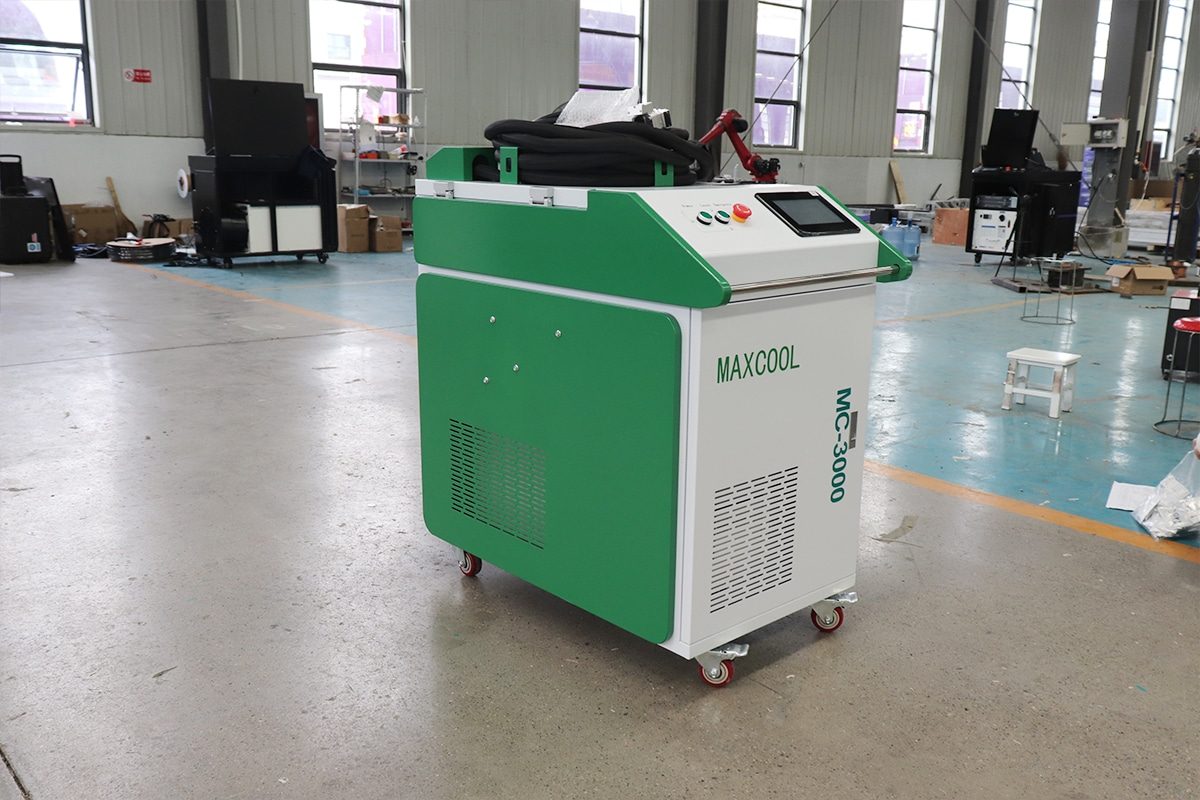
Laser cleaning machine has emerged as a revolutionary technology for surface preparation and contamination removal in industries such as manufacturing, automotive, aerospace, and heritage conservation. As a non-contact, environmentally friendly solution, laser cleaning eliminates the need for abrasive media or chemical agents, minimizing damage and reducing waste. The effectiveness of laser cleaning hinges on selecting the right parameters, such as laser power, pulse duration, frequency, and wavelength, to suit the material and type of contaminant. By fine-tuning these parameters, users can achieve optimal cleaning performance, whether removing rust, paint, oxides, or organic residues, while preserving the integrity of the substrate. This guide will delve into the key considerations and strategies for choosing the most appropriate laser cleaning parameters, ensuring efficient and safe cleaning processes tailored to each specific application.
Understanding Laser Cleaning
What is Laser Cleaning?
Advantages of Laser Cleaning
Laser cleaning offers several advantages over conventional cleaning methods, including:
- Precision and Selectivity: Laser cleaning can target specific areas without affecting adjacent regions or delicate substrates, offering unmatched accuracy.
- Non-Contact and Non-Abrasive: The process does not physically touch the material, reducing wear and tear on sensitive surfaces and eliminating the need for abrasive media.
- Environmentally Friendly: Laser cleaning avoids chemical use and minimizes waste generation, making it a safer and more sustainable option.
