Introduction
Available Models
-
Standard Continuous Laser Cleaning Machine
Rated 4.75 out of 5$3,200 – $6,600 This product has multiple variants. The options may be chosen on the product page -
Portable Continuous Laser Cleaning Machine
Rated 4.50 out of 5$3,100 – $6,500 This product has multiple variants. The options may be chosen on the product page -
High Power Pulse Laser Cleaning Machine
Rated 4.75 out of 5$9,300 – $64,300 This product has multiple variants. The options may be chosen on the product page -
Double Wobble Continuous Laser Cleaning Machine
Rated 5.00 out of 5$3,700 – $7,100 This product has multiple variants. The options may be chosen on the product page
Application
Wood laser cleaning machines are advanced tools designed to handle a variety of cleaning and restoration tasks for wooden surfaces. Their precision and eco-friendly operation make them suitable for a wide range of applications, including:
- Historical Restoration: Restore antique wooden structures, furniture, and artifacts by safely removing dirt, grime, and old coatings without damaging intricate details or the natural texture.
- Paint and Coating Removal: Strip old paint, varnish, or surface coatings from wooden surfaces to prepare them for refinishing or repurposing, ensuring a clean and smooth finish.
- Furniture Refinishing: Clean and refurbish wooden furniture by removing stains, discoloration, and old finishes, preserving the wood’s natural beauty for restoration projects.
- Architectural Conservation: Maintain and restore wooden beams, panels, and facades in heritage buildings and modern architecture by removing accumulated contaminants and weathering effects.
- Surface Preparation: Prepare wood surfaces for painting, staining, or other treatments by removing residues, adhesives, or minor imperfections, ensuring an even and high-quality finish.

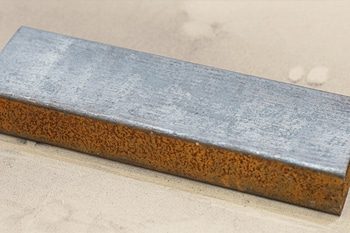
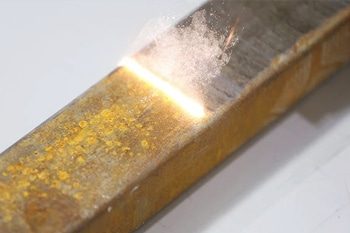
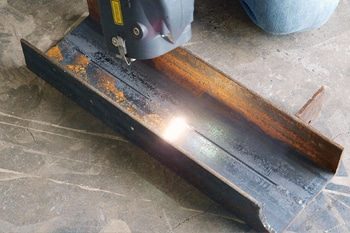

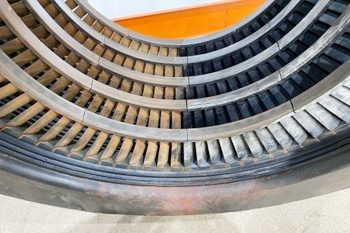
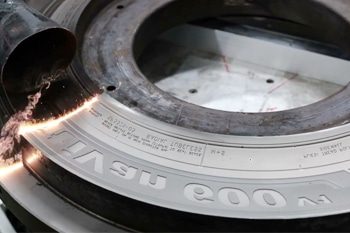
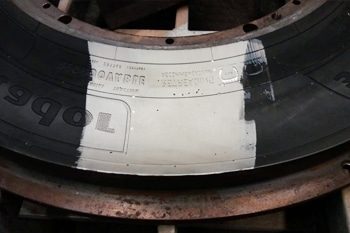
Comparison with Traditional Cleaning Methods
Feature | Laser Cleaning | Sandblasting | Chemical Cleaning | Ultrasonic Cleaning |
Precision | High precision, preserves wood texture and detail | Low precision, can damage delicate wood grains | Limited precision, risk of residue or discoloration | Not suitable for large wood surfaces |
Environmental Impact | Eco-friendly, no chemicals or abrasives used | Generates dust and abrasive waste | Uses harsh chemicals, creates toxic waste | Generally eco-friendly, but requires detergents |
Cleaning Speed | Fast and efficient, adaptable to small and large surfaces | Moderate, can be slow on intricate woodwork | Slow, involves soaking and rinsing | Moderate, best for small, intricate parts |
Setup Time | Minimal setup, ready to use quickly | Requires setup of abrasive materials and equipment | Involves chemical preparation and safety measures | Requires preparation of cleaning solutions and tanks |
