Introduction
Available Models
-
Standard Continuous Laser Cleaning Machine
Rated 4.75 out of 5$3,200 – $6,600 This product has multiple variants. The options may be chosen on the product page -
Portable Continuous Laser Cleaning Machine
Rated 4.50 out of 5$3,100 – $6,500 This product has multiple variants. The options may be chosen on the product page -
Double Wobble Continuous Laser Cleaning Machine
Rated 5.00 out of 5$3,700 – $7,100 This product has multiple variants. The options may be chosen on the product page
Application
The 2000w laser cleaning machine is engineered for the most demanding industrial cleaning applications, offering exceptional power and precision. Its advanced capabilities make it an indispensable tool across a variety of industries. Key applications include:
- Heavy Rust and Corrosion Removal: Easily removes thick rust and corrosion layers from large surfaces, restoring their structural integrity and appearance.
- Thick Paint and Coating Removal: Strips durable coatings, including paint and varnish, with high efficiency and precision, ideal for restoration and preparation.
- Oil, Grease, and Residue Cleaning: Cleans industrial equipment and machinery by eliminating stubborn oils, grease, and other contaminants.
- Weld Seam Cleaning: Removes oxidation, discoloration, and residues from welds, ensuring improved strength and aesthetics.
- Surface Preparation: Prepares surfaces for processes like painting, welding, or bonding, ensuring optimal results.

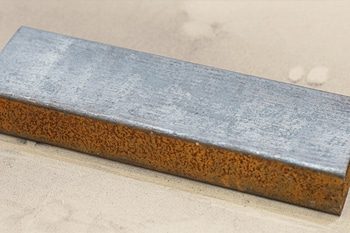
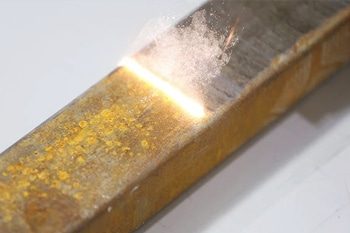
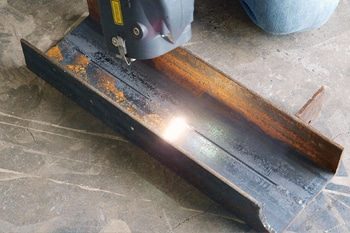

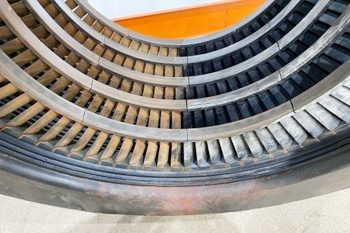
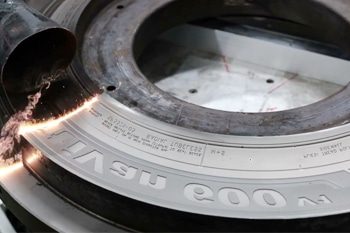
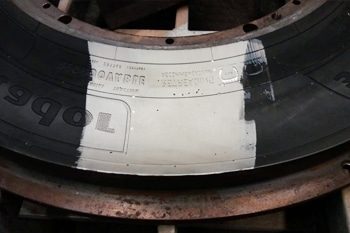
Comparison with Traditional Cleaning Methods
Aspect | Laser Cleaning | Sandblasting | Chemical Cleaning | Ultrasonic Cleaning |
Contact with Surface | Non-contact, no physical abrasion | Contact-based, abrasive material impacts the surface | Non-contact, but chemicals may react with the surface | Non-contact, but uses cavitation bubbles in a liquid medium |
Environmental Impact | Eco-friendly, no chemicals or solvents used | Generates dust and airborne particles, which can be harmful | Often uses toxic chemicals, generates hazardous waste | Requires disposal of used cleaning fluids |
Precision and Control | High precision, selective cleaning of specific areas | Less precise, may erode the surface or surrounding material | Limited precision, can affect the entire surface | High precision but limited to small, submerged parts |
Surface Integrity | Preserves surface integrity, ideal for sensitive materials | Can damage or roughen the surface, especially on delicate materials | Can cause chemical reactions that may alter surface properties | Generally preserves surface but not suitable for all materials |
Residue and Waste | Minimal residue, no secondary waste | Leaves abrasive particles as waste | Leaves chemical residues, produces secondary waste | Leaves contaminants in the cleaning solution |
Maintenance and Downtime | Low maintenance, minimal downtime | Requires regular replenishment of abrasive material and equipment wear | Frequent chemical replacement and safety measures needed | Requires regular maintenance of ultrasonic equipment |
Safety | Safer for workers, no harmful chemicals or particles | Risk of inhalation and physical harm from abrasive particles | Risk of chemical burns, inhalation, and environmental contamination | Safer, but risks associated with handling and disposing of cleaning fluids |
Versatility | Suitable for a wide range of materials and industries | Primarily used for robust materials, not ideal for delicate surfaces | Versatile, but limited by chemical compatibility with materials | Limited to small parts that can be submerged in the cleaning tank |
