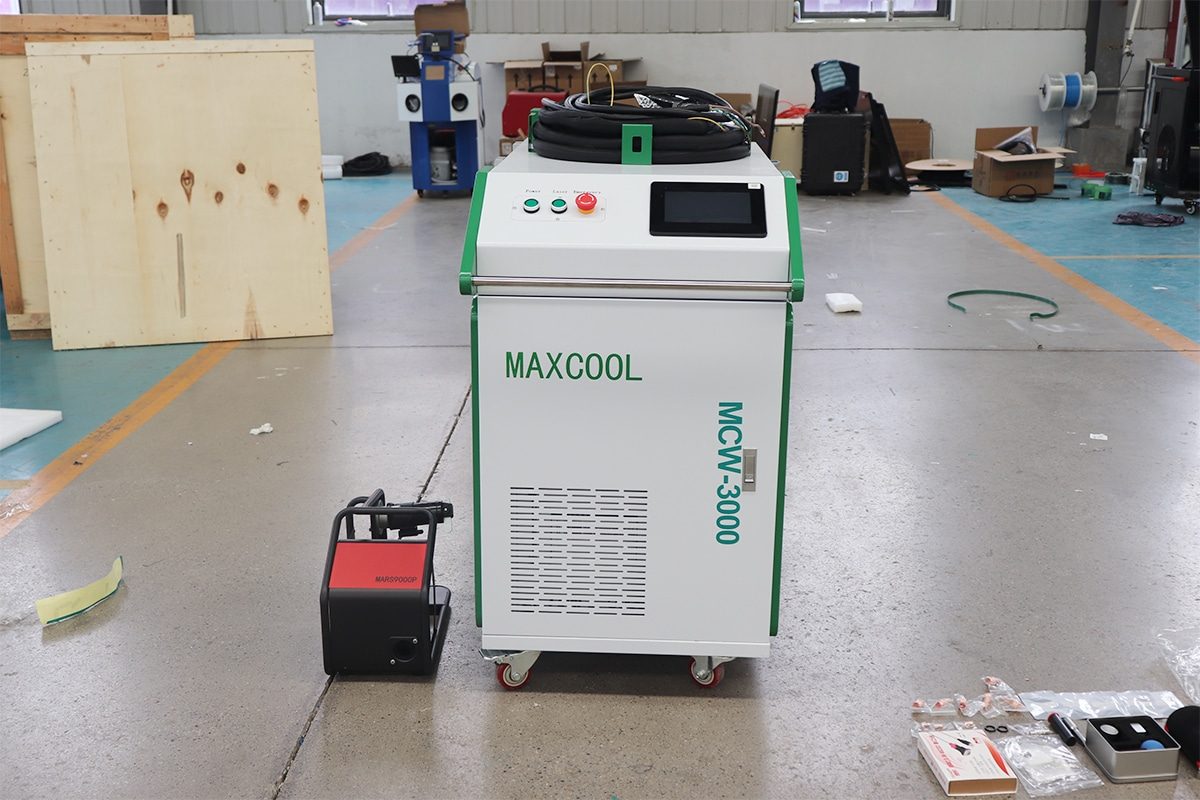
Fundamentals of Laser Welding
What is a Laser?
Basic Principle of Laser Welding
Laser welding works by directing a high-energy laser beam onto the surface of the material to be joined. The concentrated heat causes localized melting, allowing the materials to fuse upon cooling. There are two primary modes of laser welding:
- Conduction Mode Welding: The laser heats the surface, and the heat is conducted into the material, creating a shallow weld. This mode is suitable for thin materials and aesthetic welds.
- Keyhole Mode Welding: Due to its high energy density, the laser generates a small, deep cavity (keyhole) in the material, producing deep penetration welds. This mode is used for high-strength applications in thick materials.
Key Parameters in Laser Welding
Several factors influence the quality and efficiency of laser welding:
- Laser Power: Determines the energy input; higher power enables deeper penetration but requires precise control to avoid material distortion.
- Welding Speed: Affects the weld’s depth and quality; too fast can cause incomplete fusion, while too slow can lead to excessive heating.