Safety | Non-contact, safe for wood surfaces and operators | Risks damage to wood and requires PPE for operators | Exposure to harmful chemicals, and strict handling needed | Generally safe, but limited for wood cleaning |
Waste Generation | Minimal, produces only vaporized particles | Significant abrasive waste and residue | Produces hazardous chemical waste | Minimal, but the used solution needs disposal |
Surface Compatibility | Suitable for all wood types, including delicate and antique wood | Abrasive, unsuitable for soft or aged wood | Can cause discoloration or harm sensitive wood | Not ideal for porous wood or large surfaces |
Portability | Compact, portable models available for on-site use | Bulky equipment, not easily portable | Fixed setups, not portable | Requires stationary tank setup |
Operating Cost | Low long-term cost, no consumables required | Moderate, requires a constant supply of abrasives | High, continuous purchase of chemicals | Moderate, depends on cleaning solution usage |
Durability | Durable components, minimal maintenance required | Equipment prone to wear from abrasives | Chemicals degrade over time, and frequent replacement is needed | Regular maintenance of equipment and solutions |
Why Choose Us
Cutting-Edge Technology
Maxcool CNC is committed to integrating the latest technological advancements into our machines. Our laser cleaning machines feature precise control, high efficiency, and superior performance, ensuring optimal cleaning results for various industrial applications.
Reliable and Durable Equipment
Our machines are built to last, with robust construction and high-quality components that guarantee long-term reliability and minimal maintenance. You can trust Maxcool CNC to provide equipment that withstands even the toughest environments.
Comprehensive Support
From pre-sales consultation to after-sales technical assistance, we are with you every step of the way. Our dedicated support team ensures you have all the information and help you need to maximize the value of your investment.
Sustainability and Efficiency
Maxcool CNC’s laser cleaning machines are designed with energy efficiency in mind, reducing power consumption without compromising performance. This not only lowers operational costs but also contributes to a more sustainable future.
Customer Reviews
Frequently Asked Questions
What Types of Contaminants Can Wood Laser Cleaning Machines Remove?
What Types of Wood Can Be Cleaned With Laser Cleaning Machines?
Can Laser Cleaning Damage The Wood Surface?
How Fast Can Wood Laser Cleaning Machines Clean a Surface?
What Safety Precautions Are Needed When Using Wood Laser Cleaning Machines?
Does Laser Cleaning Produce Waste or Residues?
Related Resources

What Is Pulse Laser Cleaning?
This article explains how pulse laser cleaning works, explores its applications, and learn how it effectively removes contaminants while maintaining the integrity and quality of the substrate.
