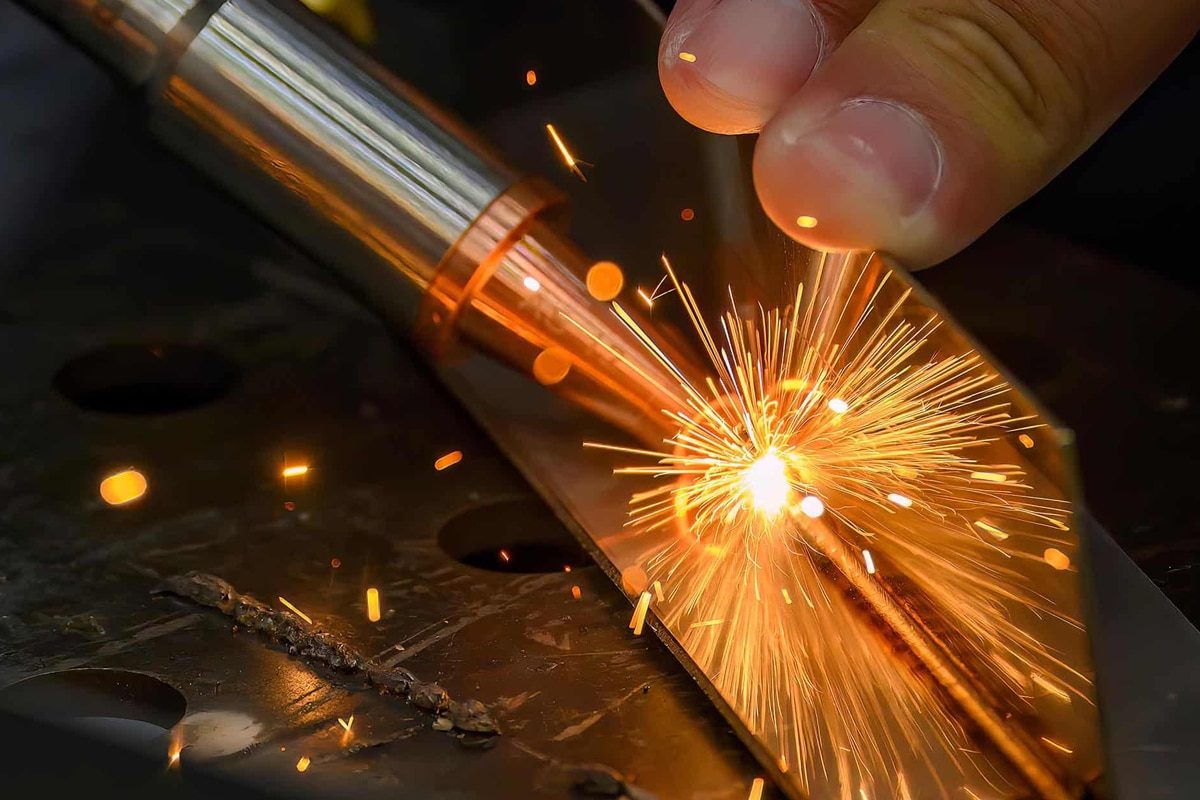
Understanding Laser Welding
What Is Laser Welding?
How Does Laser Welding Work?
Fiber laser welding operates by concentrating a high-energy laser beam onto the workpiece, generating intense heat that melts the material at the joint. The molten metal flows together and solidifies to form a seamless weld. Key aspects of how fiber laser welding works include:
- Laser Beam Delivery: A high-power laser is transmitted through a flexible fiber optic cable, allowing precise energy delivery even to hard-to-reach areas.
- Focusing and Spot Size Control: The laser is focused through optics to a small spot, creating a high energy density that melts the material instantly. Adjusting the focus can optimize penetration depth and weld width.
- Keyhole or Conduction Mode: In keyhole welding, the high energy density vaporizes the material, creating a small keyhole that ensures deeper penetration. In conduction welding, the beam melts the surface only, forming a shallow, smooth weld.
- Weld Pool Formation and Solidification: As the laser moves along the joint, the molten material forms a weld pool that cools and solidifies quickly, creating a continuous, strong seam.