Cost-Effectiveness | Higher initial cost but cost-effective in the long term | Lower initial cost but higher ongoing expenses due to abrasive consumption | Low initial cost but high cost for chemicals and disposal | Moderate cost, but limited to specific applications |
Operational Speed | Fast and efficient, reduces overall cleaning time | Can be slow, especially on large or intricate surfaces | Varies depending on chemical reaction time and safety protocols | Fast for small items, but limited by the size of the ultrasonic tank |
Why Choose Us
Cutting-Edge Technology
Maxcool CNC is committed to integrating the latest technological advancements into our machines. Our laser cleaning machines feature precise control, high efficiency, and superior performance, ensuring optimal cleaning results for various industrial applications.
Reliable and Durable Equipment
Our machines are built to last, with robust construction and high-quality components that guarantee long-term reliability and minimal maintenance. You can trust Maxcool CNC to provide equipment that withstands even the toughest environments.
Comprehensive Support
From pre-sales consultation to after-sales technical assistance, we are with you every step of the way. Our dedicated support team ensures you have all the information and help you need to maximize the value of your investment.
Sustainability and Efficiency
Maxcool CNC’s laser cleaning machines are designed with energy efficiency in mind, reducing power consumption without compromising performance. This not only lowers operational costs but also contributes to a more sustainable future.
Customer Reviews
Frequently Asked Questions
What are the advantages of using laser cleaning machines compared to traditional methods?
Laser cleaning offers several benefits over traditional cleaning methods such as sandblasting, chemical cleaning, or mechanical cleaning. These benefits include:
- Eco-friendly: No use of chemicals or abrasive materials, making it environmentally friendly.
- Precision: Laser cleaning provides highly precise control over the area being cleaned.
- Minimal wear on the substrate: Since it’s a non-contact method, there’s less physical damage to the underlying material.
- Cost efficiency in the long term: Although initial investment may be high, it reduces the need for consumables and lowers maintenance costs.
- Safety: There’s no dust or toxic waste, which reduces health risks for workers.
How efficient are 2000W laser cleaning machines?
What safety precautions should be taken when using a 2000W laser cleaning machine?
Safety is a top priority when using a laser cleaning machine. Some important precautions include:
- Protective eyewear: Operators must wear laser safety glasses to protect their eyes from harmful laser beams.
- Ventilation: Good ventilation is necessary to remove fumes generated by the cleaning process.
- Protective barriers: Fencing or shields should be used to protect operators and other personnel from accidental exposure to the laser.
- Training: Operators should undergo proper training to ensure safe operation and understanding of the equipment.
- Fire safety: The machine should be used in environments where flammable materials are not present, as lasers can generate heat.
What are the maintenance requirements for 2000W laser cleaning machines?
Maintenance for a 2000W laser cleaning machine includes regular checks on the laser source, cooling system, optics, and power supply. Operators should:
- Clean the lens and mirrors to ensure optimal performance.
- Monitor the cooling system to prevent overheating.
- Inspect the laser system for wear and tear.
- Perform software updates if applicable.
- Conduct periodic calibration of the laser to maintain precision.
What is the lifespan of 2000W laser cleaning machines?
