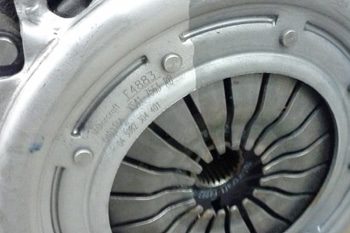
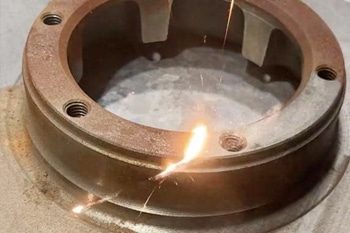
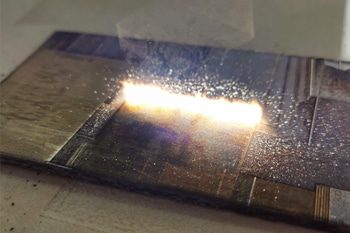
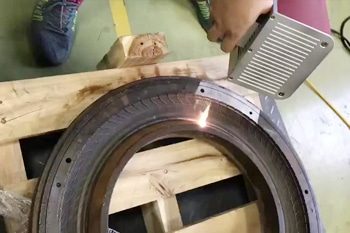