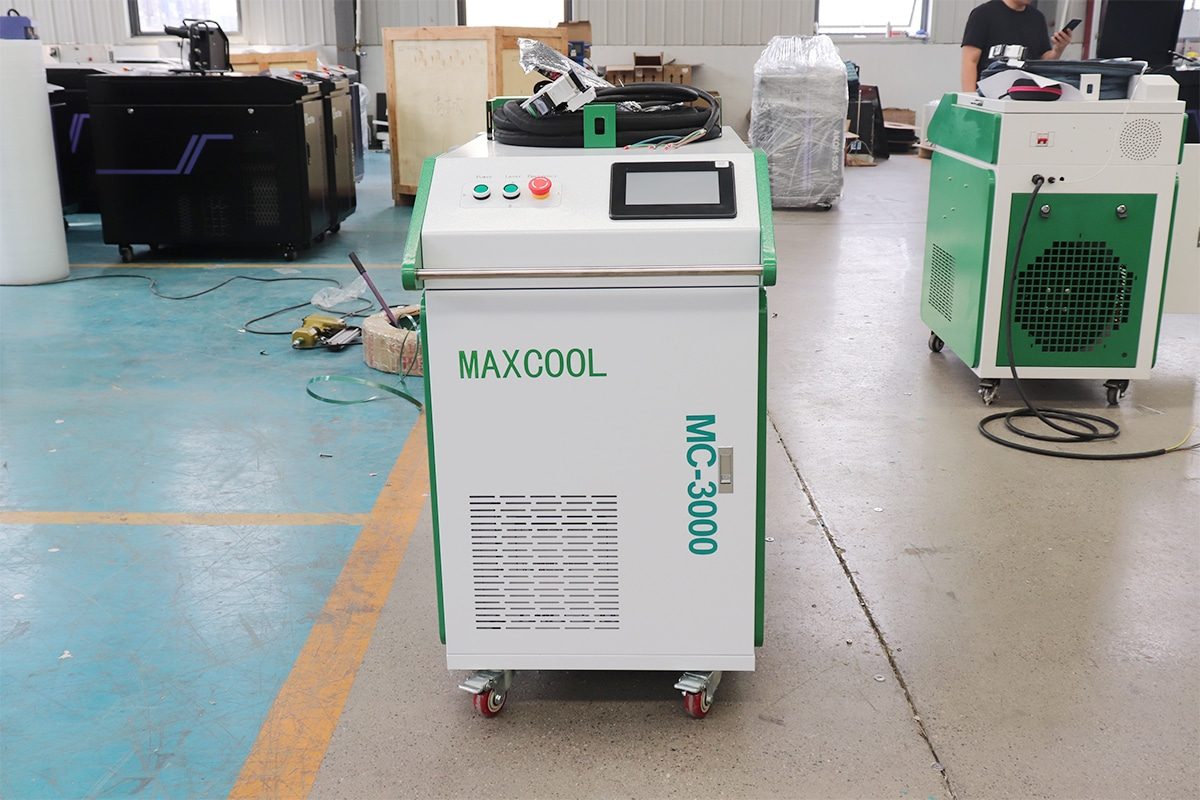
Advantages and Disadvantages of Laser Cleaning: Complete Guide
Laser cleaning is a rapidly evolving technology that has been transforming the way industries and conservationists approach cleaning tasks. Unlike conventional cleaning methods that rely on abrasives or chemicals, laser cleaning uses high-powered laser beams to remove contaminants such as rust, oil, paint, and dirt from surfaces. This technology, which is both efficient and environmentally friendly, has become an integral part of many sectors, from manufacturing to art conservation.
The development of laser cleaning technology is a response to the growing need for more precise, sustainable, and safe cleaning solutions in various industries. As global industries push for cleaner, more efficient manufacturing processes, laser cleaning stands out as a promising alternative to traditional cleaning methods. However, as with any new technology, laser cleaning comes with its own set of advantages and disadvantages.
This article aims to provide a comprehensive overview of laser cleaning, exploring its advantages, disadvantages, and practical applications. By examining both sides of the technology, businesses, and industries can make informed decisions about whether laser cleaning is the right choice for their needs.
Table of Contents
What is Laser Cleaning?
