Introduction to Laser Cleaning
Common Applications of Laser Cleaning
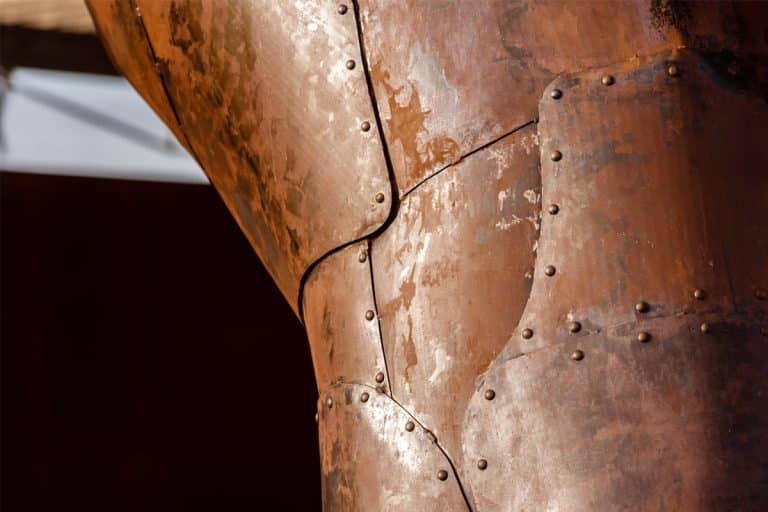
Rust
Effortlessly remove rust with advanced laser cleaning. Our technology offers precision, efficiency, and eco-friendly rust removal for metals, ensuring surfaces are restored without damage.
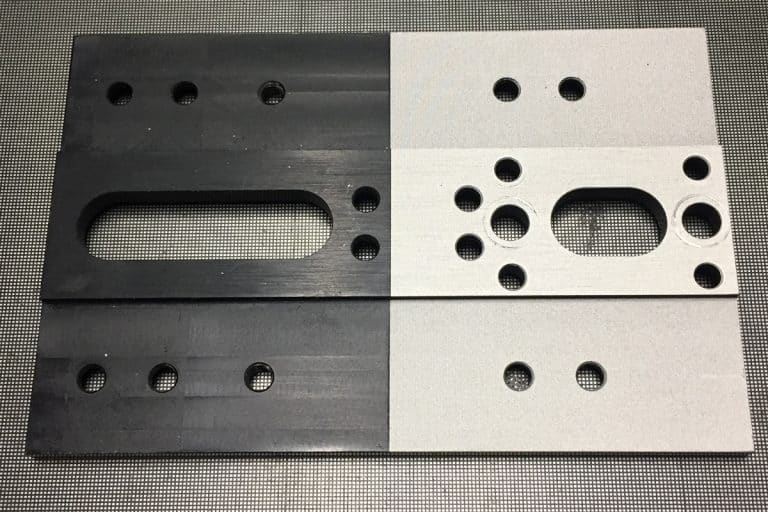
Paint
Easily remove paint with advanced laser cleaning. Our technology removes paint from surfaces without causing any damage, ensuring a clean, flawless surface for a variety of materials.
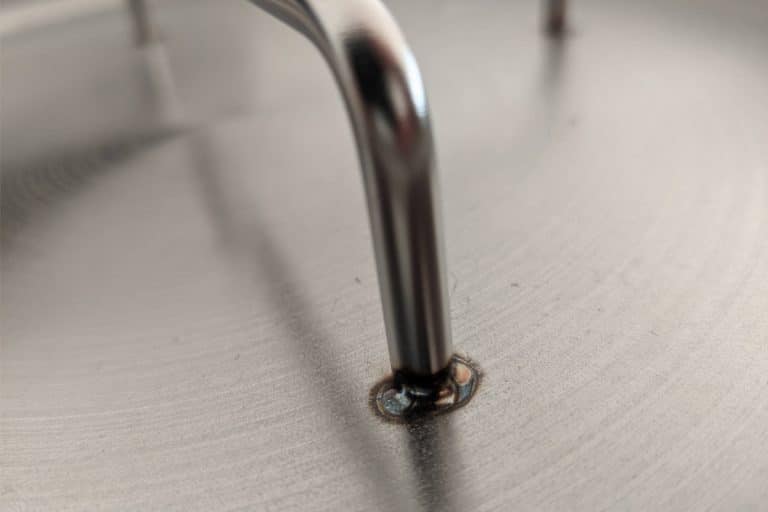
Oxide Layers
Effortlessly remove oxide layers with advanced laser cleaning. Our technology provides precise, efficient, and eco-friendly removal of oxide layers from metals, ensuring surfaces are restored to their original condition without causing any damage.
