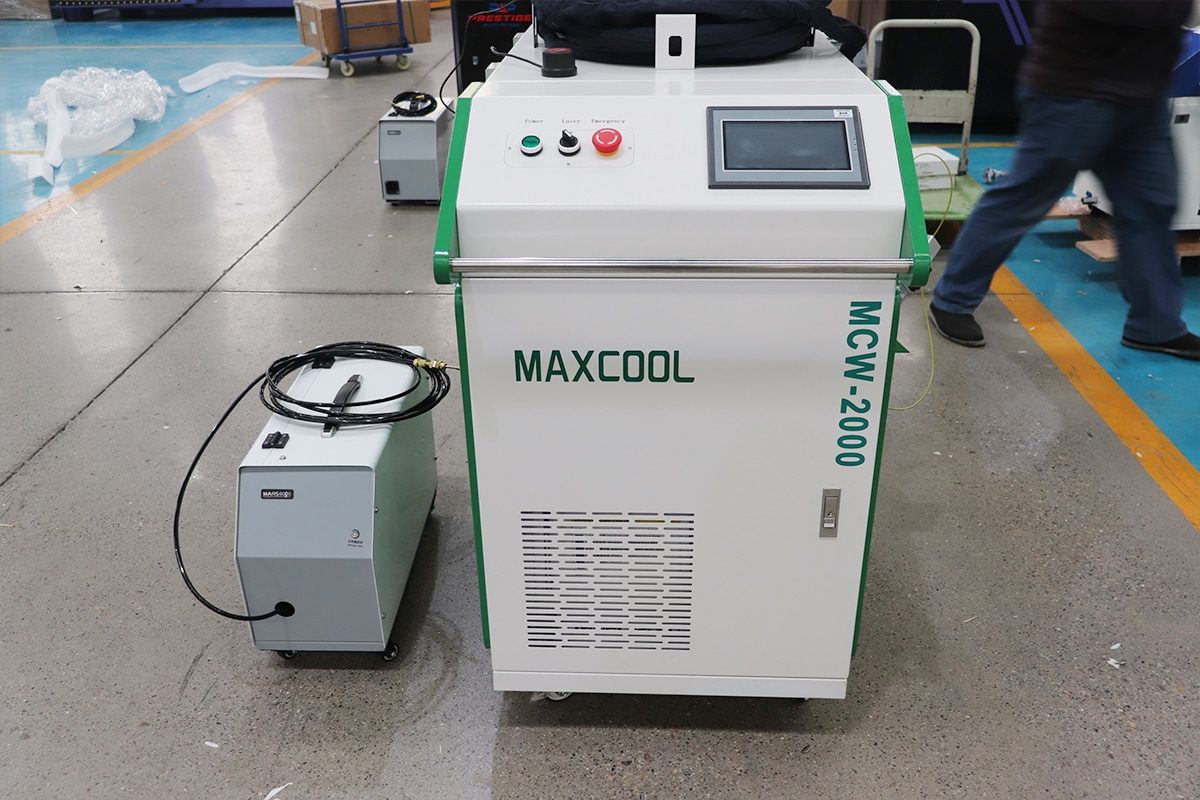
The Science of Laser Welding
How Lasers Work
- CO2 lasers (wavelength around 10.6 µm)
- Nd:YAG lasers (wavelength around 1.06 µm)
- Fiber lasers (wavelength also around 1.06 µm, but generated differently)
- Diode lasers (variable wavelengths in the near-infrared range)
Basic Principles of Laser Welding
Laser welding focuses a laser beam on the joint between two metals or materials, melting and fusing them along the seam. The key variables include:
- Power Density: Higher power or a smaller focal spot leads to higher energy density, allowing rapid and deep penetration into the workpiece.
- Travel Speed: Because of the concentrated energy, laser welding often proceeds at a faster travel speed than traditional arc welding.
- Shielding Gas: Like many welding processes, laser welding can use inert gases such as argon or helium to protect the weld pool from oxidation.
Laser welding can be categorized into two main modes:
- Conduction Welding: The laser melts the surface of the material, and heat conduction dominates. This is used for shallow welds.
