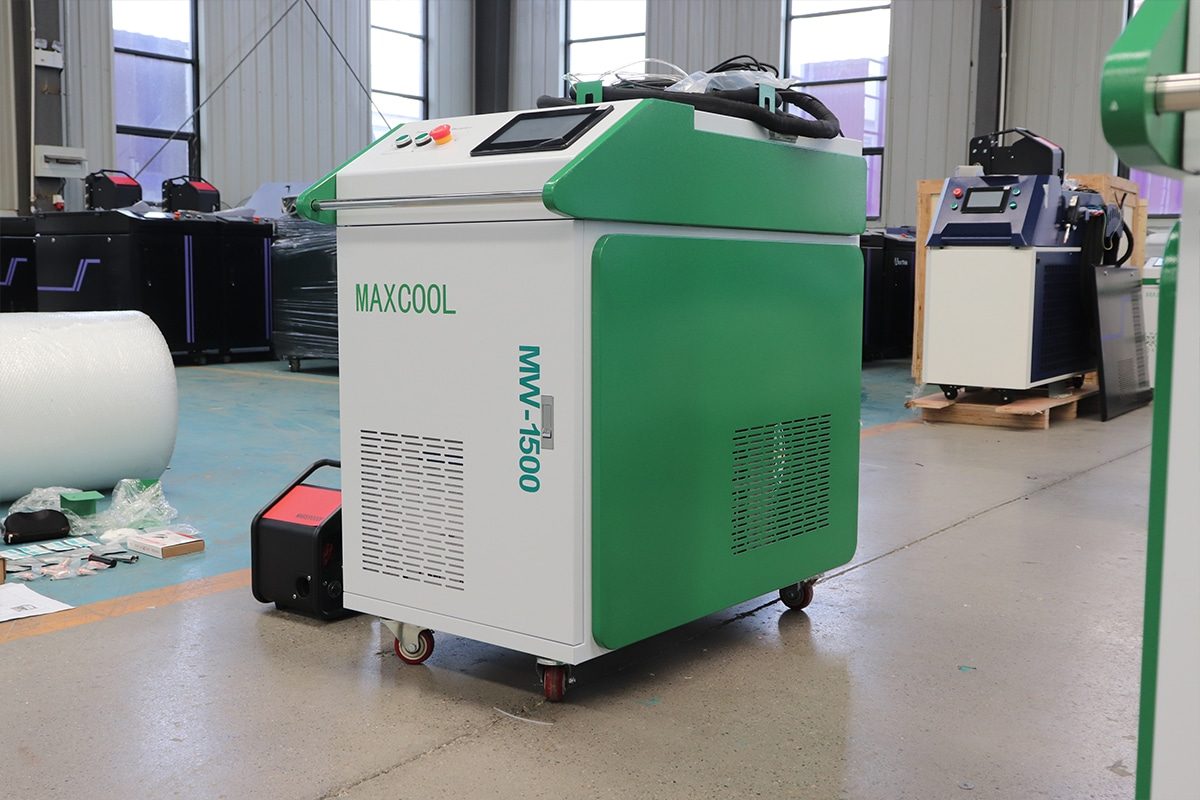
Basics of Welding Processes
Traditional Welding Methods
Welding is a fundamental process used to join metals and other materials by applying heat, pressure, or both to form a strong bond. Traditional welding methods encompass a range of techniques, each with its advantages, applications, and challenges. Some of the most common traditional welding methods include:
- Gas Metal Arc Welding (GMAW/MIG Welding): This process uses a continuous wire electrode fed through a welding gun, melting the wire to create the weld. It requires a shielding gas to protect the weld pool from contaminants in the atmosphere.
- Gas Tungsten Arc Welding (GTAW/TIG Welding): This method utilizes a non-consumable tungsten electrode to produce the weld. It often requires the use of filler wire, which is manually fed into the weld area, and a shielding gas like argon.