- Versatility: Suitable for a wide range of materials, from metals to non-metals, making it a flexible solution for various industrial needs.
- Automation Capabilities: Easily integrated into automated systems, enhancing productivity and consistency in industrial processes.
- Minimal Maintenance: Reduces maintenance costs and downtime, as there is no need for replenishing abrasive materials or chemical solutions.
Applications of Laser Cleaning
Laser cleaning technology has found applications across multiple industries due to its precision, efficiency, and adaptability. Some key applications include:
- Automotive Industry: Removing rust, paint, coatings, and surface contaminants to prepare parts for welding, bonding, or coating.
- Aerospace Industry: Cleaning delicate aircraft components, including removing coatings and oxides from metal surfaces without altering the substrate.
- Manufacturing and Fabrication: Pre-treatment of surfaces to ensure proper bonding, painting, or welding, improving product quality and longevity.
- Heritage Conservation: Restoration of historic monuments, sculptures, and artworks, safely removing dirt, grime, and corrosion while preserving intricate details.
- Electronics and Precision Engineering: Precision cleaning of circuit boards, electronic components, and sensitive machinery to prevent damage or contamination.
- Medical Device Manufacturing: Cleaning and surface preparation of medical implants and instruments to meet stringent industry standards.
- Oil and Gas Sector: Cleaning pipelines, valves, and machinery for maintenance and repair, reducing downtime and increasing operational efficiency.
Key Parameters in Laser Cleaning
Laser Power
Pulse Duration
Wavelength
Pulse Frequency
Beam Spot Size
Scanning Speed
Energy Density (Fluence)
Material Considerations
Types of Substrate Materials
The substrate material being cleaned is one of the most important factors to consider when selecting laser cleaning parameters. Different materials react differently to laser energy due to their physical and thermal properties. Common substrate types include:
- Metals: Common metal substrates include steel, aluminum, copper, titanium, and their alloys. Metals generally absorb laser energy well, making them suitable for high-power cleaning applications. However, different metals have varying thermal conductivities, which must be considered to prevent heat damage.
- Non-Metals: Non-metallic substrates such as plastics, composites, ceramics, stone, and glass may require different laser settings due to their diverse optical and thermal properties. Non-metals often necessitate lower power settings and shorter pulse durations to avoid substrate damage.
- Delicate or Sensitive Materials: Historical artifacts, artworks, and precision electronic components may require special consideration to preserve their structural integrity during cleaning. Lower power, shorter pulse durations, and tailored parameters are typically needed to avoid thermal stress or unwanted ablation.
Types of Contaminants or Coatings
The nature of the contaminants or coatings to be removed plays a crucial role in determining laser cleaning parameters. Common types include:
- Oxides and Rust: Oxide layers and rust are common contaminants on metal surfaces. Laser cleaning is highly effective for rust removal, but it requires sufficient energy density to completely ablate the oxide layer without damaging the metal substrate.
- Paints and Coatings: Removing paint or protective coatings demands precise control of laser power and fluence to avoid affecting the underlying material. Layer-by-layer removal is possible with appropriate parameter tuning, especially for multi-layered coatings.
- Organic Contaminants: Grease, oil, and other organic contaminants often require lower energy levels for effective vaporization. Careful adjustment of pulse duration and frequency helps achieve clean results without residual buildup.
- Adhesive Residues: Adhesives and bonding materials may have varying levels of adhesion to the substrate. Proper laser settings ensure complete removal without leaving residue behind.
Material Reflectivity and Absorption
The interaction between laser light and a material depends on the reflectivity and absorption characteristics of the substrate and contaminant. These properties influence how much laser energy is absorbed or reflected during cleaning.
- Reflectivity: Materials with high reflectivity, such as polished metals (e.g., aluminum or stainless steel), may reflect a significant portion of the laser energy. In such cases, using higher power settings, shorter wavelengths, or pre-treating the surface to enhance absorption can improve cleaning efficiency.
- Absorption: The wavelength of the laser light affects how well different materials absorb energy. For example, some contaminants may absorb infrared laser energy effectively, while others may respond better to ultraviolet or visible wavelengths. Selecting the appropriate wavelength for the specific material and contaminant combination ensures optimal energy transfer and efficient cleaning.
- Thermal Conductivity: High thermal conductivity materials (e.g., copper) quickly dissipate heat, making it challenging to maintain localized heating. Adjusting parameters like pulse duration and scanning speed helps control thermal effects and prevent substrate damage.