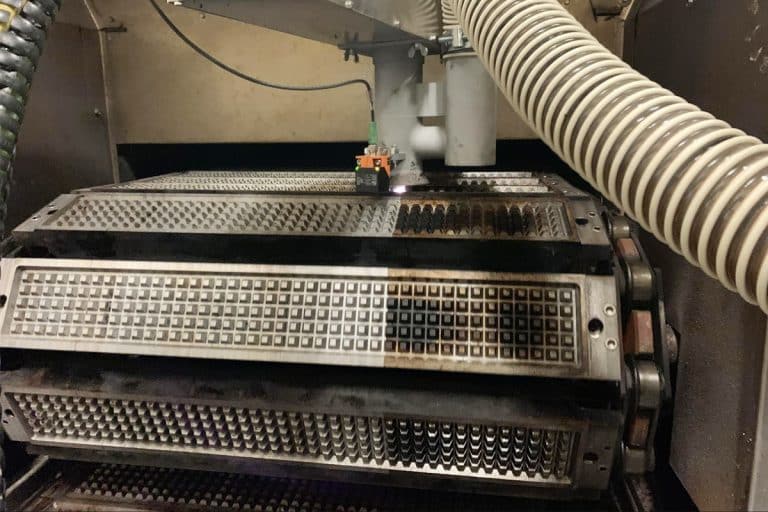
Oil and Grease
Our machines effectively remove stubborn grease residues from a wide range of surfaces, leaving them clean for further processing. Experience thorough, non-destructive cleaning solutions for all your processing needs.
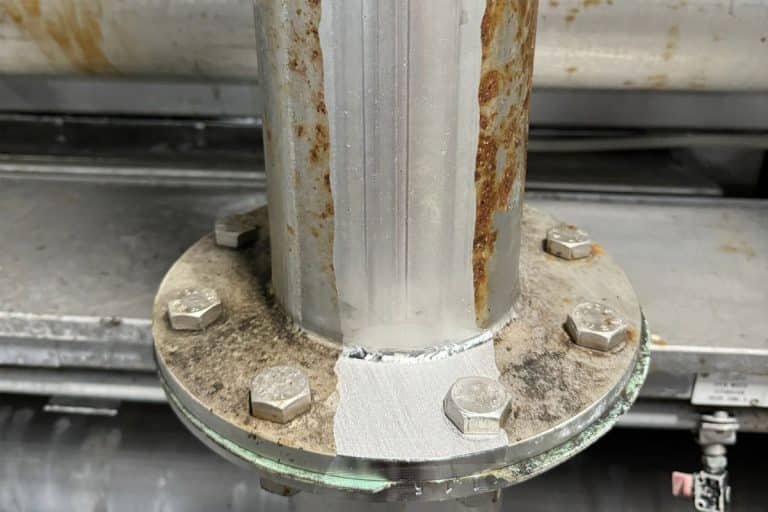
Contaminants
Maxcool CNC offers advanced laser cleaning solutions for removing rust, paint, oil, and contaminants from various surfaces, ensuring precise, eco-friendly, and efficient cleaning results.
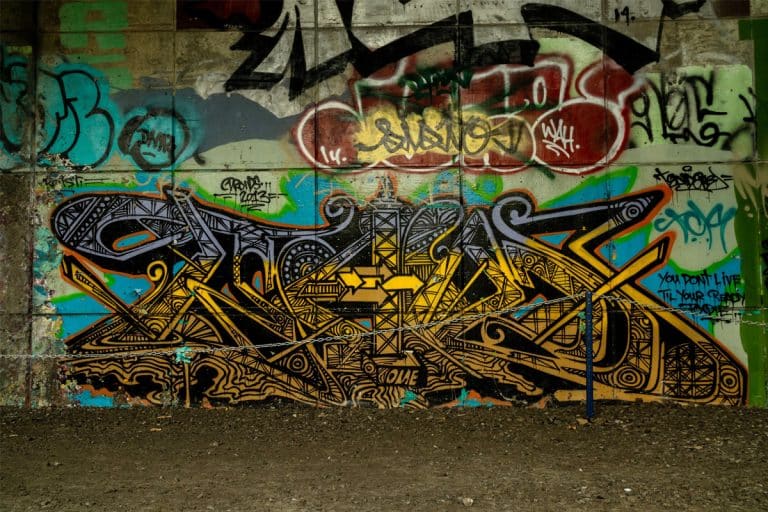
Graffiti
Maxcool CNC offers advanced laser graffiti cleaning solutions, providing eco-friendly, precise removal of graffiti from various surfaces without causing damage or using harmful chemicals.
