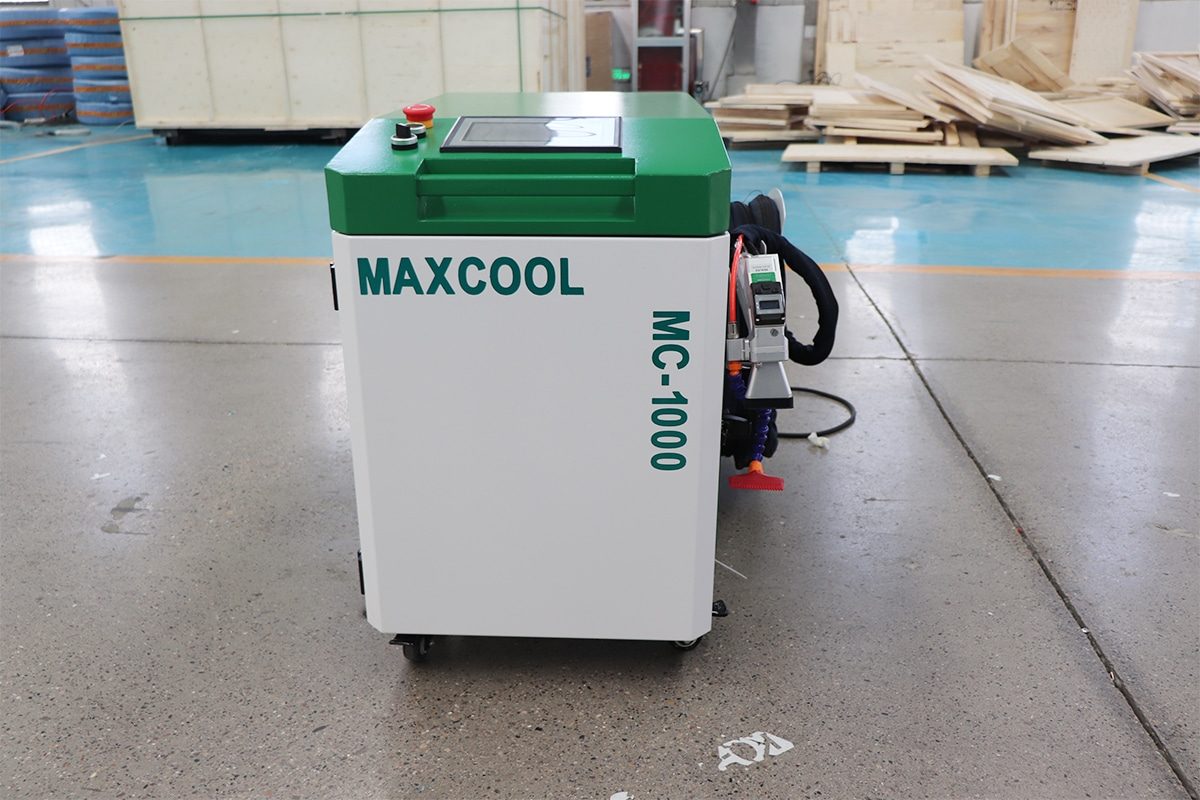
How Laser Parameters Affect the Cleaning Process?
Laser cleaning has become a preferred method for removing contaminants, coatings, rust, and residues from various surfaces without damaging the underlying material. Its precision, eco-friendliness, and efficiency make it valuable across industries—from aerospace to heritage conservation. However, the effectiveness of laser cleaning hinges on carefully selected parameters. Factors such as laser power, pulse duration, wavelength, repetition rate, and scanning speed directly influence cleaning results. The wrong settings can lead to incomplete removal, surface damage, or excessive energy consumption. Understanding how these parameters interact with different materials and contaminants is key to optimizing the process. This article breaks down the core laser parameters and explains their role in achieving effective, safe, and consistent cleaning performance. Whether you’re working with metal, stone, or composites, tuning these variables can make the difference between a successful job and a costly error.
