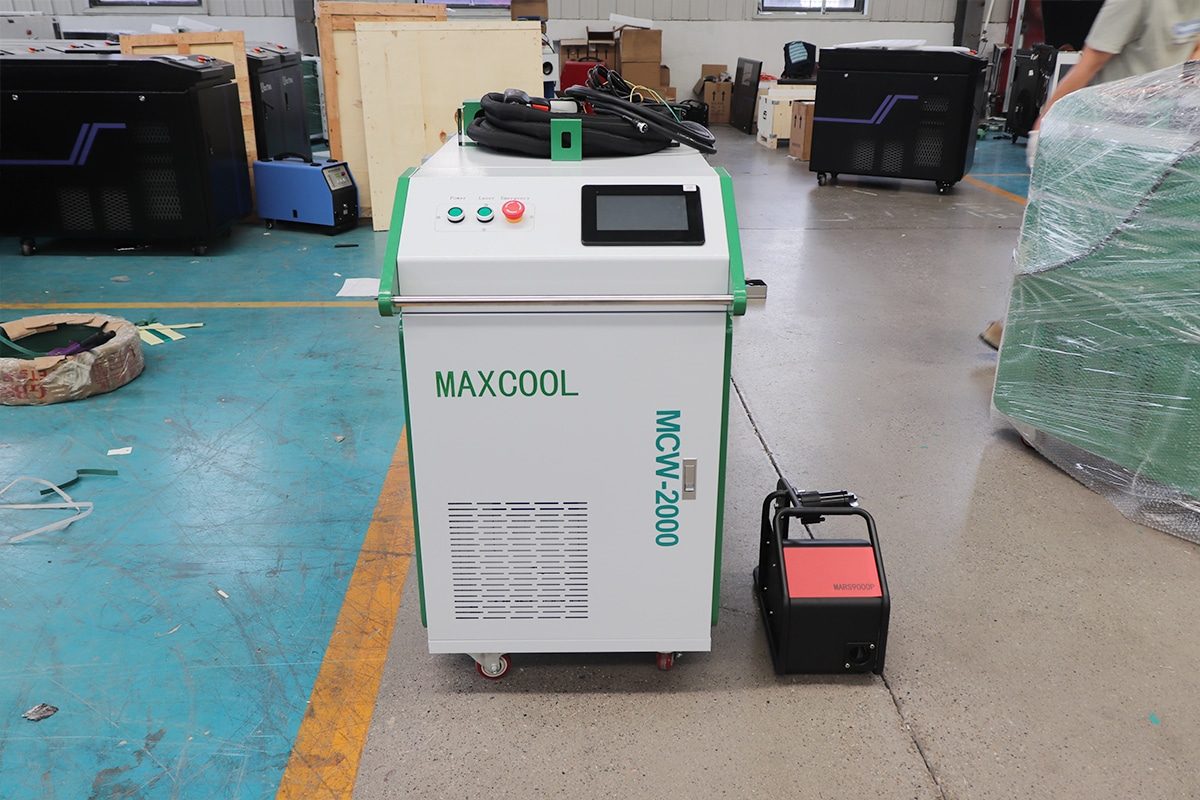
Comprehensive Guide to Laser Welding Carbon Steel
Laser welding is an advanced manufacturing technique that utilizes a highly concentrated laser beam to fuse materials with precision and minimal thermal distortion. Carbon steel, known for its versatility, strength, and affordability, is widely used across multiple industries, including automotive, construction, and heavy machinery.
Laser welding carbon steel offers numerous benefits, such as:
- High-speed processing with minimal heat-affected zones (HAZ).
- Strong and precise welds with excellent repeatability.
- Reduced material deformation compared to traditional welding methods.
However, successful laser welding of carbon steel requires a deep understanding of the material’s properties, welding parameters, equipment, and common challenges. This guide explores all critical aspects of laser welding carbon steel to help engineers and manufacturers achieve optimal results.
Table of Contents
Carbon Steel Properties
Overview of Carbon Steel Properties
Carbon steel is an iron and carbon alloy with small amounts of manganese, silicon, phosphorus, and sulfur. The carbon content significantly affects the steel’s hardness, strength, and weldability.
Key properties of carbon steel include:
- High strength and durability – Suitable for heavy-duty applications.
- Ductility and malleability – Can be easily formed and welded.
- Corrosion susceptibility – Requires coatings or treatments to prevent oxidation.
- Thermal conductivity – Influences heat distribution during welding.
Types of Carbon Steel and Their Characteristics
Carbon steel is classified based on carbon content into three main types:
- Low-carbon steel (0.05%–0.30% C): Excellent weldability and ductility. Commonly used in automotive parts, construction, and pipelines.