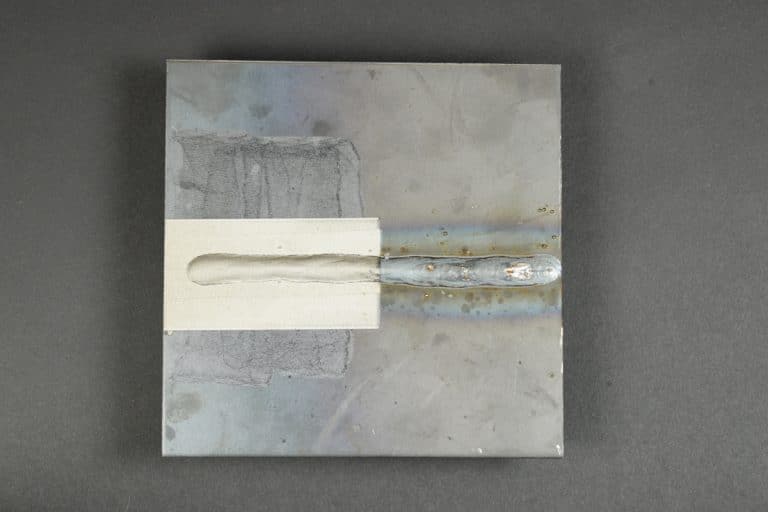
Burn Marks
Maxcool CNC’s laser cleaning machines offer an efficient, eco-friendly solution for removing burn marks from various materials, ensuring precision and surface integrity.
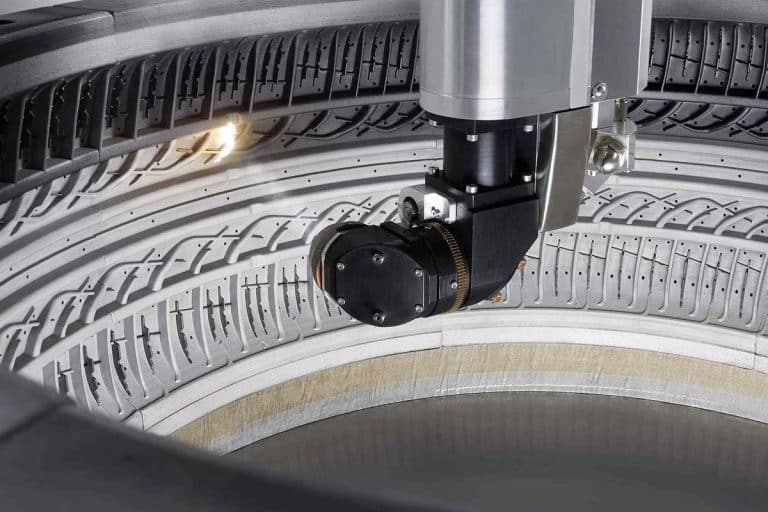
Residues
Maxcool CNC’s laser cleaning machines provide efficient, eco-friendly residue removal solutions for rust, paint, oil, and more, preserving surface integrity across various industries.
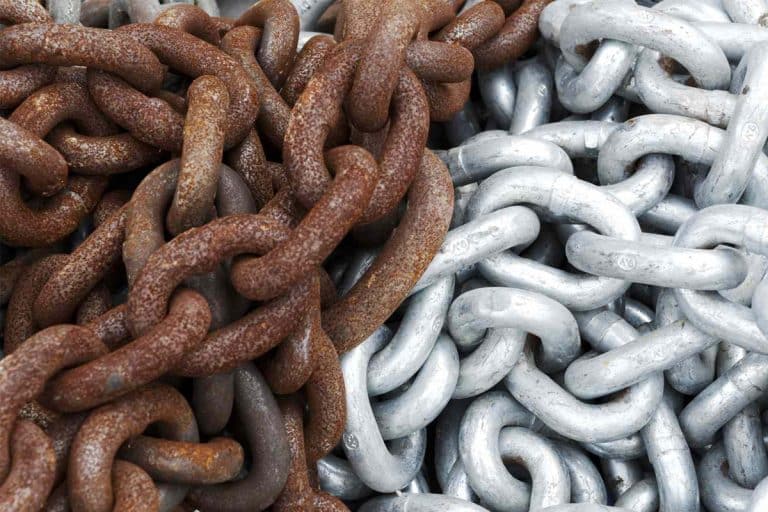
Metal
Maxcool CNC’s laser cleaning machines provide efficient, eco-friendly solutions for metal surface cleaning, removing rust, paint, and contaminants with precision and without damage.