How do I choose the right laser cleaning machine for my needs?
When choosing a laser cleaning machine, consider factors such as:
- Power requirements: Higher wattages, like the 2000W, are ideal for heavy-duty cleaning tasks.
- Material type: Make sure the machine is suitable for the materials you need to clean.
- Cleaning area size: A machine with a larger cleaning head or scanning area is better for larger surfaces.
- Portability: If you need a mobile solution, choose a laser cleaner with a compact design and easy-to-move features.
- Budget: Evaluate the total cost, including maintenance and operational costs, of your cleaning needs.
Related Resources
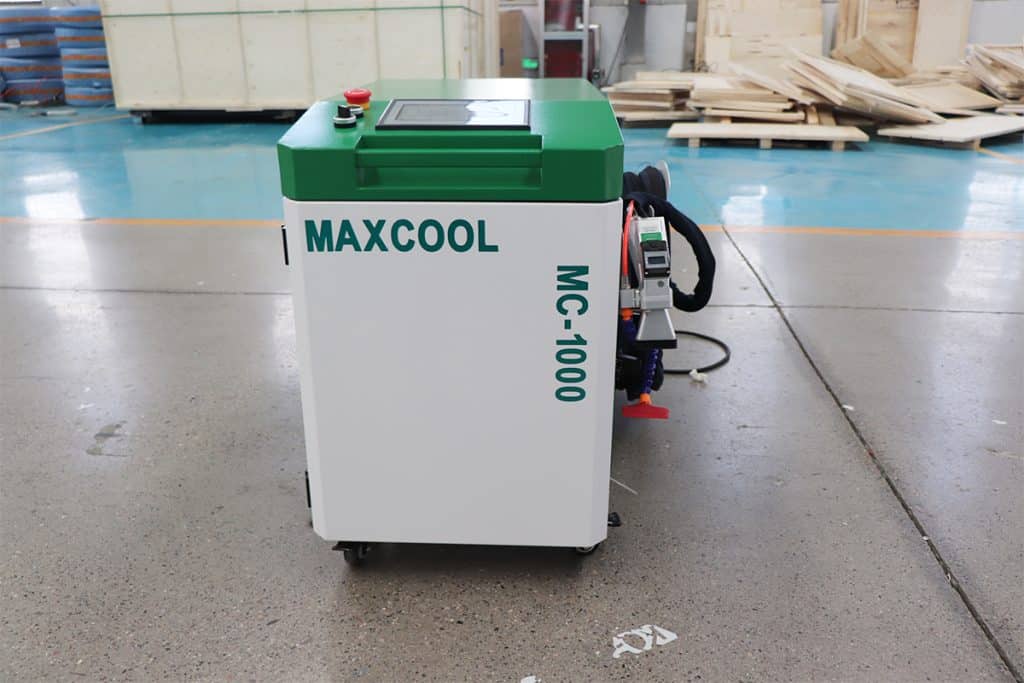
How Laser Parameters Affect the Cleaning Process?
This article explores how laser parameters like wavelength, pulse duration, energy, and scanning speed influence the efficiency and outcome of the laser cleaning process.
