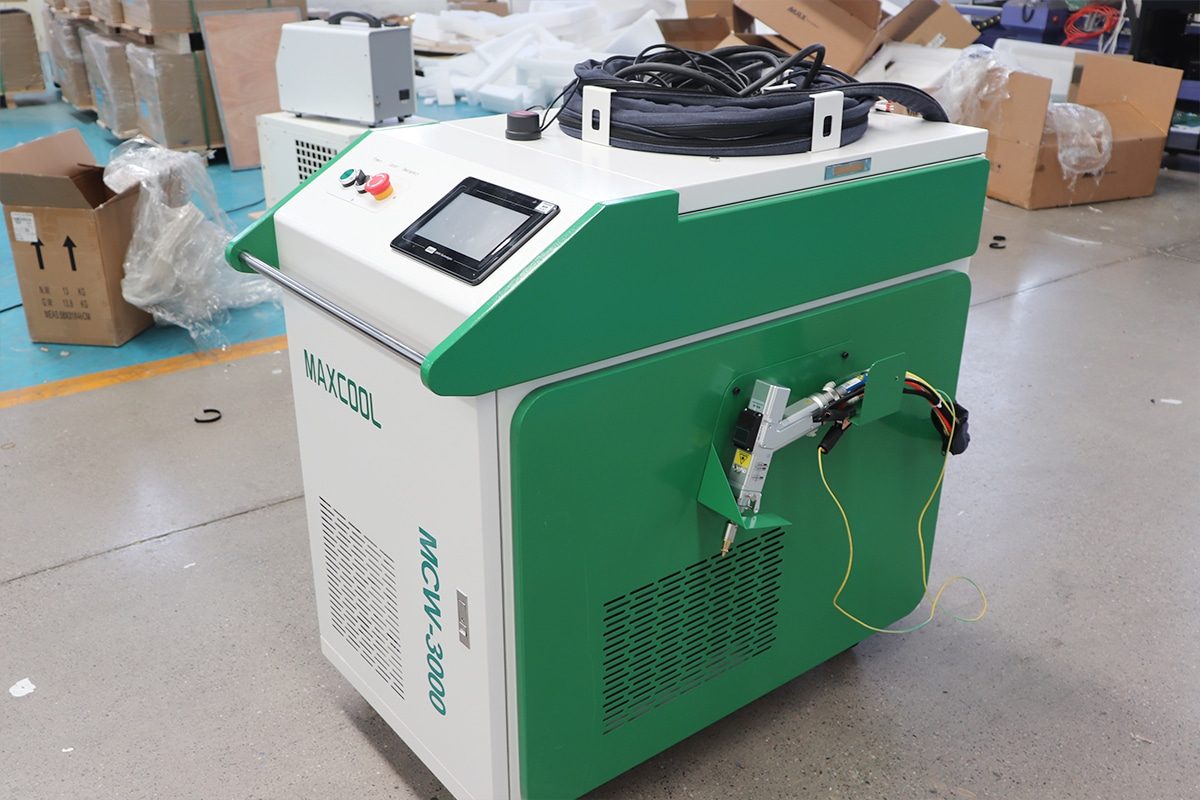
Stainless Steel Properties
Overview of Stainless Steel Properties
Types of Stainless Steel and Their Composition
Stainless steel comes in several types, each tailored for specific uses based on its composition and microstructure:
- Austenitic Stainless Steel: The most common type, it contains high levels of chromium (16-26%) and nickel (6-22%), along with small amounts of carbon. Austenitic stainless steel is highly corrosion-resistant, non-magnetic, and maintains strength at high temperatures. Grades such as 304 and 316 are popular in industries like food processing and marine applications.
- Ferritic Stainless Steel: This type has lower chromium content (10.5-18%) and no significant nickel addition, making it less expensive. It is magnetic and known for good corrosion resistance and thermal conductivity. Common grades include 430 and 409, often used in automotive parts and home appliances.