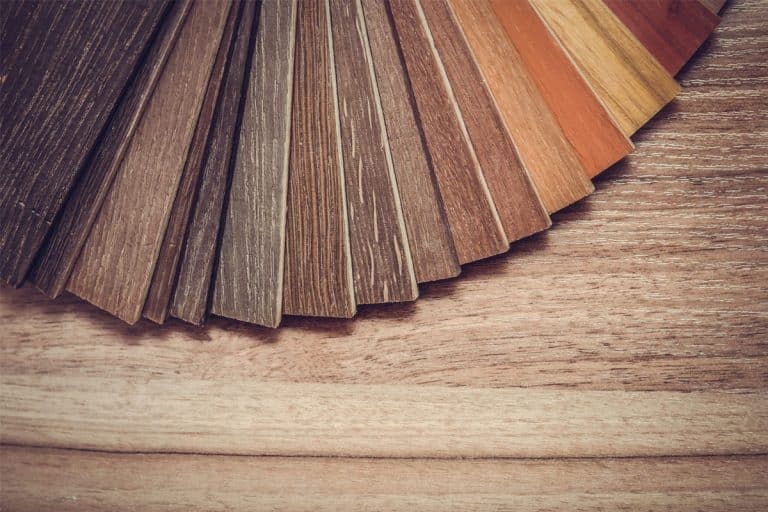
Wood
Maxcool CNC’s laser cleaning machines provide a precise, non-abrasive, and eco-friendly solution for restoring and cleaning wood surfaces, preserving their natural beauty and integrity.
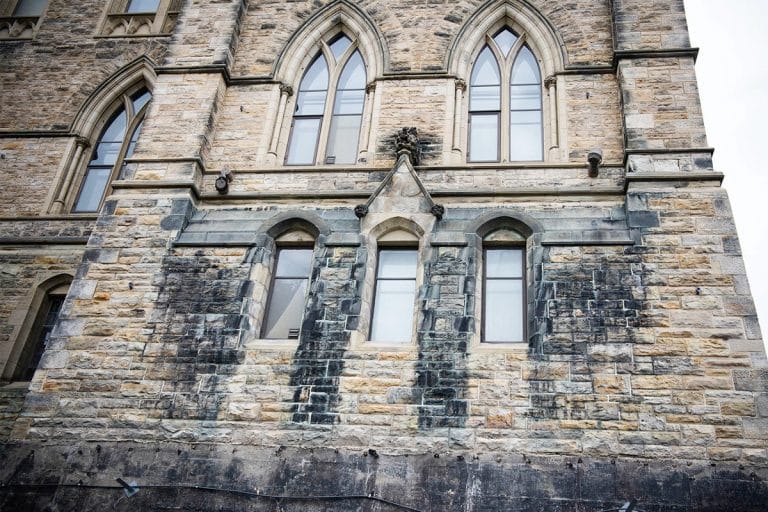
Stone
Maxcool CNC’s laser cleaning machines provide an eco-friendly, non-abrasive solution for efficiently cleaning and restoring stone surfaces, ideal for historical, industrial, and architectural applications.
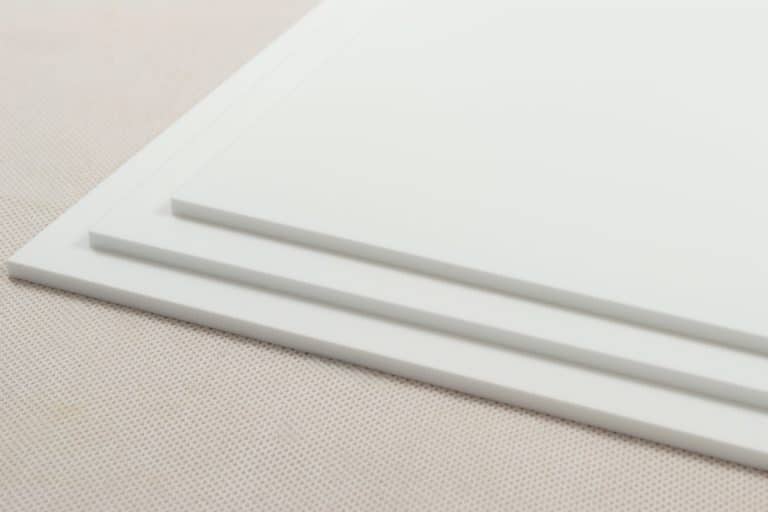
Plastic
Maxcool CNC’s laser cleaning machines offer precise, non-contact solutions for removing contaminants from plastic surfaces without damage, ensuring efficiency and environmental safety.
