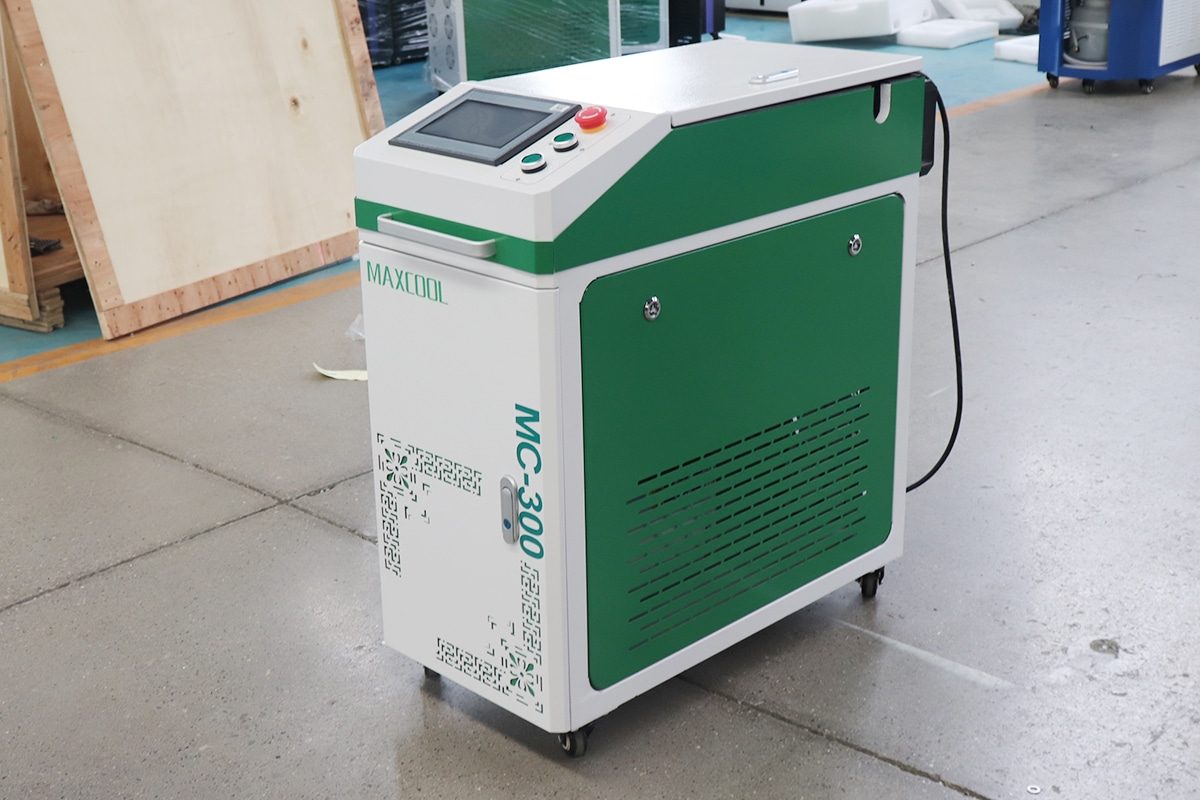
Understanding Laser Cleaning Technology
How It Works
- Laser Beam Generation: A laser source emits a high-energy beam of light.
- Targeted Application: The beam is focused onto the surface using specialized optics.
- Material Removal: Contaminants absorb the laser’s energy, causing them to break down or evaporate.
Types of Lasers Used
- Pulsed Lasers: Ideal for delicate applications where precision is key, such as in the aerospace and electronics industries. They emit short, high-energy pulses that minimize heat impact.
- Continuous Wave Lasers: Used for heavy-duty cleaning tasks like removing thick rust or industrial coatings. These lasers provide a steady energy stream for fast material removal.
Applications of Laser Cleaning
- Aerospace: Surface preparation, paint removal, and oxide layer elimination.
- Automotive: Paint stripping, rust removal, and component cleaning.
- Cultural Heritage: Restoration of monuments, sculptures, and historical artifacts.
- Electronics: Delicate cleaning of circuit boards, sensors, and intricate components.
- Manufacturing: Mold cleaning, welding preparation, and residue removal.
Factors Affecting the Speed of Laser Cleaning
Material Type
The nature of the substrate significantly affects cleaning speed. For instance:
- Metal Surfaces: Highly reflective metals, such as aluminum or stainless steel, may slow cleaning due to partial energy reflection. Pre-treatment or optimized settings can mitigate this.
- Non-Metal Surfaces: Plastics, composites, or ceramics require careful parameter selection to avoid surface damage while maintaining effective cleaning.
Contaminant Characteristics
Rust and Corrosion: Thick layers of rust require higher laser power and more time compared to light surface oxidation.
- Paint: Multi-layered coatings necessitate multiple passes, increasing cleaning time. Advanced systems can adjust settings to efficiently tackle these layers.
- Grease and Oil: Softer contaminants are generally faster to remove due to lower adhesion strength.