- Martensitic Stainless Steel: Martensitic stainless steel contains moderate chromium (12-18%) and higher carbon levels, making it harder and more wear-resistant. It is magnetic but less corrosion-resistant than austenitic and ferritic types. Grades like 410 and 420 are used for tools and surgical instruments.
- Duplex Stainless Steel: Combining austenitic and ferritic structures, duplex stainless steel offers high strength and excellent corrosion resistance, especially against stress corrosion cracking. It typically contains 22-25% chromium and 5-7% nickel. Duplex grades are commonly used in chemical processing and oil and gas industries.
- Precipitation-Hardening Stainless Steel: This type gains its strength through heat treatment. It contains chromium, nickel, and elements like copper or aluminum. Known for high strength and moderate corrosion resistance, it’s used in aerospace and military applications.
Challenges and Considerations in Welding Stainless Steel
Welding stainless steel requires careful attention due to its unique properties:
- Heat Sensitivity: Excessive heat can lead to warping, distortion, or discoloration, and in some cases, the breakdown of the protective oxide layer, reducing corrosion resistance.
- Thermal Expansion: Stainless steel expands significantly under heat, which can cause misalignment or stress in the welded joint.
- Material Selection: Matching filler materials with the base metal is crucial to maintain the integrity of the weld and prevent cracking.
- Cracking Risks: Austenitic stainless steel is prone to solidification cracking, while martensitic stainless steel may suffer from hydrogen-induced cracking.
- Oxide Formation: Oxidation on the surface during welding can affect the weld quality and aesthetic finish, often requiring post-weld cleaning or passivation.
Principles of Laser Welding Stainless Steel
Understanding the Laser Welding Process
Interaction of Laser with Stainless Steel
The interaction between the laser beam and stainless steel is influenced by the material’s reflectivity, thermal conductivity, and specific alloy composition. Key aspects of this interaction include:
- Absorption of Laser Energy: Stainless steel’s reflectivity can initially reduce energy absorption, especially on a polished surface. Surface preparation or adjustments in laser wavelength can optimize energy transfer.
- Heat Affected Zone (HAZ): The high energy density of laser welding allows for a narrow HAZ, which minimizes structural changes and preserves the stainless steel’s corrosion resistance.
- Material Vaporization and Keyhole Formation: The laser’s focused energy can create a keyhole effect, where vaporized material stabilizes the molten pool and allows for deep penetration welding with minimal defects.
- Oxidation: Interaction with atmospheric oxygen during welding can lead to oxide formation, affecting the weld’s strength and appearance. Shielding gases like argon or nitrogen are often used to mitigate this.
Key Parameters Affecting Stainless Steel Welding
Achieving optimal results when laser welding stainless steel depends on several critical parameters:
- Laser Power: The laser’s power output directly affects penetration depth and weld speed. Lower power may result in incomplete fusion, while excessive power can cause overheating or excessive melting.
- Welding Speed: The welding speed determines the heat input per unit length. Slow speeds increase heat input, leading to a wider HAZ and potential distortion, while faster speeds may result in incomplete fusion.
- Focal Position: The focal point of the laser beam must be precisely positioned to achieve the desired penetration and minimize energy loss. Variations in focus can lead to defects such as porosity or insufficient weld depth.
- Shielding Gas: Proper shielding gas selection and flow rate are essential to protect the weld from oxidation and stabilize the molten pool. Argon, helium, and nitrogen are common choices for stainless steel.
- Joint Design and Fit-Up: Stainless steel joints must be prepared with precise tolerances to ensure good fusion. Laser welding’s narrow beam requires accurate alignment to avoid defects.
- Pulse or Continuous Wave (CW) Mode: Pulse lasers are often used for thin materials or spot welding, while CW lasers are preferred for deeper penetration and faster speeds in thicker sections.
Stainless Steel Laser Welding Machines
Types of Laser Welding Systems for Stainless Steel
Laser welding systems for stainless steel are available in various configurations, each designed to meet specific application needs. The most common types include:
- Handheld Laser Welding Machines: Compact and portable, these machines are ideal for small-scale or on-site applications. They offer flexibility and ease of use for welding stainless steel in complex shapes or hard-to-reach areas.