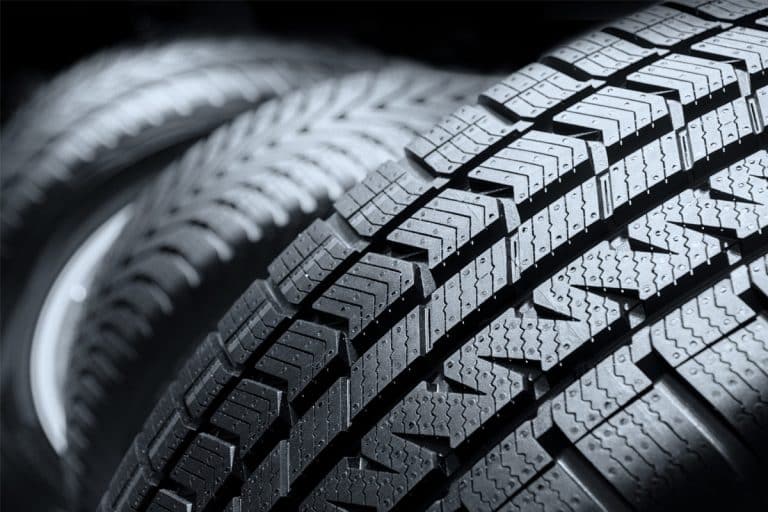
Rubber
Maxcool CNC’s laser cleaning machines offer a precise, eco-friendly solution for removing rubber residues from surfaces, ensuring efficient, non-abrasive cleaning for industrial applications.
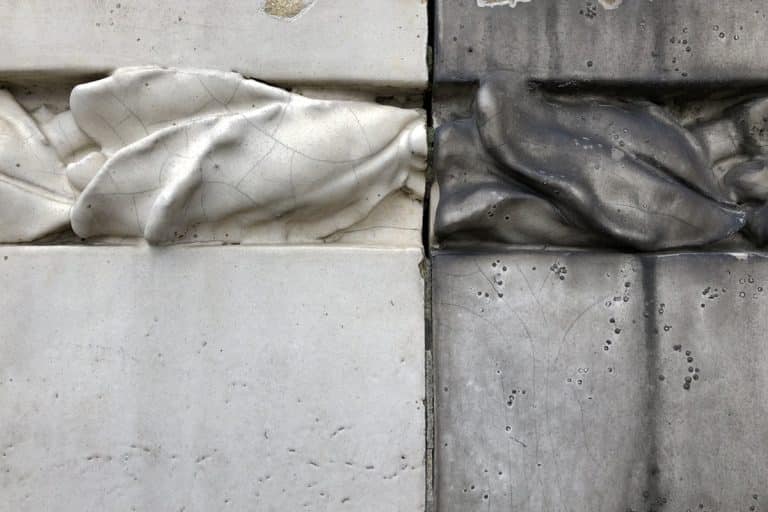
Concrete
Maxcool CNC’s laser cleaning technology provides a precise, eco-friendly solution for efficiently removing contaminants from concrete surfaces without causing damage.
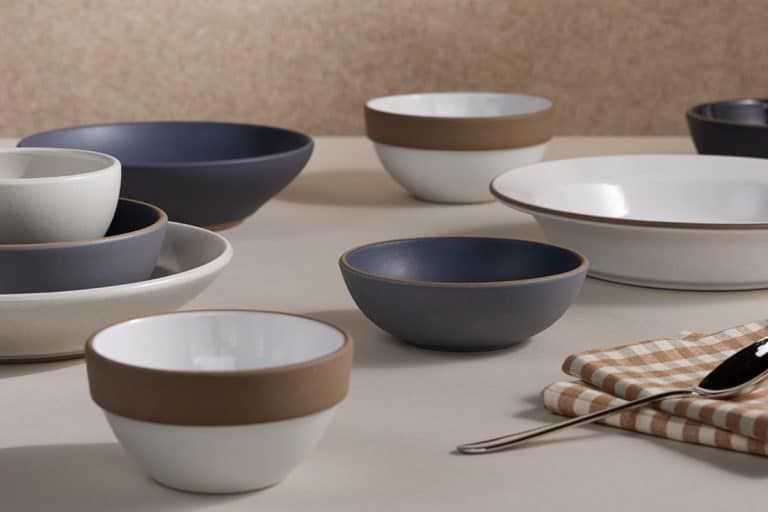
Ceramics
Laser cleaning ceramics offers a precise, non-destructive method for removing contaminants, ensuring high efficiency and surface protection across various industries.
