Laser Cleaning Composites
Composites Laser Cleaning Machine
-
Standard Continuous Laser Cleaning Machine
Rated 4.75 out of 5$3,200 – $6,600 This product has multiple variants. The options may be chosen on the product page -
Portable Continuous Laser Cleaning Machine
Rated 4.50 out of 5$3,100 – $6,500 This product has multiple variants. The options may be chosen on the product page -
Double Wobble Pulse Laser Cleaning Machine
Rated 4.75 out of 5$4,300 – $16,000 This product has multiple variants. The options may be chosen on the product page -
Luggage Pulse Laser Cleaning Machine
Rated 5.00 out of 5$6,300 – $16,800 This product has multiple variants. The options may be chosen on the product page -
Backpack Pulse Laser Cleaning Machine
Rated 4.75 out of 5$6,600 – $8,900 This product has multiple variants. The options may be chosen on the product page -
High Power Pulse Laser Cleaning Machine
Rated 4.75 out of 5$9,300 – $64,300 This product has multiple variants. The options may be chosen on the product page -
Double Wobble Continuous Laser Cleaning Machine
Rated 5.00 out of 5$3,700 – $7,100 This product has multiple variants. The options may be chosen on the product page
Benefits of Laser Cleaning Composites
Non-Contact Cleaning
Laser cleaning is a non-abrasive process that avoids physical contact, preserving the integrity and surface quality of delicate composite materials.
Eco-Friendly Solution
This method eliminates the need for harmful chemicals or abrasive materials, making it an environmentally friendly option that reduces waste and pollution.
Precise and Controlled Process
Laser cleaning offers precision, allowing the removal of contaminants layer by layer without damaging the underlying composite, ensuring accuracy in critical applications.
Minimal Material Wear
Unlike traditional methods, laser cleaning causes no wear and tear on the composite surface, extending the material’s lifespan and reducing maintenance needs.
Versatile Applications
Suitable for a variety of industries, laser cleaning can be used on different types of composites, making it adaptable for aerospace, automotive, and manufacturing sectors.
Reduced Operational Downtime
The high speed and efficiency of laser cleaning reduce operational downtime, enabling faster cleaning processes and improving overall productivity for businesses.
Factors to Consider Before Buying Composites Laser Cleaning Machines
Material Compatibility
Ensure the machine is compatible with the specific types of composite materials you use. Different composites may require varied laser settings to avoid damage.
Laser Power and Flexibility
Check the range of laser power and its adjustability. This flexibility allows you to tailor the cleaning process to different materials and contamination types.
Precision and Control
Evaluate the precision of the machine. Accurate control over parameters like pulse duration and frequency is crucial for effectively cleaning delicate composite surfaces.
Ease of Maintenance
Consider the ease of maintaining the machine. Regular maintenance should be straightforward to minimize downtime and extend the machine's operational lifespan.
Environmental Impact
Look for eco-friendly machines. Opt for models that reduce or eliminate the use of harmful chemicals and generate minimal waste during the cleaning process.
User-Friendliness
Assess the user interface and ease of operation. A machine with intuitive controls and comprehensive training will enhance efficiency and reduce the learning curve.
Safety Features
Ensure the machine includes robust safety features. Proper safeguards protect operators from potential hazards associated with laser technology and ensure a safe working environment.
Cost of Ownership
Consider the total cost of ownership, including initial purchase price, operating costs, and potential repairs. A cost-effective machine balances performance with long-term financial benefits.