Laser System Specifications
- Power: Higher power levels (e.g., 1000W or more) enable quicker cleaning but may require precision to avoid surface alteration.
- Wavelength: Shorter wavelengths (e.g., ultraviolet lasers) often provide better absorption for fine contaminants.
- Pulse Frequency and Duration: Higher frequencies deliver more pulses per second, increasing the material removal rate. Ultra-short pulse lasers minimize thermal damage for sensitive applications.
Operator and Environmental Factors
- Operator Expertise: Skilled operators can optimize laser parameters, scan paths, and speeds for specific tasks.
- Surface Geometry: Complex shapes, such as grooves or intricate designs, may slow cleaning due to limited laser access.
- Environmental Conditions: Ambient temperature, humidity, and cleanliness of the workspace can impact laser performance and results.
Real-World Speed Metrics
Rust Removal
- Light Rust: Up to 20 square meters per hour with a high-power laser (e.g., 1000W+).
- Heavy Rust: Typically 5-10 square meters per hour, depending on rust thickness and substrate conditions.
Paint Stripping
- Single Layer Paint: Approx. 10-15 square meters per hour with continuous wave lasers.
- Multi-Layer Coatings: Slower rates (3-7 square meters per hour) due to the need for multiple passes.
Oxide Layer Removal
- Welding Preparation: Achieves 10-12 square meters per hour on average.
- Aerospace Components: Precision cleaning for high-value parts may reduce speed to ensure no material damage.
Surface Preparation
- Adhesion Improvement: Cleaning for bonding or coating applications can reach speeds of 15-25 square meters per hour with optimized setups.
Technological Advancements Enhancing Laser Cleaning Speed
Recent innovations have dramatically improved the speed, efficiency, and applicability of laser cleaning systems. Below are key advancements:
- High-Power Laser Systems: Systems now offer power outputs exceeding 2000W, making them suitable for high-speed cleaning of large industrial components, such as pipelines, tanks, and ship hulls.
- Automation and Robotics: Robotic laser systems equipped with advanced sensors enable precise cleaning of complex geometries. Automated setups reduce human intervention, enhance consistency, and save time.
- AI and Machine Learning: Intelligent systems analyze surface conditions in real-time to adjust laser parameters, optimizing speed and minimizing energy waste.
- Enhanced Optics and Beam Delivery: Advances in laser optics improve beam focus and energy efficiency, enabling faster cleaning of intricate patterns or larger areas without sacrificing quality.
- Hybrid Approaches: Combining laser cleaning with pre-treatment methods like surface priming or chemical treatments can further accelerate cleaning while ensuring superior results.
Comparative Analysis
Laser Cleaning VS. Abrasive Blasting
- Speed: Laser cleaning excels in intricate or delicate tasks, while abrasive blasting remains quicker for bulk material removal on flat surfaces.
- Environmental Impact: Unlike abrasive blasting, which generates particulate waste, laser cleaning is virtually waste-free.
- Material Preservation: Lasers offer non-contact cleaning, preserving the underlying material’s integrity.
Laser Cleaning VS. Chemical Cleaning
- Speed: Chemical cleaning is slower due to soaking and rinsing cycles.
- Safety and Sustainability: Lasers eliminate harmful chemical usage, reducing health risks and environmental pollution.
- Cost Efficiency: Although initial laser system costs are high, reduced consumables and maintenance make them cost-effective over time.
Laser Cleaning VS. Ultrasonic Cleaning
- Applications: Ultrasonic cleaning is ideal for small, intricate parts submerged in a liquid bath, while lasers handle larger surfaces and dry cleaning applications.
- Speed: Lasers outperform ultrasonic systems for heavy-duty industrial tasks.
Challenges and Limitations
While laser cleaning offers numerous advantages, it is not without challenges:
- High Initial Investment: Laser systems, especially high-power units, require significant upfront capital. Small businesses may find this prohibitive, though long-term savings often offset initial costs.
- Learning Curve: Operators must undergo training to effectively manage laser systems. Industry-specific certifications can address this challenge, ensuring safe and efficient operation.
- Complex Geometries: Cleaning intricate or deeply recessed surfaces can be time-intensive. Emerging solutions, such as 3D laser scanning, aim to address these limitations.
- Resistant Contaminants: Certain materials, such as thick polymer coatings or highly reflective metals, may require specialized lasers or slower cleaning rates to achieve desired results.
Summary
Laser cleaning is a transformative technology that delivers unparalleled speed, precision, and environmental benefits. Its rapid cleaning capabilities, coupled with advancements in automation and AI, make it an invaluable tool for industries seeking efficiency and sustainability. While challenges such as cost and complexity persist, ongoing innovations promise to broaden its accessibility and effectiveness.
Industries looking to enhance productivity and reduce ecological footprints should consider laser cleaning as a cornerstone technology. With its remarkable advantages, laser cleaning is poised to shape the future of industrial maintenance and manufacturing.