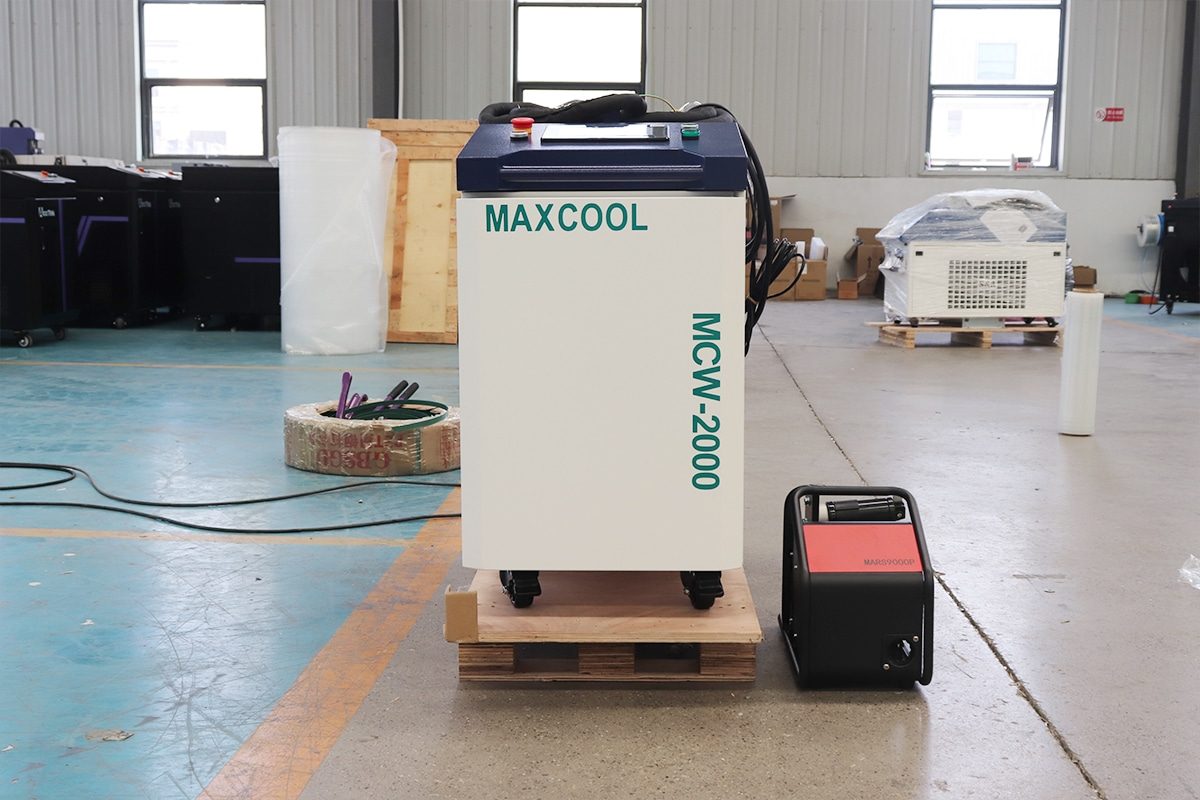
Advantages and Disadvantages of Laser Welding: Complete Guide
Laser welding is a state-of-the-art manufacturing technique that has transformed the way industries approach metal joining. As a precise, efficient, and versatile method of fusing materials, laser welding is used in many sectors such as automotive, aerospace, electronics, medical devices, and more. It uses focused laser beams to melt and bond materials together, offering a range of advantages over traditional welding methods, but also presenting some challenges. In this article, we will explore the many benefits and potential drawbacks of laser welding, providing a complete guide to its capabilities and limitations.
Table of Contents
Introduction to Laser Welding
What is Laser Welding?
Laser welding is a high-precision process that uses a laser beam to melt and join two pieces of material, typically metals, by concentrating intense energy into a small, focused area. The heat generated by the laser beam causes the material to melt, forming a weld pool that solidifies to create a strong, durable bond. This method of welding is distinct from traditional methods like MIG or TIG welding in that it uses focused light energy rather than electrical or chemical heat sources.