- Robotic Laser Welding Systems: These automated systems integrate robotic arms with laser welding equipment to deliver high-speed, repeatable, and precise welding. They are ideal for large-scale production in industries like aerospace, automotive, and medical devices.
Selection of Laser Sources and Parameters
Selecting the right laser source and parameters is crucial for achieving high-quality welds in stainless steel:
- Laser Source Types: Fiber lasers offer high beam quality, low maintenance, and energy efficiency, making them suitable for precision welding tasks.
- Power Output: The power rating of the laser must align with the material thickness and desired penetration depth. For instance, 1000W–3000W is typically sufficient for thin to medium-thickness stainless steel, while thicker materials may require higher power.
- Wavelength: Shorter wavelengths, such as those from fiber lasers, are better absorbed by stainless steel, improving efficiency and reducing reflectivity issues.
- Beam Mode: Single-mode lasers are ideal for precision welding, while multi-mode lasers handle high-power applications and larger weld areas effectively.
- Pulse vs. Continuous Wave (CW): Pulsed lasers are suitable for spot welding or thin sections, while CW lasers are better for deep penetration and high-speed welding.
Ancillary Equipment and Accessories
Supporting equipment and accessories play a vital role in enhancing the efficiency and quality of stainless steel laser welding:
- Shielding Gas Systems: Proper gas delivery systems are essential to prevent oxidation and improve weld quality. Commonly used gases include argon, helium, and nitrogen.
- Cooling Systems: Laser welding machines generate significant heat, requiring efficient cooling systems to maintain stability and performance. Water or air-cooled systems are typically used.
- Clamping and Positioning Tools: Precise alignment is critical in laser welding. High-quality clamps, jigs, and fixtures help secure the workpiece and ensure accurate welds.
- Optics and Beam Delivery: High-performance optics, including lenses and mirrors, ensure precise beam focus and minimize energy loss. Some systems also offer adjustable optics for greater flexibility.
- Welding Monitoring and Control Systems: Advanced systems include real-time monitoring tools, such as cameras and sensors, to track weld quality and detect defects immediately.
- Laser Cleaning Systems: Often paired with welding machines, laser cleaning systems are used to prepare stainless steel surfaces by removing contaminants, rust, or oxides before welding.
Applications of Laser Welding Stainless Steel
Automotive Industry
Stainless steel is widely used in the automotive sector due to its strength, corrosion resistance, and ability to withstand high temperatures. Laser welding plays a crucial role in fabricating:
- Exhaust Systems: Stainless steel exhaust components require precise welds to ensure durability and resistance to harsh environments. Laser welding enables leak-proof and aesthetically clean joints, even in complex geometries.
- Fuel Tanks: Laser welding ensures the integrity and strength of stainless steel fuel tanks, providing a seamless finish that prevents leaks and improves safety.
Aerospace Industry
The aerospace sector demands components with exceptional strength-to-weight ratios, resistance to extreme temperatures, and precision manufacturing. Laser welding is a key technology for:
- Aircraft Components: Stainless steel parts such as structural supports, ducts, and fasteners are laser-welded to ensure minimal distortion and reliable performance in demanding conditions.
- Turbine Blades: Turbine blades in jet engines require high-strength welds to withstand high-speed rotations and extreme heat. Laser welding achieves these welds with unmatched precision and minimal material waste.
Medical Devices and Equipment
Laser welding is indispensable in the medical field, where stainless steel is commonly used for its biocompatibility, sterilizability, and strength. Key applications include:
- Surgical Instruments: Precision laser welding ensures seamless joints for surgical instruments, improving hygiene and durability.
- Implants and Prosthetics: Stainless steel implants and prosthetics are welded with high accuracy to avoid defects and ensure patient safety.
- Medical Equipment: Devices like stainless steel frames, housings, and support structures rely on laser welding for clean, robust connections.