Laser cleaning, often referred to as laser ablation or laser surface cleaning, involves the use of high-intensity laser beams to remove unwanted materials from a surface. The laser energy is directed at the contaminant, and it either vaporizes, sublimates or is blown away from the surface, leaving the underlying material intact. This non-contact cleaning process is incredibly precise, offering the ability to target only the contaminants without damaging the underlying substrate.
Laser cleaning is particularly suitable for removing rust, old paint, oxidation, dirt, and other surface contaminants. The process works by focusing a high-powered laser beam onto the surface, which heats the contaminant. Depending on the intensity and type of laser used, the contamination is either vaporized or removed through a combination of thermal and mechanical effects.
The type of laser source used in a cleaning machine plays a crucial role in its performance characteristics, versatility, and cost. Laser cleaning machines can be equipped with either pulse lasers or continuous wave (CW) lasers, each offering distinct advantages and trade-offs.
- Pulse Laser: Pulse laser cleaning machines emit high-intensity bursts of energy in short durations, allowing for precise material removal without causing excessive heat buildup on the surface. This makes them ideal for delicate substrates or applications where controlled cleaning is crucial. Pulse lasers are often used for removing coatings, and oxide layers, or for restoration projects. The precision and lower risk of damage can make pulse lasers more costly than their continuous counterparts.
- Continuous Wave (CW) Laser: Continuous wave lasers emit a constant, uninterrupted beam of energy, making them highly effective for applications requiring fast, large-area cleaning. CW lasers are often used for removing rust, thick coatings, and other industrial cleaning applications that require high speed and power. While they may not offer the same level of precision as pulse lasers, they often provide higher cleaning rates. Machines with CW lasers are generally more affordable than pulse lasers, although they may consume more energy and generate more heat during operation.
Laser cleaning systems can be operated manually or automated, depending on the scale of the operation. The use of robots or automated machinery allows for more consistent results and reduces the need for human intervention in hazardous environments.
Applications of Laser Cleaning
Laser cleaning has found a wide range of applications in both industrial and non-industrial sectors. Some of the most common uses of laser cleaning include:
Industrial Applications
Laser cleaning has proven to be particularly useful in industries where precision and efficiency are paramount. For example, in the automotive, aerospace, and heavy machinery sectors, laser cleaning is used to remove rust, oil, paint, and other contaminants from metal surfaces. This is important not only for ensuring the performance and longevity of machinery but also for preparing surfaces for subsequent processes, such as coating or welding.
In the automotive industry, laser cleaning can be used to remove paint layers without damaging the underlying metal, making it an ideal solution for the restoration of vintage cars or parts. Similarly, in the aerospace industry, laser cleaning is used to clean aircraft parts, ensuring the integrity and safety of the machinery.
Art Conservation and Restoration
One of the most unique and beneficial applications of laser cleaning is in the field of art conservation. Over time, works of art—such as paintings, sculptures, and historical artifacts—accumulate dirt, grime, and old layers of varnish. Traditional cleaning methods can be abrasive and risky, but laser cleaning allows conservators to remove contaminants without damaging delicate surfaces.
The precision of laser cleaning means that even the most intricate and fragile artworks can be cleaned effectively. It has been used to restore famous paintings, sculptures, and manuscripts, allowing conservators to carefully and precisely remove pollutants and old varnish without harming the underlying material.
Surface Preparation for Coatings
In many industrial applications, laser cleaning is used as a preparatory step before applying coatings, paints, or other surface treatments. For instance, in the production of electronics or machinery, laser cleaning can be used to clean metal surfaces before applying protective coatings. This ensures that the coatings adhere properly and last longer, improving the overall quality and durability of the product.
Environmental Cleanup
Laser cleaning is also being explored for environmental applications, such as the cleanup of pollutants and contaminants in natural environments. One example is the potential use of laser cleaning for oil spill recovery. The laser could be used to remove oil contaminants from beaches, water surfaces, and other natural habitats without disturbing the ecosystem.
By targeting only the contaminants and leaving the surrounding environment unharmed, laser cleaning offers a sustainable solution to pollution cleanup. Its precision and non-contact nature make it ideal for delicate environments where other cleaning methods might cause harm.