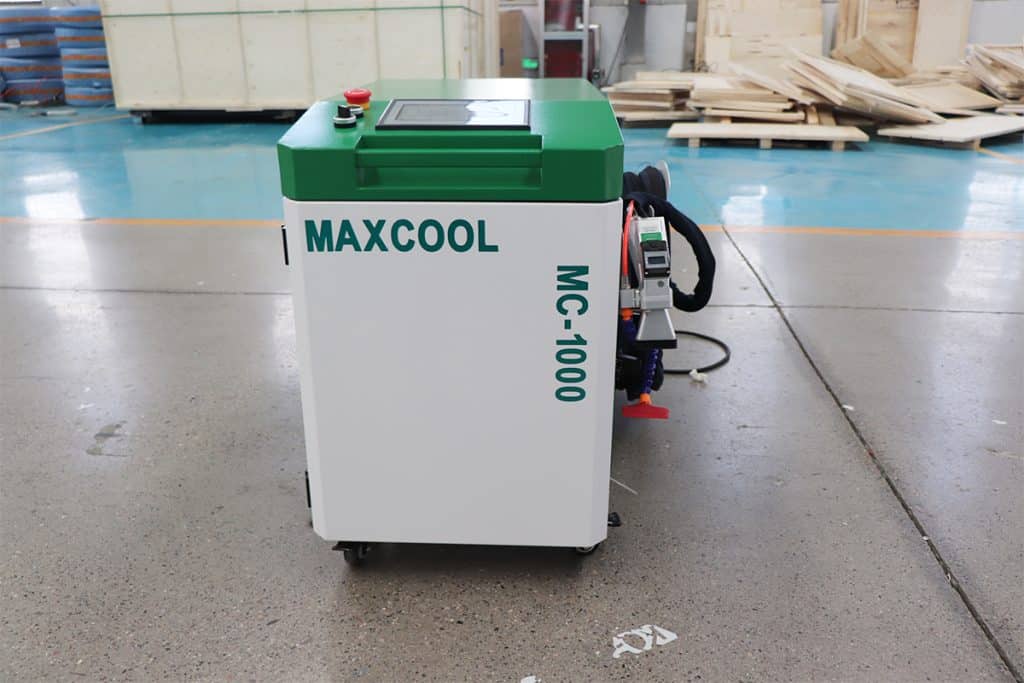
How Laser Parameters Affect the Cleaning Process?
This article explores how laser parameters like wavelength, pulse duration, energy, and scanning speed influence the efficiency and outcome of the laser cleaning process.
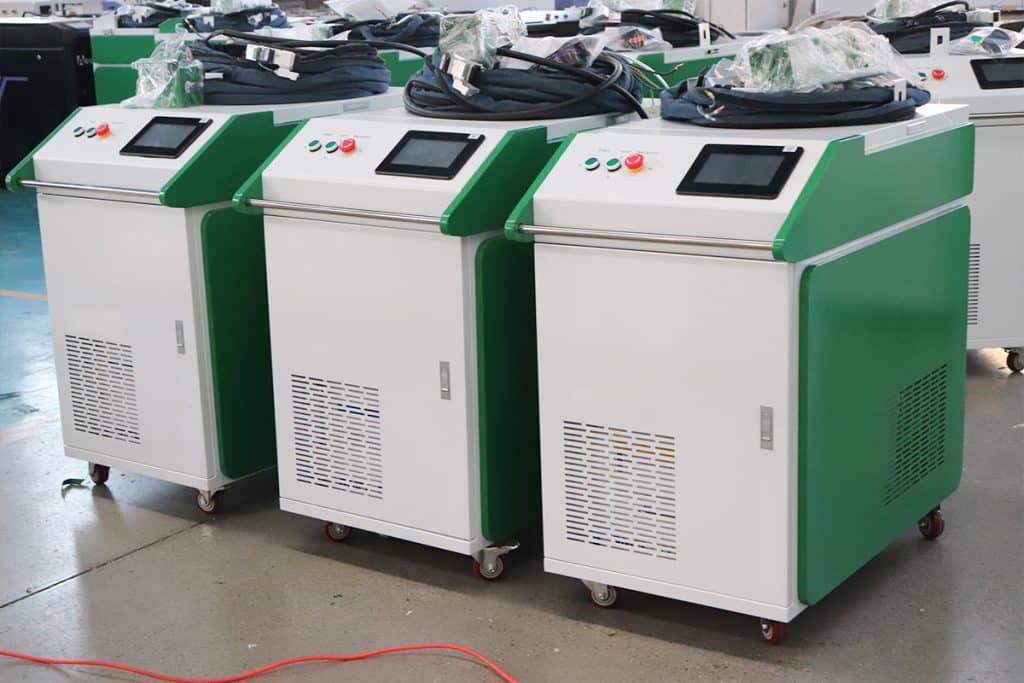
Laser Rust Removal VS Electrolytic Rust Removal
This article explores how laser and electrolytic methods can remove rust, detailing their principles, advantages, disadvantages, and typical applications for effective corrosion control.