Table of Contents
The Basics of Laser Cleaning
Laser cleaning is a non-contact, non-abrasive method that uses focused laser energy to remove unwanted substances from a surface. The process works through a combination of thermal and photomechanical effects. When a laser beam hits a contaminated surface, it delivers energy that either vaporizes, breaks apart, or lifts the contaminant layer without harming the substrate beneath, assuming the parameters are correctly set.
There are two primary mechanisms at play: ablation and thermal desorption. Ablation involves the direct removal of material through intense heat and pressure generated in microbursts. Thermal desorption occurs when the contaminant absorbs the laser energy and heats up faster than the base material, causing it to break free.
Laser cleaning is particularly useful for delicate or complex surfaces where traditional methods—like chemical solvents, sandblasting, or manual scraping—might be too harsh, slow, or environmentally harmful. Its precision and adaptability make it an increasingly popular choice across industries.
Fundamental Concepts in Laser-Matter Interaction
To understand how laser parameters affect cleaning, it’s important to grasp the basics of how lasers interact with materials.
Energy Absorption and Material Removal Mechanisms
When a laser beam hits a surface, the material absorbs part of the laser energy. The amount of absorption depends on the material’s properties and the laser’s wavelength. This absorbed energy causes rapid heating, melting, vaporization, or even plasma formation, which leads to the removal of contaminants. The goal is to remove the unwanted layer without damaging the substrate underneath.
Ablation Threshold
Every material has a minimum energy level—called the ablation threshold—required to start material removal. Below this threshold, the laser won’t clean effectively. Above it, the laser begins to ablate material, but too much energy can damage the base surface.
Heat Affected Zone (HAZ) and Thermal Effects
The Heat Affected Zone refers to the area where thermal energy alters the material’s properties without removing it. A smaller HAZ is generally better, especially for precision cleaning, as it means minimal heat diffusion and less risk of surface damage.
Role of Pulse Duration and Peak Power
Shorter pulse durations (e.g., nanosecond or picosecond lasers) concentrate energy in shorter timeframes, producing higher peak power. This increases cleaning efficiency and reduces heat spread, minimizing thermal effects and HAZ. Longer pulses, while potentially more powerful in total energy, may transfer more heat into the substrate, increasing the risk of thermal damage.
Mastering these concepts can help adjust laser parameters and perform cleaning in an effective, efficient, and safe manner.
Key Laser Parameters in the Cleaning Process
Optimizing laser cleaning requires a solid understanding of several key parameters. Each one controls how the laser interacts with the surface and how effectively it removes contaminants. Here’s a breakdown of the most critical variables:
Laser Wavelength
- Definition: The distance between peaks of the laser’s electromagnetic wave, usually measured in nanometers (nm).
- Effects on Cleaning: Different materials absorb energy better at specific wavelengths. For example, metals often absorb infrared wavelengths efficiently, while organic compounds may respond better to ultraviolet. Matching the wavelength to the material ensures better energy absorption and more effective cleaning.
Pulse Duration
- Definition: The length of time each laser pulse lasts—typically in nanoseconds (ns), picoseconds (ps), or femtoseconds (fs).
- Effects on Cleaning: Shorter pulses deliver energy in a tighter timeframe, increasing peak power and improving precision. This reduces heat transfer to the underlying material, minimizing the risk of damage. Longer pulses can cause more thermal stress and are less suitable for sensitive surfaces.
Pulse Energy and Fluence
- Definition: Pulse energy is the amount of energy in a single pulse (measured in millijoules, mJ), while fluence is that energy spread over a given area (measured in J/cm²).
- Effects on Cleaning: Fluence must exceed the ablation threshold of the contaminant for removal to occur. Higher values can improve cleaning speed, but too much can damage the base material. Careful control is essential for effective and safe cleaning.
Repetition Rate (Frequency)
- Definition: The number of laser pulses per second, measured in Hertz (Hz).