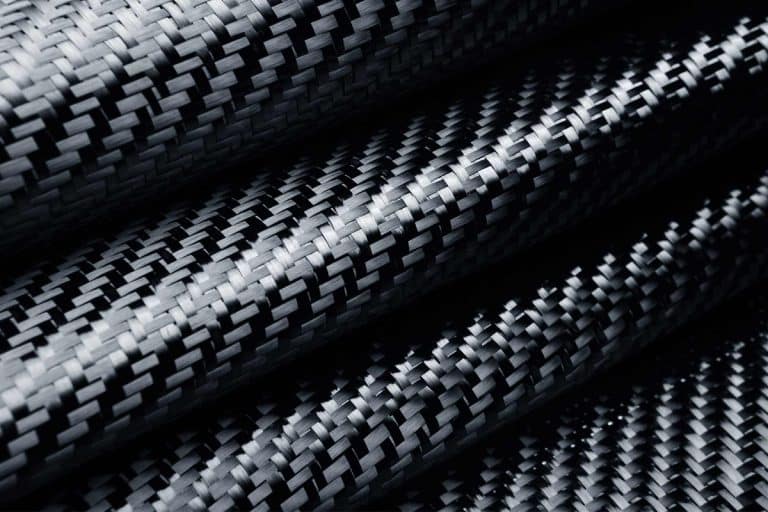
Composites
Maxcool CNC’s laser cleaning technology provides efficient, non-abrasive solutions for removing contaminants from composite materials, enhancing performance and durability across industries.
Advantages of Using Laser Cleaning
Non-Contact Process
Laser cleaning is a non-abrasive method that preserves the integrity of delicate surfaces, making it ideal for industries like aerospace and electronics.
Environmentally Friendly
This green technology eliminates the need for harsh chemicals, reducing environmental impact and minimizing worker exposure to harmful substances. It also produces minimal waste.
Precision and Control
Laser cleaning offers precise control, selectively removing contaminants without damaging surrounding material, which is essential for high-accuracy applications like artifact restoration and intricate component cleaning.
Cost-Effective
Though the initial cost is higher, laser cleaning saves money in the long run by reducing consumables, minimizing downtime, and extending the life of machinery and components.
Versatility
Applicable to various materials such as metals, plastics, and ceramics, laser cleaning meets diverse industry needs, from automotive to cultural heritage conservation.
Low Maintenance
Laser cleaning systems are durable, require minimal upkeep, and complete tasks quickly, reducing downtime and boosting productivity.
Safety
Laser cleaning is safer for workers, eliminating risks associated with harmful chemicals and abrasive particles.
Minimal Residue
Laser cleaning leaves little to no residue, crucial for industries where surface purity, like in electronics or food processing, is vital.