- Shielded Metal Arc Welding (SMAW/Stick Welding): This process employs a consumable electrode coated in flux, which melts and forms a slag layer to protect the weld from contaminants.
- Flux-Cored Arc Welding (FCAW): Similar to MIG welding, this process uses a continuous wire feed, but the wire is hollow and filled with flux, eliminating the need for a separate shielding gas in some applications.
Role of Welding Wire in Traditional Welding
Welding wire plays a critical role in traditional welding processes, serving as a filler material to bridge gaps, add material strength, and improve joint properties. The key functions of welding wire include:
- Filling Gaps: In many welding applications, precise joint fit-up is difficult to achieve. Welding wire compensates for gaps between workpieces, ensuring the weld maintains its structural integrity.
- Improving Mechanical Properties: Filler materials can be chosen to modify the mechanical properties of the joint, such as increasing strength, ductility, or corrosion resistance. This is particularly important when joining dissimilar metals or working with alloys prone to cracking.
- Providing Consistency: Continuous feeding of welding wire in processes like MIG welding ensures a consistent arc, reducing defects and improving weld quality.
- Versatility: By selecting different types of filler wires, welders can tailor the weld properties to meet specific application requirements, such as high-temperature resistance, improved toughness, or enhanced electrical conductivity.
Laser Welding: An Overview
How Laser Welding Works
Types of Laser Welding
Laser welding can be categorized into two primary types based on the depth of penetration and the nature of the weld produced:
- Conduction Welding: In this type of laser welding, the laser beam heats the surface of the material, melting it without penetrating deeply into the workpiece. The molten pool created on the surface spreads and forms a weld as it cools and solidifies. Conduction welding is typically used for thin materials or applications that require a smooth surface finish. The welds produced have a broad, shallow profile, making this method suitable for decorative or aesthetic applications.
- Keyhole Welding: Keyhole welding is characterized by deep penetration, achieved by focusing a high-energy laser beam that creates a vaporized “keyhole” within the workpiece. The keyhole allows the laser energy to penetrate deeply, creating a narrow, deep weld with high aspect ratios. This type of laser welding is commonly used for applications requiring strong and robust joints, such as in automotive and aerospace industries. Keyhole welding is highly effective for thick materials and provides excellent strength and depth while minimizing thermal distortion.
Does Laser Welding Require Welding Wire?
Autogenous Laser Welding
Advantages
- Simplicity and Speed: With no need for filler wire, autogenous welding simplifies the process, reducing setup time and complexity, which can result in faster production cycles.
- Cost-Effective: Autogenous welding eliminates the expense of welding wire, providing a direct cost saving on consumables.
- Reduced Thermal Input: Since autogenous welding typically requires less energy than welding with filler, it generates a smaller heat-affected zone, which minimizes distortion and preserves material properties.
- Higher Precision: Without filler material, autogenous welding allows for a narrower, more focused laser beam, enhancing accuracy and producing clean, precise welds, especially in small, intricate applications.
Disadvantages
- Limited Gap Bridging: Autogenous welding requires a high-quality joint fit-up, as it lacks the filler material necessary to bridge gaps or compensate for irregularities between workpieces.
- Restricted Material Compatibility: Some materials, particularly dissimilar metals, may require filler material to prevent issues like cracking, which autogenous welding cannot address.
- Lower Mechanical Strength: For applications that demand higher strength, autogenous welds may lack the reinforcement provided by filler material, making them less suitable for heavy-duty structural applications.
Laser Welding with Welding Wire
Advantages
- Enhanced Gap Bridging: The addition of filler material allows for better gap tolerance, enabling laser welding even when the joint fit-up is not perfect. This is particularly useful in applications where achieving precise alignment is challenging.
- Improved Mechanical Properties: Filler material can be chosen to enhance the weld’s mechanical properties, such as tensile strength, ductility, and corrosion resistance, which is essential in structural applications.