- Medium-carbon steel (0.30%–0.60% C): Higher strength and hardness but lower weldability. Used in gears, machinery components, and railway parts.
- High-carbon steel (0.60%–2.0% C): Extremely strong but brittle and challenging to weld. Suitable for cutting tools, springs, and high-strength components.
Weldability of Carbon Steel
Carbon content directly impacts weldability. Low-carbon steel is the easiest to weld, while medium- and high-carbon steels require preheating, controlled cooling, and post-weld heat treatment to prevent cracking and brittleness.
Key factors affecting weldability include:
- Carbon equivalent (CE): Determines steel’s susceptibility to cracking.
- Grain structure: Affects strength and heat distribution.
- Surface condition: Rust, oxides, and coatings impact weld quality.
Principles of Laser Welding Carbon Steel
Laser welding of carbon steel is a high-precision, high-efficiency process that utilizes a concentrated laser beam to fuse metal parts. This technique provides excellent weld strength, minimal heat-affected zones (HAZ), and reduced material distortion, making it an ideal choice for various industrial applications. Understanding the fundamental principles of laser welding carbon steel is essential for optimizing weld quality.
Understanding the Laser Welding Process
Laser welding operates through focused light energy that generates intense heat, allowing the materials to melt and fuse. The process can be classified into:
- Conduction Mode Welding: Used for thin sheets (≤1 mm), where heat spreads via conduction, creating shallow and wide welds.
- Keyhole Mode Welding: Utilized for deep penetration welding, forming a vaporized cavity (keyhole) that enables strong and narrow welds.
- Pulsed Laser Welding: Ideal for delicate applications, producing controlled heat input and minimizing thermal distortion.
Interaction of Laser and Carbon Steel
The effectiveness of laser welding in carbon steel depends on:
- Absorption of Laser Energy: Fiber lasers (1.06 μm wavelength) are better absorbed by carbon steel than CO₂ lasers (10.6 μm), resulting in higher efficiency.
- Thermal Conductivity: Influences how quickly heat spreads across the metal, affecting weld depth and bead formation.
- Surface Condition: Oxidation, coatings, and contaminants impact energy absorption and weld consistency.
Key Parameters Affecting Carbon Steel Welding
- Laser Power: Higher power results in deeper penetration but requires careful control to prevent defects.
- Welding Speed: Affects weld bead shape, heat input, and microstructure properties.
- Focus Position: A precise focal point ensures uniform energy distribution, reducing defects.
- Shielding Gas: Commonly used gases (argon, helium, nitrogen) prevent oxidation and stabilize the molten weld pool.
Preparation for Laser Welding Carbon Steel
Proper preparation is crucial for achieving high-quality welds and minimizing defects such as porosity, cracking, and incomplete fusion.
Material Selection and Preparation
- Choosing the Right Carbon Steel Grade: Low-carbon steel is the most weldable, while high-carbon steel requires preheating to prevent brittleness.
- Surface Condition: Rust, oil, and oxides can interfere with laser absorption, making surface cleaning essential.
Carbon Steel Joint Design Considerations
The chosen joint type influences the overall weld strength and efficiency:
- Butt Joints: Require precise alignment to ensure full penetration.
- Lap Joints: Common for sheet metal welding, providing overlap reinforcement.
- T-Joints and Fillet Joints: Used in structural applications, requiring optimal fusion depth.
Surface Cleaning and Pre-Weld Treatment
Contaminants on the surface can lead to weld imperfections, making cleaning essential:
- Mechanical Cleaning: Grinding or wire brushing removes scale and oxides.
- Chemical Cleaning: Solvent degreasing and acid pickling remove surface impurities.
- Laser Cleaning: An advanced method that eliminates rust, coatings, and contaminants without additional chemicals.
Equipment for Laser Welding Carbon Steel
The effectiveness of laser welding depends on selecting the appropriate equipment and auxiliary systems.
Types of Laser Welding Systems
- Fiber Laser Welding: Offers high efficiency, deep penetration, and energy absorption.
- CO2Laser Welding: Suitable for thick sections but less effective for carbon steel due to lower absorption.
- Diode Laser Welding: Provides cost-effective solutions for low-power applications.
Selection of Laser Sources and Parameters
- Power Output: Ranges from 500W to 10kW, depending on material thickness and application.
- Beam Quality: Higher beam quality ensures better focus and penetration.
- Pulsed vs. Continuous Wave: Pulsed lasers minimize heat input for thin sections, while continuous-wave lasers offer deep penetration.
Auxiliary Equipment and Accessories
- Shielding Gas Systems: Prevent oxidation and stabilize the weld pool.
- Cooling Systems: Maintain temperature stability to prevent overheating.
- Beam Delivery Systems: Fiber optics and mirrors ensure accurate energy focus.