Unlike other welding techniques, laser welding is capable of generating precise, clean welds with minimal distortion or heat-affected zones (HAZ), which is essential in industries requiring high-quality, intricate joints.
How Does Laser Welding Work?
The laser welding process begins with a high-powered laser beam directed at the workpieces to be welded. The laser’s energy is absorbed by the material at the weld joint, heating it to the point of melting. As the molten material cools and solidifies, the two pieces are fused to form a strong bond. The weld pool is formed by the laser’s focused energy, and the laser’s power and intensity can be adjusted to control the size and depth of the weld.
Laser welding can be carried out in different modes, such as:
- Conduction Mode: The laser heats the surface of the material, and the heat diffuses into the workpiece, resulting in shallow, wide welds.
- Keyhole Mode: In this mode, the laser penetrates deeper into the material, creating a small cavity or “keyhole” that results in deep, narrow welds.
The method of laser welding is flexible, and capable of working in various environments, including atmospheric, vacuum, or controlled atmospheres.
Advantages of Laser Welding
Laser welding has a range of advantages that make it an appealing choice for a wide variety of industries. Let’s explore some of the most prominent benefits:
High Precision and Accuracy
One of the most significant advantages of laser welding is the unparalleled precision it offers. Unlike traditional welding methods, which often involve larger heat-affected zones and may require significant post-weld finishing, laser welding allows for exceptionally fine control over the weld pool. This means the process can achieve extremely accurate welds with minimal heat dispersion. For manufacturers producing small, intricate parts or components that require high precision—such as those used in the electronics, aerospace, and medical device industries—laser welding is invaluable.
For example, in the medical device sector, where components such as surgical tools, implants, and diagnostic instruments are small and often complex in shape, the precision of laser welding ensures that joints are seamless and free from defects.
Minimal Heat-Affected Zone (HAZ)
The heat-affected zone (HAZ) refers to the region surrounding the weld that experiences changes in microstructure and properties due to the heat of the welding process. Laser welding generates a small HAZ compared to traditional welding techniques. The focused laser beam melts only the material at the weld site, minimizing the surrounding material’s exposure to heat. This results in less warping, distortion, and the retention of the material’s original mechanical properties in the surrounding areas.
In applications requiring exact dimensional tolerances, such as aerospace or automotive manufacturing, the ability to minimize HAZ is crucial. It ensures that the welded parts maintain the strength and integrity required for critical applications.
Speed and Efficiency
Laser welding is a fast process, often much faster than traditional welding methods, such as TIG or MIG welding. The concentrated energy of the laser allows it to weld rapidly, reducing production times significantly. This speed is especially important in industries where high-volume production is essential, such as automotive manufacturing, where thousands of parts may need to be welded every day.
Laser welding systems are often automated, which further enhances efficiency. Robotic arms equipped with laser welding equipment can perform repetitive tasks quickly and consistently, increasing throughput while reducing human labor.
Clean and High-Quality Welds
Laser welding produces clean, smooth, and aesthetically pleasing welds with little to no spatter. Traditional welding methods, such as arc welding, often produce excess material that requires post-weld cleanup. In contrast, laser welding minimizes spatter and oxidation, producing high-quality, well-formed welds that often do not need further processing.
This quality is especially important in industries like electronics or medical device manufacturing, where clean, precise welds are critical for ensuring the proper functioning of the product. Additionally, the quality of the welds directly impacts the structural integrity of the final product, especially in highly regulated industries like aerospace.
Minimal Material Deformation
Laser welding’s precise heat application means that the surrounding material is subjected to minimal thermal expansion, reducing the risk of deformation or warping. This is particularly beneficial when welding thin materials or components that could be damaged by excessive heat. By minimizing distortion, laser welding helps maintain the desired shape and dimensions of the parts being joined.
In high-precision industries like semiconductor fabrication or fine metalworking, where part deformation could render a product unusable, the ability to control thermal expansion is invaluable.
Automation Capabilities
Laser welding is highly compatible with automation, which is one of the key reasons it has gained popularity in industries requiring large-scale production. Automated laser welding systems can run continuously, handling multiple welding tasks with minimal downtime. Automated systems are particularly beneficial for high-volume production lines, such as in the automotive or consumer electronics sectors, where speed, consistency, and precision are paramount.