Food and Beverage Industry
In the food and beverage industry, stainless steel is prized for its hygiene, corrosion resistance, and ease of cleaning. Laser welding is widely used in fabricating:
- Tanks and Containers: Stainless steel tanks for storage and processing of food and beverages require welds that are smooth, clean, and free of contaminants. Laser welding ensures high-quality, sanitary joints.
- Conveyor Systems: Conveyor belts and equipment made of stainless steel benefit from laser welding for durability and resistance to wear and tear in demanding environments.
Architectural and Decorative Applications
Stainless steel’s aesthetic appeal and resistance to corrosion make it a popular choice for architectural and decorative uses. Laser welding enhances its utility in:
- Building Facades and Cladding: Laser welding creates clean, precise seams for stainless steel panels, ensuring a polished finish and long-lasting performance.
- Sculptures and Decorative Elements: Artists and designers use laser welding to create intricate, seamless stainless steel sculptures and decorative components that combine beauty with structural integrity.
Best Practices and Tips for Laser Welding Stainless Steel
Proper Handling and Storage of Stainless Steel Materials
Ensuring the quality of stainless steel materials before welding is crucial for achieving optimal results. Follow these guidelines:
- Prevent Contamination: Stainless steel is sensitive to contaminants such as dirt, grease, and foreign particles. Store materials in a clean, dry environment and use dedicated tools to avoid cross-contamination with other metals.
- Avoid Surface Damage: Scratches and surface defects can lead to weld inconsistencies and corrosion. Handle stainless steel with care, using protective coverings during transport and storage.
- Environmental Considerations: Keep stainless steel away from moisture, chemicals, or corrosive environments that could compromise its integrity before welding.
Optimization of Stainless Steel Welding Parameters
Fine-tuning your welding parameters is essential for high-quality welds. Key considerations include:
- Laser Power and Speed: Adjust laser power and welding speed to suit the thickness and type of stainless steel. Higher power and slower speeds may be required for thicker materials, while thinner sections benefit from lower power and faster speeds.
- Focal Point Alignment: Ensure the laser beam’s focal point is precisely positioned for maximum energy transfer to the joint. Misalignment can cause incomplete fusion or excessive melting.
- Shielding Gas Flow: Use appropriate shielding gases, such as argon or nitrogen, to prevent oxidation and porosity in the weld. Optimize gas flow rates to cover the weld area without excessive turbulence.
- Weld Joint Design: Use tight tolerances and well-prepared edges to ensure consistent weld quality. Laser welding’s narrow beam requires precise alignment for optimal results.
Post-Weld Treatment and Finishing Techniques
After welding, additional steps are often necessary to enhance the appearance, durability, and corrosion resistance of the weld:
- Cleaning: Remove any oxide layers, discoloration, or spatter using laser cleaning systems, chemical passivation, or mechanical polishing.
- Passivation: Restore the protective oxide layer on stainless steel surfaces using chemical treatments to ensure long-term corrosion resistance.
- Polishing: Polishing the weld area improves its aesthetic appeal and smooths out any imperfections, making it ideal for decorative applications.
- Stress Relief: For certain grades of stainless steel, post-weld heat treatment may be required to relieve residual stresses and prevent cracking.
Common Challenges and Troubleshooting
Even with advanced laser welding techniques, challenges may arise. Here are common issues and solutions:
- Warping and Distortion: Excessive heat input can cause warping. Minimize distortion by optimizing heat input, using fixturing tools, and welding in short sections.
- Porosity: Porosity in welds is often caused by contamination or improper shielding gas flow. Ensure materials are clean, use high-quality gas, and verify gas flow rates.
- Cracking: Cracking can occur due to improper filler material or residual stresses. Match filler material to the stainless steel grade and apply stress-relief treatments if needed.
- Oxidation and Discoloration: Oxidation during welding can lead to unsightly discoloration and reduced corrosion resistance. Use proper shielding gas coverage and clean the weld area post-welding.