- Effects on Cleaning: Higher repetition rates allow for faster coverage of the surface. However, if the rate is too high without proper cooling or scanning speed, it can lead to heat buildup and surface degradation. Balance is key.
Beam Spot Size and Focal Position
- Definition: Beam spot size is the diameter of the laser beam on the surface; focal position refers to the point where the beam is most sharply focused.
- Effects on Cleaning: A smaller spot size increases energy concentration, improving cleaning efficiency and precision. Proper focus ensures the maximum energy is delivered exactly where it’s needed. Poor focusing reduces effectiveness and can create uneven results.
Scanning Speed and Overlap
- Definition: Scanning speed is how fast the laser moves across the surface; overlap is how much one laser pass overlaps the next.
- Effects on Cleaning: Slower speeds and more overlap result in more energy per area, improving cleaning depth. However, too much energy buildup can cause thermal damage. The right combination ensures consistent coverage without overheating.
Polarization
- Definition: The direction in which the laser light’s electric field oscillates.
- Effects on Cleaning: Polarization affects how the laser interacts with surfaces, especially textured or reflective ones. Adjusting polarization can improve cleaning uniformity and efficiency, particularly on complex geometries or materials with directional properties.
Together, these parameters define the performance, safety, and precision of laser cleaning. Fine-tuning them based on the material, contamination type, and application is essential for optimal results.
Materials and Their Responses to Laser Cleaning
Different materials react differently to laser cleaning due to variations in thermal conductivity, absorption properties, and sensitivity to heat or mechanical stress. Choosing the right laser parameters requires understanding how each material type responds to laser exposure.
Metals
Metals are among the most common materials cleaned with lasers. They generally have high thermal conductivity and can tolerate higher energy levels, especially when removing oxides, rust, or paint. However, reflective metals like aluminum may require specific wavelengths and higher fluence to ensure adequate energy absorption. Fine-tuning pulse duration and spot size is key to avoiding surface melting or warping.
Glass and Ceramics
These materials are more brittle and prone to cracking under thermal stress. They often absorb laser energy poorly at certain wavelengths, so UV or short-pulse lasers are typically more effective. Careful control of pulse energy and repetition rate is essential to prevent microfractures or surface pitting.
Plastics and Polymers
Plastics are highly sensitive to heat and can degrade, melt, or release fumes when exposed to laser energy. Short pulse durations and lower fluence are usually necessary to avoid damaging the material. UV lasers are often preferred because they can break down organic layers with minimal thermal impact.
Cultural Heritage Materials (Stone, Artwork, Historic Artifacts)
Laser cleaning is widely used in conservation work due to its precision and non-contact nature. Materials like marble, limestone, and aged paint require extremely controlled conditions to avoid irreversible damage. Low fluence, long wavelengths, and highly selective pulse settings help preserve surface texture and integrity. Conservation-grade systems often include real-time monitoring to adjust parameters dynamically during cleaning.
Understanding the physical and chemical behavior of each material under laser exposure is crucial to setting the right parameters and achieving safe, effective cleaning without compromising the surface.
Common Applications and Case Studies
Laser cleaning has proven effective across a wide range of industries due to its precision, control, and environmental benefits. Here are some of the most common applications, along with real-world examples:
Rust and Oxide Removal
Laser cleaning is frequently used to remove rust and oxides from metal surfaces in automotive, aerospace, and manufacturing industries. For example, in shipyard maintenance, lasers clean corroded steel panels without damaging the base metal. By adjusting fluence and scanning speed, technicians can strip oxidation layers while preserving surface integrity.
Paint and Coating Stripping
Removing paint or coatings from sensitive components—like aerospace parts or historical structures—requires control and consistency. Lasers offer a clean alternative to abrasive blasting or chemicals. In one case, aerospace manufacturers used short-pulse lasers to strip coatings from aluminum alloy parts without affecting dimensional tolerances or structural properties.