- Beam Spot Size: A smaller spot size results in higher energy density for fine, detailed welding, whereas a larger spot size is used for broader welds.
- Focus Position: The focal point of the laser must be precisely adjusted to optimize penetration and minimize defects.
- Shielding Gas: Gases like argon or nitrogen are used to prevent oxidation and enhance weld quality by stabilizing the arc.
- Material Reflectivity and Absorption: Some metals, such as aluminum and copper, have high reflectivity, requiring specialized laser sources or pre-treatments to improve energy absorption.
Key Components and Mechanisms of Laser Welding Machines
Laser Source
The laser source is the core of a laser welding machine, generating the high-energy beam required for welding. Common types of laser sources include:
- Fiber Lasers: Highly efficient, with excellent beam quality and minimal maintenance, making them ideal for industrial applications.
- Nd: YAG Lasers: Provide good penetration and can be used with optical fibers for flexible beam delivery.
- CO2 Lasers: Effective for welding non-metallic materials and certain metals but are gradually being replaced by fiber lasers due to efficiency and precision advantages.
Beam Delivery System
Focusing Optics
Focusing optics concentrate the laser beam onto a precise point on the workpiece, ensuring maximum energy density for effective welding. The key components of the focusing optics include:
- Lenses: Converge the laser beam to the desired focal point.
- Collimators: Convert diverging laser beams into parallel beams before focusing.
- Protective Glass: Shields the lens from spatter and contaminants to maintain beam quality.
Welding Head and Nozzles
The welding head houses the focusing optics and is responsible for directing the laser onto the workpiece. Nozzles are attached to the welding head and play a vital role in gas shielding, helping to prevent oxidation and control weld bead formation. Different nozzle types are used for various welding applications, such as:
- Coaxial Nozzles: Provide uniform gas shielding around the weld.
- Side-Blown Nozzles: Direct shielding gas from one side, suitable for specific joint geometries.
Motion System
The motion system controls the movement of the laser beam or the workpiece to create precise welds. There are two main types:
- Gantry Systems: Move the laser head over a stationary workpiece, ideal for large or complex parts.
- Robotic Arms: Provide flexibility and automation for intricate or multi-angle welds.
Cooling System
Laser welding generates significant heat, requiring an effective cooling system to prevent overheating and maintain stability. There are two common cooling methods:
- Air Cooling: Suitable for low-power lasers but limited in efficiency.
- Water Cooling: More effective for high-power lasers, ensuring consistent performance during prolonged welding operations.
Control Software
Advanced laser welding machines are equipped with control software that enables precise adjustment of welding parameters, automation, and real-time monitoring. Key functions include:
- Power and Pulse Control: Adjusts laser intensity based on material requirements.
- Path Programming: Defines welding trajectories for robotic or CNC-controlled systems.
- Process Monitoring: Uses sensors and cameras to ensure weld quality and detect defects.
Advantages of Laser Welding
High Precision
Minimal Distortion
Fast Welding Speeds
Versatility Across Materials
Laser welding is highly adaptable and can be used on a wide range of materials, including:
- Metals: Stainless steel, aluminum, titanium, copper, and high-strength alloys.
- Plastics: Specially formulated thermoplastics used in precision applications.
- Dissimilar Materials: Laser welding can join different metals without requiring additional filler materials, reducing material costs and enhancing joint strength.
Automation and Integration
Reduced Consumables
Clean Processes
Disadvantages of Laser Welding
Initial Capital Investment
Joint Fit-Up Tolerance
High Reflectivity Materials
Limited Penetration for High Thicknesses
Safety Hazards
Laser welding involves high-powered beams that can pose serious safety risks to operators and the surrounding environment. Potential hazards include:
- Eye and Skin Damage: Direct or scattered laser radiation can cause severe injuries, requiring the use of protective eyewear and shielding.
- Fume Generation: Some materials produce toxic fumes when exposed to high laser energy, necessitating proper ventilation or fume extraction systems.
- Fire Risk: The intense heat can ignite surrounding materials, making fire prevention measures essential.
Metallurgical Considerations
Laser welding’s rapid heating and cooling rates can lead to metallurgical challenges such as:
- Cracking: Certain alloys, such as high-carbon steels, may develop cracks due to thermal stress.
