Laser Cleaning Contaminants
Contaminants Laser Cleaning Machines
-
Standard Continuous Laser Cleaning Machine
Rated 4.75 out of 5$3,200 – $6,600 This product has multiple variants. The options may be chosen on the product page -
Portable Continuous Laser Cleaning Machine
Rated 4.50 out of 5$3,100 – $6,500 This product has multiple variants. The options may be chosen on the product page -
Double Wobble Pulse Laser Cleaning Machine
Rated 4.75 out of 5$4,300 – $16,000 This product has multiple variants. The options may be chosen on the product page -
Luggage Pulse Laser Cleaning Machine
Rated 5.00 out of 5$6,300 – $16,800 This product has multiple variants. The options may be chosen on the product page -
Backpack Pulse Laser Cleaning Machine
Rated 4.75 out of 5$6,600 – $8,900 This product has multiple variants. The options may be chosen on the product page -
High Power Pulse Laser Cleaning Machine
Rated 4.75 out of 5$9,300 – $64,300 This product has multiple variants. The options may be chosen on the product page -
Double Wobble Continuous Laser Cleaning Machine
Rated 5.00 out of 5$3,700 – $7,100 This product has multiple variants. The options may be chosen on the product page
Benefits of Laser Cleaning Contaminants
Non-Abrasive
Laser cleaning removes contaminants without causing surface damage, making it perfect for delicate materials and high-value assets like metals and machinery.
Precision Cleaning
Laser cleaning offers precise control, ensuring contaminants are removed accurately without affecting surrounding areas, ideal for intricate surfaces and detailed parts.
Eco-Friendly
Laser cleaning is a chemical-free process, reducing harmful waste and environmental impact while contributing to more sustainable industrial practices.
Cost-Effective
By reducing the need for consumables and minimizing equipment wear, laser cleaning lowers long-term maintenance and operational costs.
Versatile Application
Laser cleaning can handle a variety of contaminants, from rust and paint to grease and oils, on diverse materials such as metal, ceramics, and stone.
Minimal Downtime
The quick, efficient process reduces downtime during maintenance and cleaning, allowing industries to maintain high productivity and meet operational targets.
Factors to Consider Before Buying Contaminants Laser Cleaning Machines
Power Output
Choose a machine with the appropriate laser power for your cleaning needs, ensuring it effectively handles tough contaminants without damaging the underlying material.
Material Compatibility
Ensure the machine is compatible with the types of surfaces you will be cleaning, such as metals, plastics, ceramics, or composite materials.
Contaminant Type
Different contaminants, such as rust, oil, or paint, require varying laser intensities. Select a machine that can target the specific contaminants you deal with.
Portability
Depending on the size of your workspace, decide whether you need a portable laser cleaning machine for mobility or a stationary machine for larger operations.
Automation Features
Look for features like automatic adjustment, precision control, and user-friendly interfaces to increase operational efficiency and reduce operator involvement.
Environmental Impact
Consider eco-friendly options that eliminate the need for chemicals and generate minimal waste, aligning with sustainability goals and reducing disposal costs.
Initial and Operating Costs
Factor in both the purchase price and ongoing operational costs, such as energy consumption and maintenance, to determine long-term affordability.
Safety Features
Ensure the machine has essential safety features like interlock systems, emergency stops, and proper ventilation to protect operators from laser-related hazards.
Comparison with Other Contaminants Cleaning Methods
Dimension | Laser Cleaning | Chemical Cleaning | Abrasive Blasting | Mechanical Cleaning | Ultrasonic Cleaning |
Cleaning Method | Non-abrasive, chemical-free, laser-based technology. | Uses solvents and chemical agents. | Blasts surfaces with abrasive materials. | Manual or machine-assisted physical cleaning. | Uses high-frequency sound waves and liquid solution. |
Environmental Impact | Minimal environmental impact, no chemicals, little waste. | High environmental impact, requires careful disposal of chemicals. | Generates significant dust and waste, requires containment. | Minimal environmental impact but can be labor-intensive. | Eco-friendly, minimal waste and no harmful chemicals. |
Surface Damage Risk | Low risk, gentle on sensitive surfaces. | Can damage surfaces if not used carefully. | High risk of surface damage, especially on delicate materials. | High risk of surface damage, especially with heavy machinery. | Very low risk of surface damage, gentle on small parts. |
Precision | High precision, ideal for intricate or delicate surfaces. | Low precision, not suitable for sensitive surfaces. | Low precision, mainly suited for heavy-duty cleaning. | Low precision, generally used for basic cleaning tasks. | High precision, ideal for small and intricate items. |
Material Compatibility | Compatible with metals, ceramics, plastics, and more. | Limited to materials that can withstand chemicals. | Limited to robust materials like metals. | Limited to durable materials that can withstand physical force. | Limited to small parts, not effective for large surfaces. |
Cost Efficiency | High initial cost, but long-term savings on consumables. | Low initial cost, but recurring costs for chemicals. | Relatively low cost, but can incur surface damage costs. | Low initial and operating cost, but labor-intensive. | High cost due to specialized equipment and solutions. |
Ease of Use | Requires trained operators, but highly automated processes. | Moderate ease of use but requires safety precautions. | Easy to operate, but requires protective gear. | Easy to operate, but manual effort required. | Requires trained operators but easy to use once set up. |
Maintenance | Low maintenance, minimal consumables, long lifespan. | Requires regular chemical replenishment and waste management. | Frequent maintenance of blasting equipment and cleaning up dust. | Low maintenance, simple tools and machines. | Moderate maintenance, regular cleaning of the tank and solution replacement. |
Application of Laser Cleaning Contaminants
- Industrial Equipment Maintenance: Laser cleaning is highly effective for removing rust, oil, grease, and other residues from metal surfaces. It ensures that machinery and tools maintain optimal performance and longevity by keeping them free of harmful contaminants.