Comparison with Other Composites Cleaning Methods
Feature | Laser Cleaning | Chemical Cleaning | Abrasive Cleaning | Mechanical Cleaning |
Surface Impact | Non-contact, preserves composite structure | May cause chemical damage to the surface | Risk of scratching or wearing the surface | Can cause surface wear and physical damage |
Precision | High precision, selective cleaning is possible | Low precision, affects the entire surface | Moderate, less precise for delicate areas | Low precision, difficult to control on composites |
Environmental Impact | Eco-friendly, no hazardous chemicals | Generates chemical waste | Generates dust and waste | Generates debris, may require water/lubricants |
Speed | Fast and efficient, with minimal downtime | Slow, requires soaking and rinsing | Moderate, depends on material and method | Slow, labor-intensive process |
Cost | Higher initial investment, lower long-term cost | Lower initial cost, high consumable expenses | Moderate cost, depending on abrasives | Lower cost, but higher maintenance due to wear |
Maintenance | Low, minimal wear on machine components | High, frequent replacement of chemicals | Moderate, abrasive material needs replacement | High, wear on tools and components |
Safety | Safe, no harmful substances or physical force | Hazardous chemicals pose safety risks | The risk of inhaling dust requires protection | Physical injury risk requires personal protective equipment (PPE) |
Application of Laser Cleaning Composites
- Aerospace Industry: Laser cleaning is essential in the aerospace industry for removing contaminants and coatings from composite materials used in aircraft. The precision of laser technology ensures that surfaces are cleaned without damaging the composite structure, which is crucial for maintaining safety and performance standards.
- Automotive Sector: In the automotive sector, laser cleaning prepares composite parts for further processing such as bonding and painting. This method removes residues efficiently without causing wear or degradation, ensuring high-quality and durable automotive components.
- Marine and Wind Energy Sectors: For the marine and wind energy sectors, laser cleaning helps maintain composites exposed to harsh conditions. It effectively removes rust, salt, and debris, extending the lifespan and performance of components like marine vessels and wind turbine blades.
- Manufacturing and Production: In manufacturing, laser cleaning keeps composite parts free from contaminants during production. This method avoids the use of chemicals or abrasives, enhancing cleanliness and operational efficiency, and ensuring high-quality output in industrial processes.
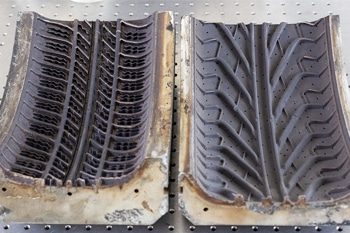
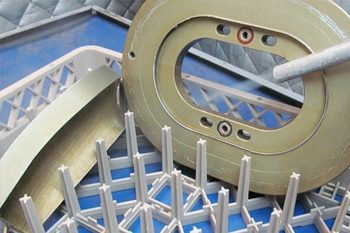
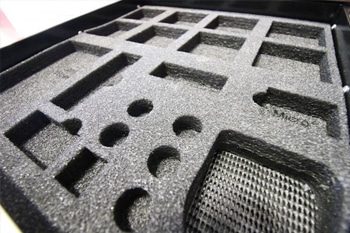
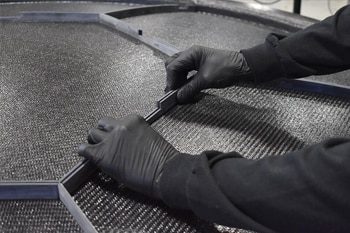
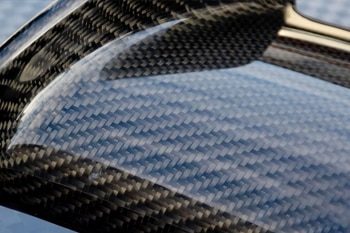
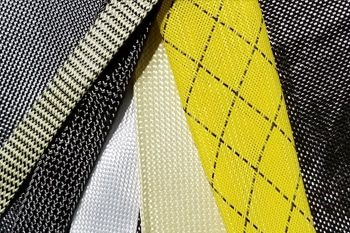
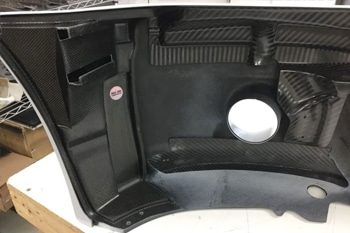
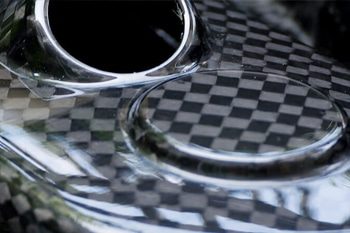