- Porosity: Trapped gases or impurities can cause porosity in the weld, reducing strength.
- Phase Changes: Some metals undergo undesirable phase transformations, affecting mechanical properties.
Welding Gas Requirements for Laser Welding
Purpose of Shielding Gases in Laser Welding
Shielding gases are used in laser welding to:
- Prevent oxidation and contamination of the weld pool.
- Improve weld penetration and stability.
- Reduce porosity and defects in the weld.
- Control plasma formation, which can affect energy absorption.
- Minimize spatter and ensure a smooth weld bead appearance.
Common Shielding Gases for Laser Welding
Different shielding gases are used depending on the material, welding process, and desired weld characteristics. The most commonly used gases include:
- Argon (Ar)
- Provides excellent protection against oxidation.
- Produces smooth, clean welds with minimal spatter.
- Can cause plasma formation at high power levels, potentially affecting penetration.
- Suitable for welding stainless steel, titanium, and aluminum.
- Helium (He)
- Does not form plasma, allowing better energy penetration.
- Provides deeper weld penetration, making it ideal for thick materials.
- More expensive than argon but improves welding performance for high-reflectivity metals like copper and aluminum.
- Often used in combination with argon to balance cost and effectiveness.
- Nitrogen (N2)
- Enhances weld strength and reduces oxidation in some stainless steels.
- Not recommended for materials prone to nitrogen embrittlement, such as aluminum or titanium.
- Can be used as an assist gas in laser cutting applications.
- Oxygen (O2)
- Improves energy absorption in certain metals, increasing welding speed.
- Can enhance weld penetration but may lead to oxidation if not controlled properly.
- Typically used in small percentages (e.g., mixed with argon).
- Carbon Dioxide (CO2)
- Increases penetration depth but can cause oxidation.
- Less common in laser welding but sometimes used in hybrid welding techniques.
Shielding Gas Delivery Methods
Shielding gases in laser welding are typically delivered in the following ways:
- Coaxial Nozzles: Direct gas flow around the laser beam for uniform protection.
- Side Blown Nozzles: Direct gas from one side to control spatter and oxidation.
- Trailing Shield: Protects the weld as it cools, especially useful for reactive metals like titanium.
Metals Compatible with Laser Welding
Carbon Steel
- Carbon steel is highly compatible with laser welding due to its good energy absorption and relatively low reflectivity.
- It can be welded in various thicknesses, from thin sheets to thick structural components.
- Key considerations include controlling heat input to prevent excessive hardening, cracking, or distortion.
- Shielding gases like argon or a small amount of oxygen can enhance weld quality.
Stainless Steel
- Stainless steel is widely used in laser welding due to its excellent strength, corrosion resistance, and weldability.
- The low thermal conductivity of stainless steel helps retain heat in the weld zone, promoting deep penetration.
- Proper shielding gas selection (typically argon or helium) is crucial to prevent oxidation and discoloration.
- Austenitic, ferritic, and duplex stainless steels all respond well to laser welding, but care must be taken to avoid sensitization in austenitic grades.
Aluminum
- Aluminum presents challenges in laser welding due to its high reflectivity and thermal conductivity.
- High-power fiber lasers or pulsed laser systems are typically required for effective welding.
- Helium or an argon-helium mix is used as a shielding gas to improve penetration and reduce porosity.
- Special surface treatments, such as oxide layer removal, may be necessary to enhance weld quality.
Titanium
- Titanium is an excellent candidate for laser welding due to its low density, high strength, and corrosion resistance.
- It requires a fully inert shielding gas environment (argon or argon-nitrogen mix) to prevent oxidation and contamination.
- Titanium welding is commonly used in aerospace, medical implants, and automotive applications where lightweight and durability are critical.
Copper
- Copper is challenging to weld with lasers due to its high reflectivity and thermal conductivity, which reduce energy absorption.
- Green or blue wavelength lasers (which have better absorption in copper) are more effective than traditional infrared lasers.
- Helium or a helium-argon mix is used as a shielding gas to stabilize the weld pool.
- Preheating or hybrid welding techniques (laser-arc welding) can improve weld penetration.