- Aerospace and Automotive: In industries where precision and cleanliness are crucial, laser cleaning is used to remove paint, coatings, and corrosion from metal parts without damaging the underlying surface. This process can help maintain structural integrity and prepare components for further processing (such as welding or painting).
- Heritage Conservation: Laser cleaning technology is gentle enough to be used in the restoration of historical artifacts and monuments. It removes accumulated dirt, pollution, and biological growth without causing damage, ensuring that delicate materials like stone, marble, and metal remain intact.
- Surface Preparation for Welding and Coating: In manufacturing, laser cleaning is ideal for surface preparation, ensuring contaminants like rust, oil, and oxides are removed before welding or applying coatings. This improves the quality of the final product and ensures strong adhesion during the coating process.
- Electronics and Precision Components: Laser cleaning is used to clean delicate electronic parts and precision components. It provides a non-contact, damage-free method of removing oxides and other residues from surfaces, ensuring that sensitive components remain functional.
- Marine and Shipbuilding: Laser cleaning is widely applied in the maritime industry to remove rust and marine growth from ships and offshore structures. It is highly effective in extending the lifespan of metal surfaces exposed to harsh environments.
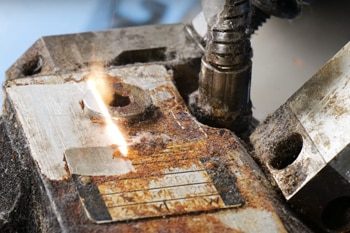
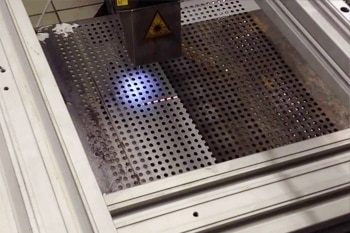
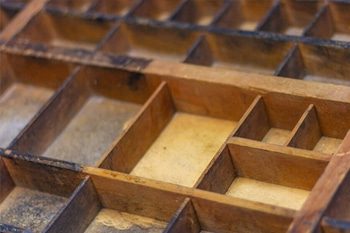
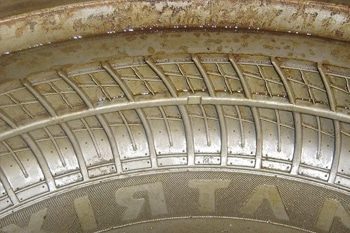
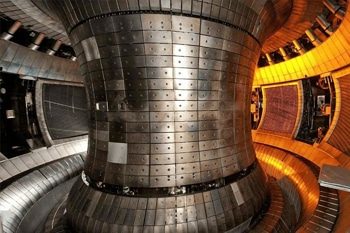
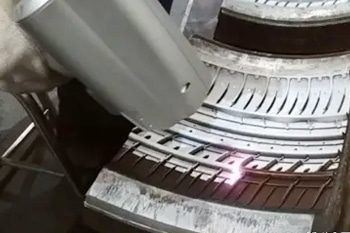
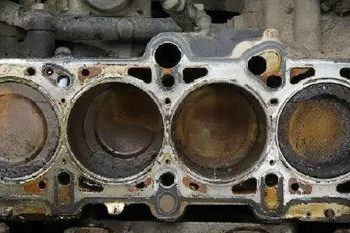
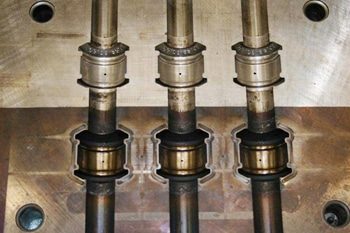