Comparison with Traditional Cleaning Methods
Aspect | Laser Cleaning | Sandblasting | Chemical Cleaning | Ultrasonic Cleaning |
Contact with Surface | Non-contact, no physical abrasion | Contact-based, abrasive material impacts the surface | Non-contact, but chemicals may react with the surface | Non-contact, but uses cavitation bubbles in a liquid medium |
Environmental Impact | Eco-friendly, no chemicals or solvents used | Generates dust and airborne particles, which can be harmful | Often uses toxic chemicals, generates hazardous waste | Requires disposal of used cleaning fluids |
Precision and Control | High precision, selective cleaning of specific areas | Less precise, may erode the surface or surrounding material | Limited precision, can affect the entire surface | High precision but limited to small, submerged parts |
Surface Integrity | Preserves surface integrity, ideal for sensitive materials | Can damage or roughen the surface, especially on delicate materials | Can cause chemical reactions that may alter surface properties | Generally preserves surface but not suitable for all materials |
Residue and Waste | Minimal residue, no secondary waste | Leaves abrasive particles as waste | Leaves chemical residues, produces secondary waste | Leaves contaminants in the cleaning solution |
Maintenance and Downtime | Low maintenance, minimal downtime | Requires regular replenishment of abrasive material and equipment wear | Frequent chemical replacement and safety measures needed | Requires regular maintenance of ultrasonic equipment |
Safety | Safer for workers, no harmful chemicals or particles | Risk of inhalation and physical harm from abrasive particles | Risk of chemical burns, inhalation, and environmental contamination | Safer, but risks associated with handling and disposing of cleaning fluids |
Versatility | Suitable for a wide range of materials and industries | Primarily used for robust materials, not ideal for delicate surfaces | Versatile, but limited by chemical compatibility with materials | Limited to small parts that can be submerged in the cleaning tank |
Cost-Effectiveness | Higher initial cost but cost-effective in the long term | Lower initial cost but higher ongoing expenses due to abrasive consumption | Low initial cost but high cost for chemicals and disposal | Moderate cost, but limited to specific applications |
Operational Speed | Fast and efficient, reduces overall cleaning time | Can be slow, especially on large or intricate surfaces | Varies depending on chemical reaction time and safety protocols | Fast for small items, but limited by the size of the ultrasonic tank |
Customer Reviews
Related Resources
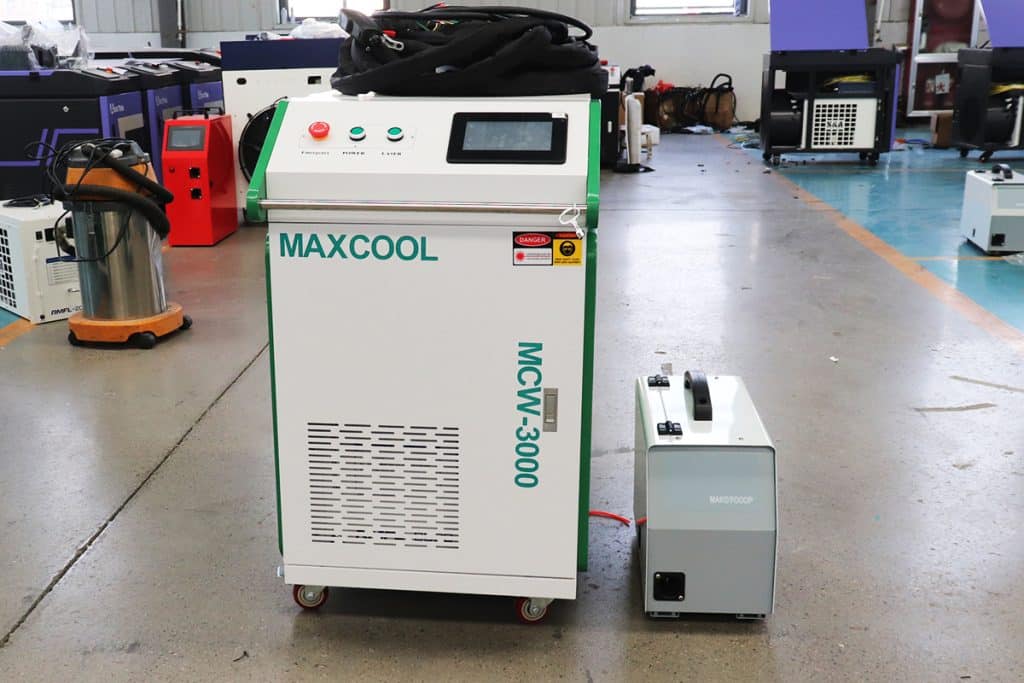
How to Maintain the Cooling System of Laser Cleaning Machines?
This article explains how to maintain the cooling system of laser cleaning machines, covering key components, maintenance schedules, troubleshooting, and best practices.