Brass
- Brass, an alloy of copper and zinc, is difficult to weld due to its tendency to vaporize zinc at high temperatures.
- Controlled heat input and pulsed laser welding help minimize zinc evaporation and porosity.
- Green or blue lasers improve absorption and welding efficiency.
- Proper ventilation is required to manage the fumes generated by zinc vaporization.
Nickel Alloys
- Nickel-based alloys, such as Inconel and Hastelloy, are commonly used in high-temperature and corrosive environments.
- These alloys have good laser weldability due to their moderate reflectivity and high melting points.
- Argon or helium shielding gases help prevent oxidation and ensure clean welds.
- Laser welding is widely used for nickel alloys in aerospace, chemical processing, and power generation applications.
Applications of Laser Welding
Automotive Industry
- Laser welding is widely used in the automotive sector for producing lightweight, high-strength vehicle components.
- Common applications include welding body panels, chassis components, exhaust systems, battery enclosures for electric vehicles (EVs), and airbag housings.
- The high-speed, automated nature of laser welding enables mass production while maintaining consistency and reducing defects.
- Hybrid laser welding (combining laser and arc welding) is often used for deep penetration in structural components.
Electronics Manufacturing
- The electronics industry relies on laser welding for the precision joining of small, heat-sensitive components.
- It is commonly used in battery connections, microcircuits, sensors, connectors, and semiconductor devices.
- Due to its ability to generate narrow, highly controlled welds with minimal heat input, laser welding prevents damage to delicate electronic components.
- Fine-pulse laser welding ensures high repeatability for miniature and intricate assemblies.
Medical Devices
- The medical industry requires high-precision, contamination-free welding for surgical instruments, implants, and diagnostic equipment.
- Laser welding is used for stainless steel, titanium, and nickel-based alloys in devices such as pacemakers, endoscopes, surgical tools, stents, and orthopedic implants.
- Its non-contact, clean process ensures biocompatibility and meets stringent regulatory requirements.
- Micro-welding capabilities allow the joining of extremely small and intricate medical components without affecting their integrity.
Aerospace and Defense
- The aerospace and defense industries demand strong, lightweight, and defect-free welds to ensure the safety and durability of aircraft and military equipment.
- Laser welding is used in fuel tanks, engine components, turbine blades, structural airframe parts, and missile guidance systems.
- Its deep penetration and ability to join dissimilar metals help create advanced materials for spacecraft and high-performance aircraft.
- The process improves production efficiency while maintaining the highest quality standards required for aerospace applications.
Jewelry
- The jewelry industry uses laser welding for precision repair, resizing, and assembly of intricate designs without damaging delicate materials.
- It allows jewelers to join gold, silver, platinum, and other precious metals with minimal heat impact, preserving fine details and preventing discoloration.
- Common applications include ring resizing, stone setting reinforcement, clasp repairs, and chain soldering.
- Laser welding eliminates the need for traditional soldering, which can affect the appearance and durability of jewelry pieces.
General Fabrication
- Laser welding is widely used in general metal fabrication for industrial machinery, enclosures, pressure vessels, and sheet metal assemblies.
- It enables manufacturers to produce clean, strong welds with minimal post-processing, improving overall production efficiency.
- Industries such as construction, energy, and appliance manufacturing benefit from laser welding’s ability to join various metals with high precision.
- The automation-friendly nature of laser welding makes it ideal for robotic welding systems in high-volume fabrication.
Hazards of Using Laser Welding Machines
Light Radiation
- Laser welding machines generate intense optical radiation, which can cause severe eye and skin damage.
- Direct exposure to the laser beam can result in serious eye injuries, including retinal burns or permanent vision loss. Even scattered or reflected laser light poses risks.
- Infrared (IR) and ultraviolet (UV) radiation from the welding process can cause skin burns similar to sunburn.
- Safety Measures:
- Use laser safety goggles with appropriate wavelength protection.
- Enclose the laser workstation to prevent accidental exposure.
- Train workers on safe laser handling and beam path awareness.
Heat and Fumes
- The high temperatures involved in laser welding generate intense localized heat, which can cause burns if workers accidentally come into contact with heated materials or components.