- Keyhole Welding: The laser power is sufficiently high to vaporize material, creating a “keyhole.” The high aspect ratio of this keyhole allows deeper weld penetration.
Advantages and Applications
Laser welding provides a variety of benefits:
- Precision and High Speed: Small, highly localized weld pools allow for precise and automated welding at high speeds.
- Minimal Distortion: The heat-affected zone is small, reducing warping in delicate or thin components.
- Clean Welds: Laser welds are often smooth and require minimal post-processing.
- Automation: Laser welding is easily automated for production lines, including robotics and CNC systems.
The Overlap of Optical Hazards and Welding
Laser Welding vs. Traditional Welding
Emission Spectra and Visibility
Beam Characteristics
Heat Input and Fume Generation
Personal Protective Equipment (PPE) Specifics
Potential Hazards of Laser Welding
Ocular Hazards
The eyes are extremely vulnerable to the concentrated radiation of laser beams. The retina (for visible and near-IR lasers), cornea, and lens can be damaged by exposure. Injuries can include:
- Retinal Burns: Caused by intense light focusing on the retina, leading to permanent vision loss or blind spots.
- Photokeratitis: Akin to “welder’s flash,” can occur from UV exposure, though UV lasers in welding are less common.
- Cataracts: Chronic exposure to IR can increase the likelihood of developing cataracts.
Skin Hazards
Respiratory Hazards
Laser welding can vaporize metal and create fumes. The type of fume depends on the base materials, coatings, and fillers. Breathing in metal particulates can lead to acute or chronic respiratory issues. Standard procedures to mitigate fumes include:
- Local Exhaust Ventilation (LEV): Often used to suck away fumes at the weld site.
- Respiratory Protective Equipment (RPE): Masks or respirators, especially when welding metals like stainless steel or nickel alloys that can produce toxic fumes.
Other Considerations
- Fire Hazards: Concentrated heat from a laser can ignite nearby flammable materials. Proper housekeeping is necessary.
- Electrical Hazards: Laser systems involve power supplies and cooling systems that can pose electrical risks if improperly maintained.
- Mechanical Hazards: Automated laser welding systems involve moving parts, robotic arms, or conveyor systems.
Protective Equipment for Laser Welding
Laser Safety Glasses
For many laser applications, the most critical piece of PPE is laser safety glasses or goggles. These glasses are specially designed with optical filters to attenuate the laser wavelength. The key specifications include:
- Optical Density (OD): This is a log-scale measure of how effectively the lens attenuates a particular wavelength. For instance, if your laser operates at 1,064 nm, you might need an OD of 5 or 6 (or higher) to reduce the power to a safe level.
- Wavelength Coverage: The glasses must specifically list the wavelength range they protect against. Many industrial lasers operate near 1,060 nm, but you might also have UV or green lasers in some specialized contexts.
- Visible Light Transmission: While the glasses need to block the laser wavelength, they must allow enough visible light to pass so you can see your work.
Protective Clothing and Gloves
Laser welding often produces less spatter than arc welding, but protective clothing is still important:
- Fire-Resistant (FR) Clothing: Shirts, jackets, or aprons made from FR materials help protect against sparks or splatter.
- Gloves: Depending on the intensity of the welding process, heat-resistant gloves can protect hands from burns.
Welding Helmets for Laser Welding
The “welding helmet” is a face shield designed to protect the welder’s head, face, and neck from sparks, spatter, and harmful radiation. In arc welding, the helmet typically contains a dark welding lens or an auto-darkening filter (ADF). This lens protects against intense visible light, UV, and IR. For laser welding, you need to consider:
- Wavelength-Specific Filters: If your laser is near-infrared, you need a filter that blocks that specific wavelength range to a safe level.
- OD Requirements: The lens or filter in the helmet should provide the required optical density for your laser.
- Enclosure vs. Open Beam: If the laser welding system is fully enclosed, you might not need the same helmet because the laser hazard is contained. If the system is open or partially enclosed, eye protection (and possibly face/neck protection) is crucial.
Respiratory and Hearing Protection
Depending on the environment, you may need:
- Respirators or Masks to filter out metal fumes.