Advantages of Laser Cleaning
Laser cleaning offers several significant benefits, making it an increasingly popular choice for various industries. Below are the key advantages of laser cleaning:
Precision and Control
Laser cleaning offers unmatched precision compared to traditional cleaning methods. The high-powered laser beam can be finely tuned to focus on specific areas of contamination, ensuring that only the contaminant is removed. This is particularly important when dealing with delicate or intricate surfaces, such as artwork or sensitive machinery components. The ability to precisely control the laser’s intensity and focal point makes it possible to clean without damaging the underlying material.
For example, when removing rust or corrosion from metal surfaces, laser cleaning can be used to target the rust specifically, without affecting the surrounding metal. This level of control ensures that the cleaning process is as efficient as possible, without compromising the integrity of the material being cleaned.
Minimal Environmental Impact
Laser cleaning is an environmentally friendly alternative to traditional cleaning methods. Many conventional cleaning techniques, such as sandblasting or chemical cleaning, generate hazardous waste materials, such as abrasive particles or toxic chemicals, that require proper disposal. In contrast, laser cleaning uses no consumables and generates little to no waste. The only byproduct of the process is the ablated material, which can often be safely collected and disposed of.
Moreover, laser cleaning eliminates the need for harsh chemicals and solvents, which can be harmful to both human health and the environment. By avoiding the use of these substances, laser cleaning helps reduce the environmental footprint of cleaning operations.
Non-Contact Cleaning
One of the key benefits of laser cleaning is that it is a non-contact method. Traditional cleaning methods, such as abrasive blasting or mechanical brushing, involve direct contact with the material being cleaned. This can result in wear and tear on the material’s surface, leading to damage over time. With laser cleaning, however, there is no physical contact between the cleaning tool and the material, eliminating the risk of surface damage.
This is especially important in industries where surface integrity is crucial, such as in the cleaning of delicate electronic components or historical artifacts. By using a non-contact method, laser cleaning preserves the material’s surface quality, reducing the need for costly repairs or replacements.
Cost-Effectiveness in the Long Run
While the initial investment in a laser cleaning system can be substantial, it is often more cost-effective in the long run compared to traditional methods. Laser cleaning systems require no consumables like abrasive materials or chemicals, which are recurring costs with conventional cleaning methods. The only ongoing costs are related to the maintenance of the equipment and the energy required to operate the lasers.
Additionally, laser cleaning is generally faster than traditional methods, reducing labor costs. For example, laser cleaning can be automated, allowing for consistent, high-speed cleaning without the need for constant human intervention. This efficiency helps lower operational costs and improve productivity.
Versatility
Laser cleaning can be used on a wide range of materials, including metals, plastics, ceramics, and even organic materials. This versatility makes it suitable for many different industries, from manufacturing to conservation. Whether it’s removing rust from a steel beam or cleaning a delicate painting, laser cleaning can be adapted to fit the specific needs of the job.
The flexibility of laser cleaning also allows it to be used in various contamination scenarios. For example, laser cleaning can remove not only rust but also oil, dirt, and even paint from surfaces. This broad range of applications adds to its appeal as a universal cleaning solution.
Safety
Compared to traditional cleaning methods that often require the use of hazardous chemicals or abrasive materials, laser cleaning is safer for operators. There are no toxic substances or dangerous physical processes involved in laser cleaning. Furthermore, the process can be automated, reducing human exposure to potentially harmful environments.
That said, operators must still take precautions, such as wearing protective eyewear and clothing, to avoid potential risks associated with laser exposure. But overall, laser cleaning offers a safer working environment than methods that involve harsh chemicals or abrasive media.
Disadvantages of Laser Cleaning
While laser cleaning technology offers a range of benefits, it also has its share of limitations. These disadvantages must be carefully considered before deciding whether laser cleaning is the best choice for a specific application. Here are the main drawbacks of laser cleaning:
High Initial Investment
One of the most significant challenges with laser cleaning is the substantial upfront cost associated with purchasing the necessary equipment. Laser cleaning systems are sophisticated and expensive, with costs that can be prohibitively high for smaller businesses or those with limited budgets. The price tag includes not only the laser machines themselves but also the required training for operators, installation, and maintenance of the system.