Common Challenges and Troubleshooting
Despite the advantages of laser welding, certain challenges must be addressed to maintain high weld quality.
Quality Assurance and Inspection
- Regular inspection ensures defect-free welds through:
- Visual Examination: Identifies surface defects such as cracks and spatter.
- Dimensional Measurement: Verifies weld consistency and alignment.
Welding Quality Assessment
Common welding defects and solutions include:
- Porosity: caused by trapped gas or surface contamination. Improve shielding gas coverage to ensure a clean surface.
- Cracking: caused by excessive heat input or inappropriate cooling rate. Stress can be reduced by using preheating and controlled cooling.
- Incomplete fusion: occurs when the laser power is insufficient or the focus is misaligned. Sufficient fusion can be achieved by adjusting the power, welding speed and focus position.
Nondestructive Testing Methods
- Ultrasonic Testing (UT): Detects internal discontinuities.
- Radiographic Testing (X-ray): Provides an in-depth weld structure analysis.
- Magnetic Particle Inspection (MPI): Locates surface cracks in ferromagnetic materials.
Quality Control Measures
- Pre-Weld Material Inspection: Ensures proper material properties.
- Real-Time Process Monitoring: Uses sensors to detect inconsistencies.
- Post-Weld Heat Treatment: Reduces residual stress and prevents brittleness.
Applications of Laser Welding Carbon Steel
Laser welding of carbon steel is widely used across industries due to its precision, speed, and strength.
- Automotive Industry: Used for welding chassis, engine components, and structural reinforcements.
- Construction: Structural applications such as bridges, support beams, and reinforcement bars.
- Machinery and Equipment Manufacturing: Applied in gears, frames, and high-strength components.
- Energy Sector: Used in pipelines, pressure vessels, and wind turbine components.
- Shipbuilding and Maritime Industry: Hull fabrication and marine engine welding.
Best Practices and Tips
Following best practices ensures optimal laser welding results and extends equipment lifespan.
Proper Handling and Storage of Carbon Steel Materials
- Store in dry conditions to prevent oxidation.
- Apply protective coatings when necessary.
Optimization of Carbon Steel Welding Parameters
- Fine-tune power and speed for different thicknesses.
- Maintain consistent shielding gas flow to prevent oxidation.
Post-Weld Treatment and Finishing Techniques
- Stress Relief Annealing: Reduces residual stresses in high-carbon steel.
- Surface Polishing and Grinding: Enhances aesthetic quality and removes imperfections.
Maintenance of Laser Welding Machines
- Regularly clean optics and lenses to prevent beam distortion.
- Monitor cooling and gas supply systems to ensure consistent performance.
Safety Considerations
Laser welding presents specific hazards, requiring proper safety measures to protect workers and maintain operational integrity.
Hazards Associated with Laser Welding
- Laser Radiation: Direct exposure can cause severe eye and skin damage.
- Metal Fumes and Vapors: Toxic emissions require proper ventilation.
- Thermal Hazards: Intense heat can cause burns if proper PPE is not used.
Personal Protective Equipment (PPE)
- Laser Safety Goggles: Protect against high-intensity radiation.
- Heat-Resistant Gloves and Clothing: Prevent burns from hot surfaces and molten metal.
- Respiratory Protection: Essential for preventing inhalation of fumes in enclosed areas.
Safety Protocols and Guidelines
- Laser Enclosures and Barriers: Prevent unintended exposure.
- Emergency Shutdown Systems: Ensure quick response in case of malfunction.
- Regulatory Compliance: Follow OSHA and ANSI laser safety standards.
Summary
Laser welding of carbon steel is a highly precise and efficient process that enhances manufacturing across industries. By understanding material properties, welding principles, equipment selection, and troubleshooting methods, engineers and fabricators can achieve superior weld quality.
Adopting best practices, maintaining laser welding equipment, and ensuring workplace safety are crucial for maximizing efficiency and weld integrity. By leveraging laser welding technology, industries can benefit from faster production cycles, reduced defects, and cost-effective manufacturing solutions.
Get Laser Welding Solutions
At Maxcool CNC, we specialize in providing advanced laser welding solutions tailored to meet the needs of industries working with carbon steel. Our state-of-the-art fiber laser welding machines deliver high-precision, deep-penetration welds with minimal heat-affected zones, ensuring superior joint strength and minimal material distortion. Whether you require handheld laser welding machines for flexibility or automated laser welding systems for high-volume production, Maxcool CNC has the right solution.
Maxcool CNC provides customized solutions, technical consultation, and comprehensive after-sales support to help businesses achieve maximum efficiency and cost savings in carbon steel welding. Contact us today to explore the best laser welding solutions for your application!