- Versatility in Material Compatibility: When welding dissimilar metals or alloys prone to cracking, welding wire can help prevent brittle intermetallic compounds, providing a more robust and reliable weld.
- Ability to Modify Weld Composition: Different types of filler materials can be used to adjust the weld’s composition, which can enhance characteristics like corrosion resistance or hardness, depending on the application’s requirements.
Disadvantages
- Increased Complexity: Adding filler material requires additional equipment, such as a wire feeder, which adds complexity to the welding setup and may require more frequent maintenance.
- Higher Costs: Filler wire introduces an additional consumable cost, making this approach more expensive than autogenous welding.
- Reduced Welding Speed: The need to feed filler material can slow down the welding process compared to autogenous welding, potentially affecting production efficiency in high-volume applications.
- Potential for Thermal Distortion: The additional heat input required to melt both the base material and the filler wire can increase the heat-affected zone, potentially leading to slight distortion or reduced material properties in some applications.
Factors Influencing the Use of Welding Wire in Laser Welding
Joint Design and Geometry
The configuration and fit-up of the joint play a critical role in determining whether welding wire is necessary.
- Butt Joints: In tightly fitted butt joints, autogenous welding is often sufficient, as the laser can effectively fuse the edges without needing additional material. However, if gaps are present, welding wire may be needed to fill the space and ensure a sound weld.
- Lap and Fillet Joints: These joints can benefit from filler material to achieve adequate penetration and ensure joint strength. Welding wire helps create a stronger, more reliable joint by providing additional material to bridge the surfaces in lap and fillet joints.
- Misalignments and Gaps: In many industrial applications, achieving perfect joint alignment can be challenging. Welding wire provides flexibility to accommodate gaps and misalignments between workpieces, ensuring the weld maintains its integrity.
Material Type and Thickness
Different materials respond uniquely to laser welding, and thickness is a significant factor in determining the need for filler material.
- Thin Materials: For thin materials, autogenous welding is generally preferred, as the laser can create a strong weld without excessive melting or burn-through. Adding filler material could introduce unnecessary heat, risking distortion.
- Thick Materials: Welding thicker sections often requires filler material to ensure complete penetration and avoid defects like undercuts or incomplete fusion. Welding wire provides the necessary reinforcement to form a solid joint, especially in thicker metals that demand deeper welds.
- Material-Specific Requirements: Certain materials, such as titanium and stainless steel, may require welding wire to meet strength and corrosion resistance requirements. Aluminum alloys, which are prone to cracking, can also benefit from filler material to prevent defects and improve weld strength.
Metallurgical Considerations
Metallurgical compatibility and the weld’s final properties are critical in determining the need for welding wire, especially when working with dissimilar metals.
- Crack-Prone Materials: Some metals, such as high-carbon steels and certain aluminum alloys, are prone to hot cracking during welding. Adding filler material can reduce the risk of cracks by altering the weld pool’s composition and cooling characteristics.
- Dissimilar Metals: When joining dissimilar materials, such as stainless steel to carbon steel or aluminum to copper, filler material can help bridge the metallurgical differences. Using an appropriate filler wire minimizes the formation of brittle intermetallic compounds, ensuring a compatible weld with balanced mechanical properties.
- Alloy Modification: For applications requiring specific weld properties, such as increased corrosion resistance or hardness, filler materials can be chosen to modify the weld composition to meet these requirements.
Mechanical Property Requirements
The intended mechanical performance of the welded joint often determines whether filler material is necessary.
- Strength and Ductility: Applications that require high tensile strength or ductility may benefit from welding wire. By choosing filler materials with enhanced mechanical properties, the weld can meet the structural demands of the application.
- Wear and Corrosion Resistance: For components exposed to harsh environments or wear, using filler material with high corrosion or wear resistance can improve the weld’s durability, extending the life of the welded part.
- Thermal Expansion and Contraction: In assemblies where thermal expansion could lead to stresses in the weld, filler material can help create a weld with properties that balance or absorb these stresses, preventing premature failure.