Factors Influencing Parameter Selection
Depth of Cleaning Required
The depth of cleaning needed is one of the primary factors influencing parameter selection. Different applications may require varying degrees of contaminant or coating removal:
- Superficial Cleaning: For surface-level contaminants, such as dust, light rust, or thin coatings, lower laser power and energy density settings are sufficient. High scanning speeds can also be used to quickly remove contaminants without damaging the substrate.
- Deep Cleaning: Removing thick layers of rust, paint, or stubborn coatings requires higher laser power and energy density. Slower scanning speeds and multiple laser passes may be necessary to ensure complete removal. It is essential to balance the depth of cleaning with substrate protection to prevent heat-induced damage.
Thermal Sensitivity of Substrate
The thermal properties of the substrate being cleaned significantly affect the choice of laser cleaning parameters:
- Heat-Sensitive Materials: Substrates such as plastics, composites, or delicate metals may be prone to heat deformation or discoloration. For these materials, shorter pulse durations, lower laser power, and faster scanning speeds minimize heat buildup and thermal impact.
- High-Thermal Conductivity Materials: Materials with high thermal conductivity, such as copper or aluminum, require tailored laser settings to ensure sufficient energy is delivered to the contaminant without excessive heat dissipation into the substrate. Proper control of pulse duration and fluence is crucial in such cases.
Surface Finish Requirements
The desired surface finish after cleaning plays a critical role in determining laser cleaning parameters:
- Preserving Surface Integrity: In applications such as historical artifact restoration or precision component cleaning, maintaining the substrate’s original surface characteristics is essential. Lower power settings, controlled energy density, and careful adjustment of scanning speed help achieve a gentle cleaning process.
- Roughening or Texturing: Some applications may require a roughened or textured surface finish for better adhesion during subsequent processes (e.g., welding or bonding). In such cases, higher energy density and slower scanning speeds can create the desired surface profile without compromising cleaning quality.
Productivity and Efficiency
Balancing productivity and cleaning quality is a key consideration for industrial applications:
- High Productivity Demands: In high-volume or automated production environments, maximizing cleaning speed without sacrificing quality is crucial. Higher pulse frequencies and optimized scanning speeds can help achieve faster cleaning cycles while maintaining the desired level of precision.
- Energy and Cost Efficiency: Efficient use of laser power and energy density ensures minimal waste and reduces operational costs. Adjusting laser parameters to match specific cleaning needs minimizes energy consumption while maintaining high performance.
Step-by-Step Guide to Choosing Parameters
Identify the Material and Contaminant
The first step in choosing the appropriate laser cleaning parameters is to thoroughly understand the material to be cleaned and the contaminants to be removed:
- Substrate Identification: Determine whether the substrate is metal (e.g., steel, aluminum, copper), non-metal (e.g., plastics, ceramics), or a sensitive surface such as historical artifacts or electronics. Different substrates have distinct thermal and optical properties that influence laser interaction.
- Contaminant Type: Identify the specific contaminant or coating, such as rust, paint, oxides, grease, or adhesive residues. The thickness, composition, and adhesion strength of the contaminant will help guide parameter selection for effective removal.
Set Initial Laser Parameters
Once the material and contaminant have been identified, establish initial laser settings tailored to the application. This involves configuring key parameters based on the characteristics of both the substrate and the contaminant:
- Laser Power: Choose an initial power level that is appropriate for the material and contamination type. Higher power is often needed for thick or strongly adhered layers, while lower power is recommended for delicate or heat-sensitive substrates.
- Pulse Duration: Select a pulse duration (e.g., nanosecond, picosecond) that balances cleaning effectiveness and substrate protection. Shorter pulses minimize heat impact, whereas longer pulses deliver more energy.
- Wavelength: Opt for a wavelength that is effectively absorbed by the contaminant while limiting interaction with the underlying substrate. This ensures efficient energy transfer.
- Pulse Frequency: Determine the pulse frequency, or number of pulses per second, to balance cleaning speed and energy delivery.
- Scanning Speed: Set an initial scanning speed based on the required cleaning depth and material sensitivity. Faster speeds reduce heat buildup but may require more passes for complete cleaning.
- Beam Spot Size: Adjust the spot size based on the precision required; smaller spots allow for a higher concentration of energy, while larger spots cover more area quickly.
Conduct Tests and Adjustments
Perform a series of controlled tests on a sample area to evaluate the effectiveness of the initial parameter settings:
- Assess Cleaning Efficiency: Check whether the laser successfully removes the contaminant without damaging the substrate. If the cleaning is incomplete, increase laser power, decrease scanning speed, or adjust other parameters as needed.