- Shielding Gas Use: In many cases, a shielding gas—such as argon, helium, or nitrogen—is used to protect the molten pool from oxidation and contamination, resulting in cleaner, defect-free welds.
- Automation and Precision: Fiber laser welding is compatible with robotic arms and CNC systems, enabling fast, repeatable welds with high accuracy. This makes it ideal for large-scale production environments.
Applications of Fiber Laser Welding
Fiber laser welding is widely used in industries that require precision, speed, and reliability. Fiber laser welding machines are designed to handle diverse applications, such as:
- Automotive Industry: Fiber lasers are used for welding car frames, battery housings, and gear parts, ensuring lightweight yet strong assemblies essential for modern vehicles.
- Aerospace Industry: Precision components such as turbine blades, fuel injectors, and structural assemblies are welded with fiber lasers to meet strict performance and safety standards.
- Electronics Manufacturing: Fiber laser welding enables the joining of small, delicate parts in sensors, circuit boards, and micro-electronics with minimal thermal damage.
- Medical Device Production: Used for welding surgical instruments, implants, and medical sensors, fiber lasers provide the precision needed to meet stringent healthcare regulations.
- Metal Fabrication and Machinery: Fiber laser welding is ideal for joining various metals and alloys in industrial machinery, pipelines, and construction components, ensuring strength and durability.
- Energy Sector: Fiber lasers are used in the production of batteries, solar panels, and fuel cells, where high-efficiency welding is critical for performance.
Role of Gas in Welding Processes
General Purpose of Shielding Gases in Welding
Common Gases Used in Welding
Several gases are commonly employed in fiber laser welding, each providing specific advantages depending on the material and application. The most widely used gases include:
- Argon: An inert gas known for its ability to provide stable coverage and excellent protection against oxidation. Argon is suitable for welding non-ferrous metals like aluminum and stainless steel.
- Helium: With higher thermal conductivity than argon, helium allows for deeper penetration and faster welding speeds. It is often used in applications requiring high heat input, such as thick or reflective materials like copper and brass.
- Nitrogen: Primarily used with stainless steel and other alloys, nitrogen helps improve penetration and can influence mechanical properties. However, it must be used cautiously, as it can cause nitriding in some materials.
- Gas Mixtures: Combining gases (such as argon-helium or argon-nitrogen) allows manufacturers to balance arc stability, heat input, and oxidation protection, optimizing the welding process for specific applications.
Effects of Shielding Gases on Weld Quality
The choice of shielding gas can significantly influence the quality and performance of the weld. Key effects include:
- Protection from Oxidation and Contamination: Shielding gases prevent atmospheric gases from interacting with the molten pool, ensuring that the weld remains strong, clean, and free of defects. This is particularly crucial when welding reactive materials like aluminum or titanium.
- Enhanced Weld Penetration and Heat Control: Gases like helium increase thermal conductivity, improving heat distribution and allowing for deeper penetration. This results in stronger joints, especially when welding thick or reflective metals.
- Improved Weld Appearance and Surface Finish: Proper shielding minimizes spatter and discoloration, resulting in a smooth, visually appealing weld. This is essential in industries like electronics and medical devices, where aesthetics and precision are crucial.
- Reduced Defects: Effective gas shielding prevents porosity, cracking, and other defects that can compromise the structural integrity of the weld.
- Process Efficiency and Speed: Using the correct shielding gas can improve the welding speed and reduce the need for post-weld cleaning or finishing, enhancing productivity.
Does Laser Welding Require Gas?
Explanation of Whether Gas Is Required in Laser Welding
Conditions Under Which Gas Is Used or Not Used
When Gas Is Used:
- Welding Reactive Metals: Materials such as aluminum, titanium, and stainless steel are prone to oxidation. Gas shielding helps prevent contamination.
- High-Precision Applications: In industries like aerospace, medical devices, and electronics, gas is used to ensure the highest quality and defect-free welds.
- High-Power Laser Welding: At high power levels, the interaction between the laser beam and the material can create plasma. Shielding gases help suppress plasma to ensure that the laser energy fully penetrates the material.