Production Considerations
Practical production aspects, such as welding speed, cost, and equipment, influence the decision to use welding wire.
- Welding Speed: High-speed production environments often prefer autogenous welding for its simplicity and efficiency. Adding welding wire can slow down the process, especially in automated systems, as the wire feed rate must align with the laser speed.
- Cost Constraints: Filler material represents an additional cost in terms of consumables, making autogenous welding more cost-effective in applications that do not require it. However, if strength or reliability would be compromised without welding wire, the extra cost may be justified.
- Automation and Accessibility: In automated setups, welding wire adds complexity to the system, potentially increasing maintenance requirements. However, if automated systems are configured for precise wire feeding, they can accommodate filler material reliably.
- Joint Accessibility: Some applications may have limited access to the weld area, making it difficult to introduce filler material effectively. In such cases, autogenous welding may be more practical due to its focused, streamlined approach.
Selecting the Right Welding Wire
Material Compatibility
The welding wire must be compatible with the base materials being joined to ensure a strong, defect-free bond. When selecting the appropriate filler material, it is essential to consider factors such as:
- Base Metal Composition: Matching the welding wire’s composition to the base metals prevents issues such as cracking or weak bonds.
- Dissimilar Metal Joining: In applications involving the welding of different metals, selecting a filler wire that bridges their metallurgical differences is crucial to ensure a stable and strong weld. For example, when welding stainless steel to carbon steel, a suitable filler material is necessary to mitigate the formation of brittle phases.
Mechanical Properties
The mechanical properties of the welding wire play a significant role in the overall performance of the weld. Depending on the specific application, desired mechanical properties may include:
- Tensile Strength and Toughness: The filler wire should enhance the weld’s mechanical strength and toughness, especially in structural applications or when joining high-strength alloys.
- Ductility: In applications where flexibility and bending stresses are present, a more ductile filler wire can improve the weld’s resilience and reduce the risk of cracking or failure.
- Corrosion Resistance: For components exposed to harsh environments, selecting a filler material with high corrosion resistance can protect the weld and ensure long-term durability.
Chemical Composition
The chemical composition of the welding wire must be carefully chosen to achieve a compatible and strong weld with the base materials. Consider the following:
- Alloying Elements: The presence of certain alloying elements, such as chromium, nickel, or molybdenum, can enhance properties like corrosion resistance, strength, or heat resistance.
- Metallurgical Behavior: Understanding the interaction between the filler and the base metals during the welding process helps prevent issues like excessive hardening, brittleness, or the formation of unwanted phases.
- Tailored Composition: In specialized applications, it may be necessary to use filler materials with specific chemical compositions to meet stringent industry standards or unique requirements.
Diameter of the Wire
The diameter of the welding wire affects its melting rate, deposition rate, and the overall welding process.
- Thin Wire: Thinner wires melt more quickly and are suitable for applications requiring precise control and minimal heat input. This makes them ideal for thin materials or intricate welds.
- Thicker Wire: Thicker wires offer higher deposition rates and are better suited for welding thick materials or filling large gaps. They provide robust welds but may require higher laser power and precise control to avoid excessive heat input and distortion.
- Wire Feed Speed: The wire diameter must be compatible with the wire feed system to ensure a consistent and controlled feed rate during welding, minimizing defects like porosity or uneven welds.
Coatings and Cleanliness
The surface condition of the welding wire can significantly impact the quality of the weld.
- Wire Coatings: Some welding wires have coatings that improve their feedability, reduce oxidation, and enhance arc stability during the welding process. For example, copper-coated wires are commonly used to improve conductivity and protect against corrosion.
- Cleanliness: Contaminants such as dirt, oil, or rust on the surface of the wire can introduce impurities into the weld, leading to defects like porosity or inclusions. Ensuring that the welding wire is clean and free from contaminants is critical for achieving a high-quality weld.