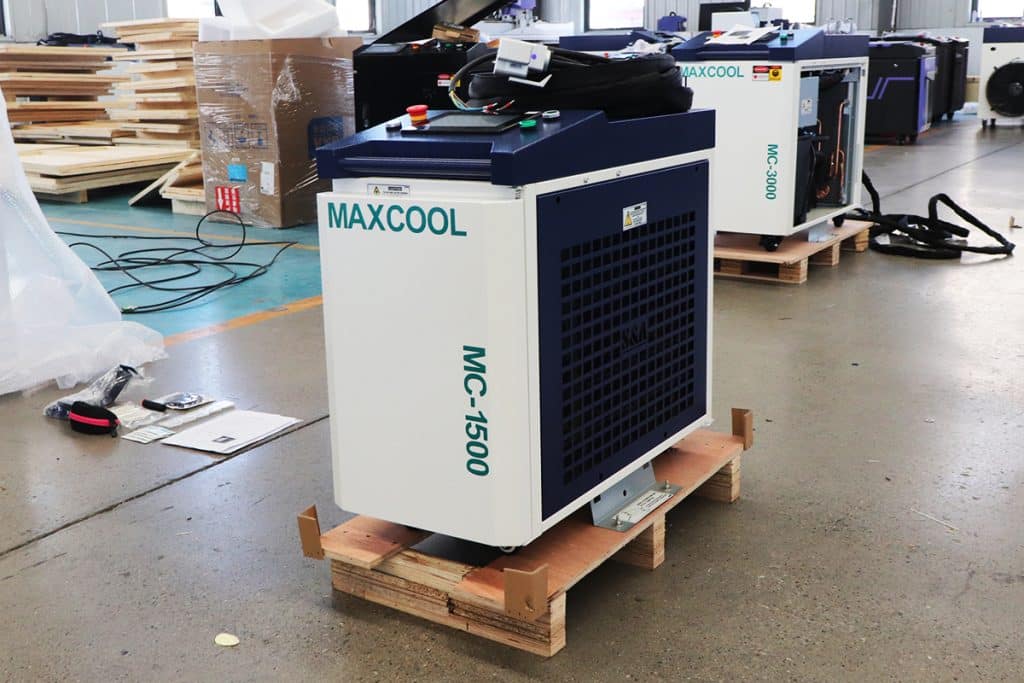
What Are The Applications of Laser Cleaning Machines?
This article explores the various industrial and specialized applications of laser cleaning machines, detailing how the technology is used across multiple sectors and processes.
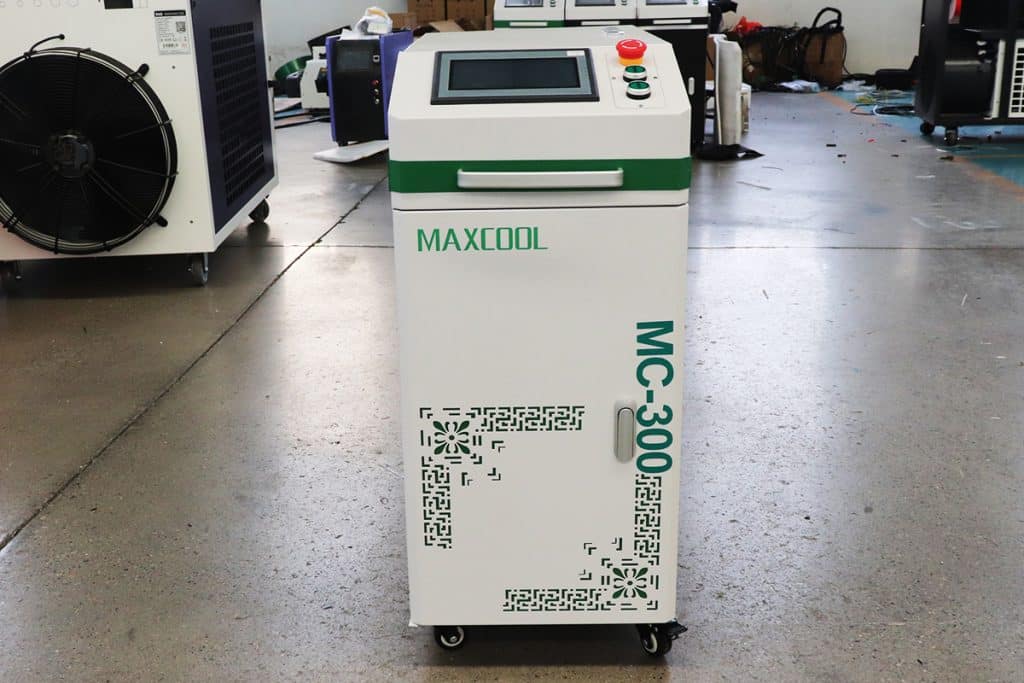
Does Pulsed Laser Cleaning Damage The Substrate?
Explores pulsed-laser cleaning fundamentals, potential substrate damage, controlling parameters, industry case studies, and best practices for safe, efficient surface treatment.