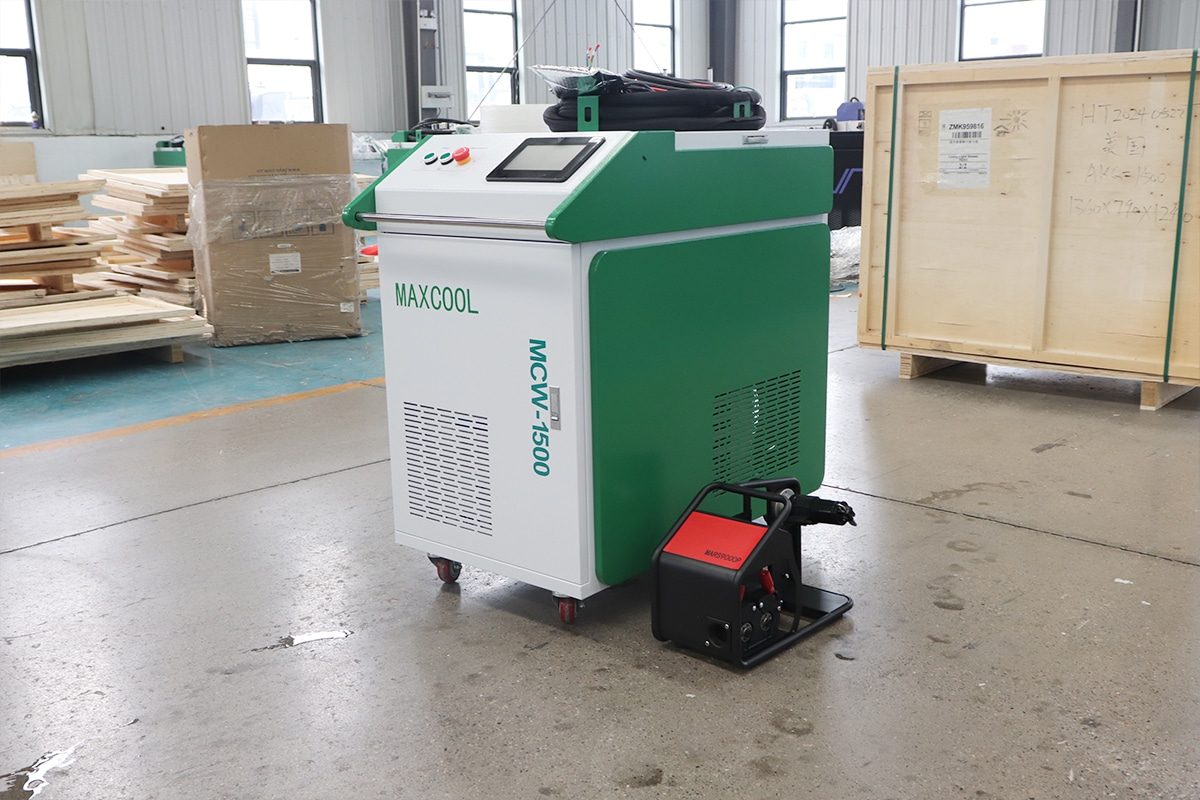
Guide to Laser Welding Aluminum
Laser welding is a cutting-edge technology used in various industries to join metal components with precision and efficiency. Aluminum, being a widely used lightweight and corrosion-resistant metal, presents unique challenges when welded. This guide explores the fundamentals, advantages, techniques, and challenges of laser welding aluminum, providing insights to optimize the process.
Table of Contents
Understanding Laser Welding
Laser welding is a process that utilizes a highly focused laser beam to melt and join metal parts. It is known for its high precision, speed, and minimal heat-affected zone (HAZ). The process is widely used in the automotive, aerospace, electronics, and manufacturing industries.