In addition, automation reduces the risk of human error, ensuring that each weld is of consistent quality, regardless of the number of parts being welded.
Versatility in Material Joining
Laser welding can join a wide range of materials, including metals, plastics, and composites. The technology is particularly effective in joining dissimilar materials, such as steel and aluminum, which are commonly used in the automotive and aerospace industries.
The ability to weld different materials is advantageous in sectors like automotive manufacturing, where lightweight materials like aluminum and magnesium need to be joined with high-strength steel for enhanced performance without compromising structural integrity. Laser welding can also be used for multi-material structures, expanding its applicability to modern, lightweight composite materials.
Additionally, laser welding allows for the joining of materials with varying thicknesses, providing more flexibility in design and material choice.
Environmentally Friendly
Laser welding is considered an environmentally friendly welding method. Traditional welding often requires the use of filler materials, and shielding gases, and generates more waste and fumes. In contrast, laser welding does not require filler material in most cases, reducing waste. Furthermore, the precision of the laser ensures that the amount of heat applied is minimal, which reduces the energy consumption compared to traditional welding processes.
Moreover, as industries move towards sustainability, reducing the carbon footprint of manufacturing processes has become a priority. Laser welding’s efficiency in terms of energy usage and minimal waste generation makes it a favorable option for meeting these environmental goals.
No Need for Filler Material in Many Cases
In many applications, laser welding does not require filler material. This is because the focused laser beam can melt the edges of the material to create a strong joint without needing additional material to fill the gap. The absence of filler material leads to cleaner, stronger, and more reliable welds, and it eliminates the need to purchase and store additional materials.
The reduction in filler material use also leads to cost savings for manufacturers, particularly in high-volume production environments.
Disadvantages of Laser Welding
Despite its many advantages, laser welding also has certain limitations that need to be considered. Below are the main disadvantages:
High Initial Equipment Cost
One of the primary drawbacks of laser welding is the high initial cost of the equipment. High-powered laser systems, precision optics, and automated robots can be expensive, making it a significant upfront investment. While the equipment is durable and often requires less maintenance than traditional systems, the initial outlay can be prohibitive, especially for small and medium-sized businesses.
However, the cost can be justified by the long-term benefits such as reduced labor costs, increased productivity, and the high quality of welds. Still, it is a factor to consider when evaluating whether laser welding is a cost-effective solution for a given application.
Sensitivity to Material Surface Conditions
Laser welding is highly sensitive to the surface conditions of the materials being welded. Any contamination such as dirt, oil, oxidation, or rust can significantly affect the quality of the weld. For this reason, the materials must be thoroughly cleaned before welding to ensure optimal results. This cleaning process adds time and cost to the overall procedure.
In cases where materials are not properly cleaned, issues like poor weld penetration, porosity, or weak joints may arise, making it crucial for operators to implement strict quality control measures and ensure proper material preparation.
Limited Thickness Capability
While laser welding is effective for joining thin to medium-thickness materials, it struggles with thicker materials, especially when the required depth of penetration exceeds the laser’s ability to focus energy efficiently. Laser welding typically excels with metals up to around 10 mm in thickness, but welding thicker materials may require multiple passes or specialized laser systems capable of deeper penetration.
This limitation is less of an issue in industries where thin or medium-thickness metals are common, such as electronics or aerospace, but it could be a challenge in industries like construction or heavy manufacturing, where thick steel plates are often used.
Requires Skilled Operators
While laser welding can be automated, it still requires skilled operators to set up, adjust parameters, and troubleshoot issues when they arise. The setup process involves fine-tuning variables such as laser power, focus, travel speed, and spot size to achieve the best weld. Additionally, operators must monitor the process in real-time, ensuring that the laser is functioning properly and that no issues arise during welding.
Inexperienced operators can make mistakes that lead to suboptimal welds, machine malfunctions, or increased downtime. Therefore, businesses must invest in proper training and certification for their staff to ensure the successful implementation of laser welding technology.
Vulnerability to Environmental Factors
Laser welding is highly sensitive to environmental conditions. Factors such as ambient temperature, air humidity, and dust can affect the quality of the weld. For example, dust or air turbulence may interfere with the laser’s focus, leading to inconsistent results. Similarly, changes in ambient temperature can affect the material’s behavior during the welding process.