- The melting and vaporization of metals produce hazardous fumes and gases, including toxic particles from aluminum, stainless steel, and coated metals.
- Prolonged exposure to welding fumes can lead to respiratory issues and metal fume fever, especially in poorly ventilated areas.
- Safety Measures:
- Use proper ventilation systems or fume extractors to remove hazardous emissions.
- Wear heat-resistant gloves and protective clothing to prevent burns.
- Provide respiratory protection if ventilation is insufficient.
Electrical Hazards
- Laser welding machines require high-voltage power sources, posing risks of electrical shock and equipment malfunctions.
- Faulty wiring, damaged insulation, or improper grounding can lead to electrocution or electrical fires.
- Safety Measures:
- Regularly inspect power cables and electrical components for wear or damage.
- Ensure proper grounding and circuit protection in the work area.
- Train personnel on electrical safety and emergency shutdown procedures.
Fire Hazards
- The high-energy laser beam can ignite flammable materials if improperly managed, leading to fire hazards in the workplace.
- Spatter and molten metal droplets can also cause accidental fires if they come into contact with combustible substances like oil, paper, or cloth.
- Safety Measures:
- Keep flammable materials away from the welding area.
- Use non-flammable protective barriers to contain sparks and heat.
- Have fire extinguishers and emergency fire suppression systems readily available.
Mechanical Hazards
- Laser welding machines often include robotic arms, moving parts, and high-speed processing units, which can cause injuries if operators are not cautious.
- Improper handling of workpieces can lead to pinching, crushing, or cutting injuries.
- Safety Measures:
- Install safety interlocks to prevent accidental machine operation.
- Ensure proper guarding of moving parts to protect operators.
- Train workers on safe material handling and the use of automation controls.
Wire in Laser Welding
Why Use Wire in Laser Welding?
Adding wire in laser welding serves several purposes, including:
- Bridging Gaps: Helps compensate for poor joint fit-up or material inconsistencies.
- Improving Weld Strength: Enhances mechanical properties and fatigue resistance.
- Controlling Metallurgy: Allows alloying to prevent cracking or improve corrosion resistance.
- Reducing Porosity: Filler wire can reduce defects in materials prone to gas entrapment, such as aluminum.
- Adjusting Weld Profile: Used to modify the weld shape and bead appearance for aesthetic or functional purposes.
Types of Wire Feeding in Laser Welding
Wire can be introduced into the weld zone in different ways:
- Cold Wire Feeding: The wire is fed into the weld pool without preheating. This method is common in precision welding applications where minimal heat input is required.
- Hot Wire Feeding: The wire is preheated using electrical resistance before it enters the weld pool, reducing energy consumption and improving deposition efficiency.
- Arc-Assisted Wire Feeding: In hybrid laser-arc welding, an electric arc assists the melting of the wire, combining the benefits of both laser and traditional welding methods.
Wire Feeding Techniques
The wire feeding angle and position impact weld quality and efficiency. The most common techniques include:
- Leading Feed (Pushed Ahead of the Beam): Enhances penetration and is ideal for deep welds.
- Trailing Feed (Following the Beam): Used to smooth the weld bead and improve finish quality.
- Perpendicular Feed: Provides uniform distribution and minimizes defects.
Maintenance and Care of Laser Welding Machines
Regular Cleaning
Laser welding machines accumulate dust, spatter, and metal debris over time, which can impact performance and lead to component wear. Cleaning should focus on:
- Laser Optics: Lenses and mirrors must be kept free of dirt, smoke residue, and splatter to maintain beam quality. Use lint-free cloths and specialized cleaning solutions.
- Nozzles and Welding Head: Remove any metal deposits or oxidation to prevent blockages and ensure a consistent gas flow.
- Machine Exterior and Work Area: Keep the surroundings free from dust and contaminants that could interfere with sensitive machine components.
Alignment Checks
Proper beam alignment is critical for achieving high-quality welds. Misalignment can result in reduced power efficiency, uneven welds, and increased wear on optical components. Regular alignment checks should include:
- Ensuring the laser beam is properly centered within the focusing lens.
- Checking for any shifts in optical components due to vibration or accidental movement.
- Verifying the path of the beam to prevent unwanted reflections or energy loss.