Key Components of Laser Welding
- Laser Source: Fiber lasers, CO2 lasers, or Nd: YAG lasers
- Beam Delivery System: Optics that focus and direct the laser beam
- Shielding Gas: Protects the weld pool from oxidation
- Workpiece Handling System: CNC machines or robotic arms for precision positioning
- Cooling System: Prevents overheating and maintains system efficiency
Working Principle of Laser Welding
Laser welding works by focusing a high-intensity laser beam onto the surface of the aluminum workpiece. The heat generated by the laser melts the metal at the joint, forming a weld upon cooling. Depending on the energy input, welding can occur in conduction mode or keyhole mode, each affecting the depth and strength of the weld.
Properties of Aluminum That Affect Welding
Aluminum is a widely used metal due to its lightweight, corrosion resistance, and excellent thermal conductivity. However, it presents several challenges in laser welding:
- High Reflectivity: Aluminum has a high reflectivity to laser beams, particularly for infrared wavelengths. This can lead to inefficient energy absorption, requiring higher-power lasers or specialized coatings. Strategies such as using green or blue wavelength lasers are sometimes employed to enhance absorption.
- High Thermal Conductivity: Aluminum conducts heat rapidly, which can lead to excessive heat dissipation and difficulty maintaining a stable weld pool. This requires precise energy control and the use of auxiliary heat sources in some cases to stabilize the process. Maintaining an appropriate heat input balance is essential to prevent localized melting and warping.
- Oxide Layer: Aluminum forms a natural oxide layer (Al2O3) that has a much higher melting point than the base metal. This layer must be removed or penetrated for proper fusion. Pre-weld cleaning using laser cleaning machines, chemical treatments, or mechanical abrasion is necessary. Additionally, oxide formation can be minimized using optimized shielding gas coverage.
- Porosity and Cracking: Laser welding aluminum can lead to porosity due to the rapid solidification and trapped gases. Preheating, optimized shielding gas selection, and the use of filler materials are crucial to mitigating these defects. Controlling solidification rates by adjusting laser power and travel speed helps reduce porosity issues, ensuring strong and defect-free welds.
Advantages of Laser Welding Aluminum
- High Precision: Laser welding provides narrow, precise weld seams with minimal distortion, allowing for intricate and delicate assemblies.
- High-Speed Processing: The process is much faster compared to traditional welding techniques, improving production efficiency and reducing processing time.
- Minimal Heat-Affected Zone (HAZ): Reduced thermal input prevents warping and maintains mechanical properties, ensuring the integrity of the welded structure.
- Automation Compatibility: Easily integrated into automated production lines, reducing human error, improving consistency, and increasing productivity.
- Aesthetic Appeal: Produces clean and smooth welds with minimal post-processing requirements, making it ideal for high-end and visible applications.
Laser Welding Techniques for Aluminum
- Keyhole Welding: This technique involves high-power laser beams creating a deep, narrow penetration, forming a keyhole effect. It is suitable for thicker aluminum sheets and high-strength applications, providing deeper weld penetration.
- Conduction Mode Welding: Lower-power lasers are used, relying on heat conduction to melt and join the material. This method is used for thin aluminum components with a focus on aesthetic finishes and applications requiring minimal distortion.
- Pulse Laser Welding: A pulse laser delivers controlled bursts of energy, ideal for welding thin aluminum sheets or delicate components while minimizing heat input. This technique is effective in preventing warping and reducing material defects.
- Hybrid Laser Welding: Combining laser welding with traditional methods such as MIG or TIG welding improves joint strength and compensates for aluminum’s reflectivity issues. This technique is commonly used in industries requiring enhanced mechanical properties and weld integrity.
Process Parameters for Optimized Laser Welding
To achieve the best results when laser welding aluminum, controlling process parameters is essential:
- Laser Power: Higher power is needed to overcome aluminum’s reflectivity and achieve deep penetration. Power adjustments must be carefully managed to prevent material distortion.
- Welding Speed: Optimized speed prevents overheating and reduces porosity. A balance between travel speed and laser intensity is crucial to achieving strong welds.
- Shielding Gas: Argon and helium are commonly used to protect the weld from oxidation, with helium providing deeper penetration. A combination of gases may be used to optimize results.
