Laser Cleaning Burn Marks
Laser Cleaning Machines
-
Standard Continuous Laser Cleaning Machine
Rated 4.75 out of 5$3,200 – $6,600 This product has multiple variants. The options may be chosen on the product page -
Portable Continuous Laser Cleaning Machine
Rated 4.50 out of 5$3,100 – $6,500 This product has multiple variants. The options may be chosen on the product page -
Double Wobble Pulse Laser Cleaning Machine
Rated 4.75 out of 5$4,300 – $16,000 This product has multiple variants. The options may be chosen on the product page -
Luggage Pulse Laser Cleaning Machine
Rated 5.00 out of 5$6,300 – $16,800 This product has multiple variants. The options may be chosen on the product page -
Backpack Pulse Laser Cleaning Machine
Rated 4.75 out of 5$6,600 – $8,900 This product has multiple variants. The options may be chosen on the product page -
High Power Pulse Laser Cleaning Machine
Rated 4.75 out of 5$9,300 – $64,300 This product has multiple variants. The options may be chosen on the product page -
Double Wobble Continuous Laser Cleaning Machine
Rated 5.00 out of 5$3,700 – $7,100 This product has multiple variants. The options may be chosen on the product page
Benefits of Laser Cleaning Burn Marks
Non-Abrasive Process
Laser cleaning removes burn marks without physically impacting or damaging the underlying material, preserving surface integrity for sensitive applications.
Environmentally Friendly
Laser cleaning uses no harmful chemicals or solvents, making it an eco-friendly method that minimizes environmental impact and reduces the need for hazardous waste disposal.
Precision Cleaning
The laser can be finely tuned for precise removal of burn marks, ensuring thorough cleaning without affecting surrounding areas, ideal for intricate surfaces.
Low Maintenance
Laser cleaning systems require minimal maintenance and have low operational costs, reducing downtime and offering cost-efficient solutions for long-term use.
Enhanced Surface Quality
Laser cleaning not only removes burn marks but also enhances the overall surface quality by eliminating oxidation and contaminants, resulting in a cleaner, polished finish.
Versatility Across Materials
This method is effective on a wide range of materials, including metals, plastics, and ceramics, making it suitable for various industrial and delicate applications.
Factors to Consider Before Buying Laser Cleaning Machines
Material Compatibility
Ensure the machine is suitable for the materials you will be cleaning, such as metals, plastics, ceramics, or glass, to achieve effective results.
Laser Power
Higher-powered machines offer faster cleaning for deep or extensive burn marks, while lower-powered models work better for delicate surfaces and light marks.
Adjustable Settings
Look for machines with customizable settings, allowing you to adjust laser intensity and speed according to different material types and cleaning requirements.
Portability and Design
Consider whether a stationary or portable machine is needed based on your workspace. Maxcool CNC offers both stationary and portable options for flexibility.
Safety Features
Ensure the machine includes key safety features like an emergency stop, a protective enclosure, and a user-friendly interface to protect operators during operation.
Cost and Maintenance
Evaluate both the initial investment and long-term operational costs, including maintenance needs. Maxcool CNC’s machines are designed for durability and low maintenance.
Cleaning Speed
Faster cleaning speeds are essential for large-scale operations. Ensure the machine provides efficient cleaning without sacrificing precision, especially for industrial applications.
Energy Efficiency
Choose a machine that balances cleaning performance with energy consumption, minimizing operational costs while delivering high-efficiency burn mark removal.