For industries or businesses that don’t require frequent cleaning or that have smaller-scale operations, the initial investment in laser cleaning technology may not be justified. While the long-term savings on consumables and reduced labor costs can offset this investment, the barrier of high initial costs remains a key consideration.
Energy Consumption
Laser cleaning requires a considerable amount of energy to operate effectively, particularly when dealing with large surfaces or tougher contaminants. The energy required for high-powered lasers to vaporize or ablate materials can lead to higher operational costs.
In industries with high energy demands, such as manufacturing or aerospace, this energy consumption could add to the overall cost of laser cleaning. However, advancements in laser efficiency may help reduce this concern over time, especially as more energy-efficient laser systems are developed.
Safety Concerns
Although laser cleaning is generally a safer alternative to abrasive or chemical methods, there are still safety concerns related to the use of high-powered lasers. Operators must take precautions to avoid exposure to laser beams, which can cause serious injury to the eyes or skin. As a result, safety measures such as protective eyewear, clothing, and shielding are necessary to ensure that operators are safe during the cleaning process.
Moreover, while the laser beam itself is non-contact, the process of cleaning can create debris or particles that need to be managed, especially in industrial settings. These byproducts need to be safely collected and disposed of, which adds an extra layer of complexity and potential cost to the operation.
Limited Effectiveness on Certain Materials
Laser cleaning is highly effective on certain materials, such as metals, ceramics, and plastics, but it may not be the ideal solution for all surfaces. For example, laser cleaning can sometimes be less effective on porous or very delicate materials, where precision is needed, or on materials that are highly reflective or transparent to the laser wavelength used.
In some cases, laser cleaning may not remove all contaminants or coatings if they are too thick or strongly bonded to the substrate. Traditional cleaning methods may be necessary to address these more challenging scenarios.
Requirement for Skilled Operators
Laser cleaning technology requires skilled operators who are trained in the proper use of the system, safety protocols, and maintenance procedures. While the technology has become more user-friendly, there is still a learning curve, especially for those unfamiliar with laser equipment.
Improper handling of the laser or inadequate training can result in ineffective cleaning, wasted time, or even damage to the material being cleaned. This means that businesses must factor in the cost of training and potentially hiring specialized personnel, which could increase operational expenses.
Comparison with Traditional Cleaning Methods
Laser cleaning has made significant strides as a modern cleaning solution, but it is important to compare it with traditional cleaning methods to better understand its advantages and disadvantages. Here’s how laser cleaning stacks up against conventional cleaning techniques such as abrasive blasting, chemical cleaning, and mechanical cleaning:
Precision and Control
Laser cleaning offers a much higher degree of precision compared to traditional methods. In mechanical cleaning, abrasives or tools come into direct contact with the surface, which can result in surface damage or wear over time. Similarly, chemical cleaning methods often involve harsh substances that can erode or corrode delicate materials if not applied correctly.
Laser cleaning, by contrast, is a non-contact process. The laser beam is precisely controlled, allowing operators to target contaminants without affecting the underlying material. This is especially valuable for sensitive or intricate surfaces, such as delicate machinery parts, electronics, or historical artifacts, where traditional methods might cause irreversible damage.
Environmental Impact
One of the strongest points in favor of laser cleaning over traditional methods is its minimal environmental impact. Many conventional cleaning methods, such as abrasive blasting or chemical cleaning, generate hazardous waste, including dust, particulate matter, and chemicals that must be carefully disposed of. These byproducts can pose serious environmental and health risks.
Laser cleaning, on the other hand, produces no harmful waste materials (other than the ablated contaminant), making it a more environmentally friendly option. There are no chemicals, solvents, or abrasive materials involved, which reduces both environmental pollution and the potential for worker exposure to hazardous substances.
Chemical cleaning, though effective in certain applications, often requires toxic solvents that can pollute both the environment and the workplace. These chemicals are also a significant disposal issue, whereas laser cleaning’s waste materials are generally easier to manage, being mostly vaporized contaminants or particulate matter.
Speed and Efficiency
Laser cleaning can be faster than many traditional methods, especially when applied in large-scale industrial operations. For example, in abrasive blasting or sandblasting, the cleaning process is often slower due to the need to continually replenish abrasive materials and remove the debris produced during cleaning.