- Focus Position: Proper focus alignment ensures deep and consistent weld penetration. Fine-tuning the focal point is critical to achieving uniform weld quality.
- Beam Modulation: Pulsed or continuous wave settings affect energy distribution and weld quality. Pulse modulation can reduce thermal damage and improve weld consistency.
Challenges and Solutions in Laser Welding Aluminum
- High Reflectivity: Use fiber lasers or pre-treat surfaces with coatings to enhance absorption. Adjusting beam angles and polarization can also help mitigate reflectivity issues.
- Oxide Layer Interference: Use laser cleaning or mechanical abrasion to remove oxides before welding. Additionally, selecting proper shielding gases can minimize oxide reformation during welding.
- Porosity Formation: Adjust shielding gas, welding speed, and preheating techniques to reduce trapped gases. Proper joint design and laser parameter optimization can significantly decrease porosity.
- Hot Cracking: Optimize filler material selection and welding parameters to control solidification rates. Managing thermal gradients can also help reduce the risk of hot cracking.
Applications of Laser Welding Aluminum
- Automotive Industry: Used in car body panels, battery enclosures, and lightweight structural components to enhance fuel efficiency and performance.
- Aerospace Industry: Essential for joining aluminum aircraft components, reducing weight while maintaining strength, and ensuring durability and safety in flight applications.
- Electronics and Electrical Industry: Ideal for welding aluminum casings, connectors, and battery components in electronic devices, improving durability and electrical conductivity.
- Industrial and Manufacturing: Applied in robotic welding cells for large-scale aluminum fabrication, enabling high precision, repeatability, and production efficiency.
Best Practices for Laser Welding Aluminum
- Pre-Weld Preparation: Clean surfaces thoroughly to remove oxide layers and contaminants. Use mechanical, chemical, or laser cleaning methods to ensure optimal weld quality.
- Parameter Optimization: Conduct trials to find the best laser power, speed, and gas flow settings for specific applications.
- Real-Time Monitoring: Use vision systems or sensors to detect defects and adjust parameters dynamically, ensuring high-quality results.
- Post-Weld Inspection: Conduct quality checks such as X-ray, ultrasonic, or dye penetrant testing to ensure weld integrity and compliance with industry standards.
By following these best practices, manufacturers can ensure high-quality laser welding results, enhancing productivity and performance across various industries.
Summary
Laser welding aluminum is a highly effective and precise method for joining aluminum components, offering significant advantages over conventional welding techniques. The process provides high-speed operation, minimal heat-affected zones, and superior weld strength, making it ideal for industries such as automotive, aerospace, electronics, and manufacturing.
However, aluminum’s unique properties, including high reflectivity, thermal conductivity, and oxide layer formation, pose challenges that require careful parameter optimization. Techniques such as keyhole welding, conduction mode welding, and pulsed laser welding can be employed to achieve high-quality welds while mitigating issues such as porosity and cracking.
Proper shielding gas selection, laser power control, and pre-weld cleaning methods are essential to improving weld quality. By following best practices and real-time monitoring, manufacturers can ensure consistent and defect-free welds. With advanced laser welding solutions from Maxcool CNC, businesses can enhance their productivity, reduce operational costs, and achieve superior aluminum welds with precision and reliability.
Get Laser Welding Solutions
Maxcool CNC is a trusted manufacturer specializing in high-performance laser welding machines and laser cleaning machines. Our state-of-the-art laser welding systems are designed for precision, durability, and efficiency, making them ideal for industries that require high-quality aluminum welds.
We offer a range of laser welding solutions tailored to meet various industrial needs, including fiber laser welding systems for deep penetration, hybrid laser welding for enhanced strength, and pulsed laser welding for delicate components. Our machines are equipped with advanced automation capabilities, real-time monitoring, and user-friendly interfaces to ensure maximum productivity and ease of operation.
At Maxcool CNC, we are committed to providing reliable and innovative welding solutions that help businesses improve efficiency, reduce costs, and achieve superior weld quality. Contact us today to learn more about our laser welding solutions and find the perfect system for your application.