In controlled environments, such as clean rooms, these issues can be minimized, but in industrial settings, maintaining ideal environmental conditions may require additional investment in facilities and equipment.
Limited Weld Size and Shape
Laser welding excels in precision, but it can be difficult to produce large welds or welds in complex geometries. While this is not necessarily a disadvantage for most applications, there are certain situations where the limitations of laser welding in terms of joint size and shape can become an issue. For larger parts or where a broader weld is required, traditional welding methods may be more practical.
Applications of Laser Welding
Laser welding is widely used in a range of industries due to its advantages in precision, speed, and material compatibility. Below are some key applications where laser welding plays a crucial role:
Automotive Industry
In automotive manufacturing, laser welding is used to join various metal parts, such as body panels, exhaust systems, and engine components. The precision and speed of laser welding help improve production efficiency, reduce weight, and ensure high-quality welds that meet safety and performance standards. Laser welding is particularly useful in assembling lightweight vehicles, where the reduction of part weight is critical for improving fuel efficiency and overall performance.
Aerospace Industry
The aerospace industry benefits from the high precision and clean welds offered by laser welding. Aircraft components, often made from lightweight and high-strength materials like aluminum and titanium, require welds that do not compromise structural integrity. Laser welding ensures that joints are solid and reliable, helping to reduce the overall weight of aircraft without sacrificing strength. Furthermore, laser welding’s ability to join dissimilar metals is particularly valuable in aerospace manufacturing, where a combination of materials is often used to optimize performance.
Electronics Industry
Laser welding is commonly used in the electronics industry to join small components such as connectors, battery terminals, and circuit boards. The precision of the laser welding process allows for the creation of delicate, high-quality joints without damaging sensitive electronic parts. In addition, the ability to minimize the heat-affected zone ensures that components remain undamaged during the welding process.
Medical Device Manufacturing
Laser welding is ideal for medical device manufacturing, where high-quality, precise joints are essential for creating safe and reliable implants, surgical instruments, and diagnostic tools. Laser welding enables the joining of complex, small parts with minimal distortion, making it ideal for producing medical devices with intricate geometries and tight tolerances.
Prototyping and Additive Manufacturing
In additive manufacturing (3D printing), laser welding is used to fuse printed layers or components, ensuring that parts are bonded together with high precision. Laser welding’s ability to rapidly join 3D-printed parts makes it an ideal solution for rapid prototyping, especially for industries like aerospace or medical devices, where the ability to quickly produce functional prototypes is crucial.
Summary
Laser welding has revolutionized the manufacturing landscape by offering a range of benefits, including unmatched precision, speed, and clean welds. While the technology does have its limitations, such as high initial costs and sensitivity to material surface conditions, the advantages it provides make it a valuable tool for many industries.
For manufacturers looking to improve efficiency, enhance product quality, and reduce post-weld finishing, laser welding offers a compelling solution. By understanding both its benefits and challenges, businesses can make informed decisions about integrating laser welding into their production processes.
Ultimately, as laser welding technology continues to evolve, its potential applications are likely to expand, offering even more possibilities for high-precision, high-quality manufacturing. Whether used in the automotive, aerospace, electronics, or medical sectors, laser welding will continue to shape the future of modern manufacturing.
Get Laser Welding Solutions
If you’re looking to enhance your manufacturing processes with precision, efficiency, and minimal post-weld cleanup, laser welding solutions offer an ideal answer. Maxcool CNC provides state-of-the-art laser welding machines designed to meet the demands of industries ranging from automotive and aerospace to electronics and medical device manufacturing. Our laser welding machines are engineered for high accuracy, fast cycle times, and the ability to join dissimilar materials, ensuring high-quality welds with minimal heat-affected zones (HAZ).
Maxcool CNC’s laser welding systems come with customizable features to suit a wide range of applications. Whether you need a solution for thin material welding or complex geometries, our machines are built for precision and durability. With a focus on reducing operational costs and improving productivity, Maxcool CNC is dedicated to providing businesses with reliable, cutting-edge laser welding technology. Contact us today to learn how our solutions can transform your production processes and drive innovation in your industry.