- Ear Protection if there is high noise from auxiliary equipment or if the welding process (especially pulsed lasers) generates noise spikes.
Additional Safety Measures
Beyond personal protective equipment, laser welding safety may involve:
- Beam Enclosures or Barriers: Physical barriers to block or contain stray beams.
- Interlocks: Safety interlock systems that shut off the laser if the enclosure is opened.
- Warning Signs and Indicators: Visual warnings like “Laser On” lights, hazard zone markings, etc.
- Training and Standard Operating Procedures: A well-trained workforce familiar with emergency procedures and the correct use of PPE.
Criteria for Selecting Welding Helmets for Laser Welding
If you decide that a welding helmet is appropriate, particularly for open laser welding scenarios, here are some criteria:
- Compatible Wavelength Range: Laser filters must list the exact wavelength or range they protect against. For instance, if your fiber laser runs at 1,064 nm, ensure the helmet filter includes coverage at that wavelength with sufficient OD.
- Optical Density (OD): Check your laser’s output power to determine the necessary OD. For powerful Class 4 lasers, you might need an OD of 5, 6, or higher. Verify the recommended OD in the laser safety manual or by consulting a certified Laser Safety Officer (LSO).
- Auto-Darkening Feature: Traditional arc welding helmets often rely on an auto-darkening filter (ADF) that switches from a light state to a dark state when the arc is struck. For laser welding, the auto-darkening function may or may not be as crucial, but be aware that standard ADFs are designed primarily for the visible spectrum from arcs; they might not provide adequate coverage for near-infrared or other specific laser wavelengths.
- Comfort and Ergonomics: Welding tasks can last for extended periods. A helmet that is heavy or poorly balanced can lead to neck strain. Look for designs that distribute weight evenly and have adjustable headgear.
- Clarity of Vision: Laser safety filters can be quite dark at specific wavelengths. Ensure that you can still see enough of the work area. Some filters provide a “multi-wavelength” approach, where they specifically block hazardous wavelengths but allow more visible light through.
- Durability and Certification: The helmet should meet ANSI Z87.1 (in the U.S.) or EN 175 (in Europe), plus any relevant laser-specific standards like EN 207. Look for markings that indicate compliance.
- Integration with Other PPE: If you need hearing protection, respirators, or other equipment, ensure the helmet design accommodates these accessories.
Maintaining Safe Laser Welding Environments
Laser Safety Program
Any facility using Class 3B or Class 4 lasers should have a Laser Safety Program with a designated Laser Safety Officer (LSO). This person is responsible for:
- Performing hazard evaluations
- Selecting appropriate control measures (engineering, administrative, and PPE)
- Training personnel
- Maintaining records of inspections, audits, and incidents
Training and Awareness
Operators, maintenance staff, and even visitors near a laser welding cell should receive appropriate training. This might include:
- Laser hazard awareness: Understanding the risks of direct and diffuse reflections.
- Correct PPE usage: Knowing how to select, fit, and maintain laser eyewear or helmets.
- Emergency procedures: What to do if there is a suspected overexposure or if a laser interlock fails.
Engineering Controls
The first line of defense is always engineering controls, such as enclosures and interlocks. By containing the beam, you reduce reliance on individual PPE. Some examples:
- Fully or partially enclosed work cells
- Automatic shut-off if a door is opened
- Beam dumps that safely terminate stray reflections
Administrative Controls
Administrative controls can include:
- Standard Operating Procedures (SOPs) that specify safe practices.
- Restricted access or “Laser On” warning lights outside the work area.
- Scheduling laser operations at times when fewer people are present reduces potential exposure.
Inspections and Equipment Checks
Lasers, like any equipment, need regular maintenance:
- Beam alignment checks to ensure the beam is correctly targeted and not scattering unpredictably.
- Protective eyewear inspections to look for scratches or degradation of filter coatings.
- Helmet lens or face shield inspections for cracks or signs of wear.
Best Practices and Recommendations
Perform a Hazard Analysis
Before undertaking laser welding, conduct a thorough risk assessment. Identify:
- Laser power and wavelength
- Required optical density for eyewear
- Potential reflections or hazards in the workspace
- Ventilation and fume extraction needs