- Aesthetic or Visible Welds: When weld appearance matters, shielding gas reduces spatter, discoloration, and oxidation, ensuring a smooth, clean surface finish.
When Gas May Not Be Necessary:
- Non-Critical Applications: In cases where minor defects or surface oxidation are acceptable, such as temporary or non-structural components, gas can be omitted to reduce costs.
- Welding in Controlled Environments: Welding in vacuum chambers or inert atmospheres can eliminate the need for additional shielding gas.
- Certain Steels or Alloys: Some non-reactive metals, such as carbon steel, may not require gas shielding under low-power settings or if oxidation is not a concern.
- Low-Power Laser Welding: When using low-power lasers, plasma formation is minimal, and the weld can often be completed without shielding gas.
Types of Gases Used in Laser Welding
The type of shielding gas used in fiber laser welding influences the weld’s quality, penetration, and appearance. Fiber laser welding machines are compatible with a range of gases to suit various welding applications:
- Argon: A widely used inert gas that offers excellent protection from oxidation. It is cost-effective and ideal for welding non-ferrous metals like aluminum and stainless steel.
- Helium: Known for its high ionization potential, helium is often used to suppress plasma formation in high-power welding. It also increases heat input, allowing deeper penetration in thick or reflective materials like copper and brass.
- Nitrogen: Frequently used with stainless steel, nitrogen enhances weld penetration and influences mechanical properties. However, it can cause nitriding in certain metals, so its use requires careful consideration.
- Gas Mixtures: Custom gas blends, such as argon-helium or argon-nitrogen mixtures, provide a balance of benefits. These mixtures optimize welding performance by combining stability, heat input, and oxidation resistance for specific applications.
Functions of Shielding Gas in Laser Welding
Protecting the Molten Pool from Oxidation
Assisting in Heat Transfer
Stabilizing the Laser Beam
Reducing Plasma Formation
Types of Gases Used in Laser Welding
Argon
Advantages of Argon:
- Cost-effective and widely available.
- Provides stable coverage and good protection against oxidation.
- Suitable for a wide range of materials, especially non-ferrous metals.
Disadvantages of Argon:
- Lower thermal conductivity compared to other gases like helium, resulting in less heat transfer.
- In some cases, it may cause arc instability, especially at higher welding speeds.
Helium
Advantages of Helium:
- Provides better heat transfer, allowing for deeper penetration and faster welding speeds.
- Reduces plasma formation, particularly in high-power laser applications.
- Suitable for welding reflective materials like copper and aluminum.
Disadvantages of Helium:
- More expensive than argon, increasing operational costs.
- Requires higher flow rates due to its lower density.
Nitrogen
Advantages of Nitrogen:
- Enhances penetration in certain materials, such as stainless steel.
- Cost-effective compared to other gases.
- Can improve weld strength in some applications.
Disadvantages of Nitrogen:
- Can react with metals to form nitrides, which may weaken the weld.
- Not suitable for all materials, particularly reactive metals like aluminum.
Gas Mixtures
Advantages of Gas Mixtures:
- Customizable to suit specific welding needs, offering a balance of protection and heat transfer.
- Helps optimize weld quality for particular materials and applications.
- Can reduce costs by using a lower percentage of expensive gases like helium.
Disadvantages of Gas Mixtures:
- Requires careful selection and adjustment based on the material and welding conditions.
- May introduce complexity in process setup and monitoring.
Gasless Laser Welding
Situations Where Gas May Not Be Required
While shielding gas is often used to enhance the quality and performance of laser welding, there are situations where gas may not be necessary. In these scenarios, manufacturers can eliminate the need for gas to reduce operational costs, simplify the welding setup, or adapt to specific project requirements. Some instances where gasless laser welding may be feasible include:
- Non-Critical Applications: When weld appearance, oxidation, or minor defects are not a concern, such as in temporary structures or non-structural components, gas can be omitted.
- Certain Steel Materials: Some low-carbon steels or non-reactive metals can be welded without shielding gas, especially at lower power settings, where the risk of oxidation and contamination is minimal.