- Monitor Substrate Impact: Examine the substrate for any signs of damage, discoloration, or deformation. If any issues arise, reduce laser power, shorten the pulse duration, or increase scanning speed to minimize heat accumulation and substrate impact.
- Fine-Tune Parameters: Make incremental adjustments to optimize the balance between effective contaminant removal and substrate protection. Consider testing different pulse durations, power levels, and scanning speeds.
Monitoring and Quality Control
To maintain consistent laser cleaning performance and ensure optimal results, establish ongoing monitoring and quality control protocols:
- Real-Time Monitoring: Utilize sensors and monitoring systems to track the cleaning process and automatically adjust parameters as needed to maintain consistent cleaning results.
- Periodic Inspections: Conduct regular inspections of cleaned surfaces to verify that contaminants have been thoroughly removed without compromising substrate integrity.
- Document Settings: Record the optimized laser parameters for future reference, enabling repeatable and consistent cleaning for similar applications.
Safety Considerations
Eye Protection
Eye protection is one of the most critical safety measures when working with laser cleaning equipment. Laser beams, even in reflected form, can cause severe eye injuries, including permanent vision damage. To ensure eye safety:
- Laser Safety Glasses: Always wear appropriate laser safety glasses rated for the specific wavelength and power of the laser cleaning machine. Ensure the glasses meet industry standards and provide adequate protection against direct and scattered laser radiation.
- Laser-Controlled Area: Establish a designated laser-controlled area with restricted access to prevent unprotected personnel from being exposed to laser radiation. Use warning signs and barriers to clearly demarcate the area.
- Prevent Reflective Hazards: Be mindful of reflective surfaces in the cleaning area, as they can scatter laser beams and pose a risk to operators and bystanders. Properly manage reflections to minimize exposure.
Ventilation and Fume Extraction
Laser cleaning can produce fumes, smoke, and airborne particles as contaminants and coatings are vaporized or ablated. Effective ventilation and fume extraction are necessary to protect operator health and maintain a safe working environment:
- Fume Extractors: Use high-efficiency fume extractors to capture and filter hazardous particles, fumes, and gases generated during the cleaning process. Ensure the fume extractor is positioned close to the laser cleaning site for maximum effectiveness.
- Ventilation Systems: Maintain adequate ventilation in the workspace to prevent the buildup of airborne contaminants. This reduces the risk of inhalation exposure and ensures compliance with workplace air quality standards.
- Personal Protective Equipment (PPE): In addition to fume extraction, operators may need to wear appropriate respiratory protection, such as masks or respirators, if exposure levels exceed permissible limits.
Equipment Safety
Ensuring the safety and proper operation of laser cleaning equipment is essential to prevent accidents and maintain reliable performance:
- Laser Interlock Systems: Use laser cleaning systems equipped with interlock mechanisms that automatically shut down the laser if safety covers are opened or if unauthorized access occurs. This prevents accidental exposure to laser radiation.
- Emergency Stop Buttons: Ensure the equipment has easily accessible emergency stop buttons to quickly shut down the laser in the event of a malfunction or safety incident.
- Regular Maintenance: Perform routine maintenance and inspections of the laser cleaning equipment to ensure all safety features, such as interlocks, emergency stops, and protective covers, are functioning correctly. Address any issues promptly to minimize the risk of equipment failure.
- Operator Training: Provide comprehensive training for operators on the safe use of laser cleaning systems, including emergency procedures, safety protocols, and proper handling of the equipment.
Summary
Get Laser Cleaning Solutions
Selecting the right laser cleaning parameters can make a significant difference in the effectiveness, precision, and safety of your cleaning operations. Maxcool CNC, as a professional manufacturer of laser welding and laser cleaning machines, offers tailored laser cleaning solutions to meet diverse industrial needs. Our expert team works closely with clients to understand their specific cleaning applications, from rust removal to delicate surface preparation and provides customized recommendations on laser power, pulse duration, scanning speed, and other key parameters. Whether you require cleaning for metals, non-metals, or sensitive substrates, we ensure optimal results with minimal substrate damage and maximum productivity. Maxcool CNC’s advanced laser cleaning systems are equipped with robust safety features, automation capabilities, and precise control options, making it easier to achieve consistent and reliable performance. Contact us today to explore how our laser cleaning solutions can transform your surface cleaning challenges into efficient and environmentally friendly processes.