Comparison with Other Cleaning Burn Marks Methods
Feature | Laser Cleaning | Chemical Cleaning | Abrasive Blasting | Manual Scrubbing |
Precision | High precision, customizable for different materials and burn depths | Moderate precision can cause material damage if not controlled | Low precision, may affect surrounding areas | Low precision, dependent on manual skill |
Environmental Impact | Eco-friendly, no chemicals or waste produced | Harmful, uses chemicals, and generates hazardous waste | Dust and debris production | Low environmental impact, but uses consumables |
Surface Damage Risk | Non-abrasive, no damage to the underlying material | Risk of corrosion or surface degradation | High risk of surface damage | Can cause scratching or surface wear |
Efficiency | High speed, minimal setup, suitable for large surfaces | Moderate, requires time for chemical reactions | High speed, but requires extensive setup | Low efficiency, time-consuming for large areas |
Operating Cost | Low operating cost, minimal consumables | High cost of chemicals and disposal | Moderate cost for abrasives and equipment | Low-cost, but labor-intensive |
Safety | High safety with built-in features like enclosures | Health hazards from chemical exposure | Risk of inhaling dust or abrasives | Low safety risk, but can lead to physical strain |
Maintenance | Low maintenance, minimal wear and tear | High, due to chemical storage and equipment cleaning | Moderate, equipment requires upkeep | Low maintenance, depends on tool condition |
Application of Laser Cleaning Burn Marks
- Metal Fabrication: Laser cleaning is commonly used in metalworking industries to remove burn marks caused by welding, cutting, or heat treatment processes. It ensures a smooth and clean surface, enhancing the appearance and quality of the finished product.
- Automotive Industry: In automotive manufacturing, laser cleaning effectively removes burn marks from vehicle components, such as engine parts, exhaust systems, and body panels. This helps in ensuring that the components maintain their structural integrity and visual appeal.
- Aerospace: Aerospace parts often undergo high-temperature processes that can leave burn marks. Laser cleaning ensures these surfaces are restored without affecting the precision or safety standards required for critical components in aircraft manufacturing.
- Electronics: Laser cleaning is used to remove burn marks from delicate electronic components, such as circuit boards and connectors. Its non-abrasive nature prevents damage to sensitive parts, making it ideal for electronics manufacturing and repair.
- Glass and Ceramics: Laser cleaning is also applied to remove burn marks from glass and ceramics, restoring clarity and smoothness without scratching or damaging the surface, making it useful in industries like construction and art restoration.
- Maintenance and Repair: Laser cleaning is valuable for restoring and maintaining surfaces in industrial settings, such as refineries, power plants, and factories, where burn marks may occur due to high-temperature operations.
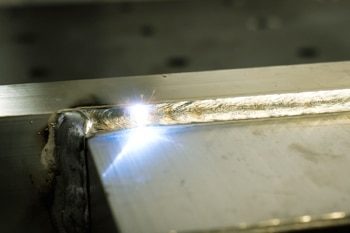
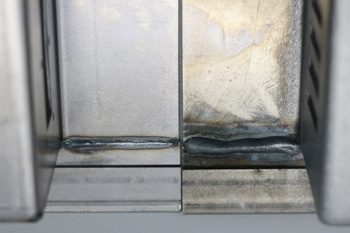
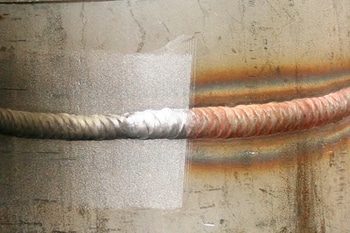
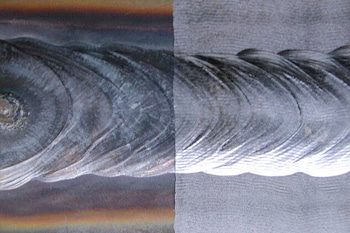
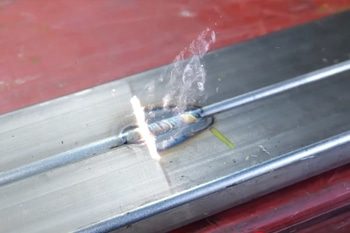
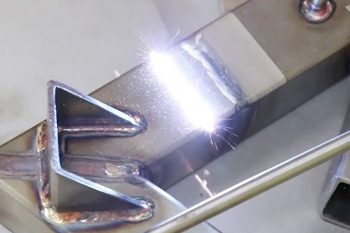
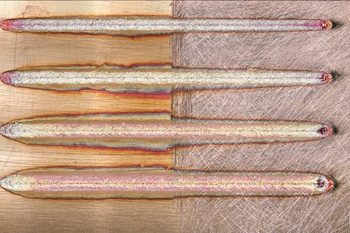
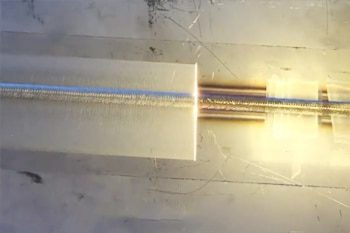