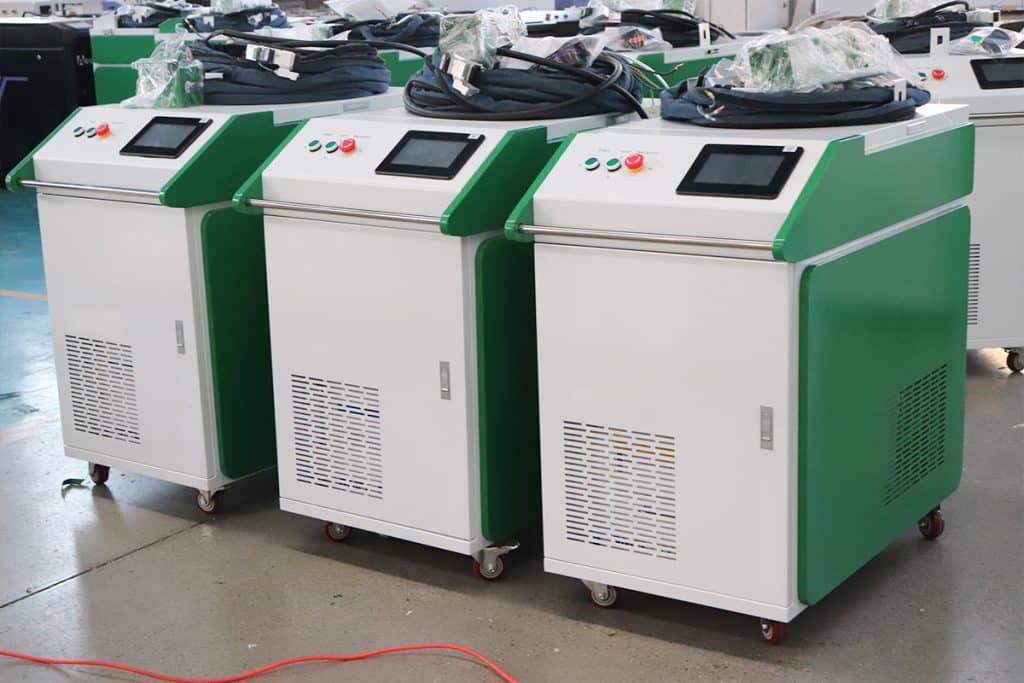
Laser Rust Removal VS Electrolytic Rust Removal
This article explores how laser and electrolytic methods can remove rust, detailing their principles, advantages, disadvantages, and typical applications for effective corrosion control.
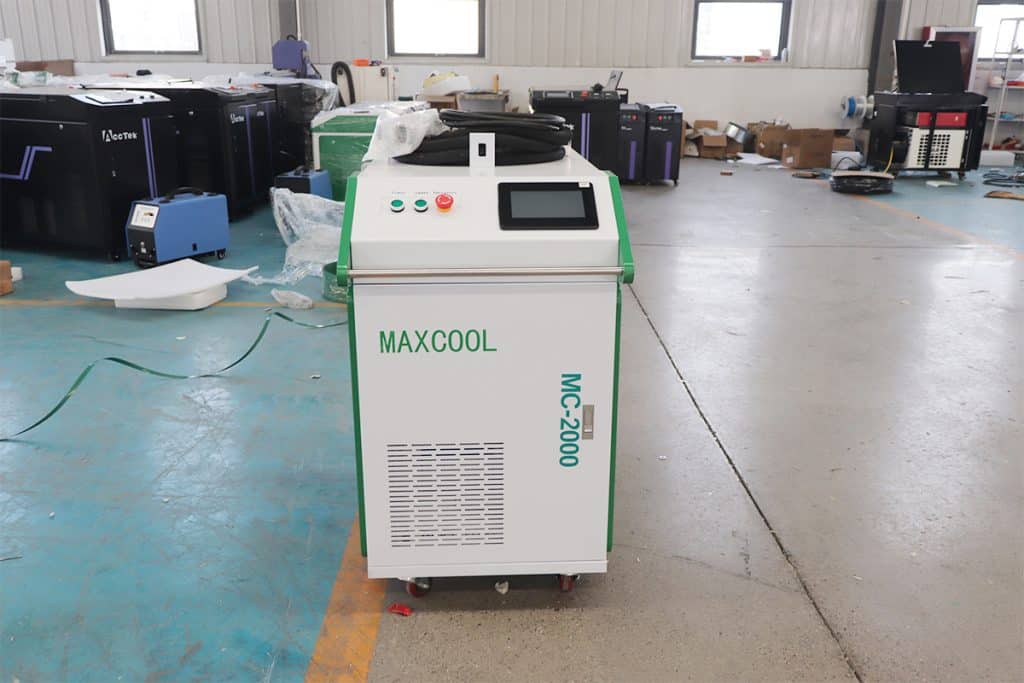
Is Laser Cleaning Eco-Friendly?
This article provides an in-depth analysis of the environmental friendliness of laser cleaning to help you understand the differences between laser cleaning and traditional methods in terms of waste reduction,