Laser cleaning, being non-contact and precise, can remove contaminants quickly and efficiently, particularly for routine or automated cleaning jobs. The ability to automate laser cleaning systems further accelerates the process, reducing downtime in manufacturing or production environments.
However, traditional methods such as high-pressure water blasting or abrasive blasting might still have an edge when it comes to bulk cleaning tasks on large, rugged surfaces. These methods can clean quickly, albeit at the cost of producing waste materials or damaging sensitive surfaces.
Safety and Operator Health
In terms of safety, laser cleaning can be advantageous because it eliminates the need for workers to handle harmful chemicals or abrasive materials directly. With traditional cleaning methods, workers are often exposed to toxic chemicals, solvents, or high-pressure blasting equipment, which pose serious risks to health and safety.
That said, laser cleaning still requires careful management to ensure operator safety. High-powered lasers can be hazardous if not handled properly, and operators must wear protective gear such as laser safety goggles and clothing. However, in terms of long-term health risks, laser cleaning is generally considered to be safer compared to many traditional cleaning methods, which involve more immediate exposure to harmful substances.
Cost Considerations
Cost remains a significant factor when comparing laser cleaning to traditional methods. The initial investment in laser cleaning systems is typically much higher than the cost of purchasing equipment for abrasive blasting or chemical cleaning. However, laser cleaning eliminates the need for consumables, such as chemicals, abrasives, or solvents, which can add up over time with traditional methods.
Additionally, because laser cleaning systems can often be automated, they can lead to savings in labor costs. This is particularly beneficial in high-volume industries where speed and efficiency are paramount. Traditional methods may require more manual labor or the ongoing purchase of consumable materials, which can result in higher operational costs over time.
In the long run, while laser cleaning systems have a high upfront cost, they can offer significant savings due to lower material costs, reduced labor expenses, and less waste disposal. For businesses that need frequent or large-scale cleaning, the cost-effectiveness of laser cleaning can outweigh the initial investment.
Versatility
Laser cleaning is a highly versatile method, capable of cleaning a wide variety of surfaces, from metals and ceramics to plastics and organic materials. This versatility is particularly valuable in industries where multiple types of materials need to be cleaned, such as in manufacturing or art conservation.
Traditional cleaning methods often require different tools or chemicals for different materials. For example, abrasive blasting may be too harsh for delicate metals, while chemical cleaning may be ineffective on certain surfaces. Laser cleaning, with its customizable parameters (laser power, wavelength, etc.), can be adapted to handle a wide range of substrates and contaminants, offering greater flexibility compared to conventional methods.
Summary
In conclusion, laser cleaning offers a range of significant advantages, from its precision and environmental friendliness to its versatility and efficiency. It stands as a cutting-edge solution for cleaning a wide range of materials and contaminants across various industries. However, despite its many benefits, certain disadvantages need to be considered, such as the high initial investment, energy consumption, and the need for specialized knowledge and training to operate the technology effectively.
As the technology becomes more refined and cost-effective, laser cleaning is expected to play an increasingly important role in industrial applications, conservation, environmental cleanup, and beyond. Industries that are looking for precision, efficiency, and environmentally friendly cleaning methods will find laser cleaning to be an invaluable tool in their operations.
Get Laser Cleaning Solutions
If you are looking for an advanced, efficient, and environmentally friendly cleaning solution, laser cleaning could be the ideal choice for your needs. Whether you’re dealing with rust removal, paint stripping, or the cleaning of delicate surfaces, laser cleaning offers precise, non-contact cleaning that minimizes the risk of damage to the material.
Maxcool CNC, a leading manufacturer of laser cleaning machines, provides state-of-the-art systems that cater to a wide range of industries. Their laser cleaning solutions are designed for versatility, efficiency, and sustainability. With customizable settings, Maxcool CNC’s laser cleaning machines can handle various contaminants on materials like metal, plastic, and even historical artifacts with minimal waste and no harmful chemicals.
For businesses looking to upgrade their cleaning processes, Maxcool CNC offers comprehensive laser cleaning systems that are easy to integrate into existing workflows. Explore the benefits of laser cleaning and invest in cutting-edge technology to improve your operations and reduce environmental impact. Contact Maxcool CNC today to learn more about how their laser cleaning machines can transform your cleaning processes.