Cooling System Maintenance
The cooling system prevents overheating and ensures stable machine operation. Without proper cooling, components such as the laser source and optics can degrade prematurely. Maintenance of the cooling system includes:
- Checking coolant levels and refilling with manufacturer-recommended coolant.
- Inspecting for leaks in hoses, connections, or the cooling unit.
- Cleaning the heat exchanger or cooling fans to prevent blockages that could reduce cooling efficiency.
- Replacing coolant filters as needed to maintain system cleanliness.
Calibration
Over time, laser power output and focus may drift due to prolonged usage. Regular calibration ensures that the machine continues to perform at optimal levels. Calibration tasks include:
- Verifying laser power output with a power meter to ensure consistency.
- Adjusting focus and beam parameters to match material thickness and welding requirements.
- Testing weld penetration and consistency on sample materials before production runs.
Routine Inspections
Conducting routine inspections helps identify potential issues before they lead to costly breakdowns. A thorough inspection checklist should include:
- Electrical Components: Checking for loose connections, worn-out wiring, or faulty switches.
- Gas Supply System: Ensuring proper flow and pressure for shielding gases to maintain weld quality.
- Software and Control Systems: Running diagnostics to ensure that automation and programming functions are operating correctly.
- Mechanical Components: Examining motion systems, robotic arms, and guides for smooth operation and wear.
Selecting the Right Laser Welding Machine
Application Requirements
The first step in selecting a laser welding machine is to assess the specific application requirements. Key factors to consider include:
- Material Type: Different metals and alloys require specific laser wavelengths and power levels for optimal welding results. For example, aluminum and copper require high-power fiber lasers or special wavelength lasers to overcome reflectivity issues.
- Weld Joint Type: Consider whether the application requires deep penetration welding, precision micro-welding, or spot welding.
- Production Volume: High-volume production lines benefit from automated or robotic laser welding systems, while low-volume or custom fabrication may require a more flexible setup.
- Weld Quality and Strength: Industries such as aerospace and medical devices demand defect-free, high-strength welds, requiring advanced control features and precision optics.
Laser Source Considerations
The choice of laser source impacts welding quality, efficiency, and compatibility with different materials. The most common laser types include:
- Fiber Lasers: Highly efficient, with excellent beam quality, making them ideal for welding steel, aluminum, and high-strength alloys.
- Nd: YAG Lasers: Suitable for pulsed micro-welding applications but require more maintenance than fiber lasers.
- CO2 Lasers: Less common for metal welding but useful for non-metallic materials and hybrid welding applications.
Automation Level
The degree of automation in a laser welding system affects productivity, consistency, and labor requirements. Consider the following options:
- Manual Laser Welding Machines: Best for small-scale production, repair work, and applications requiring operator flexibility.
- Semi-Automatic Systems: Suitable for mid-volume production where some manual handling is involved but welding parameters are controlled electronically.
- Fully Automated and Robotic Welding Systems: Ideal for high-speed, mass production environments, offering precision and consistency with minimal human intervention.
Control Features and Software
Advanced control systems and software play a crucial role in optimizing laser welding performance. Important features to consider include:
- User-Friendly Interface: Intuitive touchscreen controls or CNC programming for easy operation.
- Real-Time Monitoring: Sensors and cameras to track weld quality and detect defects.
- Adaptive Welding Technology: AI-driven systems that adjust parameters based on material conditions and joint variations.
- Connectivity and Industry 4.0 Integration: Machines with remote diagnostics, data logging, and cloud-based monitoring improve process efficiency and maintenance tracking.
Budget and ROI
Laser welding machines vary significantly in cost, depending on power, features, and automation capabilities. Factors affecting budget considerations include:
- Initial Investment: High-power fiber laser systems and fully automated machines require a substantial upfront cost but offer long-term savings through efficiency and durability.
- Operational Costs: Consider energy consumption, maintenance requirements, and consumable costs (e.g., shielding gas, and optics replacement).
- Labor Savings: Automated systems reduce manual labor costs and improve production speed.
- Long-Term Value: While a lower-cost machine may seem attractive, investing in a high-quality system with better longevity and fewer maintenance needs can lead to greater ROI over time.