Mold and Residue Removal in Industrial Settings
In food processing and electronics industries, surface cleanliness is critical. Lasers can remove mold, grease, or chemical residues from tools and machinery without abrasive wear. For example, laser systems have been installed in tire manufacturing plants to clean rubber molds, improving product consistency and reducing downtime.
Restoration of Artwork and Cultural Heritage
Laser cleaning is widely used in art conservation for its ability to remove dirt, pollution crusts, and aged varnish from delicate surfaces. In Florence, Italy, conservators used lasers to clean soot from Renaissance marble sculptures without affecting the original stone. Parameters like low fluence and specific wavelengths were key to preserving fine details.
These examples show how adjusting laser parameters for each application ensures not only effective cleaning, but also protection of the underlying material—whether it’s industrial-grade steel or centuries-old marble.
Safety, Environmental, and Practical Considerations
Laser cleaning offers precision and control, but it comes with responsibilities. Operators must consider safety, environmental impact, and cost when implementing this technology.
Laser Safety Classes and Protective Measures
Most industrial laser cleaning systems fall under Class 4—the highest risk level. These lasers can cause serious eye and skin injuries and pose a fire hazard. Protective eyewear that matches the laser’s wavelength is mandatory. Work areas should be enclosed or marked, with safety interlocks and emergency shutoffs in place. Training is critical to ensure safe operation and compliance with regulations.
Fume Extraction and Byproduct Handling
Laser ablation creates fumes, particulates, and sometimes hazardous gases, especially when removing paint, rust, or organic materials. A proper fume extraction system with filtration must be in place to protect air quality and operator health. Without it, harmful residues can accumulate in the workspace or be inhaled by personnel.
Cost and Practicality Analysis
While laser cleaning systems have a higher initial cost than traditional methods, they often reduce long-term expenses. There’s less wear on equipment, no need for abrasive materials or chemicals, and minimal waste to manage. They’re especially practical for delicate or complex surfaces, where conventional methods could cause damage or be too slow. Over time, the savings in labor, materials, and maintenance can justify the investment.
By addressing safety protocols, managing environmental byproducts, and weighing operational costs, companies can implement laser cleaning efficiently and responsibly.
Summary
Laser cleaning is a powerful and precise method for removing contaminants, coatings, and residues from a wide range of materials. However, its effectiveness depends heavily on the correct selection and control of laser parameters. Factors such as wavelength, pulse duration, energy, fluence, repetition rate, beam size, scanning speed, and polarization all influence how the laser interacts with the target surface. Understanding the fundamental principles of laser-matter interaction—like energy absorption, ablation thresholds, and thermal effects—is essential for tailoring the process to specific materials such as metals, plastics, ceramics, or historical artifacts. Additionally, safety measures, fume management, and cost considerations must be addressed to ensure responsible and efficient use. When properly configured, laser cleaning offers a non-contact, environmentally friendly alternative to traditional methods, with greater control and minimal surface damage. As technology continues to evolve, mastering these parameters will be key to unlocking the full potential of laser-based surface treatment.
Get Laser Cleaning Solutions
Choosing the right laser cleaning solution starts with understanding your specific application—material type, contamination, and desired results. At Maxcool CNC, we specialize in manufacturing high-performance laser cleaning machines designed for precision, efficiency, and durability. Whether you’re removing rust from metal, stripping paint, or restoring sensitive surfaces, our systems are engineered to give you full control over key parameters like wavelength, pulse duration, fluence, and scanning speed. Our expert team works closely with clients to recommend or customize machines that meet both technical and budgetary requirements. We also provide training, support, and integration guidance to ensure optimal performance in your workflow. With years of industry experience and a commitment to innovation, Maxcool CNC delivers reliable solutions for industrial, manufacturing, and restoration needs. Contact us today to learn how our laser cleaning systems can improve your process and results—safely, efficiently, and cost-effectively.