- Controlled Environments: In specialized environments, such as inert atmosphere chambers or vacuum systems, the absence of atmospheric contamination reduces the need for shielding gas.
- Low-Power Laser Welding: At lower laser power levels, the risk of plasma formation and oxidation decreases, allowing for gasless welding without significant compromises in quality.
Limitations and Challenges
Although gasless laser welding offers cost savings and simplicity, it presents certain limitations and challenges:
- Oxidation and Surface Contamination: Without gas, the molten weld pool is exposed to oxygen and other atmospheric gases, increasing the risk of oxidation, discoloration, and contamination.
- Weaker Welds: Welds performed without shielding gas may exhibit lower mechanical strength due to increased porosity and surface defects.
- Aesthetic Issues: The absence of gas can lead to spatter, discoloration, and rough weld surfaces, which may be unacceptable in applications where appearance is critical, such as jewelry or electronics.
- Limited Material Compatibility: Gasless welding is not suitable for highly reactive metals like aluminum, copper, or titanium, which are prone to oxidation and require shielding to achieve high-quality welds.
- Reduced Process Stability: Plasma formation can become an issue at higher laser powers, reducing the efficiency of the laser beam and compromising weld depth and quality.
Materials and Applications Suitable for Gasless Laser Welding
Although gasless laser welding has its challenges, there are specific materials and applications where it can be a viable option:
- Carbon Steel: For low-power applications or non-critical welds, certain types of carbon steel can be welded without shielding gas.
- Temporary Structures: Components that are not intended for long-term use or do not require structural integrity may be welded without gas.
- Controlled Environments: Welding in inert chambers or vacuum systems can negate the need for shielding gas, as atmospheric gases are already excluded.
- Prototyping and Repairs: In some cases, gasless laser welding is used for quick repairs or prototypes where speed and cost are prioritized over long-term durability or aesthetics.
Factors Influencing the Use of Gas in Laser Welding
Material Type
The type of material being welded is one of the most significant factors in deciding whether to use shielding gas.
- Reactive Metals: Metals such as aluminum, copper, titanium, and stainless steel are prone to oxidation. Without shielding gas, these materials may develop surface defects, weakening the weld and impairing its appearance.
- Non-Reactive Metals: Low-carbon steels and certain alloys are less sensitive to atmospheric gases, making them more suitable for gasless welding, especially in low-power or non-critical applications.
- Weldable Alloys: Complex alloys used in aerospace or medical industries often require shielding gas to prevent contamination and ensure weld strength.
Laser Type and Power
The type and power of the laser also influence whether shielding gas is necessary:
- High-Power Lasers: At higher power levels, the interaction between the laser and the material can create plasma, which absorbs and scatters the laser energy, reducing weld penetration. Gases such as helium suppress plasma formation, ensuring deeper and more precise welds.
- Low-Power Lasers: For thin materials or low-power applications, plasma formation is minimal, and gas may not be required.
- Continuous vs. Pulsed Laser Welding: Continuous lasers often demand gas to maintain weld consistency, while pulsed lasers, which generate less heat, may allow for occasional gasless welding.
Welding Speed and Environment
Operational conditions, including welding speed and environmental factors, play an important role in determining gas requirements:
- High-Speed Welding: Faster welding processes benefit from shielding gas, as it reduces spatter and prevents defects that can occur due to rapid cooling of the molten pool.
- Controlled Environments: Welding in an inert or vacuum chamber eliminates the need for shielding gas, as the atmosphere is already free from contaminants.
- Outdoor or Unstable Environments: In environments with fluctuating air currents, shielding gas ensures consistent protection and minimizes oxidation.
Quality Requirements
The required quality of the weld plays a crucial role in the decision to use shielding gas:
- High-Quality and Precision Applications: Industries such as aerospace, automotive, and medical manufacturing require flawless, high-strength welds, which often necessitate the use of shielding gas to prevent defects and contamination.
- Visible or Aesthetic Welds: For applications where appearance matters, shielding gas ensures a clean, spatter-free surface finish.
- Non-Critical Welds: In cases where minor defects are acceptable (e.g., temporary structures or internal components), welding without gas may be an option to reduce costs.